Question 66: Concerning new regulations for lower coke drum pressure prior to opening, what changes will you make?
MAYO (CITGO Petroleum Corporation)
There are options. You need a motive force to draw the drum pressure down to your target range of 0 to 2 pounds. Many refiners would consider which equipment was available and would be necessary to add. They were also looking at existing flare gas recovery systems where they were already operating at low pressure and then connecting to those systems. What is common, and what we are leaning towards, is installing ejector systems off of the blowdown system. We currently have one system in place. When you look at ejector systems, you need to take into consideration which mode of force you want to use. What are the limitations on your fractionator overhead system? Can you use recycled tail gas? Do you have horsepower? Do you have the loading available? Do you want to use steam? Steam is one of the options we are choosing. You have to take into account the additional duty on the overhead condensers, adding or making sure that you have sizing adequate there. The bottom line is that there are a lot of options available. It seems like ejectors fit this process really well, but we also have facilities looking at utilizing the available flare gas recovery compressors to lower coke drum pressure.
PRICE (Fluor Corporation)
There are a couple of refineries in Southern California that have been able to meet the new regulatory limits without any modifications, and they are among the fortunate few. Everyone can get to the 2 psig target in general, but not wanting to extend their drum cycle time is the issue. As Brent said, the use of ejectors is one of the favorite options. And of course, there are multiple locations where you can put that ejector effluent.
But once again, one of the factors to consider is where you would put your ejector. It depends, primarily, on the existing equipment design conditions, which are not often designed for vacuum conditions, and secondarily on the available condenser capacity (to condense the motive steam). Physically, where you locate the ejector is where you will have the ability to support the ejector, although the structure is not always available in the best location for the process.
We have also been looking into the use of control systems and interlocks so you can minimize your capital investment, improve your safety, and reduce any risks. And just a plug for this afternoon’s P&P, there will be a topic on this subject where the design consideration will be covered in significant detail.
SRINI SRIVATSAN (Amec Foster Wheeler)
Amec Foster Wheeler has several designs that could be incorporated in existing units to meet the expected EPA mandate of depressurizing the drums to 2 psig or less prior to opening the vent. Options include adding an ejector or vent gas compressor to lower the drum pressure. We also have a design to overfill the coke drum with water, but a separate overfill vessel is required in this case. The most typical option is to depressure the coke drum using vent gas ejectors. The sketch below shows the flow scheme using vent gas ejector.
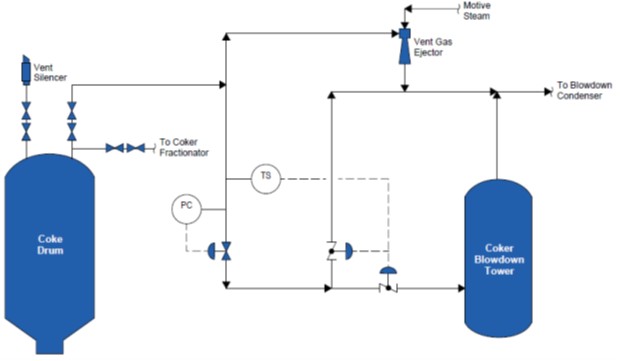
BRENT MAYO (CITGO Petroleum Corporation)
Options for reducing drum overhead pressures include utilizing alternate motive sources (compressors, ejectors, etc.) that operate at lower suction pressures (0 to 2 psig) to pull the remaining vapors away from the coke drum. Ejector systems are the most common method currently in use. Options as motive gas include recycling from tail gas compressors and steam. The motive chosen requires decisions made based upon current unit limitations to the compressors, fractionator overhead condensers, and associated equipment.
MAUREEN PRICE (FLUOR)
There are new Southern California regulations requiring the coke drum pressure to be below 2 psig before venting the coke drum to atmosphere. A few refiners have been able to meet the new regulatory rules with no modifications. The key is to achieve the 2 psig target with a minimum cut into the dead time at the end of the drum cycle.
The final solution must involve greater vapor recovery, which can be made through flare gas compression or ejectors (to lower the lower the drum pressure after drum cools down). The destination for the ejector effluent is dependent on many factors, too numerous to list in this setting, but common destinations include the coker fractionator overhead condenser, the coke drum overhead line to blowdown quench tower, or the vapor stream coming out of the blowdown settling drum.
The ejector location selected depends on the existing equipment design conditions (not often designed for vacuum conditions), the ability of the structure to support the ejector, and condenser capacity (for the motive steam and hydrocarbons).
Control systems and interlocks should be developed to minimize capital investment and improve safety and reduce risk.