Question 72: What are Best Practices for steam rates in cokers, heater velocity steam, valve purge steam, and drum steam out? Do newer, double-fired heater designs use less steam?
SHELTON (KBC Advanced Technologies, Inc.)
Sim Romero with KBC, who is sitting in the audience, will be conducting Coking 101 and will cover these topics. Since I am repeating Sim’s responses, I will summarize the answers. The question was about Best Practices for steam rates, heater velocity steam, valve purges, and drum steamout. It is difficult to give a rule of thumb for velocity steam, but we always find that the maximum allowable is the best.

We model the heater to determine the optimum velocity steam. The only potential limits are downstream including excess heater ΔP (differential pressure), coke drum velocity, fractionator flooding, vapor jet flooding, main fractionator overhead heat removal, and downstream sour water treatment. But pressed to give a number, we say that it is usually greater than 1 wt% (weight percent) of the heater feed, not of the fresh feed. Of course, high asphaltic crudes with high asphaltene contents require more steam to obtain the desired run-length. We use the KBC VIS-SIMTM model which predicts fouling and run-lengths based on feed quality and operating conditions.
Heater Geometry: Sim wants to point out that fouling is a function of the asphaltene deposited on the tube wall, so velocity steam increases shear forces and tends to strip off the asphaltene deposit to lower fouling. Purge steam is usually specified by the valve manufacturer to prevent the valve from sticking or leaking,
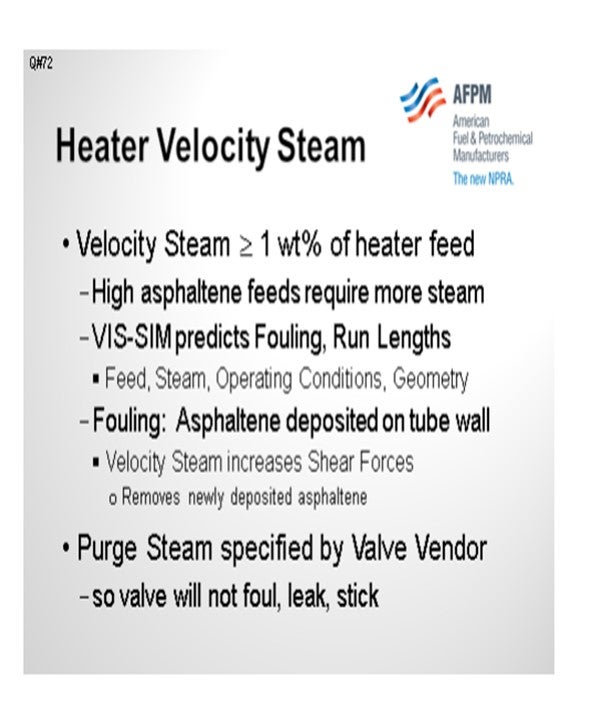
Drum Steamout: Most operating companies start slowly to avoid a disaster. Once the operation is in good shape and there is no risk of foaming, the steamout can proceed.
Fractionator Blowdown/Steamout: The rates and duration are dependent on the operation and, especially, the type of coke formed. It would be site-specific. The drum geometry would also affect the duration of steamout to the fractionator versus blowdown. Of course, the blowdown system limits may affect how long the steamout is through the fractionator and then switched to the blowdown.
