Question 68: How does your organization share operational and process safety information to foster an environment of continuous improvement?
LARSEN [Marathon Petroleum Corporation (MPC)]
I am going to put in another plug for an AFPM tool: the AFPM Safety Portal. The FCC Advisory Group at Marathon uses this portal to share information among our different unit engineers and refineries. I know that Marathon, as well as many other companies, submits process safety data there. I think it is a good tool to use. So, if you are not already using it within your organization to learn, you should take advantage of it.
I also would like to touch on Marathon’s Process Safety Advisory Program. Our program was modeled after the “Safety Beacon” of CCPS (Center for Chemical Process Safety). The document is just one page and can be printed on the front and back, if necessary. It is important that this bulletin be presented with an eye-catching layout and contain a concise listing of high-level learning events. Basically, it is just a brief, fact-based summary of the incident. We work to tailor the handout to contain a section describing what you can do in your position in the refinery to prevent incidents, whether internal or external, to Marathon and including information you can learn from these types of events.
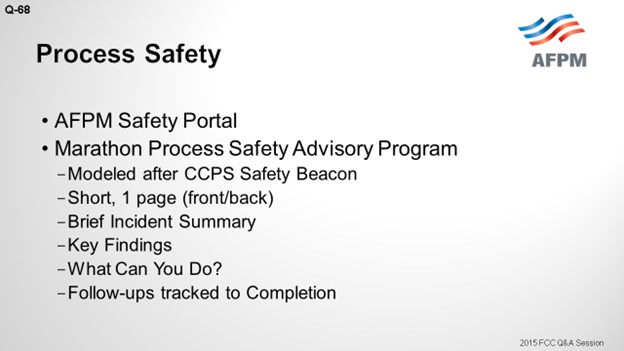
On the next slide, you see a couple of examples; nothing fancy. One of them dealt with long-bolt flanges.
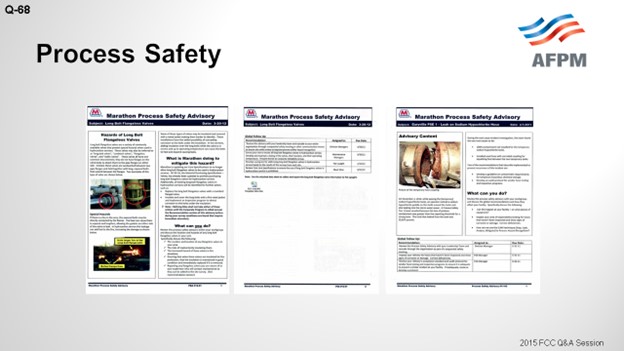
We try to do only one of these per month within our organization. It gets rolled out at refinery-wide Safety meetings and reviewed with every level of an affected organization face-to-face. So I think it is definitely a good learning tool. One of the challenges associated with it, for us, is making sure we use a well-credentialed employee to generate these documents. It should not be done by a junior person. You want someone who is recognized as having subject matter expertise about making these types of process safety advisories that have worked well for us. So that is one of the highlights of our Process Safety program that I believe works well for us.
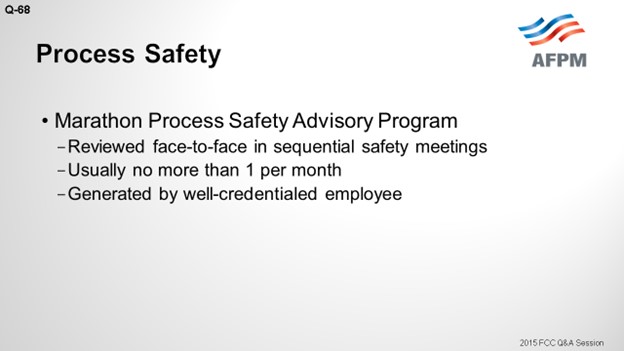
FOSHEE (Shell Global Solutions - US)
Thanks, Nik. Sharing operational and process safety information begins with the mindset of Goal Zero: Operate our facilities without significant incidence or fatalities. This is documented in our HSSE (Health, Safety, Security, and Environment) and social performance framework which communicates and shows commitment to safety and has policies, standards, and manuals that contain mandatory safety rules for all Shell employees, joint ventures, and contractors to follow. These manuals cover topics such as health, process safety, environmental projects, contractor HSSE management, personnel safety, security, product stewardship, transportation, and social performance.
