Question 71: We have coker/cracked naphtha reboilers which foul on the shell side. How can we minimize the fouling? Are you practicing on-line cleaning in this service?
Gary Gianzon (Marathon Petroleum Company)
Coker debutanizer fouling is mainly caused by conversion of diolefins to form polymerization material. The polymerization material over time can turns into hard coke. The main cause for polymerization is high temperature of the reboiling media (above 550 F). This issue is more prevalent to units that use hot HCGO pumparound or superheated high pressure steam. If steam is used, make sure that it is desuperheated below 550 F to minimize polymerization. You can also add an inhibitor to the debutanizer feed to prevent polymer formation and reduce exchanger fouling rate. The picture below was from a coker debutanizer reboiler with heating media above 600 F (superheated 600 psig steam).
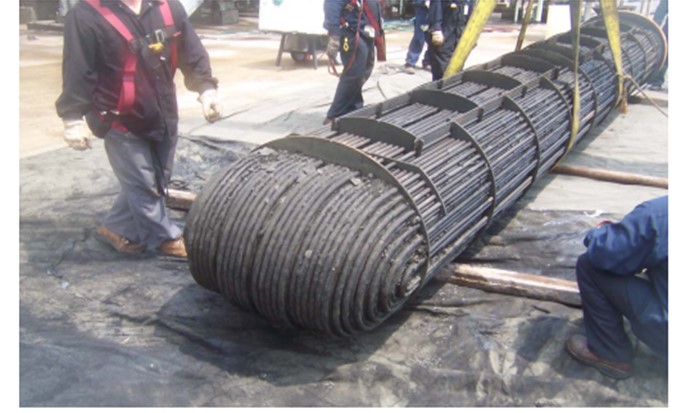
Eberhard Lucke (Commonwealth E&C)
The effect described in the question is often related to iron catalyzed diolefin polymerization caused by hot spots or local temperatures in excess of 540 to 560degF (heating medium approach temperature too high). In order to minimize fouling, a combination of the following measure will have to be applied: a) reduction of approach temperature, b) re-piping of the heat exchanger to achieve co-current flow, c) change of mechanical design to minimize low flow areas or phase separation and to reduce shell side vaporization.