Question 75: Please describe your best turnaround practice for cleaning and inspecting heat exchanger bundles versus replacement.
SHELTON (KBC Advanced Technologies, Inc.)
KBC is a nonoperating company, so we do not operate any equipment or conduct turnarounds. However, we do know that the bundle must be cleaned for inspection. We are accustomed to seeing hydrolancing or chemical cleaning for less severe services. KBC has a RAM (Reliability, Availability, & Maintenance) group that I consulted for these responses. Don talked about the type of matrix our RAM group evaluates. Our mechanical engineers also talked about inspection. Three-quarter inch tubes are difficult to inspect internally. Our RAM group has seen two-inch boiler tubes inspected with a borescope but not heat exchanger tubes.
Our Maintenance experts talked about eddy current, IRIS (Internal Rotary Inspection System), and flux leakage for internal inspection of three-quarter inch tubes. I have not personally seen any of these nondestructive inspection procedures, but they are usually limited to about 10% or 20% of the tubes because it is so time-consuming and manpower intensive.
Best Practices for inspection would be based on the failure history. For example, if there are some plugged tubes, you would obviously inspect around those tubes.
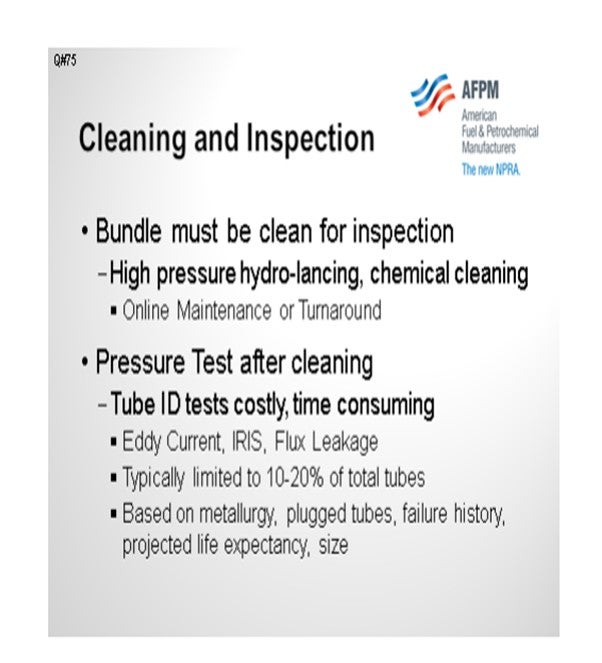
Our RAM group did say that if more than 10% of the tubes are plugged, they would replace the bundle. The decision to repair or replace is based on whether it can be done online versus during the turnaround. If it lengthens the turnaround or delays startup, then there is a payout for a new replacement bundle.
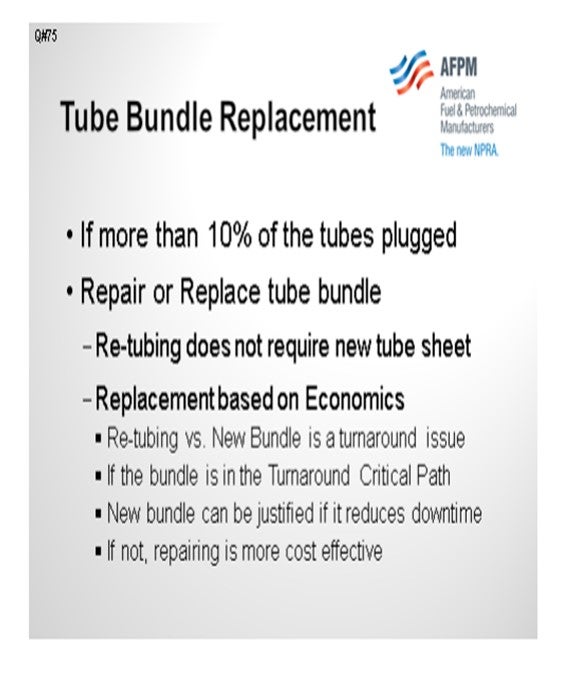
I worked for a company that licensed process units. Whenever we would start up a process unit, we would take start-of-run data, including complete temperature and pressure profiles at design flow rates. High quality data should determine whether or not the service requires cleaning. Performance monitoring tools should be used.
