Question 7: What must a refiner consider when evaluating mild hydrocracking) as a way of increasing diesel production in his/her gas oil hydrotreater?
CARLSON (Criterion Catalysts & Technologies)
For grassroots design, developing the project scope and your considerations can actually be a lot easier when starting with an empty plot space. However, for existing hydrotreaters, there are a lot of significant considerations that need to be reviewed if you are considering moving to mild hydrocracking operation, as it is usually not just a drop-in catalytic solution.
The first consideration is how the mild hydrocracking operation mode is projected to impact your overall refiner configuration and operations and what revamp scope will be needed to get that level of performance. Increased hydrogen demands, reduction of FCC VGO feed, and product quality targets all must be evaluated to ensure that facility-wide economics support the proposed project. In most cases, FCC conversion benefits require feeds to be available to maintain FCC capacity.
Instead of going for mild hydrocracking, often just optimizing your FCC pretreat operations or improving the fractionation on the backend can provide quite a bit benefit without going down the mild hydrocracking route.
However, if you are going for mild hydrocracking, the second consideration will be determining your targeted operation. This includes developing the project scope and requires an evaluation of different catalyst systems and their yield impacts on the refinery, their respective cycle lives, and how all of this information fits together, all of which is largely dependent on the individual design and configuration, feed types, and contaminant levels.
Other Considerations: There will be additional naphtha production. We would like all volume yield gains to be incremental diesel, but you are going to produce some naphtha which will have to find a home in the refinery somewhere. The FCC pretreat, by itself, is also going to have significantly shorter cycles. Typically, these cycles are halved. But again, that depends on your starting point and the kind of FCC pretreat unit you have.
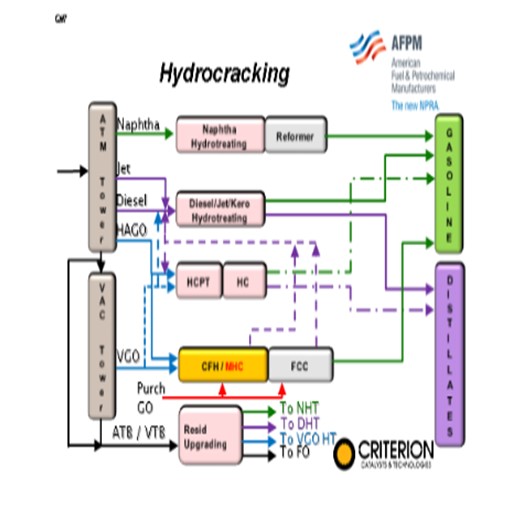
Catalyst system design considerations depend on your conversion targets, the selectivity needs for this to work in your refinery, and your existing equipment. In specifying an MHC (mild hydrocracking) catalyst system, remember that the balance of hydrotreating versus cracking catalyst and the potential addition of reactor volume are largely influenced by feed qualities and the desired level of conversion. As many of the feeds processed are high in contaminants, the pretreat section is required to ensure that a sufficient cycle life can be maintained while both meeting any product targets and minimizing nitrogen slip into the cracking section of the reactor.
HDS (hydrodesulfurization) functionality is going to remain an important criterion for some people. However, HDN (hydrodenitrification) capability is often more important as it is going to influence the cracking catalyst selection and performance due to the nitrogen slip, which really is going to end up dictating the type of long-term conversion benefits that will occur during the operational cycle.
You can look at a lot of different catalyst systems, such as those outlined on the slides. Zeolite-containing products provide the highest level of conversion but tend to be more sensitive to the nitrogen slip, which can limit their long-term cycle performance. You can go to amorphous silica-alumina (ASA), which has more nitrogen capability and tolerance, but which tends to achieve a lower level of conversion. Also, if you have units with very high levels of nitrogen in the feed or relatively low capability for HDN performance, then you can actually consider using conventional hydrotreating catalyst and just operating in a mild hydrocracking mode of operation. This mode will give you lower conversion; however, for a lot of units, it can still provide significant benefits.
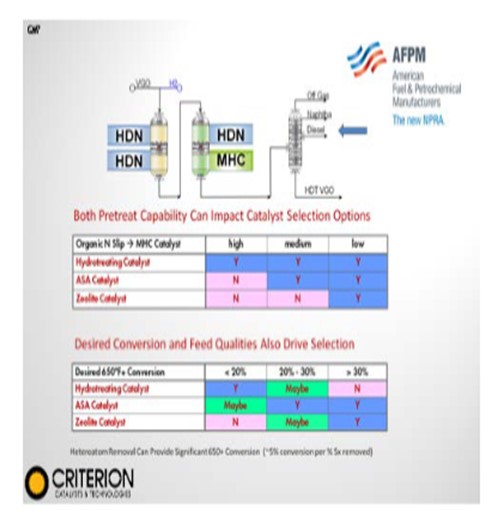
Once the facility economics are confirmed and the conceptual scope of the revamp has been determined, the detailed unit design considerations will need to ensure the safe, effective, and reliable long-term operation of the unit.