In order to further reinforce the safety mindset at Shell, we have “The 12 Lifesaving Rules” which are mandatory and cover personnel safety. Three Golden Rules within Shell to help reinforce expected behavior for our employees are to comply with governing laws, standards, and procedures; to intervene in unsafe and non-compliant situations; and, to respect our neighbors. In addition, all Shell employees take mandatory safety training on a frequent basis. Finally, there is an annual event that we call Safety Day where all Shell employees take a pause to reflect on their personal commitment to safety.
NIKOLAS LARSEN [Marathon Petroleum Company (MPC)]
MPC utilizes the AFPM Safety Portal to communicate and share experiences and knowledge within our FCC Advisory Group. It is a vital component of our goal to improve process safety performance. We also have a Process Safety Advisory Program to learn from external industry and internal MPC process safety events, significant near misses, and high value learning events. Our Process Safety Advisory Program was modeled after the Center for Process Safety (CCPS) Beacon and is a tool for the broad distribution (all MPC refining sites) and discussion of significant external and internal process safety events and high value learning events (significant near misses).
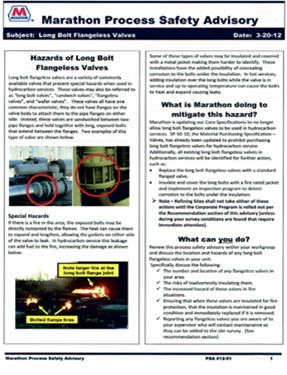
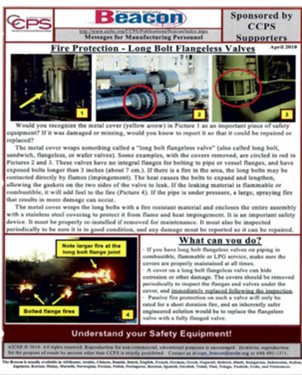
Key Features of the Process Safety Advisory Design:
-
Eye-catching, professional layout
-
Short: 1 to 2 pages (If two pages, then print on the front and back.)
-
Brief, fact-based description of the incident written in common terms
-
Key findings from the incident investigation
-
“What can you do?” section targeted for work group discussions that start with the Refinery Leadership Team and cascade down to every affected work group at the site; points in this section guide the group to explore their vulnerability to a similar incident and to take action to prevent an occurrence at their site.
-
Global Follow-up section targeted at close gaps in management systems, programs, and performance at all sites which is assigned to a responsible manager with a due date and which is put in the MPC Recommendation tracking system to follow through to resolution.
The workflow of our Process Safety Advisory Process for internal events starts with a Root Cause Incident Investigation being completed along with a first rough draft of the PSA (for external events, the corporate Refining group will compile information and generate a draft PSA). This is forwarded to the corporate Refining staff where it is reviewed. The final version of the PSA is reviewed with all refinery site managers and cascaded through the organization as a part of a sequential or other Safety meeting. Recommendations are tracked to resolution and reported quarterly in the corporate refining PSM (Process Safety Management) report. PSAs are then also connected into the PHA and Refining Standards Updates process.
Benefits of the program include:
-
Provides a high impact requiring minimal resources,
-
Creates an effective means of communicating with and engaging employees,
-
Closes the gap at all refining sites, not just at the affected site,
-
Facilitates learning and improving Process Safety Hazard Recognition,
-
Offers a robust means to follow through on Global Gaps, and
-
Permits us to be well poised to take incidents from the Industry Event Sharing Program.
Key success factors of the program include that we:
-
Get top-down buy-in on global follow-up recommendations,
-
Do not overload the sites with too many PSAs because MPC’s experience is no more than one per month, and
-
Do not assign the PSA final drafting to a junior employee because the final drafting requires a “been there, done that” experience level.