Question 69: What operational or other changes prompt evaluation and optimization of standpipe aeration? What do you monitor to ensure the standpipes remain fluidized across a range of conditions?
MALLER (TechnipFMC Process Technology)
Standpipe stability is highly dependent on the design. Some units do not have any aeration; some units have aeration that they never look at over the run; and some units require constant monitoring on a weekly or even daily basis. So, it really depends upon the design. What we are looking at is the number of head built inside the standpipe and the density through the various sections in the standpipe. It is important to have an understanding of the baseline condition and targets before you run outside and start trying to adjust the aeration.
So, what would prompt a change? If you are going to turn down, you will be looking at lower circulation rates. There is a regime where the standpipe is not going to perform well, wherein the flux rates are about 60 to 100 pounds per second per foot squared. That is the regime where the bubbles are no longer flowing downward. They start wanting to flow upward and coalesce into bubbles that are large enough to start affecting the catalyst flow.
What I like to do is monitor the pressure profile all the way down to the standpipe, with a single-gauge survey on various intervals, to get a good understanding of how it should be performing. You should be able to use the aeration taps to measure the process pressure inside the standpipe. You can take a pressure reading on each one of the taps and make a map plotting the height elevation of that tap versus the measured pressure.
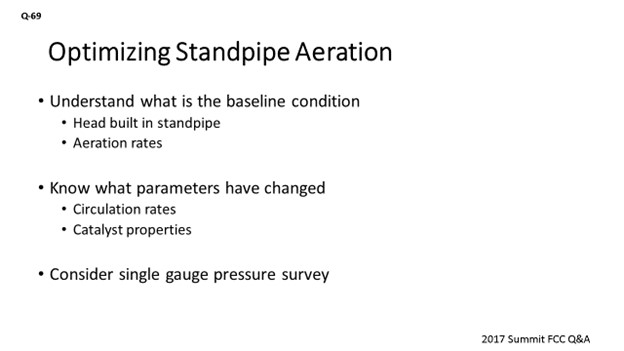
What a well performing standpipe will show is more or less a linear increase in pressure as you go down on the same pipe. Seeing areas where you are not getting the pressure being built up as much as it is in other areas could be an indication that you will want to adjust the aeration in that area. Also, seeing areas where you have pressure drop in the standpipe can be an indication that you are putting in too much aeration. Some FCC units that have really finicky standpipes have installed purged taps with pressure transmitters down the standpipe in order to monitor this profile online. That may be a good option if standpipe stability is a major concern. That way, everything is recorded so you can go back into the historian to see trends so you will be prepared for future standpipe performance.
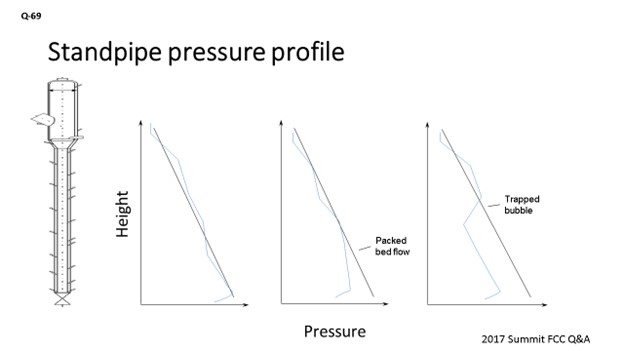
If that is not possible, you can always look at the instruments you do have available. A standpipe will typically have some kind of level instrument on the upstream side of it. There should be purged tap there. You can either use an online calculation in the DCS (distributed control system) to get a pressure reading at that location, or you could put in a dedicated pressure transmitter instrument which would piggyback on that existing tap. Then, do the same on the upstream side of the slide valve to get the pressure reading directly above the slide valve. You would then have an online measurement of what the head is being built in that standpipe, independent of what is happening on the downstream side of the slide valve.