Although operation using only the existing reactor volume offers a capital advantage, it can also have technical and economic considerations. The relevance of these constraints varies from refinery to refinery; therefore, careful technical and economic evaluation is advised before converting the unit operation. Several design issues should be fully considered, including:
•Reactor internals capability
•Fouling abatement and pressure drop mitigation
•Reactor instrumentation and control needs
•Reactor bed sizes (are they too long?)
•HS&E procedure development.
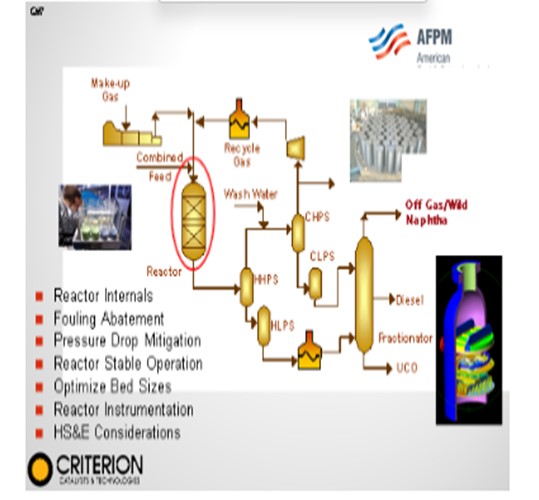
In a revamp design, significant changes to unit heat balances and flow regimes will impact the downstream recovery and fractionation section of the unit. Product separation capabilities may be a serious issue, depending on existing configuration. If a fractionation section is in place, a tower internals revamp, by itself, can often provide a low-cost solution to the increased diesel production. With this operational shift, the increased conversion will also result in more vapor traffic that needs to be accommodated in the safe operation of the unit. Final considerations also include any additional requirements for waterwash, gas treating, and metallurgy upgrades.
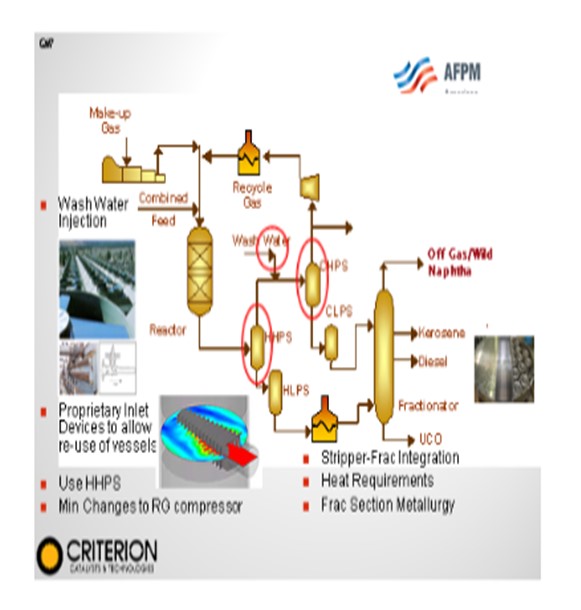
BODOLUS (CVR Energy)
Kevin covered a lot of these issues, particularly on the catalyst change, type, and amount. Hydrotreating catalyst alone might not give enough cracking, and hydrocracking catalyst may give too much if you just want to take that short little step from diesel production in a gas oil mild hydrocracking. Of course, as hydrocracking increases, the reactor dynamics change again. You need better temperature management. You may need to supply more hydrogen, if not a lot more hydrogen, and you must manage that hydrogen for both consumption and quench purposes.You have to be able to handle the product light ends, as well as heavier ends. Remember, if that product is a diesel product coming out of a mild hydrocracker, then you have to be careful about meeting your specifications for ULSD and/or cold flow properties.
In general, my recommendation is to involve the catalyst vendors, and that is plural. I suggest you go to multiple vendors. They do not always like a three- or four-way horse race, but it often provides you with a little more of an idea of where you might be.
Economics to consider, as mentioned, are a hydrocracker and an FCC, kind of two pumps for the same well. You have to be careful about the competitive economics with the FCC as you encourage more mild hydrocracking. Also, consider rationalizing the naphtha production because of hydrogen supply as a result of that naphtha production.
