Question 70: Electrostatic precipitator (ESP) fines handling is often complicated by fluidization and mechanical integrity issues. How often do you experience these types of fines handling issues, and what are some of your Best Practices to successfully mitigate these issues? What are your Best Practices for safe fines withdrawal from the ESP?
FOOTE (CHS Inc.)
Unreliable ESP dumping can lead to shorting out of the transformer rectifiers and the associated missions troubled by losing a cell of your ESP. Also, inconsistent dumping can put operators directly in harm’s way just since they are not consistent in the way they dump; and then indirectly, if the dumping leads to unit shutdown which will expose them during the shutdown. So, reliable operation of those hoppers is important.
At CHS, we have two dry ESPs on both of our operating units. We have not really noticed a difference. That catalyst morphology has much to do with whether they dump or not; but it is an unrefined operation, so I cannot really speak about it. What I can tell you is that as you let the catalyst accumulate in that hopper, it forms an insulating barrier. The thicker that insulating barrier gets, the more chance you will have for a temperature gradient across that barrier to be less than the bulk temperature of the ESP. So, as you let it build, the likelihood of condensation increases dramatically. Condensation is the leading cause of catalyst hopper issues.
Now I will talk about the importance of proper design and operation of ESP hoppers to ensure that they dump correctly. Insulation is important on your hoppers. Pay very close attention to manufacturer’s recommendations around the corners. The contractors will often get that wrong. Also, check that the heater grids are properly installed: the strike plates, level indicators (typically nuclear), and vibrators you use for evacuating the hopper. We also have fluffing nitrogen connections above the knife gate valves that may help get catalyst moving. We have never used them, but they are there.
Regarding the operation, do not let catalyst accumulate in the hopper. Empty each hopper early and often; and when there is an upset, empty the hopper more often. You cannot do it enough. Pay attention to the sensory indicators. A good operator can tell if the hopper is empty or not if it is not rattling right. Utilize strike plates to hear the difference between the sound of an empty drum and a full one. Next, monitor those hopper temperatures; and then, do grid checks. These hopper heater grids have multiple patches. You can lose one patch and have a cold spot, so make sure you are checking each one of those grids on a regular interval: maybe quarterly. I think we do ours every six months. We check those grids to ensure they are working right before the winter hits, because they can short out. We have lost patches and been able to catch it that way. The bulk temperature of ESP inlet at 425°F or greater. If you are too aggressive on your sootblowing activities for your waste heat boiler, sometimes you will get that temperature a little too cold. The ESP does not perform well when the flue gas is too cold.
DINKEL [Marathon Petroleum Corporation (MPC)]
I agree with Darin’s points about making sure your hopper heaters are working and not allowing the hoppers to back up. I will add a strategy we use internally. One of the newer units is doing biannual PM (particulate matter) audits with the manufacturer coming in to perform a complete review of the ESP, including looking at all the cells and basically going through and tuning the cells to optimize performance. On an older unit that we just retired last year, we got to the point where we were doing quarterly audits on it to make sure we could maintain our environmental compliance.
FEDERSPIEL (W.R. Grace & Co.)
We looked at what could be complicating fines handling out of an ESP. We might be able to break that down into some mechanical integrity issues where it is possible that internal abrasion is impacting your ability to offload due to long-term operation. If the valve fittings were misaligned due to thermal cycling, or if catalyst particles fouled the seats of the valve guides, then that might also impact your ability to withdraw the catalyst. I think this is the first time the panelists are going to disagree. I get to say that catalyst PSD (particle size distribution) and morphology, I believe, do play a role in the ability to move those fines material out just by the fact that an irregularly shaped particle has a higher surface area. And because these are fines, you know the surface area-to-mass ratio is a little higher and gets a little more cohesive as we increase that surface area to mass ratio.
The last part of the question is about safe handling. Using proper PPE (personal protective equipment) is going to include goggles and a face mask. Also, make sure you are properly grounded before any operators to do anything with the ESP.
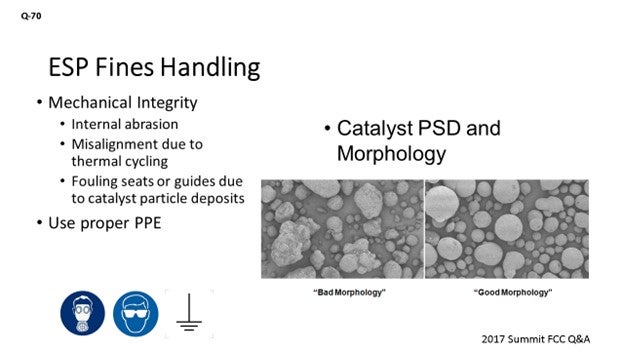
MICHAEL FEDERSPIEL (W.R. Grace & Co.)