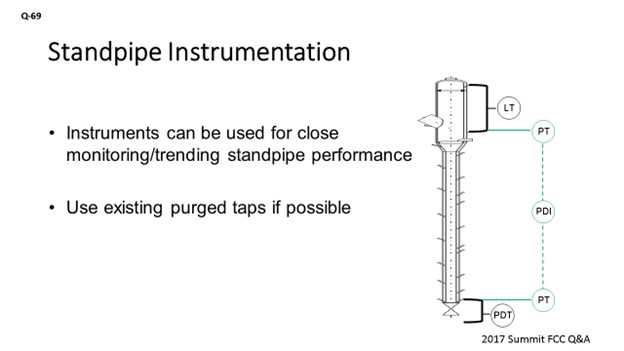
TRAGESSER (KBR)
Alex did a good job of answering the question. I will just add a more high-level comment. The overall goals of a FCC standpipe are to transfer catalyst from one vessel to the other and to help ensure that the slide valves or plug valves are operating within a reasonable range and have a steady dP to ensure a steady flow of catalyst. Since we are in Austin, I think a quote from Darrel Royal may apply here. He used use to say, “When you throw a pass, three things can happen and two of them are bad.” I think the same applies to adjusting standpipe aeration: The potential outcomes could be that 1) nothing will change; 2) it may get worse; and 3), you could get lucky and it might actually improve. So, if you have good steady slide valve dPs, it is not recommended to try and make it better.
I would like to mention one thing related to the standpipe: In order to have a standpipe with a good pressure buildup, it is important for the catalyst to be properly fluidized before entering the standpipe. If it is not well fluidized when it leaves the cone, there is not much that can be done to correct this problem in the standpipe and it will be a frustrating exercise to try. Depending on the design, there may be fluidization in the cone that will need to be set properly for this to occur.
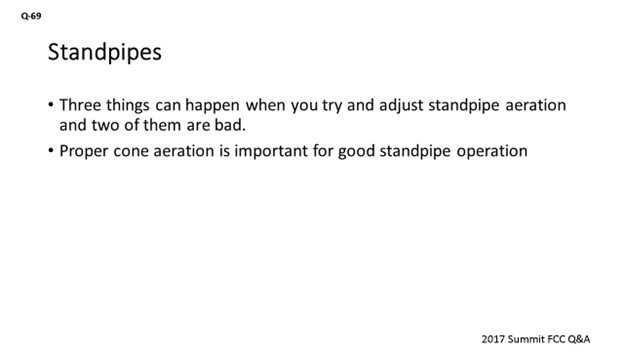
FEDERSPIEL (W.R. Grace & Co.)
I agree with what has been said. I just want to touch on the catalyst contribution to standpipe aeration. Not only do changes in operating conditions, feed rates, and fluxes prompt an evaluation, changing the catalyst type should probably also prompt that same evaluation. The graph on the slide is demonstrating this maximum stable expansion ratio: a ratio of the density for incipient fluidization over the density for incipient bubbling. It really gives you a window of a healthy operation. As we go through standpipes, we are compressing the catalyst flow and changing the circulating density. What we see here is not just the average bulk density; it is actually a proxy for particle density. It plays a role in that maximum stable expansion ratio, but the fines content does as well. So, anytime you run into an issue where you might be losing fines material, it is likely that you will probably need to go out and adjust the standpipe aeration because it might be moving the window of your healthy operation.
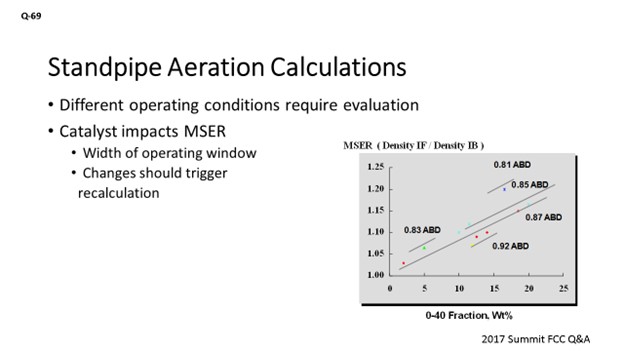
J.W. “BILL” WILSON (FCC Consultant)
All of these comments are good. I want to add one more that was prompted by the statement said about optimization. I think the best rule for dealing with standpipes is: If it is not broken, do not fix it. As Steve said, there are three things that can happen, and two of them are bad. More often than not, the two that are bad will happen when you are playing around with the standpipes. By being ‘not broken’, I mean that you are getting adequate pressure buildup in the standpipes. So, if you have good pressure drop across the slide valves and that pressure drop is stable, do not fix it. So, if you are not getting the most delta, the most apparent density, or the most pressure buildup you can out of the standpipe, who really cares if you are getting enough? You can spend a lot of time going from a 35- to a 40-lb/ft3 (pound per cubic foot) apparent density in that standpipe and gain absolutely nothing, in terms of unit operation, and greatly increase the chances that somewhere in the process you will shut down the unit.