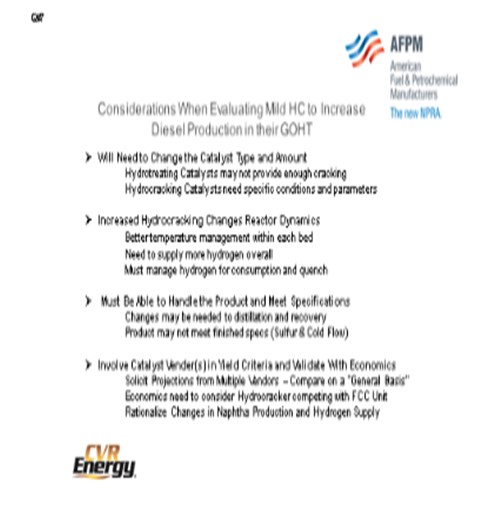
I want to briefly go through some of a case study. This slide contains a collection of data that we obtained from four catalyst vendors on different yield slates for a particular mix that we were considering. This was early on in the project. To get started, we narrowed it down, normalizing the data, and put together a single-range graph to frame up the options on the first round. As you go up in volume swell on your product, you make more potential revenue. This is net revenue on the refinery after taking most things into consideration over the cat as well. Of course, as you climb up this money line with more hydrogen consumption, as shown on the right-hand side, you can get an idea where you are.
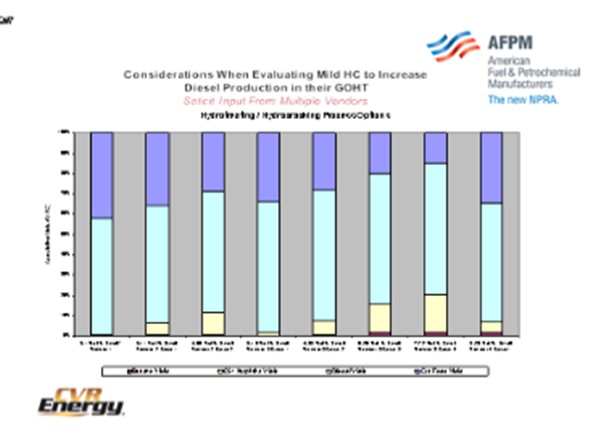
The boxes are other ranging variables that we know we can get to this part with the current production of CCR, in terms of hydrogen. The next box up is where we might have to bring in perhaps as much as 5 million scf (standard cubic feet) of supplemental hydrogen from an SMR (steam methane reformer). And then in order to cover the top end of our range, we wanted to make sure we knew the liability of importing hydrogen from an SMR. So the buzz phrase for this: Know the size and price early so you can figure out your economics and determine what will really pay out for mild hydrocracking.
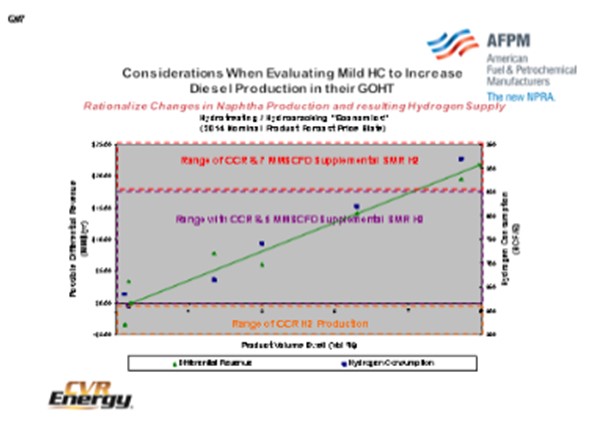
UNIDENTIFIED SPEAKER
Do any of the panelists have experience with anyone trying to do mild hydrocracking in a ULSD unit, say, to adjust T90?
CARLSON (Criterion Catalysts & Technologies)
We have done a number of designs, and we have units in operation in which we have a mild hydrocracking component in the back bed either for controlling endpoint or, as you will hear in some of the other responses, for some other benefits, for example, cold flow.
UNIDENTIFIED SPEAKER
Do you have to maintain a treat gas hydrogen availability constraint to do that?
CARLSON (Criterion Catalysts & Technologies)
It is going to depend on the operating pressure of the unit and the space velocity. If adding a mild hydrocracking component, we confirm that there is enough treat gas to not only minimize deactivation rates but also to quench that bottom bed when the conversion is not desired. This verification can provide the ability to adjust conversion levels for seasonality or market needs. Total treat gas availability can be higher in order to meet this flexibility. The minimum is typically going to be around 4:1; but again, a more detailed review is always required.
