Question 67: What strategies do you employ to optimize FCC plus hydrocracker operations? Do you process hydrocracker unconverted oil (UCO) in the FCC or FCC LCO/HCO in the hydrocracker?
BHARGAVA (KBC Advanced Technologies, Inc.)
At every client site we visit, we find a lot of opportunities in the FCC hydrocracker optimization, in spite of the LP runs and the molecular management clients are doing. Why is it so difficult, and why do most people do not get it right? This optimization is just not about the FCC and the hydrocracker. It involves units such as the reformer, the hydrogen plant, sulfur plant, and LCO hydrotreaters. So, if you do not have your constraints built in into your LP or your simulation model, most likely, you will not get the right answer. We use full refinery light simulations from crude to gasoline blending because it affects everything: from crudes to gasoline and diesel blending. The big driver here is your capacity utilization. Do you want to fill the hydrocracker, or do you want to fill the FCC? What molecules from upstream do you want to use to fill up the FCC and the hydrocracker? Capacity utilization is the key variable; secondarily, get the molecular management right between the two units.
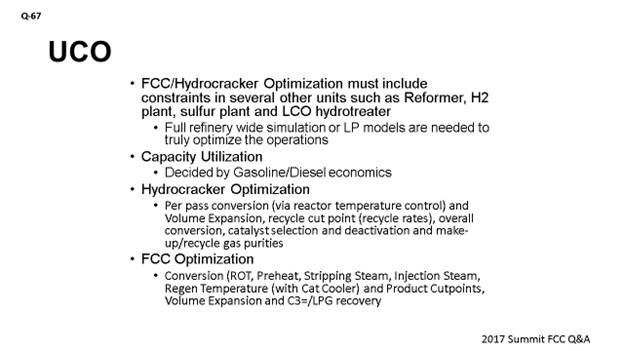
Typically, if your gasoline economics are favorable, then you will fill the FCC. If your diesel economics are favorable, you will fill the hydrocracker. Again, why is optimization so difficult? Because there are several variables on the hydrocracker side and then on the FCC. For example, on the hydrocracker, in addition to this pre-management and capacity utilization, you have to get the right per-pass conversion via reactor temperature control. Volume expansion on the hydrocracker, the recycle cutpoint, overall conversion on the hydrocracker, and catalyst selection and deactivation play a very important role in determining what severity the hydrocracker would run and at what feed rate. On the FCC side, again, it is conversion, mix of ROT (reactor operating temperature) and preheat, stripping steam, and injection steam. The biggest challenge on the FCC when you are trying to do this optimization is regen temperature, with or without a cat cooler and product cutpoints. Volume expansion of the FCC is compared to the hydrocracker and then the LPG (liquefied petroleum gas) propylene recovery as a result of the capacity utilization on the FCC.
I mentioned the regen temperature. Obviously, UCO (unconverted oil) is one of the best feedstocks to the FCC. It has an incredible conversion. Octane might not be as much as you would like, but you will have a massive volume expansion. So, from an FCC economic standpoint, they are both very favorable. The only downside of the UCO has been the regen temperature. If you are at minimum regen temperatures, delta coke becomes a concern. You have to find other ways to raise the regen temperature or reduce the hydrocracker feed to make less UCO and divert the hydrocracker feed to the FCC. The other way you can optimize is to find heavier feedstocks that you would not be able to put into the FCC if you had constraints at maximum regen temperature. So, a combination of UCO and feed molecular management allows you to get around those constraints.
Finally, we feel that processing cracked stock – like LCO and HCO – to the hydrocracker is very beneficial. The volume expansions are really good. Hydrogen consumption is high. So, as long as you have your hydrogen spare capacity, you can take advantage of it. There is a myth about recycling LCO and HCO coming back at the FCC through the UCO circuit. We found that most high-pressure hydrocrackers saturate and destroy the heavier molecules, so recycling really does not exist. You can then continue doing a real LCO and HCO processing through the hydrocracker as long as you do not have constraints on bed temperatures, or the delta T (temperature differential) increase on the beds.
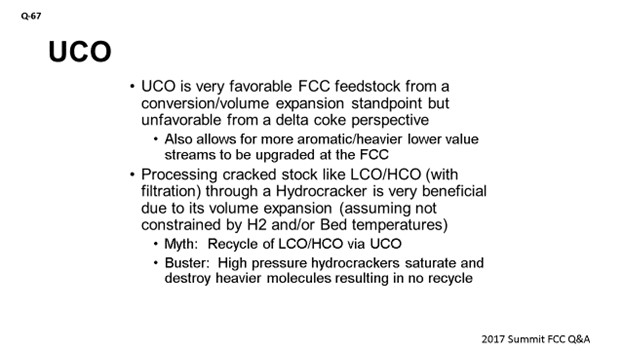
DINKEL [Marathon Petroleum Corporation (MPC)]
I agree with a lot of what Sanjay said. As far as evaluating unconverted oil on the cat, we take the same view as when we do an evaluation on any other potential feedstock within the refinery or a purchased feedstock. You need to have the right pricing. You need to have the volume and the properties. We run that data through our kinetic model and compare it to the overall LP for the refinery, just to make sure we are maximizing profit for the site and figuring out the correct location to process the unconverted oil.
