Question 68: For those refiners seeing an increase in vacuum overhead chloride concentration at constant desalted crude salt content, what are the consequences and how can they be controlled?
SLOLEY (CH2M Hill)
First, verify the chlorides found in the hot well water. Could the chlorides be from leaks from the vacuum system condenser cooling water? A hardness test will quickly identify water system leaks. Essentially, getting a high chloride concentration in the vacuum overhead at a constant salt content in the desalted crude implies either a change in the chloride type or in the operating conditions leading to more chloride hydrolysis. Enough water is present in most vacuum systems that the chloride concentration in the water condensate is low. Chloride corrosion issues in the vacuum system are relatively rare.
Some refiners have seen chloride concentrations in the vapor phase in the vacuum tower high enough that ammonium chloride directly deposits from the vapor phase. The problems from this had included near complete plugging of wire mesh mist eliminators installed in the tower above the LVGO (light vacuum gas oil) pumparound distributor and in-plugging of the LVGO drawer nozzle with solid ammonium chloride plugs.
Underdeposit corrosion has also occurred on the LVGO collector trays. In other units, ppm levels of chloride had been found in vacuum diesel which can cause downstream problems in hydrotreating end products. The most effective way to deal with chlorides is to remove them at the desalter. If they cannot be removed at the desalter, operating changes to the reduced vacuum heating severity are the most effective means of reducing the number of chlorides hydrolyzed upstream with a vacuum tower.
Vacuum tower yield economics tend to overwhelm any advantages of lower heater temperatures being used to reduce chlorides in the vacuum tower. As long as the vacuum heater, vacuum tower, and vacuum systems have the capability to handle the load, maximize heater velocity steam. This lowers the oil film temperature and shortens residence time. This will minimize chloride hydrolysis. Since these changes also improve yields and product quality—at a constant yield—they should be done in any case.
PRIBNOW (CITGO Petroleum Corporation)
I agree with what Andrew said. The overhead chloride concentrations will cause corrosion within the tower and the overhead system. We have observed some different corrosion mechanisms in the outlet piping of our ejectors, as well as the shells and the condensers, to the point that we even holed-through one of the elbows. You can have some corrosion issues in that overhead.
One of our vacuum towers is a dry tower. It has a pre-condenser. Andrew mentioned these ammonium chloride salts that come out. We will see them laying down in the ODs (outside diameter) of the tubes at this condenser. They will create higher differential pressure and ultimately degrade lift in the vacuum tower and affect the gas oil cutpoint. We found that doing a heat-up of some sort will move this ‘goo’, as we call it, or ammonium chloride salts. It will move the material right off those tubes and allow you to continue operation without a shutdown and without having to clean the bundle. If we have to clean the bundle, we will need to get it wet. We have experienced corrosion from the water/ammonium chlorides and upgraded metallurgy to alleviate.
The higher chloride concentrations can be a result of many causes. Each has its own method of remediation. Injecting wild streams directly to the vacuum tower may be a likely cause.
Organic chlorides: I think Andrew mentioned that the chlorides will travel out of the bottom of the atmospheric tower and hydrolyze in the heater, going overhead in the vacuum tower. Some halogens, which we call Smarties, can be measured as chlorides in lab tests. These are tightly bound asphaltene salt crystals. They are harder to get out in the desalter and are hydrolyzed in the heater, eventually coming out in the overhead system.
Aside from troubleshooting some of the above-mentioned items to improve desalting, as Andrew mentioned, we optimize our water and raise our ∆P and mix valves to get better mixing to break apart the Smarties. Acidification of the washwater will remove calcium and magnesium salts. And then, always maintain that minimum salt point temperature on the top of your vacuum tower. Salt point should be calculated. We like to be conservatively 20°F over the salt point. Do not allow the overhead temperature to get below the salt point or, as was mentioned, salting of the LVGO section and plugging will occur. Try and keep the salts in the overhead where chemistries can treat.
VILAS LONAKADI (Foster Wheeler USA Corporation)
Of course, the chloride is the inorganic versus the organic, though organic ones are saline. In one vacuum unit, I have seen temperatures increased so high that the design went from a normal system using just ejector, to having to install a pre-condenser.
DENNIS HAYNES (Nalco Champion Energy Services)
I want to point out a few additional causes. There was some research that originally started in the 1930s. When I was working over in Japan in the 1990s, I reviewed some material done by the Japan Petroleum Institute on Middle Eastern crudes where they reviewed various blends. They noticed that depending upon which crudes they were blending, they were able to get different hydrolysis rates. Subsequently, more modern research was done by others; specifically, regarding naphthenic acid-bearing crude blends. It was noticed that as the naphthenic acid content of the blend was directionally increased, there was more hydrolysis of the calcium and the sodium chloride. This may actually push some of the hydrolysis further downstream. So, I want to point that out as an additional cause. As far as the solution to the hydrolysis, it gets back to improved desalting caustic utilization and neutralization, if the chlorides make it to the overhead system.
HAROLD EGGERT (Athlon Solutions)
Before going on too much with the chloride quest, I will say that we see unexplained, elevated chloride levels a couple of times a year; so, it is important to get a sample of your overhead water and run a hardness test on it. It takes a very small cooling tower exchanger leak to actually drive the chlorides up in the overhead. That is often simple. So have your vendor start adding that to the test, not only in the vacuum tower but also in the crude overhead. Do not be fooled into thinking it is just cooling water. It is innocuous. Cooling water is saturated with oxygen. We have had discussions here today about all the evils of oxygen. You can have oxygen coming into the hot well and move that water back to the desalter. It just sets up a vicious cycle. It is a quick, easy task. Have your vendors run hardness on all the overhead water samples, assuming there is a cooling water exchanger in their system.
