Question 74: How do you mitigate aqueous corrosion in the main fractionator overhead and gas concentration unit? What contaminants do you test for in the sour water, and what limits do you impose? What are your concerns with using stripped sour water as waterwash?
DINKEL [Marathon Petroleum Corporation (MPC)]
There are quite a few questions from previous Q&As and Cat Cracker meetings, so I will summarize them in the written response in the Answer Book section of the final transcript.
I will stress that design details are important to make sure the injection quill is designed right with the correct lengths of pipe run, as well as to confirm that your sour water handling is set up appropriately.
The commercial example I will discuss is about one of our units that, years ago, needed to increase the washwater rate to the main column overhead. We define the washwater requirement by doing ionic modeling and then setting the target with a 15°F buffer above the dew point. The required water rates would have required an overhaul of the entire overhead system, including the waterdraws, boots, pumps, and piping. Their solution was to put a staged injection into the fin fans in the overhead system. The system consists of automated valves and a PLC (programmable logic controller) that controls and sequencing through the fans. It is injecting for a set period of time on each fan bank. It goes down the line and then comes back to the front of the line. That is a way to mitigate really having to increase the amounts of sour water handling on the unit.
I will share a good example about the importance of getting the design details correct based on inspection findings during the last turnaround. We inspected those fin fans and discovered that about half of them had accelerated wall loss, which meant that there was accelerated corrosion of the tubes. The investigation aligned the different corrosion rates with a hydraulic piping difference. There was a smaller diameter piping on the wash water to the specific exchangers with higher corrosion. They were added on at a later time, and the new piping was a different thickness than the original piping. It ended up being about a 20% lower washwater rate to those fin fans; so, it is just very important to pay attention to the design details.
Regarding the part of the question about whether or not stripped sour water is used, I will tell you that we do not use stripped sour water to overhead in any of our units. However, I do not see why you could not, as long as you are monitoring your sour water containments, purging the system, and making up with a clean water source appropriately.
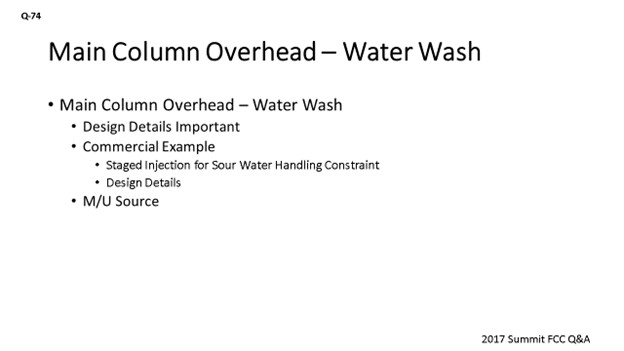
The next slide is about the gas concentration system. I will just highlight that the objective for us is to remove the water, and our preferred option is using the coalescer. We have had good success with being able to remove the water with a coalescer on the stripper feed, and we were able to dry up the debutanizer. You do not see any moisture in that overhead system, and there is the added benefit of it being energy efficient. You also end up debottlenecking that tower, so you will be reducing the loading and getting some performance benefit.
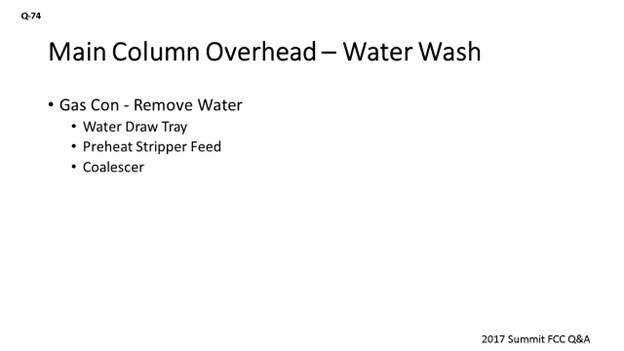
BHARGAVA (KBC Advanced Technologies, Inc.)
I want to add to what Bryan said about aqueous corrosion. The aqueous corrosion is best handled by injecting water before the fin fans and the overhead of the fractionator. Inside the fractionator, you have three deposits, including ammonium chloride. And if you have those deposits, you will not want to leave it there because you will underdeposit corrosion.