ZIAD JAWAD (Phillips 66)
I think one of the biggest problems with troubleshooting standpipes is the fact that the taps are not accessible. So, it is important that during the turnaround, when you have access to those taps, make sure that the root valves are working and not plugged. When you go through your inspection, stick a wire rod through just to make sure you actually have a tap you can work with during the run if there is a problem.
ALEX MALLER (TechnipFMC Process Technology)
Standpipe aeration is something which has been studied and reported on since the inception of cat cracking. Some standpipes require no attention and may not even have any aeration provisions provided. Others may be so sensitive to changing conditions that adjusting aeration is a daily action. Standpipe design is the most important factor. They tend to be very sensitive to changing direction, such as going from vertical to slanted.
The operational changes that would prompt a review of the standpipe performance are changes in catalyst circulation rate. Standpipes tend to not perform well in a certain range of catalyst flux, where the bubbles formed by the aeration flow neither down nor up. Instead, they coalesce together until they are large enough to have buoyancy to flow in the upward direction. These large bubbles can block the catalyst flow and are a source of instability in the slide valve dP. The range of catalyst flux which is to be avoided is generally 60 to 100 lb/ft2/sec (pounds per square foot per second).
An important aspect to monitor when reviewing standpipe operation is the pressure profile in the standpipe. Some units have dedicated, purged, pressure instruments along the standpipe for this purpose. Another option is to consider a pressure instrument on the aeration tap to give an indication of the pressure inside the standpipe. Most units just use the slide valve dP to indicate standpipe performance as the downstream pressure is usually constant; therefore, any variance in dP is changes in the head being built in the upstream standpipe. One suggestion is to consider a pressure instrument that piggybacks off the upstream slide valve dP tap. This pressure transmitter would give a direct reading of the pressure at the base of the standpipe. Having the same type of pressure tap upstream of the standpipe, such as on the high pressure tap of a level instrument, will give a direct reading of the standpipe head being built.
Regardless of your instrumentation arrangements, it is important to take regular single-gauge pressure surveys to understand the baselines for standpipe performance. These surveys should be taken at multiple elevations down the standpipe. If taking a reading off of an aeration tap, ensure that the aeration air is temporarily throttled to ensure that the backpressure through the tap is not impacting the pressure reading. An area in the standpipe where no head is being built is an indication that aeration adjustment may be warranted.
Although it is important to ensure standpipe fluidization over all modes of operation, when standpipes are not stable, operators have a tendency to want to increase the aeration rates to the taps. Overaeration of a standpipe can show similar symptoms as an underaerated standpipe. Both should be avoided. Establishing a good baseline of proper standpipe performance will help to give you a better idea of which direction to turn the valve when adjusting aeration of a finicky standpipe.
MICHAEL FEDERSPIEL (W.R. Grace & Co.)
Standpipe aeration is provided to replace the volume of gas lost in a fluidized catalyst as head pressure builds and compresses the gas. Not all standpipes have provisions for aeration; usually those without aeration taps are short in length and have minimal change in direction. Longer standpipes require aeration to ensure the smooth circulation of catalyst and sufficient slide valve delta P.
To calculate how much aeration a given standpipe requires, the first step is to calculate the volume of circulating catalyst emulsion (VEmulsion).
VEmulsion = QCatalyst/ρEmulsion
VEmulsion is used to calculate the volume of gas circulated with the catalyst.
VGas = VEmulsion * (1 – ρEmulsion/Skeletal Density)
The next step is to calculate the absolute pressure at the inlet to the standpipe and at each aeration tap location.
PInlet = PDilute + ρEmulsion * ΔH where ΔH is the distance from the inlet to the top of the bed
and
PTap = PInlet + ρEmulsion * ΔH where ΔH is the distance from the tap to the inlet
Finally, the calculated terms VGas, PInlet, and PTap are used to compute the change in gas volume due to the increased pressure.
ΔVGas = VGas – (VGas * PInlet)/PTap
ΔVGas is the theoretical amount of aeration required at each tap. Note: Each tap must be calculated individually, and experience shows the actual aeration requirement is usually 30% lower than theoretical.
