Question 63: How are refiners monitoring and controlling the efficiency of fired heaters? Are adjustments made to fuel gas composition to improve heater performance?
PRIBNOW (CITGO Petroleum Corporation)
At CITGO, we utilize both daily monitoring tools and weekly programs to rank the heaters based on performance and missed opportunity. Optimization targets get set based upon best efficiency points, and the consoles are expected to be at these optimization points. These efficiencies are reviewed daily for potential issues that may de-optimize the heater. We also have a real-time monitoring program in our PI System. The operators just pull up the PI to see the efficiency of their heaters and if there were any missed opportunities.
efficiency calculations are based upon API 560. We have an efficiency target, and we have actual O2 targets. We also have duty differences where we can do some calculations for the console personnel. Console operators have the ultimate ownership in the heaters. They can either make moves from the console or call their operators outside to have them tuned. We provide the operators and the console heater-tuning classes every year or two to make sure they stay fresh and trained on how to properly tune a heater. We also give them a troubleshooting tree on how to properly tune a heater.
Operators outside perform their daily rounds. First, they check flame patterns and color. They then note how the heat is distributed in the heater. They check for even-glowing firebrick or cold spots. This analysis determines if there is a fouled burner or not, as well as if there is excessive header pressure on your fuel gas. So, when we see these conditions, we will have the operators take the burner out of service. We will clean it and then put it back in service.
When we take these burners out of service and disconnect them, we are careful to note the proper burner tip hole orientation. Tip alignment must be set prior to reinstalling. We experienced a burner tip that was not set properly, and the flame was shooting out to the side. Luckily, we caught that alignment issue quickly. Ensure there is a proper PSSR (pre-startup safety review) process for putting the burner back in service.
Some of our heaters have boiler feedwater or economizer sections to promote better efficiency. A word of caution: Make sure outlet temperature indicators are properly alarmed. If temperatures increase, super-heated steam will be generated and there is a potential to fail the tubes. We had an experience where we failed a set of boiler feed water tubes in the heater due to overheating.
Lastly, the question asked if we adjust fuel gas. At CITGO, we do not adjust fuel gas to increase the Btu (British thermal unit) content to fire harder or affect heaters. Often, we will dump excess hydrogen to fuel gas that will depress the Btu value. It is not a common practice, and we do not like doing it; so, we will try to avoid it, if at all possible, because it does affect the heaters. Typically, we will not vaporize propane or butane into the fuel gas or reduce recoveries to improve Btu valve to the heaters.
SRIVATSAN (Foster Wheeler USA Corporation)
There are a few issues that affect the performance of the heater including the source of fuel gas, heater mode of operation, and automation and controls that are in place. The DCU (delayed coking unit) is a net exporter of fuel gas, so the refiner has a choice to either use the DCU fuel gas in the heater after it is amine-treated or send it across to the refinery header and bring the gas back from the mixing drum. If you use the DCU off gas after amine-treating into the heater, the composition is expected to be fairly constant, unlike refinery off gas that may, at times, exhibit a spike in the hydrogen content or the LPG (liquefied petroleum gas) content. But the DCU fuel gas could exhibit variations or swings in the flow, especially when you switch the drums. If you are expecting spikes in hydrogen or LPG content in the refinery off gas, then an online analyzer would be required to monitor the heating value.
As far as the flow gas variation in a DCU, I have a couple of slides that exhibit the phenomenon. The first slide is a two-drum coker operating on a 20-hour cycle, which means that a drum is switched every 20 hours. So as we can see, each time a drum is switched, the fuel gas rate dips significantly. On a two-drum coker, the dip is about 20%. It takes about two and a half hours to bring the fuel gas back to the average values.