LEICHTY (Chevron USA, Inc.)
It also depends on the feedstocks being processed. If your feed is 100% straight run, then you may be able to get by with three times the chemical consumption for your treat gas ratio. The ultimate determining factor is the reactor outlet partial pressure and fouling rate at that pressure. Without any specific data, a four-to-one ratio would be fairly conservative.
UNIDENTIFIED SPEAKER I am talking about the pooled amount of hydrocracking. Do you think 3:1 would be okay?
LEICHTY (Chevron USA, Inc.)
It could be sufficient; but again, it really boils down to the catalyst fouling rate at the outlet hydrogen partial pressure.
JEFF JOHNS (Chevron Products Company)
I am interested in the commercial experience. How low do you have to get the nitrogen slip to get a reasonable amount of conversion – say, more than 10% to 15% – in a mild hydrocracking unit?
CARLSON (Criterion Catalysts & Technologies)
We have done reviews where, as you saw, it depends on your catalyst system. We have units running in excess of 400 ppm (parts per million) or 500 ppm nitrogen into the cracking section of the reactor, which might not be a cracking section where you want to put in zeolite catalyst. So you can either utilize a catalyst system with conventional alumina or use ASAcatalyst systems. And if you look at the cycle economics, you might have to evaluate it based on your projected yield shift from start-of-run to end-of-run. You will get better performance early on, and you might end up at an end-of-run performance that did not result in a big benefit from that cracking bed. However, the overall cycle economics can be favorable. If you really want to put in high zeolite catalyst and be pushing the conversion up to the 25% to 35%, then you musthave the pretreat capability of getting the nitrogen down sub-100 ppm. We have a couple of papers on the web where you can see some case studies.
SERGIO PIMENTEL (CITGO Petroleum Corporation)
In ULSD units with no specific cracking bed, what is your experience trying to adjust the cold properties, like pour point adjusting severity?OHMES (KBC Advanced Technologies, Inc.)From what we have seen, you really do not have a big impact. In fact, if you look at the cold flow profile of the components from feed to product, it is basically the same. You just happen to crack away some of the very heavy components. So yes, if you want to crank up severity and over-treat, getting a little backend destruction will slightly improve cold properties. But normally, you are only going to get about 5°F, 10°F, or 15°F distillation shift on most units without having some kind of cracking catalyst. You really will not see a big impact, maybe just a couple of degrees of pour point or cloud point.
CARLSON (Criterion Catalysts & Technologies)
That actually ties into our next question.
UNIDENTIFIED SPEAKER
We operate our hydrocrackers with 95% conversion with 5% bleed fed to FCC unit. This 5% bleed is purely for PNA (polynuclear aromatics) management. Is there a more effective way to have a better PNA management to increase the conversion in terms of advancements in engineering within the fractionator, guard bed, or clear beds? Is there a way to increase the conversion and reduce the bleed?
OHMES (KBC Advanced Technologies, Inc.)
I think we will answer your question on that a little bit later.
LEICHTY (Chevron USA, Inc.)
You have to be able to control the PNAs in order to avoid fouling in the second-stage effluent coolers and catalyst with a recycle operation. I am not aware of any ways to do that other than to bleed, so that is what we monitor and optimize.
CARLSON (Criterion Catalysts & Technologies)
With a continued trend and long-term forecast of strengthening distillate margins many refiners look to ways of maximizing their facilities ULSD production. One area of focus is the FCC pretreat/FCC complex that typically has been designed and optimized to maximize the conversion of 650+ material into the gasoline pool, typically with a minimization of production and recovery of distillate boiling range material.
Looking at existing FCC PT (FCC pretreat)/FCC complexes, the pretreat unit objectives have tended to change over the past decade with the move to clean fuels production. In the past, the FCC PT units overall value proposition has been a combination of environmental compliance via sulfur removal and increased FCC yields. During the period of 500 ppm sulfur diesel and 300 ppm sulfur gasoline production, the pretreat objectives often were set to produce either a side-draw blendable low-sulfur diesel stream or resultant on-spec FCC naphtha product or both, with the bonus being improved FCC yields via aromatic saturation and nitrogen removal. The extent of FCC yield improvements often were a function of desired operational cycle life and available hydrogen for the pretreat units. Hydroprocessing catalyst systems were developed utilizing cobalt molybdenum (CoMo) and nickel molybdenum (NiMo), depending on these objectives and constraints.
