Question 73: Gasoline octanes continue to have a high value for many refineries. What fractionation strategies do you apply to increase gasoline octane? What rules of thumb do you apply for estimating changes in octane with gasoline endpoint adjustments?
BHARGAVA (KBC Advanced Technologies, Inc.)
There is one way to increase FCC gasoline octane for refiners who have full-range naphtha. Full-range naphtha can be fractionated into LCCN (light catalytic-cracked naphtha) and HCCN (heavy catalytic-cracked naphtha) in a separate tower; or if the HCCN is coming off the side draw of the main fractionator, it will not really increase the octane of the pool. However, it will afford the refiner one higher octane component and one lower octane component, which will provide more flexibility in the blender that is constrained by motor octane. If the constraint is aromatics, sulfur, or olefins, the additional flexibility will allow you to have a more profitable gasoline blending pool. The other traditional way of affording more blending flexibility is to remove the heart-cut gasoline fraction, which is the MCCN (medium catalytic-cracked naphtha) using a couple of towers to get the MCCN out of the FCC naphtha and then send that to a reformer in order to boost the octane.
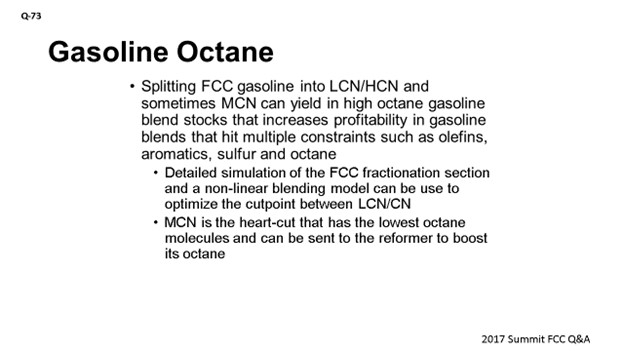
The second part of the question asked: What is the octane response as the gasoline endpoint is increased? Theoretically, you will see differences based on the octane curve. So as you keep increasing your endpoint beyond a certain point, the octane will start to drop to somewhere around 390 to 400°F. But in reality, from our experience testing refiner’s units, we know that it is very, very difficult to see an octane response when changing the gasoline endpoint in the normal range of, say, 380 to 410°F. The reason is purely the engine octane test. The reproducibility on an octane engine is about 0.7 octane number, and it is about 0.3 octane number on the repeatability test. So, if the net change you want is less than those thresholds, you will not see it. There is a lot of variation in the octanes, and you cannot really come to a firm decision on what endpoint changes to make. The other problem is that there are many other variables that affect the octane much more than the endpoint. It could be either feed quality, severity, or loss of fractionation efficiency which will change the backend of your curve on gasoline. So, our stand is that we do not really see much of an octane change in real life.
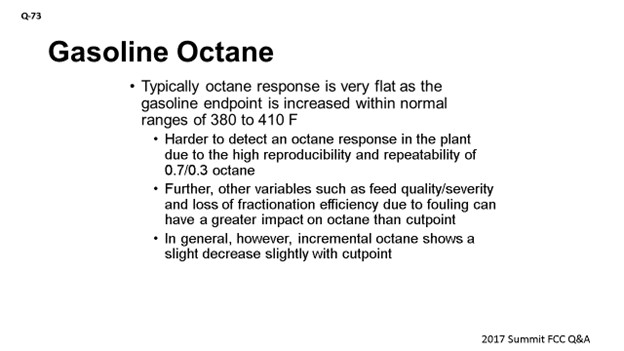
FOOTE (CHS Inc.)
All I will add is that it depends. This slide shows data from the same unit. The data on the left is operating at between 1,000 and 1500 ppm feed sulfur. The data on the right is operating between 50 and 100 ppm feed sulfur. That octane response is traditional; but as you saturate that feed more, your octane response to endpoint becomes flatter, even decreasing.
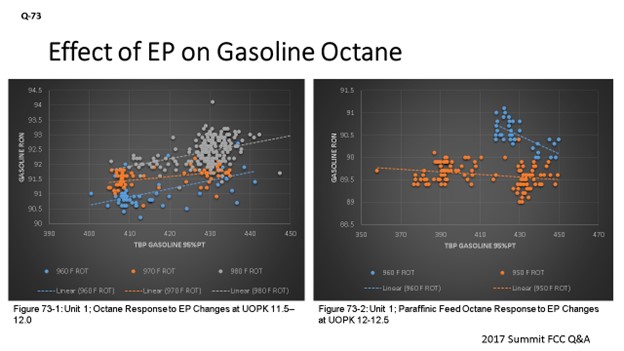
The next slide shows data from Unit #2, which operates at 50 to 100 ppm feed sulfur and which shows a relatively flatter response than the one on the left in the first slide. But actually, the MON (motor octane number) goes down and results in a considerably flat (R+M)/2. Gasoline endpoint is really not a good handle in this situation and why I say, “It depends.” So, the response is really impacted by the extent of feed saturation and the paraffinicity of your feed.