Electrostatic precipitators (ESPs) represent an effective medium for particulate emissions control and are, therefore, commonly used within the FCC industry, especially in North America. Although ESPs are not designed to capture all of the catalyst particles present in the regenerator flue gas, they usually exhibit sufficient performance to successfully reduce the particulate content in the flue gas below 50 mg/Nm3. As the question suggests, fluidization and mechanical integrity issues can significantly hinder the withdrawal and handling activities of catalyst fines.
With respect to mechanical integrity, the most common issues correspond to malfunctioning catalyst discharge valves to the collection hoppers due to any of the following causes, among others:
- Internal abrasion throughout long-term operation,
- Misalignment of the valve fittings due to thermal cycling, and/or
- Fouling seats or guides due to catalyst particle deposits.
The electrode and collection plate rappers can also experience mechanical integrity issues that can significantly hinder catalyst withdrawal efficiency. These mechanical rappers help maximize the recovery of the ESP fines while properly preserving electrode efficiency and performance throughout long-term operation. Complete failure, or suppressed performance of these rappers, generally reduces the number of fines withdrawn from the system at constant particulate loadings and can significantly shift the particle size distribution (PSD) of the withdrawn fines towards a coarser profile. The reduced capability of withdrawing fines is usually accompanied by gradual increases in particulate emissions at the stack beyond the normal or allowable ranges. The mechanical integrity of the rappers can be affected by thermal cycling over time, as well as fouling issues stemming from the ingress of fines.
Operating conditions also influence the mechanical integrity of the ESP. Sudden thermal cycles, such as those associated with an emergency trip of the unit or sudden bypass of the ESP train, can increase the threat of mechanical integrity deficiencies associated with buckling or thermal expansion. Electrical or pneumatic supply deficiencies have also been reported, although they can be mitigated through redundant supply systems and/or onsite spare parts for the critical components. These types of mechanical failures have generally exhibited frequencies of zero to five times per planned turnaround cycle. Other mechanical or electrical supply issues are also commonly reported, but these tend to impact ESP performance to a much greater extent than the capability of handling fines.
The morphology and PSD profiles of the ESP fines will have a strong impact on the fine's withdrawal efficiency. Cyclone performance within the regenerator plays a major role in ESP performance and the corresponding fluidization properties of the ESP fines. Healthy cyclone operation typically results in average particle sizes (APS) in the range of 15 to 30 microns, depending on the regenerator design and overall hydraulic profile. Adequate cyclone performance helps maintain a manageable particulate loading to the ESP while sustaining a healthy PSD profile for the ESP fines. Excessive loadings to the ESP, over an extended duration, can have the following impacts:
- Increased erosion of the internal ESP components and fines withdrawal fittings.
- Increased quantity and APS (in the absence of catalyst attrition) of the ESP fines, which can improve fluidization of the withdrawn fines, but hinder overall capability due to the higher amount of material; and/or,
- Inadequate cooling of the ESP fines before the collection bins become full, which can constrict logistics during operation.
Excessive attrition within the reactor-regenerator system or the regenerator flue gas train can significantly reduce the APS of the fines, essentially increasing the concentration of microfines and fractured particles. These microfines and fractured particles tend to agglomerate, preventing smooth flow of the ESP fines into the collection hoppers. This type of fluidization issue is more prevalent once the APS of the fines drops below 15 microns. The jagged edges caused by catalyst fracturing can be identified by SEM analyses of the ESP fines samples. Even with a healthy PSD profile in the fines, agglomeration can occur due to other flue gas system failures, such as a flue gas cooler leak. The steam and boiler feed water in contact with catalyst fines can quickly lead to undesired catalyst agglomeration. Further, in extreme cases, acid dew point corrosion may be observed. These types of flue gas cooler leaks can be detected through sudden increases in the process-side pressure and much higher metals deposits on the ESP fines than those of the circulating e-cat inventory. The affected flue gas cooler tubes, or banks, should be isolated as quickly as possible to mitigate further erosion and downstream issues.
With respect to safe handling of the ESP fines, the industry Best Practices involve adequate use of PPE and easily accessible manifolds for the fines withdrawal system. In addition to the standard PPE requirements for refinery operations, fines handling activities should be accompanied by safety goggles, a respirator mask, and adequate equipment grounding facilities.
