Question 65: Please share experiences in crude tower fouling from organic and/or phosphorous-containing deposits.
PRIBNOW (CITGO Petroleum Corporation)
We have experience with two types of organic tower fouling. The first was an organic fouling in the top portion of the tower due to rerunning cracked slop oil, coker naphtha, and kerosene material. Typically, we do not want to do that. Since then, we have stopped processing those materials or limited the amount that we are rerunning so it does not happen anymore. The second incident we all want to talk about is the phosphorous organic fouling we observed at CITGO Lemont. We have experienced that type of fouling just above the kerosene draw in the crude tower. Our crude tower is a typical three-pumparound three-product draw tower with four-pass trays. What we began to observe was almost like a heartbeat. The tower was dumping liquid down the trays at regular intervals. The gas oil tray is a total draw tray; so, every once in a while, a rush of liquid came down and we observed an increase in the level in the gas oil stripper.
The pressure/level fluctuation intervals started getting shorter between events. We then took a look at the tower and at the common places where plugging could be seen, like in the top trays where you could have some salting if your salt point calculations were not right or if you were too cool. We ensured that we were 20°F ∆T (temperature differential) away from the salt point and ruled that out. We performed a tower scan and found that just above the kerosene product draw tray, there was some non-uniform plugging. Part of the tower would fill up, and part of it would dump. It was a very strange phenomenon which was not uniform across all four passes of the trays.
We tried some chemistry options, but they did not work very well. We did not see a significant change. We even tried condensate washing that section of the tower. We did not see a significant change with condensate either. What we did next was take some pumparound exchangers and rearrange them in the train. We moved them below the tower section that was plugged to try and remove heat. That marginally improved the situation in the crude tower. Then eventually, we installed two 12-inch vapor jumpers around those trays. The fouling was in a very specific place; and since we were not close to a turnaround, we were not ready for a complete shutdown. We hot-tapped the two jumpers around these fouled trays, and that worked well. We performed the work in January up in Lemont when it was 0°F. I have to say we did it safely. The guys were a little cold, but we gained back 15% of the lost capacity due to the plugging.
Here are two pictures showing observations of what we saw when we went in the tower at turnaround. This first two slides show a portion of the tray above the kerosene draw. Observe the fouled material that was plugging the fixed valves. This fouling material there is substantial.
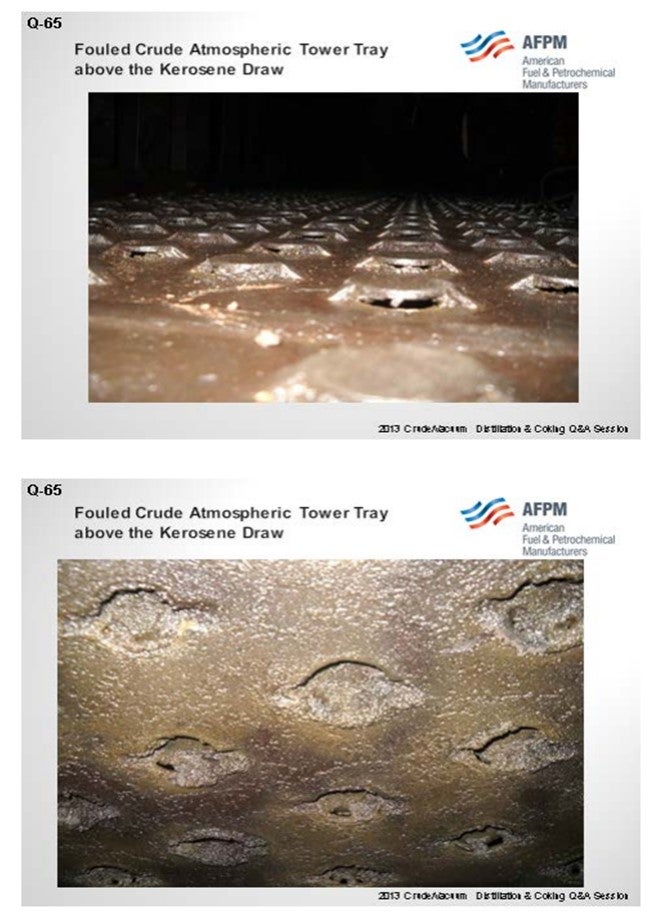
The next slide shows some of the samples taken by our engineers. We had it analyzed, and this is what we saw: carbon, oxygen, and that last component: phosphorous. That is really why we believe this was phosphorous organic fouling in this section. At turnaround, we made some modifications. We replaced the trays with some low fouling trays. We also replaced the top pumparound return distributor. Since that startup, we have not seen any degradation in this section. We feel those modifications will get us through the run.