In today’s clean fuel operations, much investment has been made in ULSD and FCC naphtha HDS with few refiners now achieving environmental compliance via previously designed pretreat units. An additional result of the global drive towards clean fuels is the continued advances in catalyst technology that have provided significant gains in both HDS and HDN performance. These technology gains are being utilized to drive new FCC pretreat designs to very high levels of performance and have provided refiners the option of revisiting how best to maximize the value of existing FCC pretreat units.
This has resulted in many units shifting catalyst system designs in order to provide higher levels of nitrogen removal and aromatic saturation by using more high activity NiMo catalysts, resulting in maximizing FCC conversion capability. If distillate maximization is desired, many FCC pretreat units can be revamped to effectively operate in an MHC mode of operation. This more severe operation is performed with higher reactor temperatures and often by modifying the catalyst system to include a more active conversion catalyst such as an amorphous silica-alumina (ASA) or zeolite.
In considering mild hydrocracking operations for VGO hydrotreating, a comprehensive facility constraint and capability review is vital to ensure that the project scope provides both the desired yield based economic return, as well as the longer-term objectives of reliability and operational flexibility to respond to market changes.
What is VGO MHC? VGO MHC typically refers to a mode of operations and catalysts system design intermediate to the severity of a conventional FCC pretreat unit and a high conversion (~65+%) hydrocracker. They typically serve two purposes: both improving FCC feed quality, as well as increasing distillate production.
It can be a low-cost alternative for difficult feeds and heavy oil conversion.
•Typically 1000 to 1500+ psig pressure
•Conversion levels usually between 20% and 60%
•Simplified process design
•Selective hydrogen consumption
•Excellent FCC feed quality
•Existing VGO units successfully revamped
•Unique configurations for cases where high quality distillates required
For grassroots designs, the project scope can actually be more clearly defined as you are starting with an empty plot space; however, with revamps of existing VGO hydrotreaters, significant considerations exist as this is usually not a catalytic drop-in solution.
Focusing on revamps of existing units, the first consideration is how will the projected MHC mode impact existing refinery configuration and downstream operations and what revamp scope will be required to provide the desired performance. Increased hydrogen demands, reduction of FCC VGO feed, and product quality targets need to be evaluated to ensure facility-wide economics support the proposed project. FCC conversion benefits require that in most cases feeds are available to maintain FCC capacity. Often, optimized FCC PT operation and improved product recovery, by itself, can provide significant gains with minimal costs.
Determining the optimal targeted operation and process scope requires an evaluation of catalyst system designs with their predicted yields slates and cycle life estimates, all of which are largely dependent on the individual design and configuration, feed types, and contaminant level, as well as the scope of the proposed revamp.
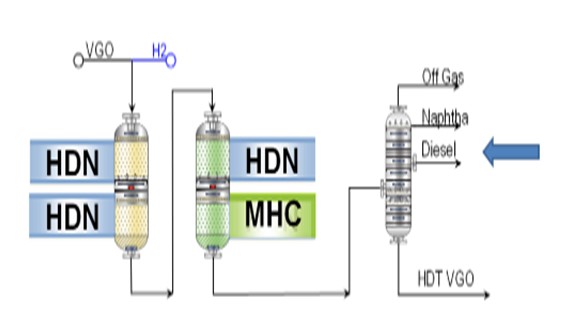
Depending on the conversion and distillate selectivity required, all alumina, alumina/ASA, or alumina/zeolite stacked systems can be considered. Higher conversions can be achieved by alumina/ASA stacks and even higher by alumina/zeolite stacks compared to total alumina system. In specifying an MHC catalyst system, the balance of hydrotreating versus cracking catalyst and the potential addition of reactor volume is largely influenced by feed qualities and desired level of conversion. As many of the feeds processed are high in contaminant metals, sulfur, and nitrogen, the pretreat section is required to remove these contaminates to ensure a sufficient cycle life can be maintained while both meeting any product targets and minimizing nitrogen slip into the cracking section of the reactor. Feed quality, reactor and catalyst system specified determine the ultimate S and N removal capability for a given cycle life; HDS functionality can remain an important criterion for some MHC units depending on existing product specifications that are dependent on-site refinery constraints and capabilities; however, HDN capability often is more important as it influences the cracking catalyst selection and performance due to remaining nitrogen heteroatoms, reducing cracking reactions. As mentioned, zeolite-containing products can provide highest ultimate levels of conversion; however, they tend to be the most sensitive to nitrogen slip, reducing their long-term effectiveness in such cases. Amorphous silica-alumina cracking catalysts provide increased levels of nitrogen tolerance with a lower level of conversion capability, and for units with limited HDN capability conventional pretreat catalyst, can be operated in a MHC mode, however, with a reduced conversion capability.
