Question 74: For a unit targeting low vapor pressure gasoline, which variables have the greatest impact on isopentane production?
REYNOLDS (Phillips 66)
Phillips 66 has not done very much research towards iC5, specifically. We did review some base data and looked for some correlations with what impacts the iC5 production, and we did not find too many that are strongly correlated.
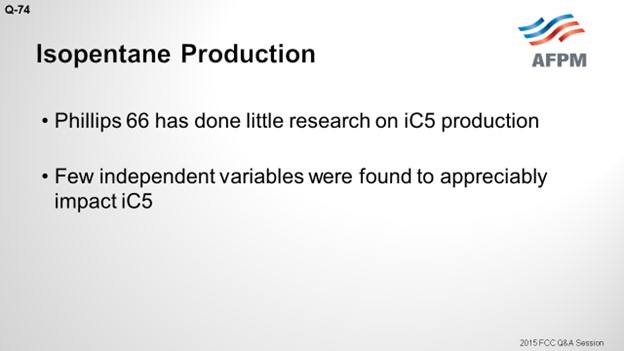
The riser does have an impact. On the Y axis, this plot shows the isopentane as a percentage of the gasoline; a 430°F+ conversion is shown on the X axis. There are three curves representing three different riser temperatures. There is a very wide range in these three risers: from 930 to 1013°F; but at constant conversion, the iC5 decreases with riser outlet temperature by about 1.5 wt% across that really wide range of riser temperatures. Across the conversion, there is a fairly significant change. So, as you crack more material into gasoline, the fraction of gasoline that is comprised of the total C5s will go up.

I included isopentene. The C5 olefins will be present along with the iC5s. They have a similar RVP (Reid vapor pressure). As opposed to iC5, C5 olefins increase with increased riser with a similar magnitude of change. So essentially, you are trading barrels of iC5 for C5 olefins, which has a negligible effect on RVP.
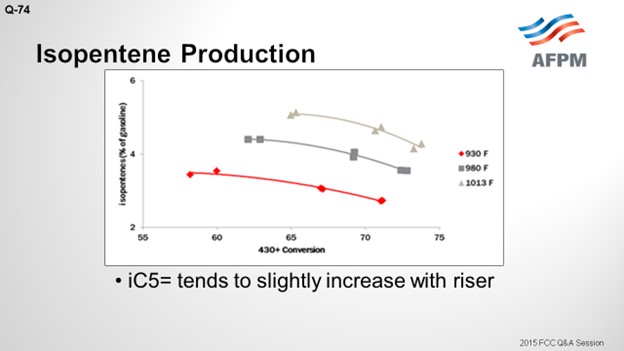
Other parameters we have reviewed which really do not seem to influence iC5 production are feed temperature and distillate content in the feed. You must have a significant change in distillate content; for example, a 40% change of your feed distillate will make about a 1% iC5 change. Unexpectedly, we did not see too much of a correlation with ZSM-5. You would think that if you crack the C6/C7 range of gasoline into LPG, you will have a concentrating effect; but we did not see that. Bart probably will disagree with me. Rare earth content will shift your olefins to your iC5 via hydrogen transfer reactions; but again, it will not have a huge impact on the RVP.
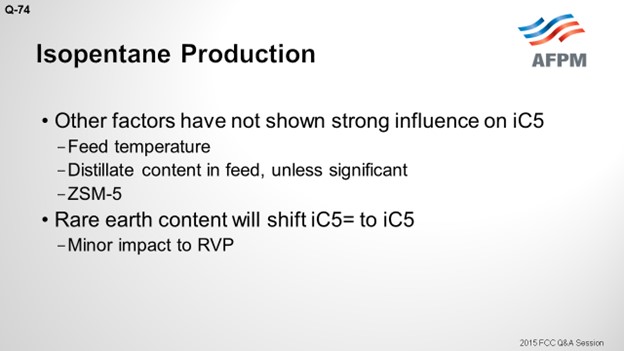
This table shows some of the RVPs for the C4- and C5-range materials. I included a column that indicates the volume percent required to add one psia (pounds per square inch absolute) of RVP to gasoline. You can see that there is a significantly larger impact from the butanes. So, when comparing normal butane to iC5, you can see that it has about four times the impact.