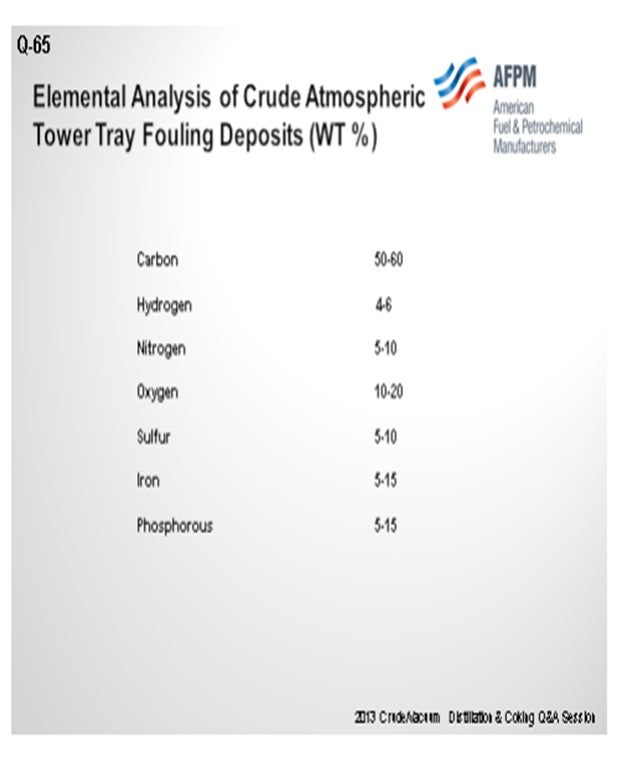
HERLEVICH (Marathon Petroleum Corporation)
In one of our plants, we had a very similar event with flooding in the kerosene section. It manifested as a downcomer problem. We scanned the tower and conducted other normal troubleshooting activities. We also consulted our friends at the Canadian Crude Quality Technology Association. They had seen very similar problems in the past and indicated phosphorous fouling, which is exactly what we discovered upon entry. We also found significant fouling in the pre-heat train. I have a couple of pictures here in the next slides.
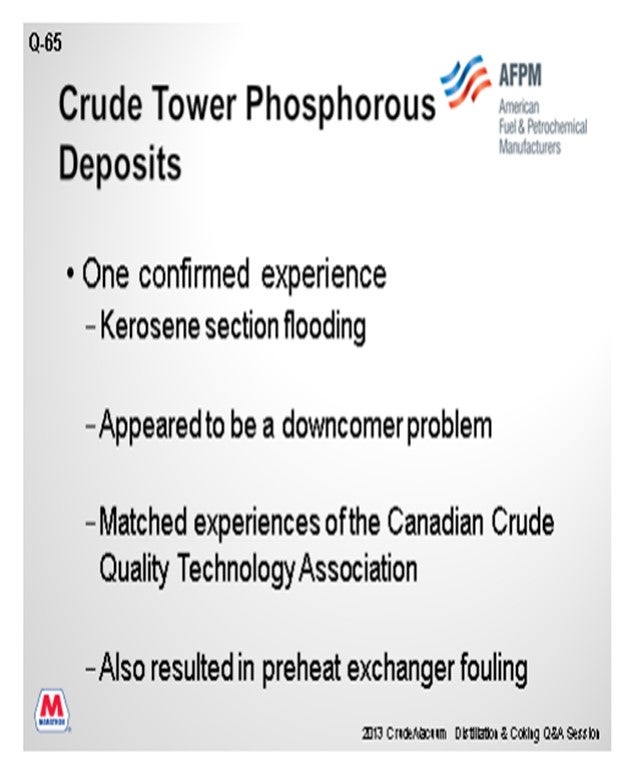
As an early online mitigation during the troubleshooting phase, we tried an organic acid wash without success. Long-term mitigation was upgraded in the trays in several sections of the tower to low fouling designs.
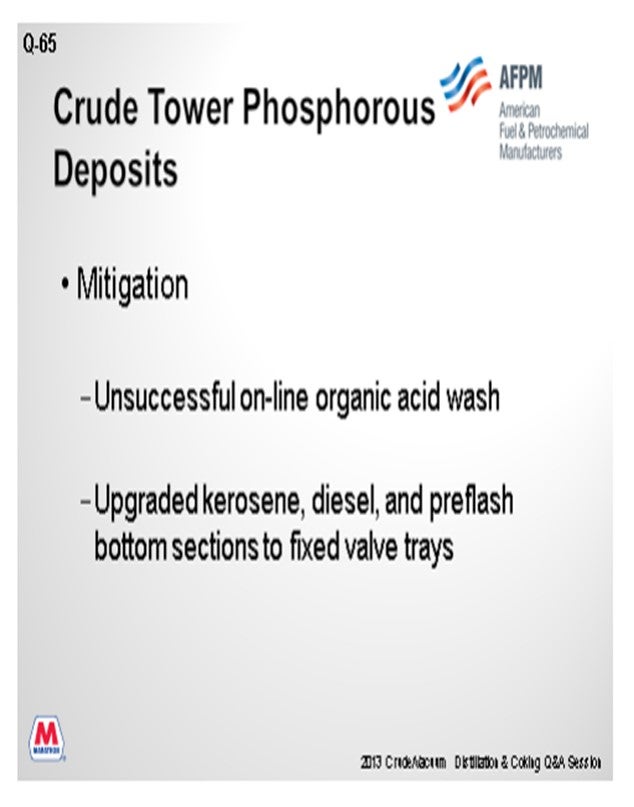
On the next slide, you can see how the trays looked when we opened the tower.