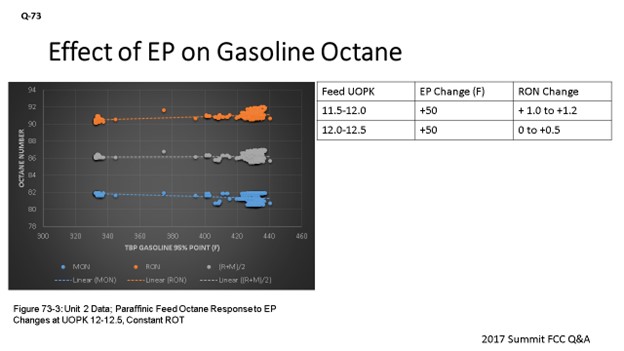
DARIN FOOTE (CHS Inc.)
RVP and endpoint both have a minor effect on gasoline octane. With other operating parameter changes and repeatability of octane results in the lab (+/- 0.5 RON), it is difficult to quantify small changes in octane caused by fractionation changes. Literature suggests that for every 1.5 psi RVP increase, RON will increase 0.3. We have very little data to support the literature, because the octane and RVP value of mixed C4s is much greater as alkylate than on the frontend of FCC gasoline. The effect of gasoline EP on octane depends on feedstock quality. For hydrogen deficient feedstocks, an increase in gasoline EP will increase RON. This relationship is shown in Figure 73-1, which represents operating data from Unit 1 at 22 to 24 API Gravity, UOPK 11 to 12, and 0.12 to 0.15 wt% sulfur. Figure 73-1 suggests a one-number increase in RON for every 50-degree change in EP.
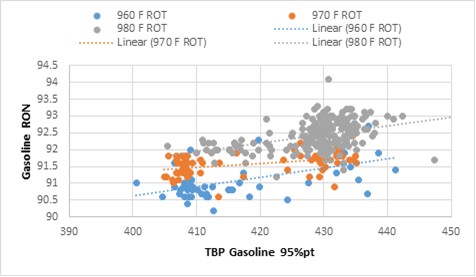
Figure 73-1. Unit 1 Octane Response to EP at Various Riser Outlet Temperatures (ROTs) for Feed Qualities of 22-24 API Gravity and 0.12 to 0.15 wt% sulfur
However, as feedstock and products become more paraffinic, the octane response to EP is less dramatic. This relationship is shown in the operating data shown in Figures 73-2 (Unit 1) and 73-3 (Unit 2). Both units are operating with a paraffinic feedstock. In Figure 73-2, the same Unit 1 under conditions where the UOPK is 12 to 12.5, API Gravity 26 to 29 showed a decreasing response in octane with EP. Data from Unit 2 (Figure 73-3), also with a paraffinic feedstock, suggests that a 50-degree change in EP will increase RON by 0.5. This figure also shows that MON is flat or decreasing, resulting in a flat R+M/2 result.
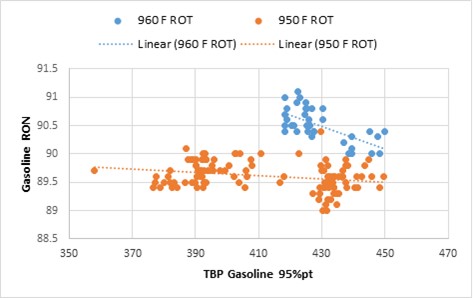
Figure 73-2. Unit 1 Octane Response to EP at Various Riser Outlet Temperatures for Feed Qualities of 26-29 API Gravity and 0.005 to 0.02 wt% Sulfur
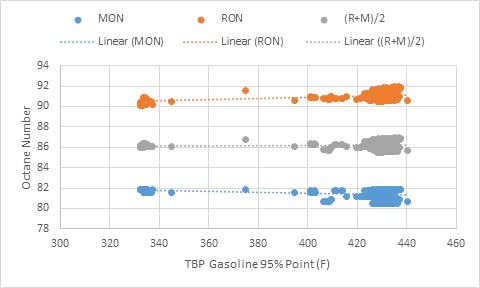
Figure 73-3. Unit 3 Octane Response to EP at Various Riser Outlet Temperatures for Feed Qualities of 26-29 API Gravity and 0.005 to 0.02 wt% Sulfur
SANJAY BHARGAVA (KBC Advanced Technologies)
Refineries use multiple configurations to split FCC gasoline into a high-octane LCCN and low-octane HCCN. The split can be made either in the main fractionator with HCCN side-draw or in a naphtha splitter downstream of the debutanizer. A detailed, nonlinear, blender model with a representative fractionation model should be used to optimize the cutpoint and fractionation between LCCN and HCCN in situations where the gasoline blender is hitting multiple constraints, such as octane, aromatics, and olefins. This flexibility results in more profitable gasoline blends.
Some refiners have an additional MCCN (medium catalytic-cracked naphtha) cut which has a still lower octane and which gets post-treated in a reformer to increase the octane of the MCCN. Removing the low-octane MCCN from LCCN and HCCN increases the octane of the remaining LCCN and HCCN.
In general, the octane response with endpoint change is very flat and hard to detect in the plant due to the repeatability and reproducibility of RONC/MONC (research octane number clear/motor octane number clear) being higher than any predicted theoretical change. Theoretically, higher octane is attained as endpoint rises but then drops on further increases in endpoint.
Hence, we have no rules of thumb between octane and endpoint of gasoline as the octane profile changes more due to other FCC variables, such as feed quality, severity of operation, catalyst, use of ZSM-5, and fractionation efficiency. Further, the octane profile can also change over the course of operation as the fractionator fouls due to salt deposition in the top of the tower.