Large changes in catalyst circulation rate, bed density (emulsion density or ρ in the calculation above), or system pressure should trigger an optimization of standpipe aeration. Additionally, if any taps along the standpipe were to become plugged with catalyst, the surrounding taps would need an adjustment.
Although the skeletal density of different FCC catalysts is usually very similar, changes in catalyst can impact the emulsion density and pressure profile and require aeration optimization. Catalyst properties (along with aeration medium) also sets the maximum stable expansion ratio (MSER), which is defined as:
MSER = Catalyst Density at Incipient Fluidization/Catalyst Density at Incipient Bubbling
The MSER indicates the “width of the operating window” over which a bed of fluidized catalyst is well-behaved. In the context of a standpipe, the MSER indicates how much a fluidized bed can be compressed before it will revert to a packed bed (defluidizes). The MSER is a function of catalyst particle density (with ABD used as a proxy) and 0-40 fines content, as shown in Figure 1.
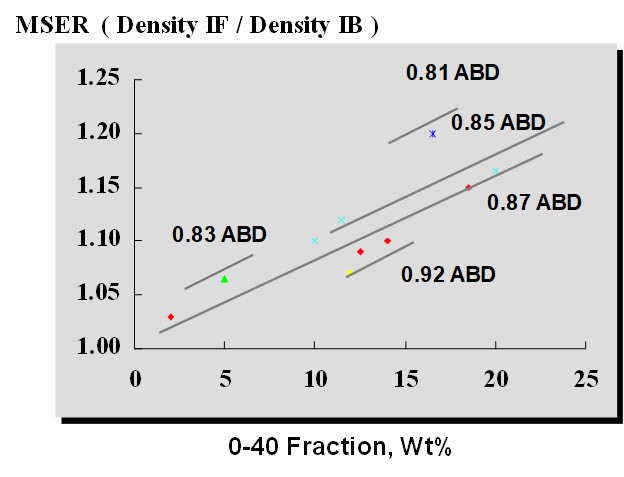
Figure 1. Maximum Stable Expansion Ratio at Different Catalyst Properties
Monitoring the physical properties of the FCC catalyst is an important part of standpipe aeration optimization. Changing catalyst types should cue an evaluation of the standpipe aeration. Taking a single-gauge pressure survey of the standpipe can give valuable insight into the condition of the standpipe’s aeration. This survey is especially important to do while the unit circulation is healthy in order to establish a baseline, as shown in Figure 2.
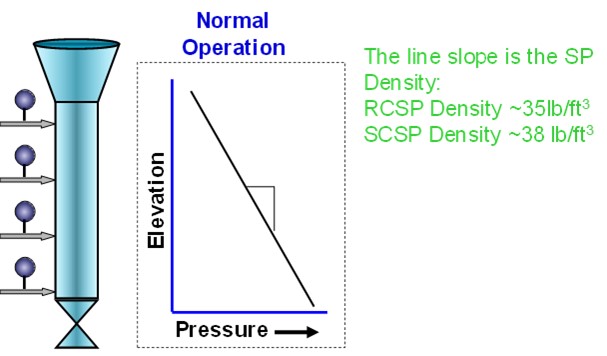
Figure 2. Typical Standpipe Pressure Profile
Pressure profiles, like those in Figure 3, indicate it is time to adjust standpipe aeration.
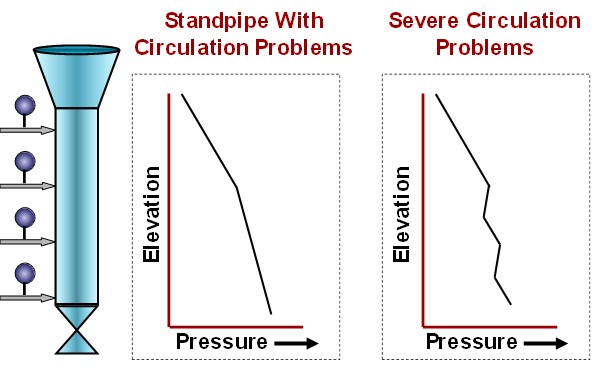
Figure 3. Abnormal Standpipe Pressure Profiles
Finally, monitoring slide valve delta P is another method of tracking standpipe aeration. If the slide valve delta P unexpectedly changes or becomes erratic, the standpipe aeration should be reviewed.