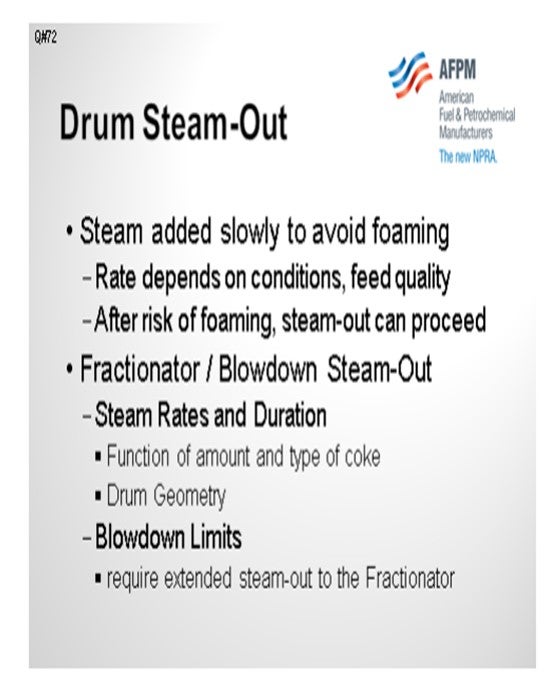
There was a question about the new double-fired heater designs using less steam. Again, we have to model the heater. We can say that if the design were 10,000 BTU/hr-ft2 heat flux for a single- versus a double-fired heater, then this would be the difference in peak temperature. The peak temperature is about 1.8 times the average flux for a single-fired versus 1.2 for a double-fired heater. In theory, if they were both designed for 10,000 BTU/hr-ft2 , then the double-fired heater would use less steam. However, we frequently see heater vendors providing double-fired heaters at relatively high flux rates.
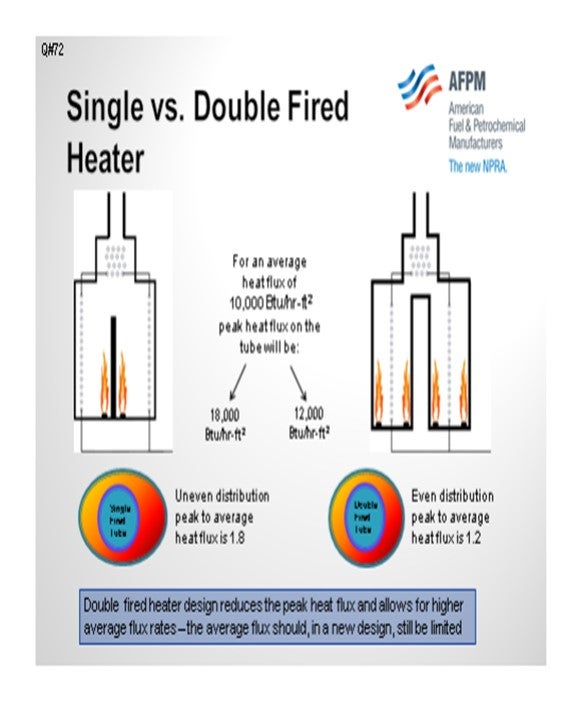
BASHAM (Marathon Petroleum Corporation)
I want to expand a little on Al’s points about double-fired heaters. In Robinson, we are currently replacing the four-pass single-fired heater with a three-pass double-fired heater. The design steam rate is about 25% less. As Al mentioned, the average heat flux is higher, which translates to fewer passes and lower steam rates that are required.
The purge steam to the valves will be dependent upon the manufacturer. For a large two-drum coker, we typically see it somewhere around 6,000 lbs/hr (pounds per hour). When you look at all of the other steam on the structure with the orifices, it could be up to 18,000 lbs/hr. Drum steamout for our large 30-foot diameter drums can be up to 30,000 lbs/hr, including steaming to both the coker fractionator and the blowdown drum. So, a considerable steam load is required.
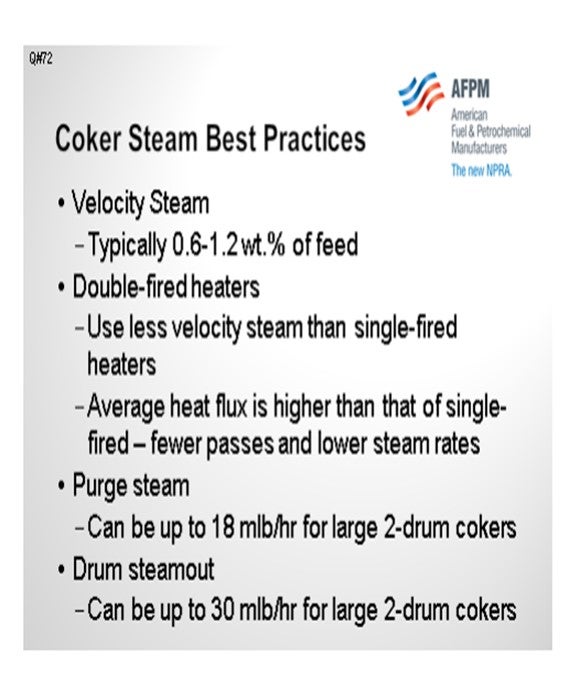
SHELTON (KBC Advanced Technologies, Inc.)
