Question 66: What strategies should be considered to adjust for phosphorous in crude oil to protect downstream catalyst and processing units?
HODGES (Athlon Solutions)
Extensive work was done with Western Canadian refineries in the late 2000s to investigate and solve this problem, including adjusting desalter pH to extract phosphorous in the desalter brine, adding a phosphorous removal chemistry, changing the trays in the crude tower to reduce fouling susceptibility, solvent-washing the deposit to avoid long cleanouts and shutdowns, and adjusting process temperatures. These were not met with great success. This was a consortium effort where many operators tried many approaches. What they determined was that the only solution was source control from the upstream additives used in crude production.
When we started the panel discussion this morning, I mentioned that I have been in the special chemical industry for over 30 years. Eighty percent of that has been the in downstream operations, but I did spend a good part of the time in the upstream. What was very amazing to me was seeing everything that is put into the wells when they are completed and producing. The work that was done in Canada identified that one of the primary sources of the phosphorus they were seeing was volatile dialkyl phosphate esters which are used in gel fracs. Fracking is a high-pressure pumping operation that is used to open formations when wells are completed prior to production.
Another common use of chemicals during oil well production is for scale control in the near well bore area, production tubing, and associated equipment. Commonly, this involves an application technique known as a scale squeeze. During a scale squeeze, well production is stopped and then phosphonates are pressure pushed down the production tubing and into the reservoir. After a soak period, the well is returned to production. These phosphonates slowly desorb off the reservoir rock as the oil and water are produced and prevent scale buildup in the system. This is effective in terms of preventing well scaling problems but also adds phosphorous to your crude. Compounding the “contamination” problem, scale squeeze frequency greatly accelerates over the life of the well as it waters out. The implication here is that early on in the life of a particular reservoir, there will be no scale treatment and therefore no phosphorus contamination; but as time goes on, it may ramp up very sharply. There are many classic examples of this in the North Sea.
I encourage everyone to visit the CCQTA website where there is a wealth of information on the work done by the member organizations.
In addition to the source control, if running a naphthenic high TAN crude, many people will apply a phosphorous-based naphthenic acid inhibitor. Make certain that your process chemical supplier has the capability to model the distribution of the phosphorous in your system and to assure good phosphorous management practices.
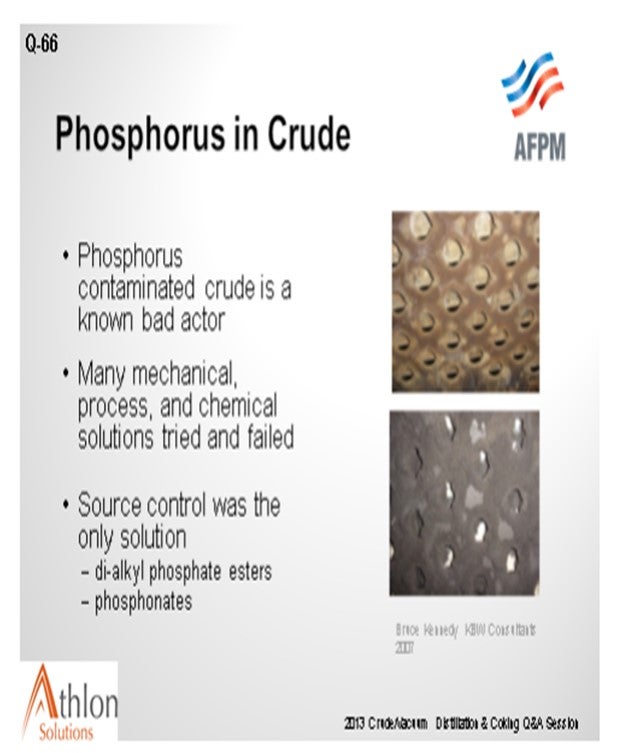
SHENKLE (Flint Hills Resources, Ltd.)
We have not really seen a change in phosphorous into the refinery and therefore have not made any crude slate changes. We have received confirmation from our last crude turnaround that there was no evidence of phosphorus in the jet section of the tower. There are some detailed responses in the Hydroprocessing Q&A for downstream effects on catalyst.
