Question 70: What are your experiences with processing oil sludge in the delayed coker?
BASHAM (Marathon Petroleum Corporation)
One of our delayed cokers does process crude rag layer draw, wastewater sludge, and oily water. I think they primarily process the crude rag layer, however. What we do here is introduce the sludge after we have steamed the coke bed and established the quench water flow. We then temporarily remove the quench water to allow the sludge injection, and then we maintain a minimum temperature – I think it is around 600°F – to ensure that no oil accumulates in the cutting water. We also have to take a look at the cutting water to check for any emulsion. If it is milky-looking and has a foul odor, then we know we probably have either too much injection or our temperature is too low.
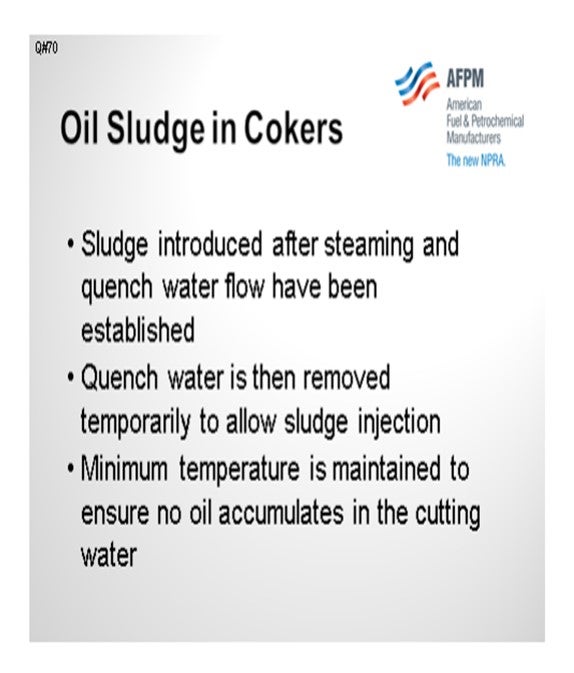
TRAN (Houston Refining LP)
We do a similar process at one of our delayed cokers at the Houston Refinery. I want to add that we have experienced hot drums issues due to sludge processing the slurry. When we did the particle size distribution, we found that the volume of solids in the water injection was higher than typical, as was the size itself. We mitigated it by reducing the injection rate and the number of solids in the slurry mixture, and then requested that the site itself grind it down a little smaller.
MIKE FINK (CITGO Petroleum Corporation)
What sort of limits do you put on percent oil and percent solids?
TRAN (Houston Refining LP)
We try to keep the solids to under 1%. In terms of micron size, the majority of it is typically below 25µ (micron). The whole range is up to about 100µ.
AHMAD AL-JEMAZ (Kuwait National Petroleum Company)
Can you still maintain anode-grade qualities affecting the sludge in the coker?
BASHAM (Marathon Petroleum Corporation)
Yes, we can.
TRAN (Houston Refining LP)
We do not have any experience producing anode-grade coke.
AHMAD AL-JEMAZ (Kuwait National Petroleum Corporation)
What are the specific parameters that you monitor in the sludge to avoid affecting the coke quality?
BASHAM (Marathon Petroleum Corporation)
As Don mentioned, some of the parameters are particle size and amount of sludge being injected. You also have to watch the minimum temperature, as I mentioned. That is all the experience that we have on it. We do not do a lot of injection, but I am not aware that we have had any coke quality issues. The primary concern is the effect on the cutting water.
BASHAM (Marathon Petroleum Corporation)
One of our delayed cokers processes a crude rag layer draw, wastewater sludge, and oily water. These components are processed after steaming and establishing flow with the quench water. Quench water is removed temporarily to allow injection of the sludge. After the sludge injection is complete, quench water is reintroduced. To minimize the potential for accumulating oil in the cutting water, the amount processed and the minimum temperature of the coke drum minimum temperature are both regulated.
TRAN (Houston Refining, LP)
We process slurry between the steam stripping and water quench steps. We limit the slurry injection amount based on the coke drum outlet temperature. The slurry stream contains solids which can cause reliability issues on pipes and pumps. We have also seen coke bed plugging issues that have resulted in hot drums and fallout. Some of coke morphology issues have been alleviated by reducing the slurry injection rate, the solid amount in the slurry, and the solid sizes.
LEE (BP Products North America)
We have some experience with quench injection as a method of recycling sludge in the coker. This involves injecting it with quench water at the beginning of the coke cooling step. To minimize problems and maximize sludge processing a refiner should: Prepare the sludge to have little or no free oil and small particle sizes (usually performed by an experienced contractor; centrifuge to recover free oil and grind to obtain small particle sizes), and strictly limit the amount of sludge injected (usually limited by a combination of time, quantity and/or drum temperature). It is important that the sludge injection is discontinued at a drum outlet temperature of not less than 550ºF to insure the oil is recycled through the blowdown system. If not done correctly, sludge processing on the coker can contribute to severe odor problems when the drum is opened and with the coke in storages, problems with drum cooling if the sludge particles are too large (can contribute to water channeling and subsequent hot spots/eruptions), problems with draining the coke drum prior to decoking, and increased coke toxicity and industrial hygiene issues.
Active drum sludge coking is another option where this sludge is slurried with oil and injected into the coke drum during the coking phase. BP has one site that does active drum sludge injection through the top of the drum. Sludge injection during the coking phase takes up some coker capacity. Typically, there are not the same problems with odorous coke. Injection rates need to be as low as possible to prevent lowering the drum overhead temperature and increasing coke make and preventing the coking reaction temperatures from being too low. Sludge injection should be discontinued approximately three hours prior to the drum switch to get the drum outlet temperatures up to convert any unreacted material.