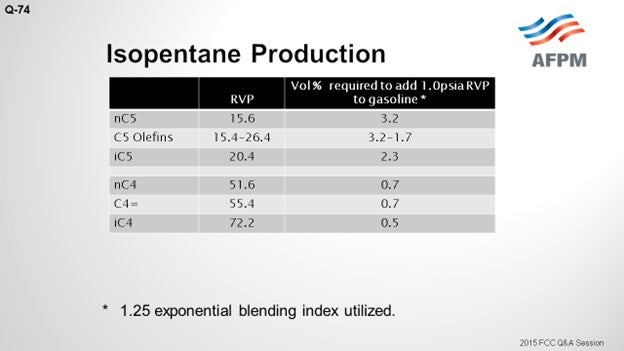
In conclusion, I think a facility must have an extremely high value of RVP barrels to warrant riser or catalyst formulation to make a negligible impact on iC5. I think your first priority is to try to get as much of the C4s out of your gasoline as you can. If you really do have C5s that are impacting your blending pool RVP, you should look at fractionating them out of gasoline into your C4 streams.
DE GRAAF (Johnson Matthey Process Technologies)
Isopentane is one of the lightest components in gasoline, and typically everything that increases conversion will increase isopentane. The rarer earth you have, the more hydrogen transfer of your catalyst, the more isopentane you will create. So, if you go for a higher riser outlet temperature, you will shift the equilibrium between isopentane and isopentene. A higher rise will give you more isopentane. Use of ZSM-5 additives can increase isopentanes because isopentenes can be transformed into isopentanes by hydrogen transfer. However, the effect of conversion is the most important factor affecting the amount of isopentane formed.
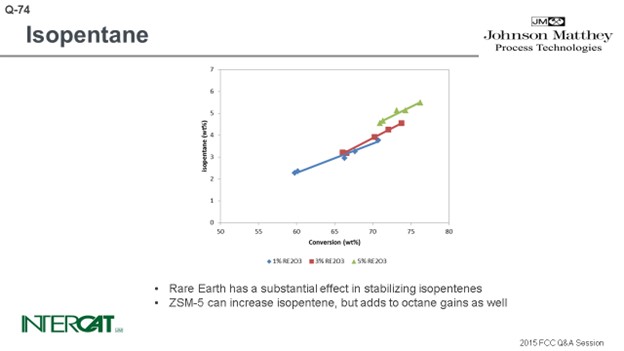
KENNETH BRYDEN (Grace Catalysts Technologies)
While the question asks specifically about isopentane production, other C5 hydrocarbons also have significant vapor pressure. Isopentane has a Reid Vapor Pressure (RVP) of 20 psi (pounds per square inch); n-pentane has an RVP of 16 psi; and, the C5 olefins have RVPs between 14 and 26 psi9. For refineries desiring to minimize RVP, it is also important to minimize the quantity of C4s in the gasoline pool since C4s have even higher vapor pressures than C5s.
Isopentane is mainly produced in the FCC unit via two pathways. The first pathway is cracking where isopentane is formed when a larger paraffin molecule cracks via β-scission to form isopentane and an olefin. The second main pathway for isopentane production involves hydrogen transfer reactions that transform C5 olefins into isopentane. Hydrogen transfer is a disproportionation reaction where hydrogen is moved between molecules. Isopentane production is influenced by operating conditions, feedstock properties, and the properties of the catalyst used. Factors that influence hydrogen transfer have the greatest impact on isopentane production.
As conversion is increased (by either increasing reactor temperature or by increasing catalyst-to-oil ratio), the quantity of isopentane (and gasoline) increases. At constant conversion, increasing reactor temperature will reduce the amount of isopentane produced, as hydrogen transfer tends to be favored at lower reactor temperatures. And since hydrogen transfer is a bimolecular reaction, decreasing reactor pressure lowers hydrogen transfer and will lower the amount of isopentane produced.
As a feedstock becomes more naphthenic, the production of isopentane tends to increase. This is because naphthenes are good hydrogen donors and react with gasoline range olefins to make aromatics and gasoline range paraffins10.