KBC has the HX MonitorTM utility in Petro-SIMTM, which can be used to monitor complex heat exchange networks. With our software, we can monitor a single service or an entire heat exchanger network. Complete process units are pinched in the entire facility.
None of the tools are very beneficial if the unit does not have good start-of-run data. So, we highly recommend taking good start-of-run data with temperature and pressure surveys across the exchangers.
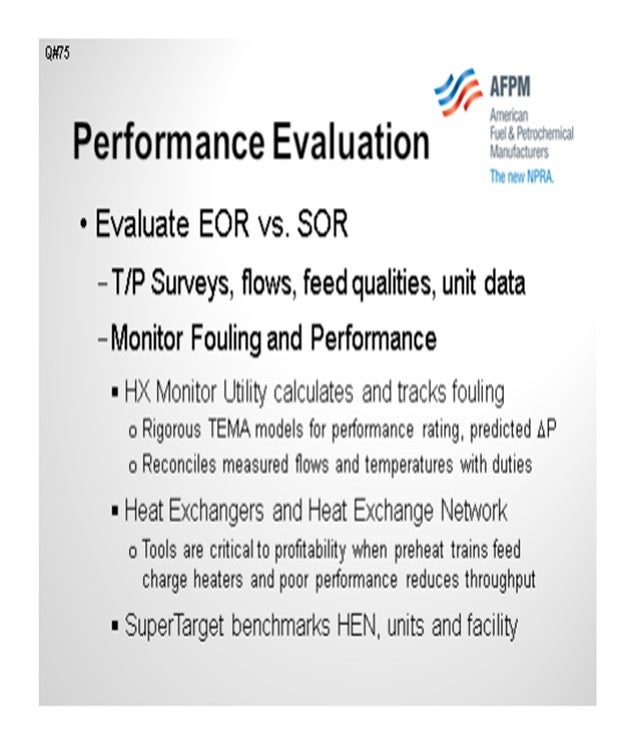
KEVIN PROOPS (Solomon Associates)
I agree with most of Al’s points and want to add a few points. We have had a lot of these discussions with clients lately. We are seeing a trend towards more aggressive replacement instead of repair, which is driven by the desire to shorten the turnaround duration and probably to avoid doing work twice, if you will. If you think about pulling the bundle when you are staged to do that and getting the permit to do that work, if you then go back a week later and put the bundle back in, then you are doing the work twice. If you can mobilize and just work at the shell once, you will have a shorter job scope at that site. There is a macro-optimization of the whole turnaround. This relates to Al’s point about whether or not it is on the critical path, which was, “Maybe you want to be a little more aggressive if you want to have a shorter turnaround."
Considering all of the risks he discussed, you are not [or may not be?] sure of the condition of the bundle, and you will want to evaluate whether you can upgrade the performance of heat transfer. I know a lot of people now talk about bundle designs that stay clean better, and those are drivers as well. The point is that if the person making the decision is only looking at the economics of the exchanger itself and not considering the economics of the total turnaround downtime, then he or she may not really get the optimum answer.
AHMAD AL-JEMAZ (Kuwait National Petroleum Corporation)
We typically operate our cokers for 11 months before we go for a shutdown for decoking. This is without online spalling. I wonder where it puts us among the coker operators as a community in the States.
BASHAM (Marathon Petroleum Corporation)
We use online spalling. Typically, we are shooting for five-year turnaround cycles.
AHMAD AL-JEMAZ (Kuwait National Petroleum Corporation)
So how long you can achieve run-length without online spalling?
BASHAM (Marathon Petroleum Corporation)
It depends on the feed quality. We have gone as long as 12 weeks between spalls and as short as four weeks between spalls. We typically average somewhere around seven to eight weeks between spalls.
TRAN (Houston Refining LP)
We do online spalling, too. The interval may range from three weeks to several months. Our turnaround cycle is six to seven years. We may shut down for a mid-turnaround cycle offline decoking (pigging) because the spallings are not effective anymore.
MAHENDRA SHEVADE (Reliance Industries Limited)
Mr. Basham, what percentage of FCC slurry will react with the feed to improve the coke quality?
BASHAM (Marathon Petroleum Corporation)
It is somewhere between 2% and 5%. First of all, it depends on whether you even have the capability. Most of our cokers do not. In fact, we have very little experience with it. You can take a look and see if that helps your condition. This response is based on licensor recommendations.
