Question 63 What is your refinery's first stage vacuum ejector configuration (single or parallel, idle/standby or all in service)? How do you evaluate your ejector system to determine if it is properly sized and performing optimally? Have you made any modifications to reduce steam consumption?
Rajkumar Ghosh (Indian Oil Corporation)
Typically, vacuum unit ejector systems have three ejector stages in series. Large crude vacuum units have multiple three-stage ejector system in parallel. Our system is designed with three-stage ejectors, each having three parallel ejectors with capacity distribution of 1/7th, 2/7th and 4/7th. We keep 4 to 5 ejectors (out of total 9) in line based on the requirement for maintaining the target vacuum level of 25 mm Hg(a). The average steam consumption is 60% of the design consumption.
The ejector systems have typical arrangement of ejector-condenser pairing, which reduces the load on the downstream ejector. The ejectors are sized based on predefined gas load, which consist of non-condensable (air + cracked gas), steam and condensable oil vapors. To ensure air leakage into the vacuum column is within acceptable limit, vacuum holding test (fall in vacuum <5 mmHg/hr) is carried out during commissioning and after every M&I shutdown. Generally, design incorporates enough margin to accommodate higher than normal air leakages that may be resultant of emergency shutdowns and start-ups.
Ejectors performance is expected to follow ejector performance curve, provided by the manufacturer as long as the motive steam pressure and temperature are kept close to design. However, comparing actual performance with performance curve is not easy as the estimation of gas flow often poses difficulties. In practice, we monitor the vacuum level and steam consumption for any unusual deterioration. It may be a good idea to provide a non-contacting type flow meter for estimating the non-condensable gas going out to furnace from the last stage ejector.
The under-performance of ejectors will be reflected in higher Vacuum column pressure. When an ejector system is under-performing, it is necessary to determine the specific cause for the underperformance. The process of troubleshooting is often by the process of exclusion. In our units, we have observed deterioration in the performance of ejector system due to following reasons:
a. Fouling in the inter-condensers is the most common cause for fall in ejector performance. We had couple of occasions, where the Fills from the cooling tower packing clogged the channel of the 1st ejector condenser. We had to take unplanned shutdown for the quick clean-up. Finally, we had provided a simple back-flushing system on the cooling water side, which paid rich dividend.
b. We also had occasions where, there was gradual deterioration of the ejector performance due to erosion in the ejector nozzles and had to replace the nozzles during the unit turnaround. Steam supplied to the system should be clean and dry. The header should be equipped with strainer and steam trap arrangement, and they should be maintained in proper health.
c. There are also occasions, when the vacuum column pressure gets temporarily elevated, which are generally traced back to inadequate long residue stripping in the atmospheric column.
Temperature and pressure values for the complete ejector system (upstream and downstream of each stage) are essential pre-requisite for effective troubleshooting of most ejector system. The field values are compared with the design data to ascertain the problem areas.
We have not done any modifications in our vacuum ejector system. Steam consumption is optimized by taking some of the parallel ejectors on-line or off-line based on the vacuum level in the column. We try to ensure that our spill-back valve remain closed all time.
Gary Gianzon (Marathon Petroleum Company)
Within the Marathon Petroleum Company LP (MPC) refineries we have multiple examples of first stage ejector configurations, ranging from a single ejector to three in parallel. In the systems that employ multiple first stage ejectors all are kept in operation. In the systems with multiple ejectors, the design load from the vacuum column has been split evenly across the ejectors.
An evaluation of the ejector system starts with the ejector performance curve provided by the ejector manufacturer. This is an example of a performance curve for a first stage ejector, and is typical. The minimum motive steam pressure, with temperature, is listed along with the maximum discharge pressure of the ejector. These two variables must be satisfied before any determination of adequate sizing and optimization can be made. If either the motive pressure is below the design point or the discharge pressure is above the maximum design point, the ejector would be expected to break and not perform as designed. When these two design variables are met, a properly functioning ejector will follow its performance curve.
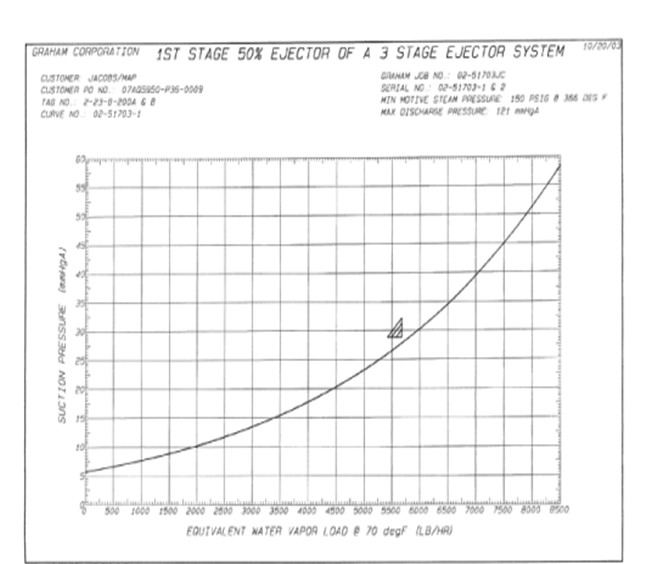
The performance curve is a plot of the equivalent water vapor load from the tower against the suction pressure of the ejector. In this example, the ejector was designed to process 5,757 #/Hr of equivalent water vapor from the tower at a suction pressure of 28.8 mmHgA. At a tower load less than this amounts the suction pressure will drop accordingly, following the curve. In converse, if the ejector load is higher than design the resulting suction pressure of the ejector will be greater. If the ejector is following the curve, it is considered operating per design and no further optimization is warranted. An ejector operating at a point above the curve would be an indication of a problem with the ejector system with further troubleshooting required.
In systems that employ multiple ejectors the load from the tower can be evaluated and an ejector shut down to reduce steam consumption. This is the only avenue for reducing steam consumption, as the minimum motive steam pressure is set by design. The tower load would subsequently be distributed across fewer ejectors, with the performance curve followed to determine if the resultant inlet pressure is acceptable. This is certainly a feasible option during turned down operation. Depending on the configuration of the first stage condensers, the tower load may be then processed across fewer condensers also, with a possible unacceptable increase in pressure drop. The ejector outlet pressure must be confirmed to be below the maximum allowable pressure for the remaining ejectors to function properly.
MPC has not made modifications to reduce steam consumption, except in turned down operation. Rather, MPC strives to take advantage of the reduced tower pressure.