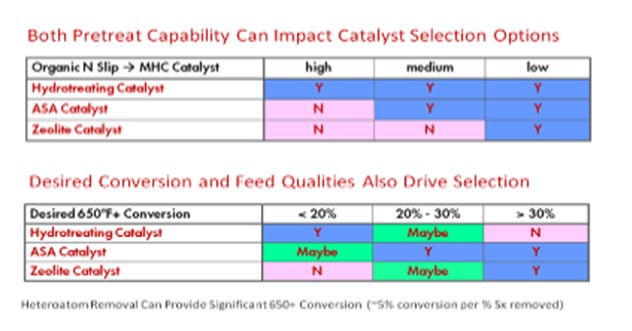
Once the facility economics are confirmed and the conceptual scope of the revamp has been determined, the detailed unit design considerations need to ensure the safe, effective, and reliable long-term operation of the unit.
Although operation in the mild hydrocracking mode using only the existing reactor volume offers many potential advantages, it can also have technical and economic constraints. The relevance of these varies from refinery to refinery and a careful technical and economic evaluation is needed before converting the unit operation. Several Issues should be fully considered:
•Conversion of VGO streams may leave the FCC underutilized, unless there is additional FCC feed available (e.g., from imports or there is additional FCC pretreat capacity e.g., due to de-bottlenecking)
•Additional hydrogen should be available as unit expansion and/or higher conversion will require more hydrogen consumption.
•The mild hydrocracking operation will result in additional naphtha that may need additional processing
•Seasonal demand factors may lead to operation for gasoline in summer and middle distillate in winter so that the advantage can only be realized for a part of the year.
The FCC pretreat unit will have shorter cycles operating in the MHC mode. Typically cycles are halved (although this depends on the feed, operating conditions and conversion target).
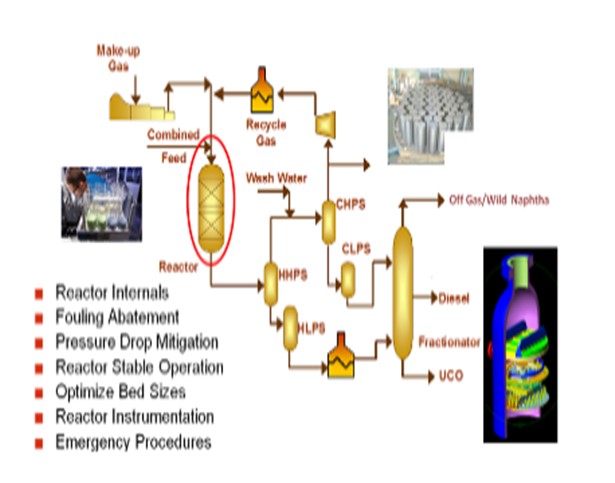
In a revamp design due to the changing in operating conditions, yields and reactor catalyst system design, significant changes to unit heat balances and flow regimes will impact the downstream recovery and fractionation section of the unit.
Product separation capabilities may be a serious issue depending on existing configuration; in case that a fractionation section is in place the tower internals discussed earlier can provide a low-cost solution to the increased diesel production.
•The increased conversion will result in more vapor traffic that needs to be accommodated for safe operation of the unit.
•Additional requirements for waterwash, gas treating, fractionation section equipment constraints need to be reviewed and addressed.
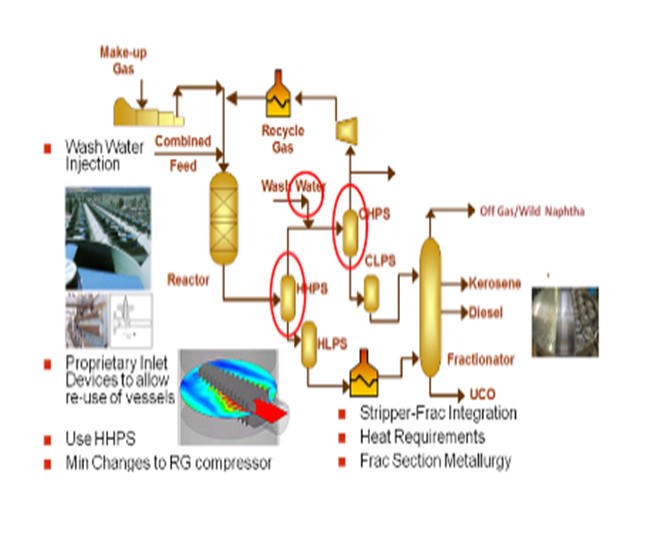
Key to MHC success is this full consideration and review of unit capabilities, constraints and refinery benefit combined with a unit specific catalysts system designed for balancing pretreat and cracking activity optimizing facility value.
