Question 71: Describe your practices for minimizing flaring and flue gas emissions during startup, shutdown, and malfunction operations?
LARSEN [Marathon Petroleum Corporation (MPC)]
Our Marathon FCCs all have a flareless startup procedure, but the type of equipment we have at our different FCCs varies somewhat. I pulled together an overview of what we have at our different plants and some licensor recommendations I learned through discussions I have had with them. I think we all agree that it makes sense, from a financial standpoint, to recover that material enough, whether or not the environmental stance is compelling us. It is just a part of being a good neighbor to the community in which we operate.
The first column you see on the slide is the wet gas compressor. Just the ability to start that machine before we put feed in the unit is a big accomplishment. In our units, we have seen FCCs with dedicated LPG vaporizers to control the molecular weight of that machine which have a little easier time. In some other units, we use a C3/C4 splitter or something like that to try and bring in LPG, vaporize it, and send it back to the compressor. It is a little harder with that setup.
And certainly, from an emissions reduction standpoint, the earlier you get the WGC (wet gas compressor) online in the FCC startup sequence, the better. I know I have been surprised before about how much material you can generate just by circulating hot gas oil through the main column and how much natural gas you have to use in the overhead system to dilute the oxygen levels to your targeted ranges. So, the sooner you can get that online, the better.
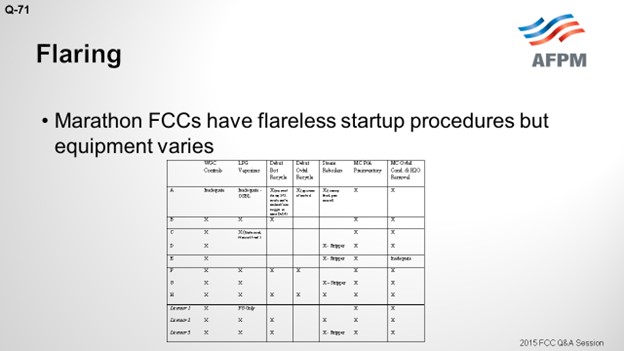
Other features we like to use include getting the gas concentration unit mostly online and recycling before we put feed in the unit. So you will see a couple of items, shown on the slide, that are able to recycle the debutanizer bottoms back to the primary absorber to establish the flow of liquid through the gas condenser. The other feature we use is the ability to get your gas con towers heated up to temperature, so to speak, to prevent any light ends from slipping past the stripper and the debutanizer and causing pressure problems and potential emissions there.
We do like to have a vent from the top of the debutanizer receiver back to the compressor. If we end up losing a few non-condensables to that area of the unit, that recycle back to the WGC gives it another chance to get to where it needs to go – that is, off the top of the absorber – in a startup to prevent any kind of flaring or overpressure situations. So, in a nutshell, that is our flareless startup sequence and recommendations.
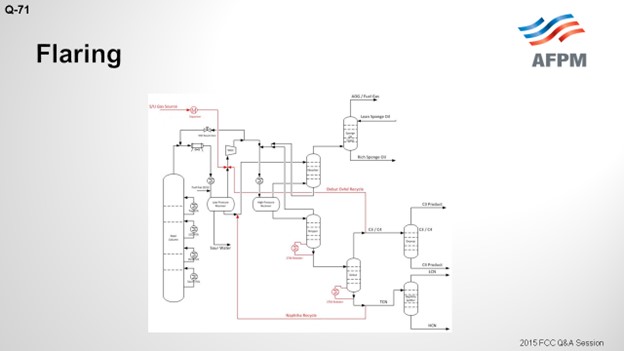
SINGH (Indian Oil Corporation Limited)
I think Nik covered most everything I wanted to say. Nevertheless, I will add a few points. We have to start the wet gas compressor (WGC) and pressure-up gas con section before feed into the riser to ensure that we are able to start the unit with minimum flaring. All of our FCC units are capable of running the WGC before feed in the unit. In case the WGC is not designed for operating prior to feed in, introducing some heavy molecular weight vaporized LPG to the WGC suction is a very good option to overcome this limitation.