PRIBNOW (CITGO Petroleum Corporation)
Even though we had the fouling in those trays, we have not attributed any mid-barrel hydrotreating catalyst deactivation at this time. The phosphorous compounds probably all ended up on the trays. I know that desalter washwater acidification has been mentioned a couple of times. We are considering performing a trial to determine if we can remove the phosphorous components and direct them to the desalter brine. That is a trial we are pursuing to see if we can take care of that problem.
ALLEN KAISER (Delek Refining, Ltd.)
How much phosphorous is too much? Where is the breakpoint between it being a minor irritant and a major problem?
HODGES (Athlon Solutions)
I would not say that is well-known by refiners. I think it is very much dependent upon the type of phosphorous compound that is being used in upstream scale control, which can be further acerbated if you are applying phosphorous-based naphthenic acid inhibitors to your system as well. Because of the wide variety of the nature of the phosphorous compounds that are used in the upstream, you can and do get different chemistries and different concentrations. That will change from crude type to crude type and over the age of the field, and as the producer changes chemical suppliers. Unfortunately, there is not a very clear answer to that question. Proper management of phosphorus, in our estimation, is best worked out with your chemical supplier who can help you characterize crude, monitor the fouling propensity, and also investigate alternate methods of removal.
Going back to some of the previous answers, in the case of the Western Canadian refineries, they actually put a specification on the pipeline in the transport of the crude where they had a phosphorus spec. So, in that case, the producers of the oil were forced to comply by not putting phosphorous compounds into the oil. It is a very unique situation; because in most cases, refiners cannot greatly influence producers in terms of what they do and do not use as long as they meet sales specifications. Phosphorus is not a sales specification on crude. In the case of the Western Canadian refiners, changing the phosphorus spec on the pipeline was the only solution they found to control the huge issues they had running phosphorus contaminated crude.
XIOMARA PRICE (GE Water & Process Technologies)
The recommendation from the CCTQA was less than 0.5 ppm of phosphorous in the feed. However, there are other types of crudes I see that now create problems with phosphorous fouling in the tower. You have to be careful and look at it. It is volatile phosphorous; so, unless you are injecting it in there, you have to measure it properly; not total phosphorous, but volatile phosphorus.
UNIDENTIFIED SPEAKER (Shell Global Solutions U.S.)
I heard you mention other crudes, but is there evidence of more phosphorous contamination in tight oils specifically, other than Canadian crudes?
HODGES (Athlon Solutions)
I think you are asking are specific pipelines more notorious for transporting phosphorous-containing crude. Again, there is not a pat answer for that, particularly with all the advent of the tight oil in the U.S. It is a completely different chemical landscape upstream today than it was five years ago. The types and amounts of chemicals that producers are putting into their well, both when they complete it and during production, have not been seen before. I can speak from firsthand knowledge that there is a tremendous amount of focus by the producers to use materials that help them operate more reliably and efficiently, which is not necessarily in the best interest of the refiner.
I do not think there is an easy answer to this problem. Obviously, if you could put a phosphorous specification in place, it will help you manage this. But over the life of the field, even a specific crude type will increase in phosphorous content because of the increase in scale squeeze frequencies that typically take place over time. So it is a challenging question. I encourage you to work with your chemical supplier to understand and better characterize the crudes coming in and have him/her provide some additional surveillance for your particular operation.
BOB SHENKLE (Flint Hills Resources, LP)
At FHR, we have not witnessed a substantial increase in phosphorus. Within the Hydroprocessing Q&A session, we present a detailed response regarding the expected impact of phosphorus on hydrotreater catalyst.
SAM LORDO (Nalco Champion Energy Services)
Nalco Champion has developed a phosphorous sequestering agent. In the lab and in limited field trials, this product has been shown to react with free phosphate-ester compounds or derivatives to form a thermally stable complex and move the phosphorous out of the vacuum bottoms of the crude unit.