BODOLUS (CVR Energy)
Simply increasing severity in a gas oil hydrotreater will not produce the desired selectivity to diesel products. It is preferred that some fraction of the hydrotreating catalyst be changed out. Catalyst vendors can assist in selecting the specific hydrocracking catalyst, but a catalyst change is just one of the many things to consider. Temperature and hydrogen supply management within the reactor need to be considered as the reaction chemistry moves from hydrotreating to hydrocracking. Quench flows and internal metallurgical limits need to be carefully evaluated.
The fractionator will need to be evaluated to determine if it can handle and produce the desired diesel cut. Note that making the distillation range in the fractionator does not guarantee that the product will meet all other specifications of ultra-low sulfur, cetane or cold flow properties. Post-treat or a “polishing” step may be needed to reach sulfur targets.
As with all other refinery slate changes, overall economic considerations include the impact that increased diesel/reduced gas oil/increased hydrogen consumption has on the facility.
Evaluation Program:
•Involve catalyst vender(s) in yield criteria and validate with economics.
•Solicit projections from multiple vendors and compare on a “general basis”
.•Economics need to consider hydrocracker competing with FCC unit. •Rationalize changes in naphtha production and resulting hydrogen supply.See the following slides.
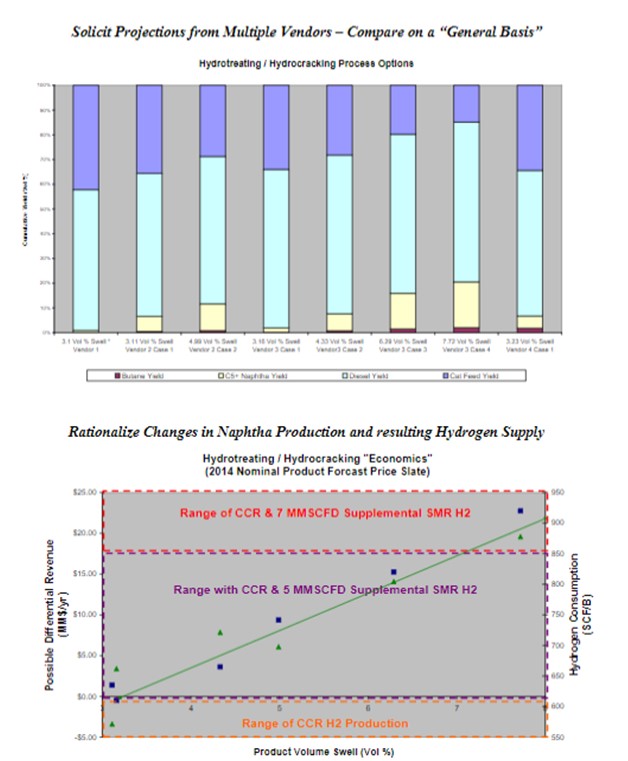
SUBHASH SINGHAL (Kuwait National Petroleum Company)
The right choice of a catalyst makes the difference in achieving max diesel yield. Once we rightly define our objective while procuring the catalyst, the catalyst suppliers can offer the right mix of catalyst to achieve the refiner’s objective. If the refiner has a highly active catalyst that is suited for jet/naphtha production, even reducing the catalyst temperature does not help much.
STEFANO MELIS (Albemarle Corporation)
A common way to increase diesel production is to increase the operating severity of an existing VGO hydrotreater. Conversion in the unit is mainly thermal, but catalyst changes can increase the relative contribution of catalytic cracking if the unit is capable. Operating a VGO hydrotreater in MHC mode yields a moderate conversion increase of typically 5% to 15% over the course of a cycle, depending on unit pressure. Almost all of the converted product falls in the diesel boiling range and an improvement in bottoms quality (in particular S and N content) is also realized, however, at the cost of additional hydrogen and a significant reduction in unit cycle length.
Technical feasibility of such solution is often limited by associated processing equipment. Sufficiently high compressor capacity, hydrogen availability and quench capability are important. Downstream fractionator design is also critical to ensure the increased diesel make can be fully captured.