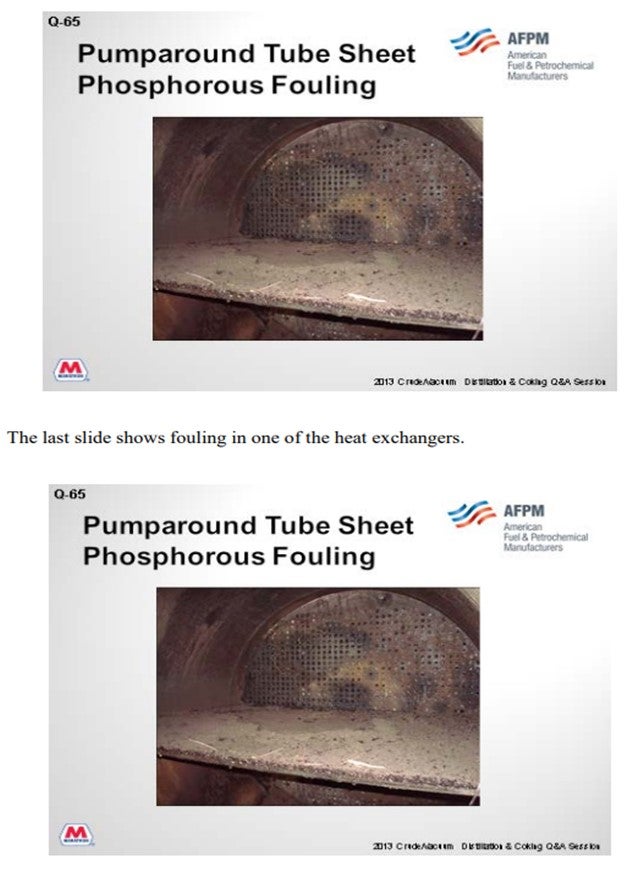
HODGES (Athlon Solutions)
In addition to phosphorus-based fouling compounds, please refer to my comments on Question 59 follow-up from the floor. Under special circumstance where you have elemental sulfur, filmer, and iron sulfide, you will form a rubbery fouling material on your A tower walls and trays.
MARIA ELIZABETH MARSIGLIA (Petróleo Brasileiro S.A.)
you trace back to where the phosphorous might have originated?
HODGES (Athlon Solutions)
The next question actually addresses that.
CELSO PAJARO (Sulzer Chemtech USA, Inc.)
the fixed valves, you have to be careful what kind of design you use. If you look at the picture from CITGO, you see that the tray has fixed valves that are plugged. So there are several features to take into account to avoid tray plugging. It is not only fixed valve that would allow the tray to have anti-fouling properties.
HECTOR GAMBOA-ARIZPE (CITGO Petroleum Corporation)
That picture was very similar to a situation at another one of our CITGO refineries. A word of caution: What ended up happening there is that we had corrosion in those trays during a previous turnaround. At the time, they were movable valves; so we would get some corrosion. The valves eventually fell out, so there were no DP issues. We upgraded the metallurgy on those trays. Now they are corrosion-resistant, but they started plugging up because there were no holes. So we went from a corrosion problem to a plugging problem, which we are addressing during this turnaround. That is just one situation that occurred when we went to a fixed-valve design with corrosion-resistant properties.
Now as Phil mentioned, we addressed most of that by just ensuring that a lot of the polymerants that were causing problems on that particular section of the tower no longer get in there at the same concentrations as before.
SAM LORDO (Nalco Champion Energy Services)
Phosphorous-related fouling of crude towers has been observed and tracked back to some crudes that use phosphate-ester-based fractionator gellants since the mid-1990s. The foulant is tenacious and appears to be focus in the kerosene-jet section of the tower. CCQTA (Canadian Crude Quality Technical Association), www.ccqta.com, has a long-term joint industry study on the subject. These particular gellant packages are used due to the geology of the field. In more recent times, a similar (maybe the same, but there is no definitive proof) type of foulant is being observed from processing crudes that either are crudes that are not produced using fracking techniques or those that are being produced from fields that geology would dictate using the less expensive fracking technique. For these crudes, it is suspected that some scale inhibitors may be involved.
CHRIS CLAESEN (Nalco Champion Energy Services)
We have had one or two applications in Europe where we have seen phosphorous coming in with the crude feed, resulting in fouling. The fouling is controlled by injecting a specific antifoulant into a return stream to the tower