Question 68: What is your experience with toxicity issues at the Water Treatment Plant as related to naphthenic acid content in desalter brine water? What strategies are you employing employed to mitigate this issue?
Dennis Haynes (NALCO Champion)
The top causes of fouling with tight oil are asphaltene, destabilization on blending with asphaltene bearing crudes and also the potential for thermal production of foulant material. Operational changes due to processing a higher degree of light tight oil may also impact fouling trends in crude unit preheat systems. Modification of blending strategies or use of antifoulant additives have both been used to control fouling in the preheat train.
Greg Savage (NALCO Champion)
Crude preheats and furnace fouling is an observed problem in processing price advantage crudes like light tight oils (LTO) and heavy Western Canadian crudes. Tight oils blended with asphaltenic crudes (like Western Canadian Crudes) can reduce crude stability and precipitate asphaltenes. The higher the proportion of LTO in the crude feed slate the greater the potential for fouling (as seen below).
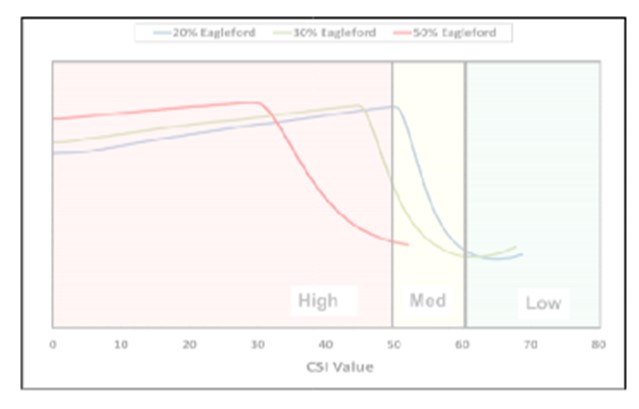
In addition to reduced stability due to blending, when thermally stressed, tight oil forms polar aromatic particles that are unstable in the bulk fluid (pictured below). It is theorized, the aromatic portion of light tight oils dehydrogenates and undergoes condensation reactions to form polynuclear aromatic particles that are unstable in the bulk oil due to the tight oil’s poor oil solvency power. These polar aromatic particles have been observed in the ALCOR Hot Liquid Process Simulator (HLPS) as well as in field deposits. Also, high inorganic solids levels have bound with organic foulants deposit on heat transfer surfaces.
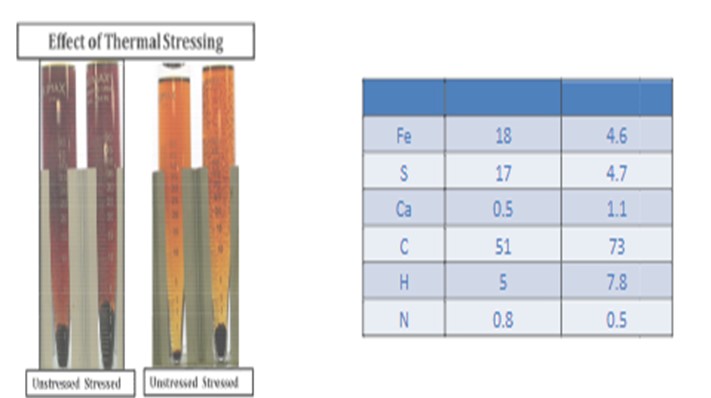
Waxes from tight oils frequently foul cold exchanger trains. A number of refiners have identified crude column fouling from upstream phosphorous additives or amine salts. Consequently, crude preheat, furnace, and tower fouling are increasing problems in processing tight oil/Canadian crudes.
Contaminants that cause fouling are frequently not identified in conventional crude assays, crude diets frequently change, and unit operations can be very dynamic. Crude heater fouling can be very challenging to diagnose. Fouling of the crude preheat and the crude heater could be caused by:
•Poor tube cleaning
•Slops processing
•Poor desalter operation
•Chemical additive treatment
•Over fired tubes
•Flow imbalance between passes
•Locally high heat fluxes due to poor heat distribution or burner tip plugging
•Inadequate mass velocity
•High heat flux
•High fluid bulk temperature
•Excessive vaporization in the crude preheats and heater
•Destabilization and agglomeration of asphaltenes
•Deposition of inorganic salts such as iron sulfide, sand, as well as alkali and alkaline earth metal salts present in the feed
When troubleshooting crude preheat and heater fouling problems, the mechanical and operational conditions of the unit should be evaluated from the tank farm to the boundary limits using a unit audit assessment, temperature and pressure survey, as well as rigorous heat transfer simulation using software such as NALCO MONITOR™. The evaluation of mechanical and operational conditions includes but is not limited to:
•Tank farm mechanical capabilities and limitations as well as blending operation
•Desalter operational and mechanical capabilities and limitations
•Desalter optimization
•Mud wash study
•Evaluation of caustic injection systems
•Exchanger and heater velocity calculations
•Heat flux profile for exchangers and heater comparison to design
•Exchanger train splitter optimization
•Evaluation of cleaning effectiveness with optimum cleaning schedule recommendations
•Heater fireside evaluation with thermography survey
•Vaporization evaluation in exchangers and the heater
•To evaluate the chemical fouling risks the crude slate is initially evaluated using a crude operating experience data base. Additionally, samples should be collected, and chemical analysis performed including deposit analyses, crude characterization, and laboratory fouling simulation in order to determine fouling mechanisms and evaluate solutions. Proper monitoring of preheats and furnaces is essential to success of any fouling control program as the system is complex and extremely dynamic.
Refiners have reduced fouling rates when processing light tight oils through improving furnace heat distribution, minimizing furnace vaporization, increasing desalter solids removal through optimization and chemistries, optimizing caustic addition, online exchanger cleanings, and the use of antifoulants. Recent antifoulant trials have demonstrated reduced furnace fouling rates from 3 - 5°F/day to less than 1°F/day.