KBC’s Best Practice for heater velocity steam and valve steam is to maximize steam rates within operating limits. Potential limits to higher steam rates are summarized below.
1. High velocity steam rates increase heater pressure drop and can result in hydraulic limits.
2. Excessive coke drum velocities can cause solids carryover or foaming.
3. High fractionator velocities can cause flooding and poor separation.
4. Fractionator overhead heat removal may limit steam rates.
5. The capacity of downstream sour water treatment facilities may be limiting.
KBC has developed a rigorous thermal kinetic heater model VIS-SIMTM that predicts heater fouling and can be used to estimate run lengths based on operating conditions and heater geometries. Simulations show that velocity steam rates should be approximately 1 wt% or more of the heater feed. Steam rates are dependent on feed rate and feed quality. High asphaltene coker feeds require more steam than low asphaltene feeds at the same rate. Some operators limit velocity steam due to concerns that high velocity steam could cause annular flow in the heater. Simulations show just the opposite; higher steam rates move the operation further away from annular flow.
Fouling in coker heaters is a function of asphaltene deposited on the tube wall and stress forces tend to strip newly deposited asphaltene from the tube walls. Velocity steam increases shear forces which remove newly deposited asphaltene and reduces fouling.
The amount of valve purge steam is determined by the valve manufacturer. If minimum steam purge rates are provided for a drum switch the valve will not foul, leak or stick. Ensuring that the correct amount of steam is actually delivered to the valve can be challenging. The steam required during a drum switch can significantly increase coker steam loads. Supply steam header diameters and lengths can limit the amount of steam that can actually be delivered. Best practice is to install a steam flow meter on the total steam to the switch deck so that changes in operation can easily be monitored.
The initial steam stripping step immediately after a drum switch can cause foaming in the coke drum. Adding stripping steam must be conducted slowly and carefully to avoid foaming or re-foaming in the coke drum. This is highly dependent on operating conditions and feed quality. Once steam is fully introduced to the full drum and any risk of foaming has passed, then the steamout can progress. How much steam is required (flow rate and duration) for both the steamout to the fractionator and the blowdown is a function of the amount and quality of the coke and drum geometry. Additionally, limitations in the blowdown system may require extended steamout to the fractionator.
A double-fired heater design generally has a lower peak heat flux, but it is designed with a higher average heat flux. Additionally, a double-fired heater has a lower residence time.
The high average heat flux would imply a higher fouling rate. Without a detailed design comparison, it is not possible to evaluate whether more or less steam is required for a double-fired heater.
A poorly designed double-fired heater with an average radiant heat flux greater than 14,000 BTU/hr-ft2 or a heater operating at higher feed rates than the original design will require more velocity steam.
The effects of single versus double-fired coker heater designs on peak heat flux for an average heat flux of 10,000 BTU/hr-ft2 are shown below.