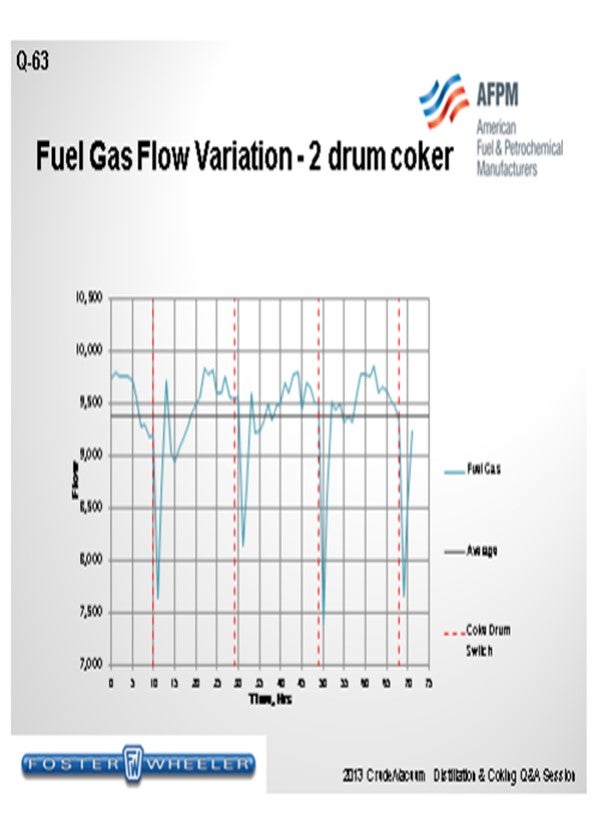
This slide contains data from a four-drum coker. The effect of the swing in fuel gas during a drum switch is mitigated as you have more coke drum modules. This four-drum coker operates on a 16-hour cycle, which means that a drum is switched every eight hours. In this case also, there is a swing in the fuel gas flow rate. However, it is not as rapid: about 10%. If you operate your coker on shorter cycles, you will have to account for that, as well as the flow variations being more frequent. Also, if you route the blowdown vent gas back into the coker, as is normally done these days, you must account for the effect of the blowdown composition and flow rate. Although there is a dip in the fuel gas flow rate, it normally should not affect the coker heater because the coker is a net exporter of fuel gas, provided your controller is attuned properly. That is the key.
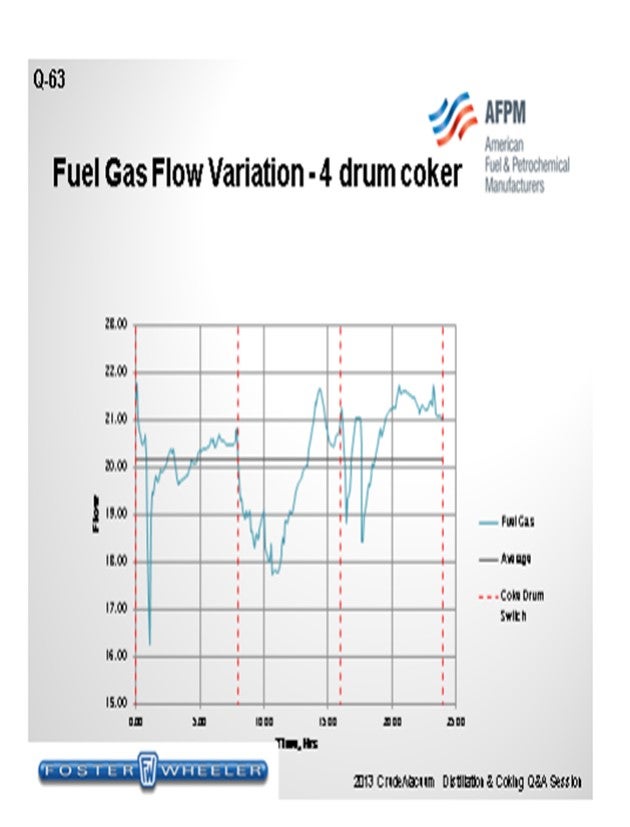
The next issue is the type of heater operation. The heater could operate in a natural draft or balanced draft mode. Now most of the natural draft furnaces do not have automated control of the air registers or stack dampers. The operators basically set it in a fixed position and leave it. So, you get more excess air than what you normally would require, which affects the efficiency of the heater. On the other hand, the balanced draft furnace can offer higher efficiency as the air flow can be automatically controlled. The efficiency could also be increased further if you have an air pre-heat system. Additionally, it is easier to implement a lead-lag algorithm or an air-fuel cross limit in a balanced draft heater.