You have waterwash facilities you have seen where your clients have – on a regular basis – water-soluble and oil-soluble corrosion inhibitors, polysulfide injection to prevent the attack of cyanides by forming non-corrosive thiocyanates, and filming as means of forming a protective layer to prevent H2S (hydrogen sulfide). These are all different mechanisms that can be used to reduce the corrosion in the overhead system.
Finally, we prefer a parallel wash system to protect upstream and downstream of the wet gas compressor. If it loads the sour water stripper too much, the second option is to go over the coker and waterwash system. The countercurrent is not preferred because it creates a recycle of the cyanides from the high-pressure area to the low-pressure system.
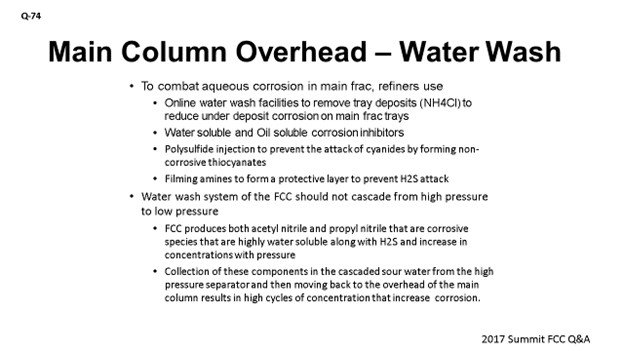
TRAGESSER (KBR)
Corrosion in FCC main fractionators can be broken down into mainly corrosion of steel by sulfides and cyanides and hydrogen blistering. Water, ammonia, and H2S – along with trace number of chlorides – are present in fractionator overhead systems. Corrosion is typically higher for units processing heavier feedstocks with high amount of sulfur and nitrogen in the feed.
Hydrogen blistering is found to be the most common concern in FCC recovery units. However, the prevention begins at main fractionator. KBR provides waterwash in the fractionator overhead system to dilute cyanides, prevent salts from building up, and control pH. We use water collected from wet gas compressor interstage drum, high pressure separator drum as wash water. In our experience, injection of this water minimizes the possibility of salt deposition on the tube surface of the exchanger. The relatively high wash water pH also helps dissolve acidic polysulfides into the water phase. Net wash water, along with the water condensed from the fractionator overhead, is rejected in the fractionator reflux drum and sent to the sour water stripper. KBR also recommends using a corrosion inhibitor in the main fractionator overhead system to prevent hydrogen blistering in the downstream section. Typically, ammonium polysulphate solution is used as corrosion inhibitor.
To further minimize the possibility of hydrogen blistering in the vapor recovery unit, we use wash water injection at both hot discharges of the wet gas compressor. The water dissolves components in the gas stream that would otherwise promote hydrogen blistering. Corrosive soluble salts are also removed by waterwashing as well. As a side benefit, the water injection also provides some cooling of the compressor discharge streams. Usually, oxygen-free steam condensate is used as the source of the wash water. Oxygen brought in with wash water can create severe corrosion.
We believe that non-phenolic stripped sour water can be used as the waterwash in the FCC. However, care must be taken as sour water from the FCC sour water stripper would usually have residual phenolic compounds. Therefore, sour water from FCC sour water stripper should be avoided.
BRYAN DINKEL [Marathon Petroleum Corporation (MPC)]
Over the last six years, there have been a number of questions related to different aspects of overhead and gas concentration unit corrosion management, including design recommendations. For completion of the Answer Book, here is a brief summary of the topics covered. Please refer to the following historical transcripts and/or Answer Books for full details:
-
2016 Q&A, Question 65: Feed property impacts, the use of chemicals for corrosion control, and whether or not waterwash is a sufficient strategy when used on its own
-
2014 Q&A, Question 95: Design of wash water nozzles
-
2014 Cat Cracker, Question 11: Recommendations for waterwash rates and locations and sources of makeup
-
2012 Cat Cracker, Question 33: Techniques for and frequency of collection of sour water samples and the specific contaminants monitored
-
2011 Q&A, Question 79: Management of chloride fouling in FCC fractionators
As discussed in these previous-year responses, MPC also uses ionic modeling to determine the salt dew point. Our internal recommendation is to set a minimum tower top temperature 15°F above the dew point. In the tower, corrosion is avoided by using a spray header reflux distributor and by limiting the minimum reflux temperature to approximately 210°F. The spray distributor allows for direct contact heat transfer prior to the top of the packed bed, which helps to avoid shock condensation.