Even more critical is the economic evaluation. The value of the extra diesel produced is offset by a reduction in cycle length, in some cases halved compared to normal operation, with corresponding additional downtime, production loss and catalyst cost. The consequences of reduced bottoms production must also be evaluated as it typically reduces throughput to the FCCU. Finally, the effect of improved bottoms quality should be evaluated, as a significant improvement in FCCU operation and product quality is anticipated; in particular, higher FCC conversion associated with lower feed N content and improved product quality due to lower S content in all FCC products.
ROBERT WADE and CHARLES OLESEN (Advanced Refining Technologies, Worms, Germany)
There are a number of considerations when designing a catalyst system for mild hydrocracking service. This mode of operation tends to have higher fouling rates than conventional high pressure hydrocracking (HCU) service, and also has two competing constraints compared to a single constraint for the typical high pressure service. In a mild hydrocracking operation, cracking conversion is controlling at SOR; and as the hydrotreating (HDT) catalyst deactivates through the run, the HDS and HDN conversion will start to become controlling. This means it is critical to understand how the H2 partial pressure varies throughout the run and the impact this has on the expected fouling rate of both the HDT and HCU catalysts. In addition, it is important to having a good understanding of the nitrogen slip to the HCU catalyst so that the activity of the HCU catalyst is properly balanced against desired selectivity.
The addition of HCU catalyst to an existing hydrotreater will come at the cost of decreased HDS/HDN catalyst volume. This will reduce the activity and life of the HDT section. The HCU catalyst does have some level of HDT activity, but not enough to overcome the decreased volume of HDT catalyst. Figure 1 below summarizes pilot plant data which demonstrates how the HDS activity of the catalyst system is impacted by the addition of HCU catalyst. The addition of a small amount of HCU catalyst has little or no impact on HDS activity, but higher volumes of HCU catalyst result in decreasing HDS activity.
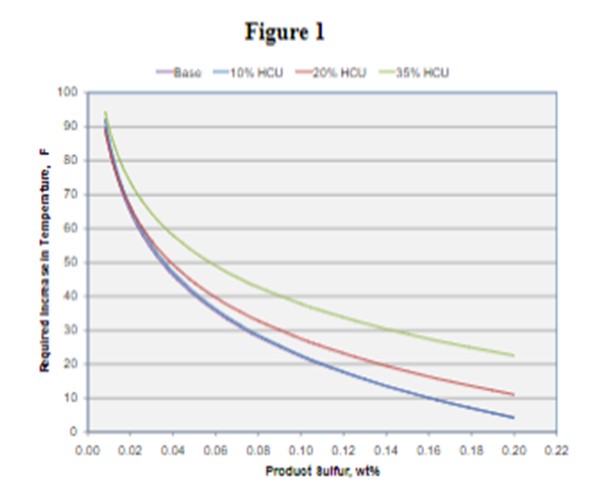
The changes in HDT activity need to be balanced against the cracking activity of the catalyst system as shown in Figure 2 below. Not surprisingly, increasing the amount of HCU catalyst results in higher levels of conversion.
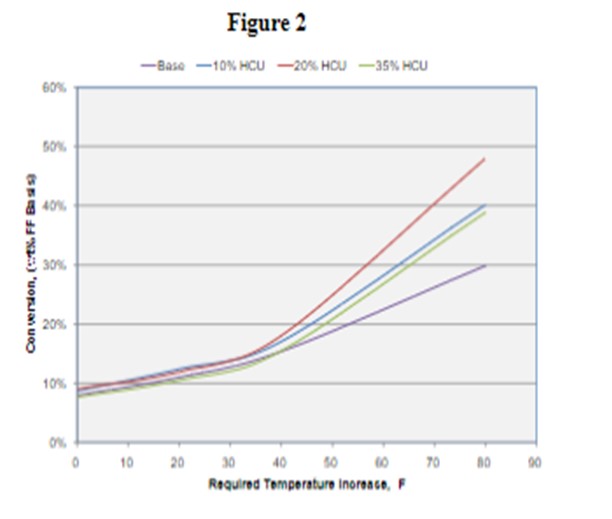
Achieving the proper balance of HDS/HDN activity and cracking activity is a challenge and the system is best customized on a case by case basis. The volume and type of HCU catalyst needs careful consideration in order to provide the desired conversion and minimize production of excess gas and naphtha. This is especially important as the cycle progresses and the reactor temperatures approach EOR.
A mild hydrocracking system will make more light products so the product recovery section needs to be evaluated to ensure it can handle the increase in lighter products. In addition, there will be an increase H2 consumption and corresponding increase in heat release (higher exotherms). Consideration needs to be given to make up H2 requirements and temperature control scheme to make sure they are adequate for the expected changes.