Lastly, automation and controls in place. By far, the most effective way to control and monitor heater efficiency is to have the required instrumentation. These include an online heating value measurement for fuel gas (either a calorimeter or Wobbe Index Analyzer), air and fuel gas flow measurements, analyzers for oxygen combustibles and CO (carbon monoxide), automated stack damper control for draft control, and automated guide vanes on FD (forced draft) and ID (induced draft) fans.
HECTOR GAMBOA-ARIZPE (CITGO Petroleum Corporation)
You mentioned a Btu analyzer or a calorimeter when you have compositional changes due to the coker cycle and refinery fuel gas. Do you all typically tie that to either vaporizing the propane or the reduction of sponge oil to the sponge absorber to control the Btu content, to steady it out, or just to control the heater itself (meaning, instead of feedback control)? Or are you using it to stabilize the Btu value itself?
SRIVATSAN (Foster Wheeler USA Corporation)
No, it is a measurement tool used to understand what is going on. Typically, when we design the Foster Wheeler fired heaters, we prefer to take the gas from the coker unit itself as it is a net exporter. In that case, we do not have a Btu analyzer. It is only when you are using or supplementing with LPG or other fuels that you may want to have one. Also, if you are bringing fuel gas from the refinery mixing drum and have other situations occurring (such as a hydroprocessing unit down or a startup/shutdown scenario where you expect wide variations in fuel gas flow), then it may make sense to have a calorimeter.
HECTOR GAMBOA-ARIZPE (CITGO Petroleum Corporation)
Does anyone in the audience stabilize Btu content by either adjusting the sponge oil on the gas condenser absorber or vaporizing a propane/LPG?
PUI-NANG LIN (Flint Hills Resources, LP)
We typically do not automatically adjust the sponge absorber with LPG recovery, but our fuel gas system does have a Btu analyzer which allows us to raise our Btu content with additional purchased natural gas, if necessary.
HERLEVICH (Marathon Petroleum Corporation)
We do not tie Btu analyzers into control schemes. They are an indication which aides' rapid response by the operators.
RICHARD DOSS (CITGO Petroleum Corporation)
Our experience at Lake Charles is that the bigger upsets are caused by hydrogen introduction into your fuel systems since there is such a large difference in the Btu value. What we do have is some ability to not send disturbances in the reformer area into our fuel gas system by giving them another outlet. In doing so, we take away some of the disturbances in the fuel gas system.
UNIDENTI FIED MALE SPEAKER
Be very careful about adjusting Btu values, particularly if you are doing it in sponge absorption or other places of recovery. We had a bad incident when we did not have good procedures for doing that, and we got overzealous. It actually created a lot of liquids in the fuel gas system, which caused some problems. Stabilization sounds good on paper. It is probably better to deal with unit instability than trying to create another permutation to fix it.
MEL LARSON (KBC Advanced Technologies, Inc.)
One of the key questions was about oxygen content. In our review of refineries around the world, we have found that there is no diligence necessarily in place to trash oxygen getting bled into the furnaces. Flame temperature and patterns were mentioned as ways to control it. I highly recommend training your staff on that procedure. Also train them to ask, “Do we have holes around the tubes that are just bringing in air so that our oxygen analyzer is not really reading combusted oxygen?” It is actually reading a lot of the trash oxygen that comes into the furnace, which really makes control cycle downward. The operators have a target to hit, and the flame pattern looks bad. You will actually get flame impingement on tubes and accelerated coking. So first, go out and confirm that your fire box is tight. And at turnaround, make sure you have all of those potential holes and peep doors closed, which are two other problems that have occurred in the past. Then you will be able to really tighten up your furnaces and get good performance.