Secondly, immediately after starting the FCC, routing the gas to the refinery gas network leads to a substantial amount of extra gas availability in a very short time, which may then lead to flaring from the gas network if gas consumption is not increased quickly. All of our refineries have captive power plants, so we can consume that extra gas quickly and minimize flaring. In FCC units, before the feed is cut in, there is continuous gas backup of fuel gas in the system, as well as a requirement of continuous purging of gas from the system, to avoid oxygen buildup in the system. There is, therefore, continuous flaring, which is commonly done through the very large-sized pressure control walls provided for emergency release in the event of WGC trip. A couple of units are fitted with smaller bypass valves of these large control valves, which are able to control the flaring during the startup stage.
Similarly, for streamlining the gas plant before feed in, it is absolutely essential that we have provisions to make up gas con inventory with external naphtha and bring the section as close to normal operation as possible. In our experience, using unstabilized naphtha for inventory building in the gas con section stabilizes this section very quickly. We should also take precautions to avoid any water ingress to the gas plant. If there is water ingress, it should be drained immediately, particularly from the debutanizer or stripper bottoms. There should be provisions to drain water from the lowest points; otherwise, it might take an abnormally long time to stabilize.
SANJIV SINGH [Indian Oil Corp Ltd. (IOCL)]
First, in order to reduce the flaring during startup, commissioning the wet gas compressor (WGC) and pressuring up gas condenser prior to feed in is absolutely essential. Prior to feed in, purge from the main column overhead is continued to maintain the oxygen level within acceptable limits. The WGC should be designed to operate in spillback mode with normally available gas, prior to feed in. Else, the addition of vaporized LPG to WGC suction may be provided to increase molecular weight of the gas and facilitate s WGC startup.
Apart from starting the WGC and pressurizing the gas condenser prior to feed in, the following are suggested to achieve minimum flaring during FCC startup. These should also help during plant upsets, as well as while shutting down the unit.
-
Refinery gas balance during FCC startup/upsets remains unstable. This results in intermittent flaring from the refinery gas system. Capability in the system to absorb wide fluctuations in fuel gas generation would help. Switching fuel between fuel gas and fuel oil in a captive power plant is a common practice followed by IOCL.
-
The WGC suction/main column overhead is equipped with a pressure release control valve to release gas to flare in the event of sudden pressure buildup/WGC trip. These valves are typically large in size and using them for purging during catalyst circulation stage amounts to unwarranted purge to flare. Having a smaller sized control valve for this stage is useful. Please note that incorporating this equipment helps reduce flaring but does not completely eliminate it. Minimal flaring is still required to prevent the buildup of O2 that is entrained with the catalyst.
-
From a reliability point of view, our preference has been for steam-driven WGCs over motor-driven gas compressors. Adequate actions are taken to ensure high reliability of the machine.
-
Stripper and debutanizer reboilers typically use circulating streams from the main column. The provision of backup steam for these reboilers helps streamline the gas plant early.
-
Adding a startup line to bleed noncondensables from the debutanizer overhead receiver to the main column overhead receiver is found to be useful in minimizing flaring.
-
The provision to inventory the gas plant with naphtha and establishing flows through liquid circuits prior to feed in have both been found to be very useful in streamlining the gas plant quickly. Almost all of our units have this provision.
-
Water carryover to the gas plant to be avoided at all times, especially during startups and upsets. Common sources are boots of the main column reflux drum and HP separator. It should be detected quickly for corrective action. A provision should exist to drain water from the bottoms of the stripper and debutanizer reboilers where the water tends to accumulate. Difficulty raising the bottoms temperatures of these columns may be an early indication of abnormal quantity of water ingress to these columns.
NIKOLAS LARSEN [Marathon Petroleum Company (MPC)]
All of MPC’s FCC units have a flareless startup procedure in place, but the equipment used to do so varies. Minimizing flaring during startups on the FCC is desirable from both a financial perspective as well as an environmental standpoint. The recovery and placement of hydrocarbons from the flare into the appropriate product stream provides value. The minimization of flaring also adds value, in terms of reduced environmental impact. MPC’s preferred practice for minimizing flaring and emissions during startup encompasses the following:
-
Pre-Inventory of the Main Column Pumparound (PAR): Pre-inventory PAR circuits with appropriate range material to allow pumps to be started and provide immediate cooling when required. This step improves control of the main column overhead temperature during startup.