FCC catalyst can affect the rate of isopentane production through hydrogen transfer activity. As hydrogen transfer increases, more paraffins are formed and isopentane production increases. Figure 1(a) presents isopentane yields on a fresh feed basis at 72% conversion for a series of catalysts with a range of unit cell sizes (UCS) between 24.22 and 24.44 Å. To maintain similar activity, the higher UCS catalysts were formulated to a lower zeolite level. Figure 1(b) presents isopentane concentration in gasoline as a function of UCS for the same catalysts. As expected, isopentane yield and concentration in gasoline increase with UCS since the acid site density and the relative rate of hydrogen transfer to cracking is increasing.
The use of ZSM-5 based additives does not significantly change the yield of isopentane on a fresh feed basis, but it will increase the relative concentration of isopentane in the gasoline. As the higher olefins in gasoline are cracked by the ZSM-5 to propylene and butylene, the gasoline becomes enriched in isopentane. Figure 2(a) presents isopentane yield on a fresh feed basis for a series of ZSM-5 additive levels. While there is a slight increase in isopentane yield with ZSM-5 additive level, the isopentane yields are all close together. Figure 2(b) presents isopentane concentration in gasoline for the same series of ZSM-5 additive levels. As seen in the figure, isopentane concentration in gasoline increases with increasing ZSM-5 additive level.
In summary, a number of factors influence isopentane production, including feedstock, unit operating conditions, and the properties of the catalyst system used. Refiners desiring to reduce gasoline RVP should look at more than just isopentane since other C4s and C5s also contribute to vapor pressure. If catalyst changes are envisioned to minimize RVP, it is important to remember that 1) multiple objectives must be met in FCC operation and 2) careful consideration of operating objectives and unit constraints is needed when selecting a catalyst. Grace’s Technical Service team can help identify the best catalyst choice to meet refinery objectives.
BART DE GRAAF (Johnson Matthey Process Technologies)
Isopentane is one of the lightest components in gasoline. Typically, everything that increases conversion increases isopentane production. Isopentanes are formed from isopentenes via hydrogen transfer. Hydrogen transfer is a fast reaction under FCC conditions. High concentrations of zeolite in catalyst, and especially high rare earth stabilized USY, favor the formation of isopentanes. With riser outlet temperature, iC5 production increases, but mostly of the olefinic species. ZSM-5 additives can create isopentenes, which will form isopentanes after hydrogen transfer.
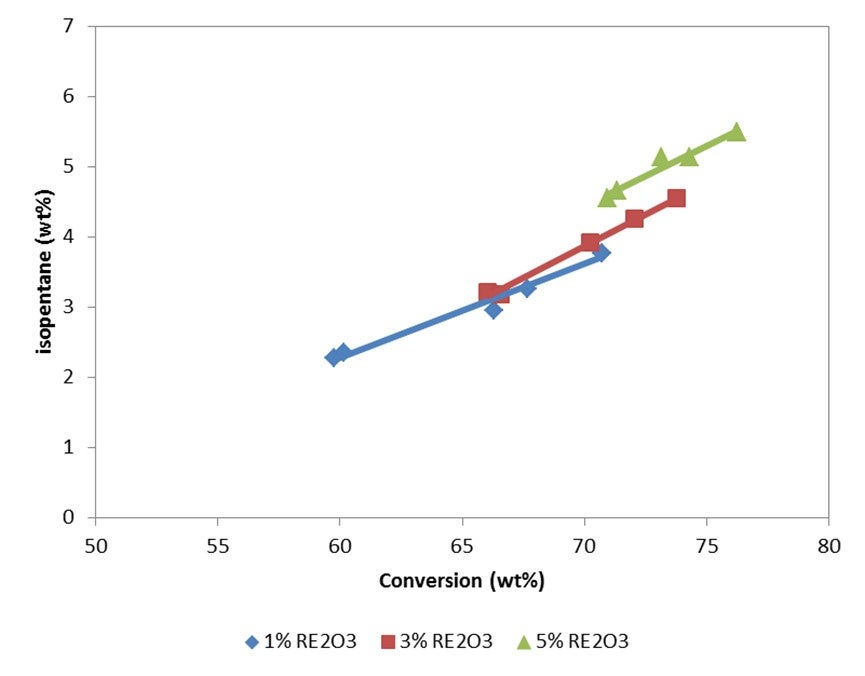