Question 71: For the main column, "tri lines" can be utilized to monitor bottoms level. When other level instruments are being verified or have failed, what are the best operating and safety practices being employed to verify the level? What do refiners use to monitor and control level in the bottom of the main column?
Emerson Domingo (Sunoco)
At Sunoco, tri lines are not used on our FCC main fractionator towers but are found and used instead at some of our crude desalter vessels. At the desalters, tri lines systems also known as tri-cocks, have multiple level taps located vertically on the vessel. This is used to determine water oil interface by opening up each tap individually and visually checking the liquid that is being drained.
For all our main fractionators, we have redundancy for level indication and use a combination of at least two different types:
Nuclear, DP transmitters, and Sight glasses. Nuclear has been the most reliable as there are no moving parts and no blocked nozzles to worry about. The only time nuclear indication has been issue is if an inspection x-ray is occurring in the area. The x-ray interferes with the nuclear instrument readings.
When x-ray is occurring, we rely on our secondary level indication such as DP transmitters or sight glass. Our DP transmitter taps are continuously purged with LCO to the lower taps and fuel gas on the upper taps to keep the taps from plugging up. However, even with purging the taps tend to get plugged and occasionally need to be blown down.
Our third means of level indication has been sight glasses, but they can get greasy and black. It is common to steam out the sight glasses to get a good indication.
Another simple technique used to check level is to simply get a pressure reading on the bottom liquid line, perhaps at the pump suction, and through the use of typical specific gravity one can estimate the liquid level in the fractionator.
Alec Klinghoffer (Coffeyville Resources)
The three most common devices used to measure main fractionator bottoms level are a dP cell, nuclear gauge and an internal/external float. Typically, all three methods provide good and reliable measurement of level in the main fractionator bottoms. The only real issue with these level measurement strategies is if there is “foaming” in the bottom of the tower. This can use erroneous level measurements and additional methods can be used (flow rates and pumps operation) to make sure there is a level in the bottom of the tower. Typically, the level is controlled in tower bottoms by setting and adjusting the slurry to storage rate.
Paul Hewitt (Tracerco)
Two online methods exist for verifying bottoms level in columns – gamma scans and neutron backscatter scans. If the possibility of foaming exists then gamma scans would be better, otherwise the choice of method could come down to access and what type or length of level monitoring is required. For monitoring or verifying the bottoms level alone it is not necessary to scan the entire column. Nuclear gauge technologies are commonly used for continuous bottoms liquid level measurement in cases where other types of level control have failed due to the nature of material being processed. The main benefit of nuclear gauge technology is its non-contact design.
A radioactive source is housed in a lead filled container, which emits a collimated beam of radiation. When the vessel is empty this penetrates the vessel wall, across the inside of the vessel, through the other wall and is incident upon the detector. An angle is cut into the container that allows a specific vertical range to be covered. Figures 1 and 2 show general arrangement diagrams for the external source variation used for bulk level control, alarm and critical process shutdown. As the level of liquid in the vessel rises to the detector vertical position, it attenuates the radiation reaching the detector. This causes a decreasing pulse rate to be produced by the radiation detector, which is then converted into a 4-20 mA or digital signal.
Typical nuclear gauge instruments typically incorporate many advanced features to enable accurate and reliable level detection, including.
•Automatic correction for radioactive source decay,
•Automatic correction for changes in vessel operating pressure,
•Linear and logarithmic linearization options for level correction,
•Extensive self-checking and error reporting facilities,
•Digital Interfaces
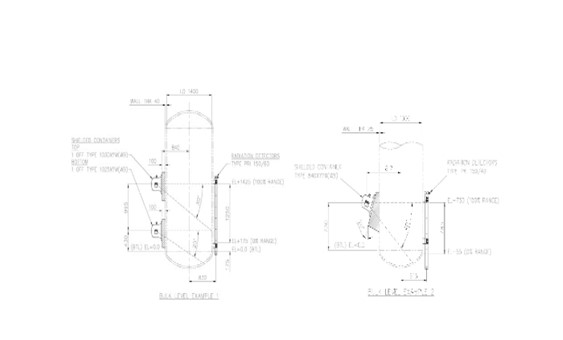
The main advantage to this technique is that the equipment is externally mounted and therefore not affected by adverse conditions in the vessel (high pressures, temperatures, corrosive liquids, abrasive solids) and can easily be retrofitted (without shutdown for externally mounted radioactive sources). The system has no moving parts and is therefore extremely reliable and requires low maintenance.