HERLEVICH (Marathon Petroleum Corporation)
Just to add on to that, one method for finding tramp air ingress locations is to toss a non-toxic smoke generator into the firebox and run the forced draft fan. Use the stack damper to hold slight pressure, and smoke will evolve from the heater casing at leak points. We have been successful with this approach on boilers.
SRIVATSAN (Foster Wheeler USA Corporation)
You must also pay attention to the piping configuration to the burners. You should have a fuel gas knockout drum close to the heater, as well as strainers on the line going into the burners. You should also insulate the fuel gas line and heat trace in a cold climate to avoid the problems of condensation or hydrocarbon liquids going into your fuel gas burners.
SRINI SRIVATSAN (Foster Wheeler USA Corporation)
The most efficient heater is one that results in complete combustion of fuel gas with the least amount of excess air. To that end, the best operation is to achieve the lowest oxygen content in the stack at the lowest draft and stack temperature but stay in the safe practice's region of -0.1 inches of water column draft and 2 to 3% excess oxygen. Listed below are a few points to consider while monitoring and controlling heater efficiency:
1. Source of Heater Fuel – if internally drawn from the unit [as the delayed coking unit (DCU) is a net exporter of fuel gas] or if drawn from the refinery fuel gas mix drum,
2. Heater Operation – natural draft versus balanced draft, and
3. Automation/controls – properly placed.
Source of Heater Fuel Double-fired coker heaters use only fuel gas for firing. If the source of fuel is amine-treated coker off gas only, then the composition is expected to be more stable compared to refinery off gas (ROG). ROG, at times, may have a spike in hydrogen content or C3/C4 LPG that will affect the heat content. Ideally, this requires an online composition analyzer with advanced automation to monitor the heating value.
Off gas from the DCU, while having a relatively stable composition, exhibits a flow variation during drum switches. This should not be an issue to the heater as the coker is a net exporter of fuel gas, provided the controllers are tuned properly. If the blowdown vent gas is recycled back to the coker gas compressor, as is typically done today, the effect of the blowdown vent gas on the gas flow rate and composition has to be taken into account. If the source of the heater fuel is DCU off gas, we recommend sending the entire DCU off gas to a knock-out drum located close to the heater. Excess gas after providing fuel to the heater is sent to refinery battery limits. Attention should also be paid to the piping configuration to the burners with strainers in the main line and insulation/heat tracing (cold climate) to avoid any hydrocarbon condensation.
Shown below is the effect of the DCU off gas rate in two-drum and four-drum delayed coking units. Fuel gas flow rate dips approximately 21% for two-drum unit and 11% for fourdrum unit during drum switches. In a two-drum unit, it may take as long as two and a half hours for the off gas flow to come back to normal levels. Operating shorter cycles will cause more frequent disturbances to the flow rates.