BRYAN DINKEL [Marathon Petroleum Corporation (MPC)]
Within the MPC system, we have only one operating unit with an ESP and we utilize gravity dumping into roll-off bins. This ESP is a relatively new piece of equipment that followed recommended design guidelines from the manufacturer. We do not have handling issues, as long as hopper heaters and vibrators are maintained. As a precaution, we have the equipment manufacturer conduct biannual field assessments to perform preventative maintenance (PM) and assurance that the equipment is functioning properly. During the design phase of a TSS (third-stage separator) project, MPC funded a hopper study that was completed by Jenike & Johanson. The goal was to optimize hopper selection and design angles based on their own analysis to determine physical properties of the catalyst fines. This strategy could be applied to ESP hoppers as well.
We recently retired a unit that had an old ESP which had design, maintenance, and operational deficiencies. That unit battled frequent issues with elevated opacity due to hoppers backing up. A hopper backing up poses multiple risks to the ESP performance, including being the cause of breaking wires, shorting out cells, and re-entraining fines into the flue gas flow path. A focused response was implemented to address these failures. We utilized quarterly preventative maintenance audits to resolve most of the issues. These audits included onsite electrical engineers, I&E (instrumentation and electrical) technicians, Operations and Maintenance personnel, and the equipment supplier. Key findings included the following:
- Hopper Heaters: The majority were not functioning, which allowed moisture to condense in the hoppers. The mix of catalyst fines and moisture resulted in plugging in the hoppers, an inability to properly empty the catalyst to the roll-off bins, and backed-up catalyst into the ESP. These were repaired to keep the temperatures hot.
- Hopper Levels: The manufacturer recommended installing hopper level indicators to keep from running catalyst levels too high. The short-term solution implemented was to increase the frequency of operator rounds to dump hoppers into the roll-off bins.
- TR (Transformer/Rectifier) Tuning: Quarterly re-tuning of voltage to TRs was completed to optimize collection efficiency.
- Roll-Off Bins: Attention to detail was elevated regarding connections from the hopper into the roll-off bins and the integrity of bag filters on the roll-off bins to keep the catalyst fines in the enclosed system.
- Cell Design Dimensions: With rate increases over the years, the equipment no longer met the recommended design aspect ratio from the manufacturer, resulting in less than the recommended residence time. A recommendation was made to replace the equipment to address this problem. Talk to your manufacturer about his/her recommended dimensions relative to your operating conditions.
DARIN FOOTE (CHS Inc.)
At CHS, we have dry ESPs on both of our operating units. Both utilize gravity dumping into contained roll-off bins.
Our experience is that catalyst fines content or morphology does not have a noticeable effect on whether or not ESP fines will dump from the hoppers. Catalyst that is allowed to accumulate in the hoppers can act as an insulator to the bulk temperature inside the ESP. As the accumulated catalyst piles up, the likelihood of condensation increases near the wall. Condensation is the most common cause of catalyst dumping problems. The following are important elements of design and operation that help ensure safe and reliable hopper evacuations.
Design
- Insulation: Proper insulation design is essential. One common pitfall is for insulation contractors to ignore the manufacturer’s insulation standard around corners, creating cold corners.
- Heater Grids: Ensure that properly sized hopper heater grids are installed correctly.
- Strike Plates: Confirm that strike plates are accessible and used on a regular basis.
- Vibrators: Check that they are installed to the manufacturer’s standard.
- Level Indicators (typically nuclear): Confirm that they are installed properly and accessible for maintenance.
- Fluffing Nitrogen Connection above the Knife Gate Valve: Use this option as a last resort to resolve dumping issues. We have these connections but have never used them.
Operation
- Do not let catalyst accumulate. Regular hopper evacuation is essential during normal operation. Frequencies should be increased around startup, shutdown, and malfunction events.
- Pay attention to sensory indicators when dumping. Seasoned operators can tell an empty hopper by the sound of the hopper vibrator. If you suspect an incomplete evacuation, use the strike plates and/or fluffing nitrogen connections.
- Monitor hopper temperatures regularly.
- Do regular electrical checks of the hopper heater grid to ensure that all circuits are working.
- Verify that ESP bulk inlet temperature is at least 425°F. If your sootblowing program on the regenerator waste heat boiler is too aggressive, this practice can decrease the bulk inlet temperature and increase the likelihood of condensation.