-
Main Column Overhead Steam Condensing and Water Removal: There needs to be adequate condensing and pumpout capacity to condense and remove all steam coming from the reactor.
-
Wet Gas Compressor Startup: Advanced surge controller configuration with spill backs and WGC design allows operation on total recycle. The WGC is started prior to feed being introduced.
-
Dedicated Gas Source Vaporizer with Controls: We typically desire a C3- or C4-rich gas source that can be vaporized in a dedicated exchanger. The required gas source will be dependent upon the WGC design and required MW (molecular weight) of the material. Appropriate indications and automatic controls provide the flexibility to put the equipment in service and then turn attention to other aspects of the startup.
-
Pre-Inventory of Gas Condenser Towers and Drums
-
Naphtha recycle from debutanizer bottoms to absorber: This allows liquid from the debutanizer bottoms to be pumped back to the front end of the gas con, which allows for pump and instrumentation checkout and to put towers in auto prior to charging feed to the riser(s). This is the preferred option to pre-inventory.
-
Batch naphtha to gas con: If unable to circulate the gas con, capability to batch material to the overhead receiver and pump forward to establish levels in towers and drums for instrumentation checkout is preferred.
-
Debutanizer Overhead Recycle to WGC: This process prevents flaring from the debutanizer by allowing for noncondensables in the gas con to be reprocessed and purged from the system via absorber off gas product.
-
Gas Con Reboilers: The reboilers allow the gas con towers to be heated up during startup of the unit, prior to introducing feed. The preferred option is a steam reboiler, particularly on the stripper, that allows the tower to operate independently of the main column pumparound. Another option being used within the MPC system is to utilize jumpers to route slurry into other PARs (pumparounds) as a heat source for gas con reboilers.
Summary of Recommended Equipment and Practices for MPC FCCs and Licensor Recommendations
|
WGC Controls |
LPG Vaporizer |
Debut Bottom Recycle |
Debut Overhead Recycle |
Steam Reboilers |
MC P/A Pre-inventory |
MC Overhead Condensation & H2O Removal |
A |
Inadequate |
Inadequate - OSBL |
X (not avail. during S/U; need transfer method from stripper to main DeC4) |
X (upstream of coolers) |
X (running blind, poor control) |
X |
X |
B |
X |
X |
X |
|
|
X |
X |
C |
X |
X (Undersized, Material Avail.) |
|
|
|
X |
X |
D |
X |
|
|
|
X – Stripper |
X |
X |
E |
X |
|
|
|
X – Stripper |
X |
Inadequate |
F |
X |
X |
X |
X |
|
X |
X |
G |
X |
X |
|
|
X – Stripper |
X |
X |
H |
X |
X |
X |
X |
X |
X |
X |
Licensor 1 |
X |
FG Only |
|
|
|
X |
X |
Licensor 2 |
X |
X |
X |
|
X |
X |
X |
Licensor 3 |
X |
X |
X |
|
X – Stripper |
X |
X |
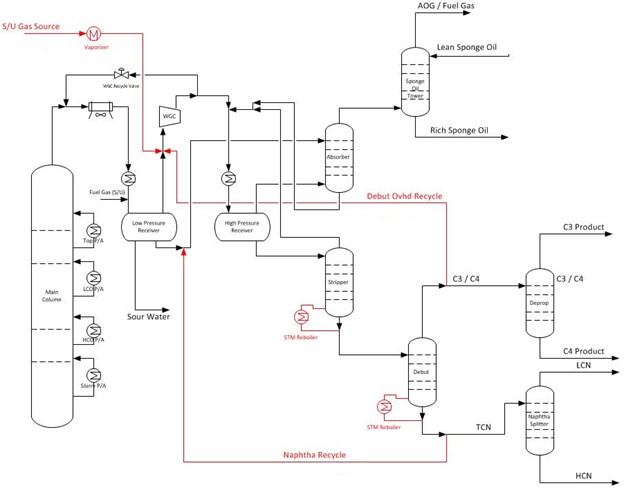