SHELTON (KBC Advanced Technologies, Inc.)
Tube bundle inspection procedures during turnarounds vary among operating companies. Standard procedure is to pressure test bundles after cleaning. Nondestructive tests, such as eddy current, IRIS, and flux leakage can be used for inside diameter inspection. Tube ID tests are costly and time consuming so inspections are typically limited to a percentage of the total tubes based on metallurgy, tube characteristics, failure history, degradation mechanism, re-tubing history, number of plugged tubes and projected life expectancy. The bundle must be clean for manual tube ID inspection by a technician.
Our Best Practice is to use high pressure hydrolancing or chemical cleaning. Cleaning can be an online maintenance or turnaround task depending on isolation valves.
Tube bundles are typically not replaced due to fouling if they can be cleaned. Turnaround tube bundle replacement criteria are based on inspection history and economics. If the bundle life is eight years and at the four-year mark 10% of the tubes have been plugged, then re-tubing versus a new bundle becomes a timing issue for the turnaround. If the bundle is in the critical path of the turnaround, then a spare bundle to swap during the turnaround can be justified if it reduces downtime. Decreasing downtime determines whether to repair or discard outside the turnaround. If not, repairing would be an option.
Each heat exchanger tube bundle must be assessed individually based on operating data collected at start-of-run, during the run, and end-of-run. SOR temperature and pressure drop surveys should include flow rates, feed qualities and unit operating data. It is important to accurately benchmark each service including individual heat exchangers and the entire Heat Exchange Network (HEN). Fouling, performance and operating history should be tracked throughout the run to determine the justification for online cleaning between turnarounds. EOR performance determines if the service must be cleaned during the turnaround.
There are several software programs available for onstream monitoring of STHE networks and individual heat exchangers. HX Monitor™ Utility for calculating and tracking fouling with rigorous Petro-SIM™ STHE models for performance rating and pressure drop predictions. HX Monitor™ translates measured flows and temperatures into reconciled exchanger duties to facilitate performance evaluation. KBC’s SuperTarget™ can benchmark complex STHE networks. These tools can be used to optimize thermal efficiency and the cleaning cycle for individual tube bundles or entire heat exchange networks. Many tube bundles do not have full instrumentation so monitoring tools with data reconciliation are required to analyze complex networks and identify individual tube bundle cleaning requirements.
Monitoring the fouling of preheat trains that set the inlet temperatures to fired heaters can improve heater performance and reduce fuel consumption. The proper analytical tools can be critical to profitability when preheat trains feed charge heaters and poor performance can reduce process unit throughput. The Best Practice is to identify when to clean individual tube bundles are based on economics.
It is a common observation that many facilities do not collect detailed SOR flow, temperature and pressure surveys for each service and tube bundle after turnarounds at maximum throughput. Modern turnarounds involve multiple units and at times, the entire facility, depending on the number of crude units. After a major turnaround, efforts are focused on commissioning all process units until the refinery is at full utilization. SOR data collection may slip to the middle of the run. The Best Practice is to collect SOR data as a basis for performance comparison.
BASHAM (Marathon Petroleum Corporation)
Cleaning cycles should be determined by the rate of fouling or U trends, with a cost/benefit analysis of the recovered duty compared to cost of cleaning, which the actual mechanical cleaning cost and lost production. At Marathon Petroleum Company, one of our refineries has utilized Conoco ‘pigs’ to clean select heat exchanger bundles that are difficult to jet clean, especially in the return bends. The pigs will return the heat exchanger bundles to new condition. Historically heat exchanger bundles have been replaced based on a set percentage of plugged out of service tubes (i.e., 15%) with no appreciation for how many outages it would take to reach the set percentage. Currently the heat exchanger bundle cycle life between failures is tracked, with a cost/benefit analysis completed on the expected life cycle with associated maintenance and production costs versus the cost to replace. Metallurgical options are included in this evaluation. In transitioning to this system, heat exchanger bundle life cycles followed an exponential curve in projecting the next cycle time before failure to determine the optimal replacement time.
ROBERTSON (AFPM)
That concludes this Q&A. I want to thank the panelists. You did a great job. Thank you very much. I want to thank Harold for coaching this group. We appreciate your helping this team to prepare. Steve, thanks for mic handling also. Great job, guys.