FOOTE (CHS Inc.)
Both of our FCCs run 100% unconverted oil. One limit we have run into is the ASTM T50 point on finished gasoline blends. So, we push FCC conversion – and then the hydrocracker – towards a 2-1-1 refinery. Making more distillate yield, coming from the heavy end of the cat gasoline volume, goes a long way in moving the gasoline T50 point to the right of the distillation curve. So, if you are not careful, you could come out of balance at light straight-run gasoline. It can then also impact butane blending economics.
When you are evaluating the optimization of the FCC and hydrocracker, you also want to make sure you do not leave any alkylate capacity on the table. If you are not filling your alkylate, especially to achieve ISO (International Organization for Standardization) these days, that is undesirable. So, make sure your Economics people are evaluating it from that standpoint, too. By all means, fill the alky.
KEVIN KUNZ [Shell Global Solutions (US) Inc.]
Sanjay, I like your point about getting the molecular management correct. Recycling back and forth between the cat cracker and the hydrocracker, depending on where you are in the run of the hydrocracker, can lead you down a path that could seriously jeopardize the performance of both units. What do I mean by that? There comes a point – in all your hydrotreaters and hydrocrackers – where you stop saturating aromatics and start making aromatics.
Now if you start bringing those aromatics over into the cat cracker, you will increase your slurry and cycle oil yields. These two streams concentrate the aromatics. And when they are recycled back to the hydrocracker, which is now in what we call the ‘thermodynamic regime’, even more aromatics are made. Eventually, you will create a condition called ‘red death’ where the unconverted oil yield off the hydrocracker will significantly increase and turn red in color. This is a well-documented phenomenon34,35 and is resolved by taking a continuous bleed off the unconverted oil stream, to prevent continued aromatics buildup.
SANJAY BHARGAVA (KBC Advanced Technologies)
FCC plus hydrocracker optimization covers several additional units including the reformers, H2 plants, sulfur plants, and LCO hydrotreaters (neat or mixed with other feeds). If the H2 plant and/or sulfur complex (including amine and sour water strippers) are constraining, then these constraints need to be considered in the optimization. Hence, we recommend a full, nonlinear flowsheeting simulation from crude processing to blending to be used for this purpose: to optimize the feed and operating conditions for the FCC and hydrocracker. Well-tuned LPs representing actual plant operation can also be used in case a full simulation is not available.
The key optimization parameters in the hydrocracker include per-pass conversion (via reactor temperature control), recycle cut point (recycle rates), overall conversion, catalyst selection and deactivation, and makeup/recycle gas purities.
The key optimization parameters in the FCC include conversion [ROT, preheat, stripping steam, injection steam, sometimes regen temperature (if there is a cat cooler), and product cutpoints], liquid volume percent on feed, and C3= or LPG recovery.
In most cases, diesel economics will favor hydrocracker utilization while gasoline economics will favor FCC utilization in an unconstrained environment. However, depending on refinery unit and equipment constraints, the optimum capacity utilization and unit severities will lie in between the two extremes.
In a typical high-pressure hydrocracker/FCC refinery, the VGO (including coker gasoils) within 95% ASTM distillation and Concarbon (Conradson carbon) specifications (to avoid earlier-than-planned shutdowns) is fed to the hydrocracker, filling the hydrocracker, which is based on the economics. The UCO from the hydrocracker is fed to the FCC (or lube units). The amount of UCO is limited by the heat balance in the FCC due to the low coking tendency, which can limit UCO processing. The impact on the heat imbalance can be mitigated by processing lower value feedstocks in the FCC to allow for more UCO processing. The overall hydrocracker feed rate and conversion are controlled by mainly economics and catalyst cycle length within unit constraints. The FCC feed rate/quality and conversion are also optimized to economics and/or equipment constraints.
Processing any cracked feeds – like LCO/HCO – into a high-pressure hydrocracker will saturate aromatics and result in beneficial volume swell through the addition of hydrogen. There are companies that do process both LCO and HCO in the hydrocracker. Some clients are concerned about the “recycle” of the LCO/HCO via UCO to the FCC, but most hydrocrackers have HPS (high-pressure separator) pressures of 2200 to 2700 psig (pounds per square inch gauge). The result is aromatic saturation and subsequent cracking of LCO/HCO out of the UCO boiling range. So, there is no recycle. The amount of LCO/HCO recycled is limited by reactor delta temperature and maximum outlet temperature. In addition, the amount of HCO recycled is limited by hydrocracker catalyst cycle. It is also important for the LCO/HCO to the filtered prior to being fed to the hydrocracker.