SIMON ARENDS (Marathon Petroleum Corporation)
Can you give more details on asphaltene hydrolysis? At Galveston Bay, we have seen fouling of our vacuum overhead system with this gooey asphaltenic-looking material. How do you mitigate that? How do you clean it?
SLOLEY (CH2M Hill)
It comes back to the question of phosphorus. We had a discussion earlier this morning about the phosphorus going with the kerosene. Depending upon the level of effectiveness of your stripping section in the atmospheric column, you will end up with kerosene boiling-range material in the overhead of the vacuum system. There have been at least a couple of incidents where phosphorous in the overhead of vacuum systems makes deposits when it mixed with hydrocarbon carried over from the vacuum tower. It is often difficult to be prove that this might be happening, but it is one potential cause of vacuum system problems.
PRIBNOW (CITGO Petroleum Corporation)
Right now, I believe that all we do is improve that desalter efficiency. We try to sheer in the mix valve and get better mixing in the desalter. Tower delivery temperature steam-to-crude ratio can be evaluated. You said that the heater outlets can be decreased so that you do not hydrolyze. And then, like we said, we are going to try the acidification process and see if that can break down the tightly bound asphaltenes.
HODGES (Athlon Solutions)
I want to add that the mixing is a key component, as Phil mentioned. In several studies we have done, we have learned that adding as much water as you can into the crude charge pump suction is the only way to effectively contact and remove the interstitial salt coming in that is bound up with the asphaltene compounds.
GLENN SCATTERGOOD (Nalco Champion Energy Services)
The observed increased in vacuum tower overhead chlorides, in some cases, can be related to the increase in TAN crudes. This phenomenon has been observed since the 1930s and was re-demonstrated recently by several research groups. The figure shows an example of this phenomenon.
Control of an increase in chloride in the vacuum tower overhead is similar to those used to control chlorides in a crude overhead tower:
a) Add caustic to suppress hydrolysis. This will help minimize some of the calcium chloride that was not hydrolyzed in the crude furnace from readily hydrolyzing.
b) Accurate monitoring of vacuum overhead chloride and proper neutralizer injection dosage is critical to control corrosion from this higher chloride concentration.
c) Improve CaCl2 removal by improving desalting (washwater rate and location, mix valve, demulsifier type, temperature, crude tank treatment, etc.).
d) Improve metallurgy of the vacuum tower overhead.
e) Reduce the amount of the high TAN crude that is causing the increase in hydrolysis.
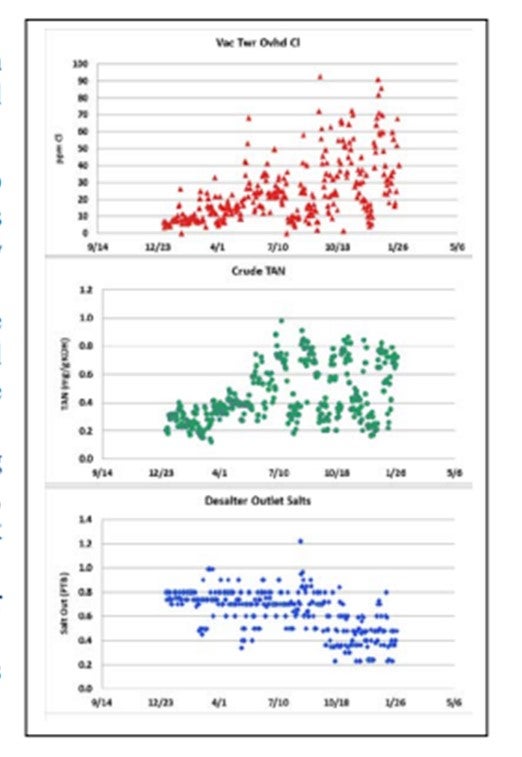
DENNIS HAYNES (Nalco Champion Energy Services)
Through the years, various studies have been done which show that crude composition can impact the hydrolysis of salts and increase hydrogen chloride to downstream distillation columns. The consequences are increased corrosion rates and requirements for corrosion control technologies (caustic, neutralizer, filmer, metallurgy changes, etc.). The best way to deal with incoming chloride is by removal via desalting, where possible, and then using a caustic (if the unit has the capabilities to apply it). Surrounding this discussion is the uncertainty of undesaltable chlorides or chlorides coming in with the crude that are in a form not removable by extraction (discussed in various industry publications and forums). In the case of undesaltable chlorides, the control becomes blending down the low-quality crude source and using washwater, neutralizer, and filmer where appropriate.
PHILIP THORNTHWAITE (Nalco Champion Energy Services)
The consequence of increased chlorides in the vacuum unit is that it increases the risk of overhead corrosion in the pre-condenser (if present) and in the condensed water after each ejector stage. This will require a subsequent increase in neutralizer and additional monitoring to maintain corrosion rates at acceptable levels.
An additional consequence is that in particular cases where there are high levels of ammonia or possibly tramp amines present, the elevated chloride levels significantly increase the risk of salt formation inside the vacuum tower and upper pumparounds. Once packed beds and pumparounds begin to foul, the fractionation efficiency can quickly deteriorate and ultimately lead to an unplanned shutdown to allow cleaning of the unit.