Question 69: What are the effects of a poorly insulated coke drum? What is a good way to assess coke drum insulation effectiveness? How can the benefits of new insulation be estimated?
Jeff Lewellen (HollyFrontier)
Poor coke drum insulation impacts both the mechanical integrity and unit operation.
The mechanical integrity issues tend to be the easiest to quantify and address in our facility. The mechanical integrity impact of ineffective insulation includes:
• Uneven heating/cooling of drum wall causing elevated stress in these areas leading to shorter drum life.
• Under Insulation Corrosion (UIC) initiated by compromised insulation systems allowing rain and cutting water to infiltrate under the insulation.
Potential poor insulation impact to unit operation includes:
• Potential for lower drum outlet temperatures that impact foam stability, coke type, VCM, yields, internal recycle, etc.
• Potentially, slower drum warm-up step if significant loss of insulation performance. This may impact unit rate if the unit is cycle limited.
Our coke drum insulation maintenance begins with our mechanical integrity program. We rely upon visual inspection of equipment by operations and inspection personnel to initiate preventative/routine maintenance as necessary to maintain the integrity of the insulation system. Inspection by thermal imaging camera has also provided to be useful in locating problem areas.
Process indicators can be more difficult to monitor in our facility due to varied feed slate that impacts the coke formation properties in the drum. This makes monitoring the drum inlet/outlet temperature unreliable to predict heat loss. Monitoring coke cutting logs for unusual coke qualities and problems can be insightful to detect several issues including insulation problems. Notations that describe difficulty to clean walls in certain drum elevations or unusual changes in coke types with elevation may indicate problem areas in the drums.
Rajkumar Ghosh (Indian Oil Corporation)
A poorly insulated coke drum results in heat losses to the atmosphere, reducing the available heat for cracking reactions. The effects of poorly insulated Coke Drums as per our experience are as follows:
a. VCM or the Volatile Combustible Matter in the Green Coke tends to be on the higher side with a poorly insulated Coke Drum as compared to the one which is properly insulated. Coke Drum outlet temperature (before quench) is a key parameter to monitor the VCM content of the Coke. We have experience of a Coke Drum having damaged insulation. The change in Coke Drum outlet temperature (with the same inlet temperature) before and after the complete replacement of insulation is in the range of 3-4°C.
b. Condensation of heavy ends on the relatively cooler Coke drum walls results in higher Coke yields and loss of corresponding liquid yields, as this correspondingly increases the internal recycle within the drum. The Coke produced would be soft because of the higher internal reflux and higher VCM.
c. Poor insulation may also lead to uneven cooling and accelerated ‘banana effect’ of the coke drum.
Good ways to assess Coke Drum insulation effectiveness are:
a. The drop in temperature across the drum. The temperature drop of the Coke Drum inlet and the vapor outlet from the top of the drum should be around 40-45o C. If the drop is more than this figure, then the Coke drum insulation needs reinforcement.
b. Monitoring the quench flow that is being injected into the vapor line for the same throughput can indicate the effectiveness of insulation. The quench flow comparison over a period of time can help ascertaining the condition/ effectiveness of the insulation.
c. Monitoring of the skin temperatures of the coke drum can also give an idea about the condition of the coke drum insulation. A lower indication of the skin temperature than normal can indicate poor insulation.
d. Above all, visual inspection gives a good insight to the state of health of the insulation. The benefits of new insulation are derived from lower coke VCM, which can be directly translated into improvement in liquid yield.
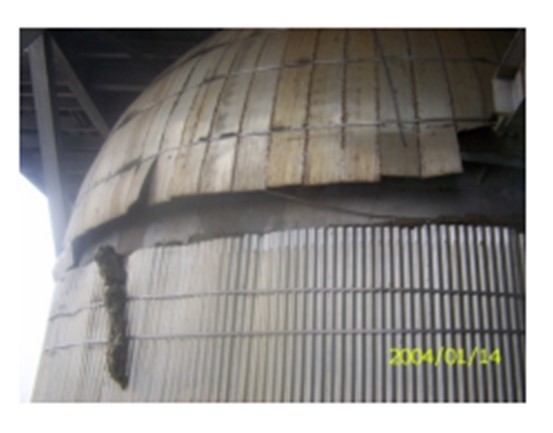
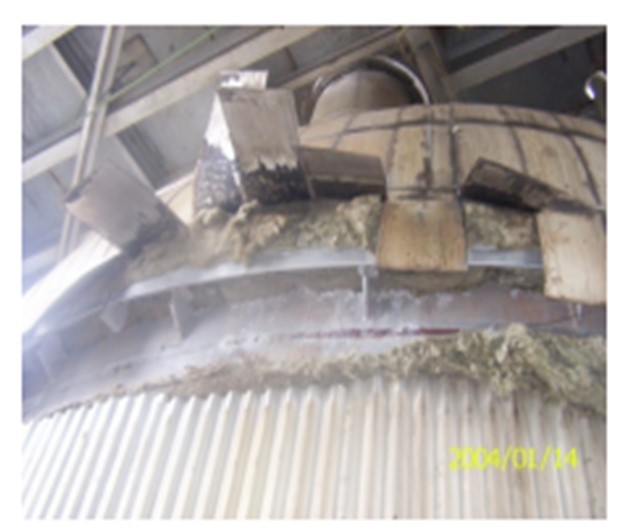