BRYAN DINKEL [Marathon Petroleum Corporation (MPC)]
For our refineries that have the option of feeding hydrocracker unconverted oil (UCO) to the FCC, we evaluate the UCO the same way we do any other available feed. The refinery configuration, catalyst, operating constraints, and price valuation of feeds are assessed in both the LP and the kinetic model to determine the optimum feed slate that will maximize profit. A similar evaluation is conducted regarding LCO/HCO (heavy cycle oil) dispositions to sales or as feedstock to the hydrocracker, which determines the optimum economics.
MICHAEL FEDERSPIEL (W.R. Grace & Co.)
The ability to optimize FCC and hydrocracker (HCR) operations will depend on many refinery-specific factors. The first factor is the specific operating modes of the FCC and the hydrocracker. We can generically group FCC operations as “Gasoil FCC” and “Resid FCC (RFCC)”, and we generically group hydrocrackers as “full-conversion” (FCHR) and “partial-conversion” (PHCR). An additional configuration factor that will impact the optimization solution is the existence of a cat feed hydrotreater (CFH) or resid hydrotreater (RDS).
In the simplest optimization, considering FHCR and FCC/RFCC, it is almost always beneficial for both conversion units to divert some hydrocracker unconverted oil to the FCC. Converting that last barrel of feed in the HCR can often result in higher gas make and lower total liquid than if the same barrel were cracked in the FCC. However, depending on the amount and quality, UCO can cause fouling in the FCC slurry circuit; therefore, this threat must be considered.
Synergistic benefits are highly refinery-specific and are impacted by availability and type of feed to both units, prices of feedstock and products (including hydrogen), and refinery operational objectives. Often, the operational objectives can have the largest impact. Typically, cost of catalysts is not a big factor in this exercise. A detailed study – lead by or including FCC and HCR SMEs, as well as the Refinery Planning Group – is recommended to ensure success. One of the most important steps is to determine the expected longevity and variation in those factors because they drive the synergy and help the team determine if a more complex FCC and hydrocracker integration project can be expected to provide benefits.
Some PHCRs are designed for synergy with the FCC. In these cases, modern hydrocracking catalyst developments can offer unexplored/unexpected synergies. Adding capacity to the FCC/RFCC, improving the mechanical condition (upgrade or turnaround) of the FCC/RCC, or adding CFH or RDS may allow for further optimization steps, including converting the PHCR to a higher conversion or partial-recycle operation to increase desired products in both conversion units and/or reduce hydrogen consumption.
When feed streams are discrete, one optimization that can be counterintuitive is to not necessarily process the most difficult feedstocks in the high-pressure HCRs; rather, the most economic place for these streams may be in the CFH or RDS. The HCR severity increase with challenging feed streams, such as HCGO or DAO, can have a very negative effect on both the product slate and product qualities. This effect can overwhelm any benefit from improved FCC operation. Of course, we are not suggesting that HCRs be fed highly convertible HGO or LVGO only, but we believe that technology SMEs of each refinery can find a happy optimum for their specific operation.
Finally, on the question of LCO and HCO processing in the hydrocracker, the answers are again complex. HCO processing is not recommended in the HCR as HCO contains very stable multi-ring hydrocarbons that will pass through the HCR unconverted (at best) or precipitate out onto catalysts, causing deactivation. Even if the HCR is able to crack the HCO using specialized catalysts (such as self-supported catalysts like ICR 1001 from ART), hydrogen consumption would be very high and could reduce economic benefit. Often, a leading home for the HCO is in the refinery fuel oil pool.
LCO processing in a hydrocracker could also be a counterintuitive case. Normally, if the HCRs were designed to process LCO, then there are no issues. Depending on the availability and cost of hydrogen, processing LCO can lead to high volume gain and good economics. However, there are cases where LCO is added intermittently to increase bed temperature rise and kick off the reaction in downstream beds; but the effectiveness of this strategy is highly dependent on the feedstock and catalysts used in the downstream beds. LCOs contain very reactive molecules that will preferentially occupy hydrogenation sites of catalysts in the top half of the hydrocracking reactor. Therefore, depending upon catalyst type and placement, overall yield response may not meet expectations. Careful consideration and a study with HCR SMEs are recommended to ensure that such synergy actually exists.
The lesson is: Continuously study to identify synergistic opportunities with HCR and FCC SMEs.