Question 67: As distillate demand has decreased, current economics favor maximizing gasoline and octane. What operating and catalyst changes do you recommend for increasing octane barrels?
ZACH BEZON [United Refining Company (URC)]
Operational Moves:
*Increase cat/oil ratio (decrease preheat temperature).
*Increase reactor temperature (until overcracking starts).
*Increase API gravity of feed. This typically leads to a bump in conversion and octane; however, this is usually not economical as there may be diesel-range material that could be cracked into gasoline.
Catalytic Moves:
*Increase MAT activity (increase fresh cat additions/reformulation).
*Increase matrix by using a smaller unit cell size.
ALEXIS SHACKLEFORD (BASF Corporation)
An FCC unit contributes to the gasoline pool through both cracked gasoline production and C4s production, which is used to generate high octane alkylate for blending. For optimizing octane barrels, there are four main operation variables: reactor temperature (ROT), catalyst activity, catalyst selectivity (lower rare earth), and the use of a light olefins additive (ZSM-5). Due to differences in operating constraints, a Best Practice is to use a kinetic model such as FCC-SIM to determine the best operating variables and catalyst properties for the refiner’s unit. The figures below show the effect of these operating variables on LPG, gasoline, dry gas, and octane for a 1 vol% increase in butylene's. The optimized profit for the unit is likely to be a combination of these variables up to the unit is constraints.
Figures 1-4: Comparison of ROT, catalyst activity, catalyst rare earth oxide (REO), and ZSM-5 versus the effect on LPG (liquefied petroleum gas), gasoline, dry gas, and gasoline RON. All four cases give a 1 vol% increase in butylenes.
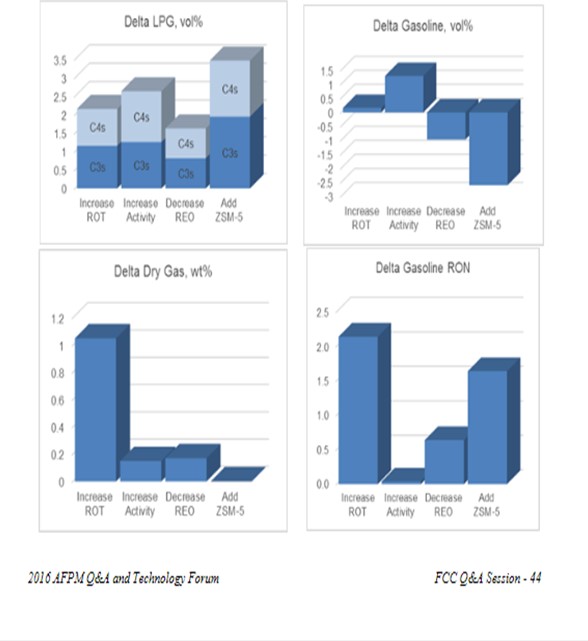