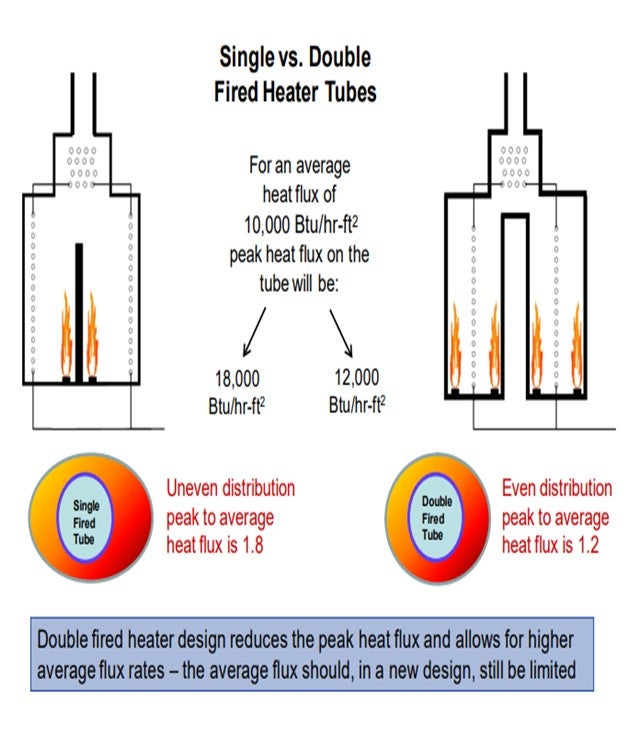
BASHAM (Marathon Petroleum Corporation)
Heater Velocity Steam: Velocity steam promotes vaporization and reduces heater tube residence time, both of which reduce the fouling rate. Optimal velocity steam rates may depend on heater design, feed composition, feed rate, and recycle rate but are typically between 0.60 wt% and 1.2 wt% of the feed. Too much velocity steam can cause high heater tube pressure drop, excessive sour water make, high coke drum velocity, and high coker fractionator loading.
At Marathon Petroleum Company (MPC), we performed test runs where velocity steam was raised from 0.60 wt% to 1.2 wt%. We saw a marginal reduction in the heater tube fouling rate, but it was not significant enough to justify the increase in velocity steam.
We are currently replacing a four-pass single-fired coker heater with a three-pass double-fired design in one of our refineries. The design velocity steam rate for the double-fired heater is 25% less than what is currently used in the single-fired heater. The average flux of a double-fired heater is higher than that of a single-fired heater for the same tube metal temperature. This means that less radiant heat transfer surface area is required (fewer passes), and, hence, lower steam requirements.
Valve Purge Steam: Valve purge steam consumption is highly dependent on valve design/manufacturer. For a ball valve with steam energized bellows, the steam consumption can be significant. Steam balances based on a ball valve manufacturer’s estimate a valve purge at around 6,000 lbs/hr for a large two-drum coker. There is an additional 12,000 lbs/hr of steam usage from the orifices around the drum structure for a total of around 18,000 lbs/hr.
Drum Steamout: The purpose of the drum steamout to the fractionators and blowdown is to clear the feed line of resid/pitch and provide a clear channel for the water to flow through. It also helps transfer heat from the coke bed to the unconverted pitch on the top of the coke drum to complete the coking reaction.
Recommended steam rates and duration will vary based on drum size, as well as coker licensor design and preference. At MPC, we currently steam the larger 30-foot diameter drums to the coker fractionator for a minimum of 30 minutes at a rate of 15,000 lbs/hr to 20,000 lbs/hr. These drums are then steam to the blowdown drum for a minimum of 30 minutes at a rate of 20,000 lbs/hr to 30,000 lbs/hr. We steam our 22-foot diameter drums at rates of 5,000 lbs/hr to the fractionator and 12,000 lbs/hr to the blowdown drum for a combined duration of 30 minutes.
LEE (BP Products North America)
Furnace velocity media [steam or BFW (boiler feed water?)] injection rate is ~1.0 wt%. The primary reason for this rate is to minimize heater fouling. At some velocity the impact of more velocity media has limited effect. Injecting BFW requires additional heater duty to vaporize the water. The same is true for steam, but the amount of duty increase is small. Automating velocity steam control to increase velocity media as the oil charge rate decreases, and to reduce velocity media as the charge rate increases, can help maintain desired coil velocity. Valve purge steam requirements are dependent on the manufacturer and type of valve. Many ball valves require continuous steam purges. The wedge plug style uses steam only when the valve is moving from one position to the other. Steamout of the coke drums is necessary to remove O2 that is present prior to warming the drum up. Purge the drum with enough steam to turn over the drum volume at least five times to get the oxygen concentration low enough to prevent hazards in the gas plant downstream.