Question 67: Have you experienced coking or other fouling of reboilers in naphtha distillation service (splitter, debutanizer, etc.)? If so, what operational or design changes did you implement to eliminate this problem?
Frank Tracy (ConocoPhillips)
I have two examples from our refineries.
First is a case of severe coking in one of our FCC debutanizers.
•The Debutanizer Reboilers are two kettle reboilers with U-tube bundles.
•Debutanizer bottoms flows through the shell side and is heated with Heavy Cycle Oil on the tube side.
•The shells and original bundles were carbon steel.
•History of tube leaks, but no records of significant shell-side fouling.
•Due to leak history purchased new chrome bundles for installation.
•At shutdown, very difficult bundle extraction.
•Extensive coke formation within the bundles bulged the tops rows of tubes into the shell cavity. •Shell-side fouling was found largely in the top 1/3 of the bundles.
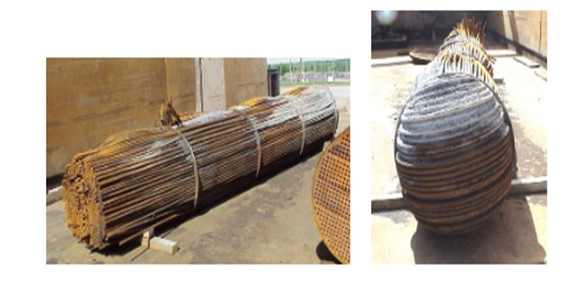
•Fouling was believed to be caused by iron-catalyzed diolefin polymerization that eventually became coke and was a function of ·Reboiler tube wall temperature
·Diolefin concentration
·Iron concentration
•We eliminated issue by lowering HCO temperature some and changing metallurgy to 9Cr bundles. It has been four years since bundle replacement without performance problems. We will confirm during next year’s turnaround.
My second example is from a debutanizer in coker service that uses HCGO as the reboiler heating medium. This unit has found through experience that they must maintain HCGO inlet temperature below 530 °F to avoid polymerization fouling on the reboiler side of the exchanger
. Any debutanizer reboiler in cracked feedstock service could experience fouling if the reboiler heating medium is too hot. Consequently, we are also careful to ensure that when using 600 psig steam as the heating medium, that the steam is properly desuperheated.
Jill Brown Browns (Sulzer Chemtech USA)
Two types of fouling are common in naphtha reboilers. The first type of fouling is generated as a result of the more reactive cracked stock hydrocarbons and is typically seen only in units like Cokers or FCCUs with a cracking process. The second type of fouling is a more complicated issue related to the presence of sulfides in the naphtha and can be seen in straight run units like the Atmospheric Crude.
Cracked naphtha, with its high olefin content, is subject to polymerization when in the presence of high temperatures. When the Stripper or Debutanizer reboiler is driven by a high temperature (>550 °F) heating fluid (Heavy Coker Gas Oil or Heavy Cycle Oil), the exchanger tube walls can see high temperatures which allow diolefins present in the cracked naphtha to polymerize in the presence of iron compounds.
In order to mitigate/ eliminate the problem of polymerization fouling, the refiner can heat the reboiler with a cooler stream of HCGO or HCO (temperature 550 °F maximum) at a higher flow rate for the same heat duty.
The second type of fouling looks very much like coke, adhering to the exchanger outside tube wall in a very tight layer of scale. Sample analyses should show that the material is not, in fact, hydrocarbon, but instead almost entirely inorganic. One Gulf Coast refiner found such deposits to consist of pyrrhotite, pyrite, and magnetite. They processed an external stream of natural gasoline in their Splitter column in addition to the Crude overhead naphtha. This stream contained some oxygen compounds as a result of transport. In systems processing sour crude, H2S attack on carbon steel metallurgy is very common. When in the presence of the high temperature from the reboiler and the oxygen molecules, the iron sulfide corrosion species baked to the tube walls held together by oxidized "glue".
In the case of the Gulf Coast refiner, the only method to remove the reboiler scale, once formed, was by high pressure water blasting. Aromatics and other solvents were ineffective in dissolving any deposits. Removal of the oxygen species, along with addition of an H2S scavenger, can contribute to prevention of the scale formation.
Paul Fearnside (Nalco Company)
Fouling of crude unit debutanizer reboilers is usually associated with contaminants, such as iron sulfide, amine salts etc., being transported into the column down into the tower bottom and then fouling the reboiler. Excessive corrosion byproducts from the crude tower OVHD are the contaminant identified most frequency. Some sources and solutions of these contaminants are:
•Problem: One source of this is if the crude tower OVHD water pH is consistently run > 7.0, then an interface rag layer of FeS will develop that can grow upwards in the reflux drum and then “pukes “over into the debut feed. The FeS then fouls the reboiler. Solution: Improve ovhd corrosion program to eliminate/mitigate corrosion.
•Problem: Undersized crude unit reflux drums resulting in excessive water carryout into the debut tower. This water contains all kinds of salts and particulates.
Solution: Reduce water going to the ovhd or increase the drum size or effective settling time. Use of parallel plates or coalescing pacs in the accumulator to enhance water settling can improve water coalescence and settling. Use of demulsifiers is also successful in reducing water carryover.
•Problem: Some filming amine corrosion inhibitors can cause slight emulsions in the accumulator resulting in water carry over into the crude tower as well as downstream into naphtha distillation towers.
Solution: Review the filming amine emulsion formation potential (MSEP/WSIM properties),
•Problem: Rerun cracked naphtha’s will increase fouling from all the gums now introduced.
Solution: Reroute cracked stocks to other process units. Use of antipolymerants and oxygen scavengers can minimize their impacts.
Eberhard Lucke (Commonwealth E&C)
Most problems have occurred in the debutanizer reboiler. In one case it was a hydraulic problem in the set-up of a stacked, 2-shell reboiler. The pipe arrangement to the shells favored the lower shell, while the upper shell was starved and had severe fouling problems. We had to redo the inlet piping to the reboiler to solve that problem. The other case of severe reboiler fouling was caused by a high approach temperature on the HCGO pumparound side. This was the result of many years of debottlenecking and pushing the unit to new capacity limits. To resolve this problem, we had to revamp the feed preheat and steam generation system and route a lower temperature HCGO to the reboiler.