The design details of the main column overhead waterwash injection systems are important. Some of the components that need to be reviewed carefully include the design of injection quills, recommended upstream/downstream pipe runs, piping hydraulics for the balanced flow to parallel exchangers in continuous waterwash systems, and water disposal limitations. Regarding sour water handling limitations, one option to address is a major redesign of water handling and disposal components: water boots, pumps, piping, and control valves. An alternate solution we have implemented on one of our units is batch injection of water to individual overhead fin fans, which also reduces the duty load on the downstream condensers. This staged injection of water is automated such that it cycles between the multiple fin fans, injecting water for a set period of time on each and then starting back at the beginning.
An example highlighting the need to review design details stems from these fin fans on the staged waterwash sequence. During turnaround, inspection of the fin fan tubes identified some exchangers with accelerated wall loss compared to the remainder of the fan banks. Upon investigation, it was identified that the accelerated corrosion was on exchangers with smaller wash water supply piping and a lower flow rate of filmer due to the injection point locations. For the waterwash rates alone, the piping difference resulted in about 20% lower wash water which contributed to the accelerated corrosion.
I have no direct experience with using stripped sour water as a makeup water source; however, one should be able to use it as long as contaminant levels are monitored to determine if they are cycling up over time. Ideally, a purge and fresh, clean makeup water source should be utilized to control contaminant loading. I am familiar with the use of condensate as a clean source to supplement the quantity of steam feeding forward to the fractionator from the reactor.
Regarding corrosion control in the gas concentration unit, MPC’s preference is to remove the water from the absorber and stripper feed to eliminate the water source throughout the gas concentration unit for both corrosion control and debottlenecking the stripper tower loading. Water removal can be accomplished with the use of a water trap-out tray or feed coalescers or by preheating the feed to the stripper and recycling that feed back to the high-pressure separator for another pass at removing the water. MPC has implemented each solution. Our preference is the coalescing option based on water removal performance; it is a more energy-efficient solution. We have one unit with a coalescer on the stripper feed which has resulted in maintaining the debutanizer overhead system dry.
SANJAY BHARGAVA (KBC Advanced Technologies)
In FCCs, we have general and localized aqueous corrosion due to water-soluble corrosive species; typically, H2S and hydrogen cyanide. The FCC systems also have ammonium chloride salts that deposit on the main fractionator trays and overhead prior to water injection in the overhead; thus, it is common to have wet underdeposit corrosion mechanisms. Refiners have waterwash facilities to remove the ammonium chloride from the main fractionator intermittently. Refiners also have both water-soluble and oil-soluble inhibitors as part of the corrosion control program.
Any freshwater makeup should be either condensate, BFW (boiler feed water), or stripped sour water of the correct quality. Polysulfide injection can prevent the attack of cyanides by forming non-corrosive thiocyanates. Filming amines have also been used to form a protective layer to prevent H2S attack.
The waterwash system of the FCC should not cascade from high pressure to low pressure. The FCC produces both acetyl nitrile and propyl nitrile which are corrosive species that are highly water-soluble, along with H2S, and increase in concentration with pressure. The collection of these components in the cascaded sour water from the high-pressure separator and then moving the water back to the overhead of the main column results in high cycles of concentration that increase corrosion.
The sour water should be tested for Fe, NH3 (ammonia), and chlorides.
Properly controlled sour water stripper can provide a good source of reuse water in the FCC overhead. The contained ammonia can actually assist in corrosion control in the overhead system. This practice has been done without issue but should be reviewed for a specific application at a site.
CHRIS CLAESEN (Nalco Champion)
Corrosion and fouling mechanisms are mainly governed by HCl, NH4Cl (ammonium chloride), NH4HS (ammonium hydrosulfide), and cyanide contents or formation temperatures. A good waterwash helps to control the overhead corrosion, but problems may also exist in the fractionator top. This issue can only be controlled by reducing HCl levels or by implementing a salt dispersant. Pathfinder ionic modelling will determine the formation temperatures of NH4Cl and NH4HS and help determine the actions needed to control this situation. Cyanide levels can be controlled with the use of APS. Stripped sour water is a good source for a waterwash as long as it does not introduce oxygen, hardness, corrosives, or foulants.