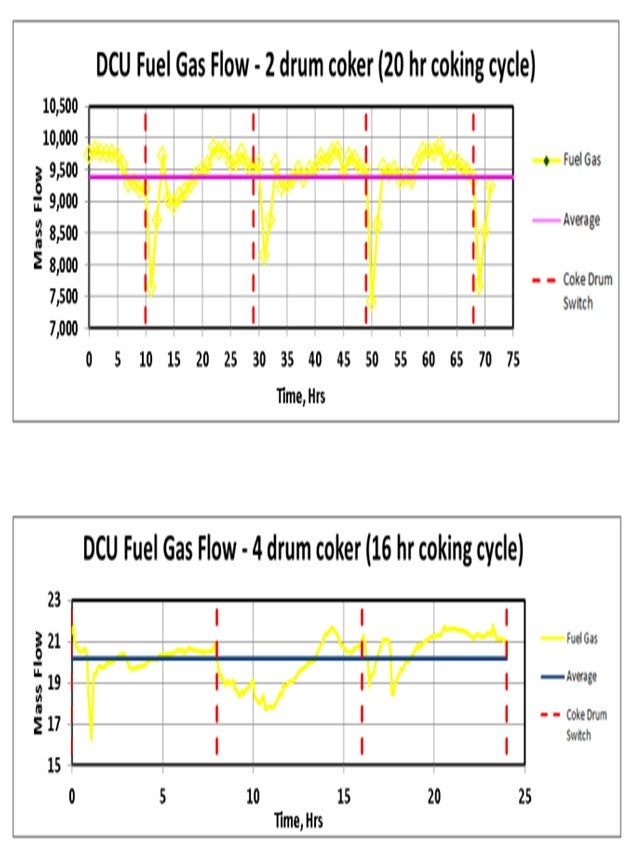
Type of Heater Operation: Natural Draft versus Balanced Draft
Most of the natural draft furnaces do not have automated control of the air registers or stack dampers and rely on operators to adjust them. The experience has often been that these dampers are set at one fixed position, providing more than the required amounts of excess air, resulting in lower efficiency. Balanced draft furnaces, on the other hand, can offer higher efficiency as the air flow can be automatically controlled. The efficiency could be further increased with the use of air pre-heat system. It is also easier to implement an air-fuel cross limit in a balanced draft heater.
Automation/Controls
By far, the most effective way to control and monitor heater efficiency is having the proper instrumentation required. These include:
1. Online heating value measurement for fuel gas (Calorimeter or Wobbe Index Analyzer),
2. Air and fuel gas flow measurement,
3. Analyzers for O2, combustibles and CO,
4. Automated stack damper control for draft control, and
5. Automated guide vanes on FD (forced draft) and ID (induced draft) fans.
Foster Wheeler double-fired balanced draft heaters have the ability for individual pass flow and firing control, which provide maximum flexibility in monitoring and controlling efficiency. Typically, no adjustments are made to the fuel gas composition. However, there is always a secondary source of gas as backup to the heater fuel. Most times, this is natural gas that is also used in the pilots. In places where natural gas is unavailable, vaporized LPG could be used as a backup source for heater fuel.
GARY HAWKINS (Emerson Process Management)
Since refinery fuel gas composition can vary at any time, refiners have been measuring the flow of refinery fuel gas on a mass basis rather than a volume basis for many years. The reason is that the heating values of light hydrocarbon gases on a mass basis are very similar to the heating value of light hydrocarbon gases on a volume basis. Thus, by controlling mass flow, the refiner has a better grasp of how to control the heat input to the heater in order to maintain a given objective temperature at the combined outlet as the composition of the fuel gas varies, if the fuel gas is primarily hydrogen and light hydrocarbon gases.
traditional scheme for measuring a mass flow of fuel gas with an orifice plate is to use an online density meter, too. The square root of the measured gas density at the operating conditions of the orifice, multiplied by the measured differential pressure across the orifice plate, will give a signal that is proportional to mass flow of the fuel gas. The flowing density measurement of the gas already accounts for changes in flowing pressure and temperature. The second edition of API RP 556, “Instrumentation Control and Protective Systems for Gas-Fired Heaters”, now recognizes mass flow measurement using Coriolis flow technology as a recommended practice. It should also be noted that if the content of non-combustibles in the fuel gas were to vary, then the relationship between mass flow and heating value would vary. This should be considered when the refiner discharges gas to the fuel gas system that may contain varying amounts of non-combustible components such as PSA (pressure swing adsorber) tail gas, flare recovery gas, and storage tank recovery gas. In these cases, a gas chromatograph can be considered to monitor the fuel gas composition.
Emerson Process Management offers a pre-engineered fired heater optimization and control solution with cross-limiting combustion control and uses Model Predictive Control (MPC) to adjust the fuel and air demand and pass flows to reduce excess combustion air and meet process control objectives. Typical constraints include control valve and damper limits, fuel pressure, heater temperatures, and draft pressure.