Question 63: Certain crudes are treated with H2S scavenger to meet a 10 ppm or less specification in the vapor space. In your experience, what is the disposition of the reacted and unreacted scavenger additive through the crude unit? Will this product and/or associated byproducts create corrosion or product quality issues in the crude unit or downstream units?
Jim Johnson (Marathon Petroleum)
The majority of H2S scavengers used today are water-soluble, cyclic amines which can quickly react with H2S, forming a water-soluble reaction product. However, these amine-based scavengers are not without potential problems. As formulated, these scavengers often contain un-reacted amines. In addition, low molecular-weight amines (such as MEA) are generated as side-products via the scavenging reaction shown.
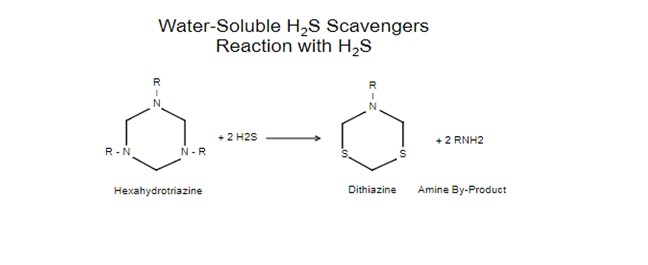
Under certain processing conditions, these amines can undergo a vapor phase reaction with hydrochloric acid (HCl) and produce salts. When deposited on equipment surfaces, these HCl salts can generate unacceptably high corrosion rates and associated fouling. Distillation towers and towers overhead condensing systems are particularly susceptible to this under-salt corrosion when amines are present in tower feeds.
MEA-HCl Salt Formation Field Example
• Exchanger tube failures in TPA circuit.
• Evidence of MEA-HCl in deposits.
• Periodically, crude blends contained MEA. -MEA present in desalter water and atm. OH water. -Suspect H2S scavenger treatment.
• Calculated MEA-HCl temp. range: 230-260 deg F -
Within range of tower operating temperatures.
We experienced a recent problem with amine-HCl salt formation in the Top Pump Around (TPA) exchangers of an Atmospheric Tower. Localized deposition occurred on the shell-side of the TPA exchangers which led to tube failures with MEA-HCl salts identified in the exchanger deposits. Analytical measurements indicated the intermittent presence of MEA in the process, presumably from upstream H2S scavenger treatment. For typical tower operating conditions, there was potential to form MEA-HCl salts in the tower and in the TPA circuit.
Mitigation Strategies:
• Blend crudes to reduce contaminant levels.
• Increase monitoring frequencies
• Improve Communication
• Between producers and refiners
• Between additive suppliers and refiners
• Treat with alternative scavengers
• Oil-soluble rather than water-soluble
• Modify desalter operation
• Reduce desalter wash water pH
• Increase wash water %
Troubleshooting efforts can be difficult since crude cargoes may only be treated intermittently. As such, the effects of these scavengers are often transient in nature. Frequent sampling is often required to identify the presence of these additives. Mitigation efforts can also be hampered because refiners rarely have knowledge that these additives are present in the crude.
Benefits can be realized through improved communication between producers, refiners and the chemical vendors who supply the additives. For example, chemical vendors offer alternate, oil-soluble H2S scavengers which form more thermally stable reaction products than those of amine-based scavengers. However, oil-soluble scavengers contain more expensive raw materials than water-soluble scavengers and higher application costs often preclude their use.
Organizations such as the Crud e Oil Quality Association (COQA) and the Canadian Crude Quality Technical Association (CCQTA) have been established to provide details on the quality of various crude types and to foster communication between producers and refiners.
Improved monitoring techniques at the refinery, such as more frequent analyses of raw crude blends and more frequent use of ER probes in overhead systems can provide an “early warning” of potential problems.
Modifications to desalter operation can help reduce the formation potential of amine-HCl salts in tower overheads. For example, reducing the pH of desalter wash water can minimize the amounts of amines which remain in the desalted crude.
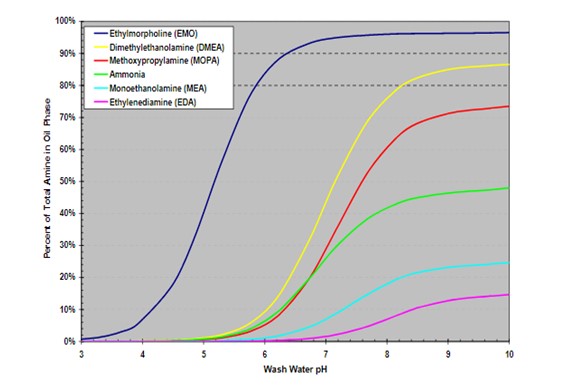
As shown in the graph, the partitioning behavior of amines is strongly a function of amine type and of desalter water pH. With a thorough knowledge of this amine behavior, a proper operating range for desalter water pH can be determined. In addition, an increase in the wash water rate can enhance the fraction of amines which partition to the desalter effluent water.
The consequences of amine contamination are most notable in the crude unit but may extend to other refinery processes as well. Light ends distillation systems can be affected when the naphtha feed to the system contains entrained water from the crude overhead drum. The entrained water can carry amine and HCl contamination to the light ends' unit.
Entrained water in the naphtha can also carry amine contamination into the naphtha hydrotreating units, contributing to ammonium chloride deposition in the reactor effluent section.
Heavier sidestream hydrotreaters may also see amine and HCl contamination. In these situations, amine salts formed in the crude atmospheric tower can be carried down the tower to these side draw trays. As in the naphtha hydrotreating unit, the amines can contribute to ammonium chloride deposition in the reactor effluent circuit, and subsequent increased potential for corrosion.
Doug Meyne (Champion)
A refiner is most likely to encounter high levels of H2S scavengers in seaborne crudes since vapor space concerns are highest during loading and unloading. Most H2S scavengers sold today react to form a non-reversible product; however, some (MEA, EDA) can form reversible reactions when exposed to heat. Most unreacted scavengers will partition to both the oil and water phase in the desalter. A significant portion (50+%) can leave with the water and cause significant issues at the wastewater treatment plant creating nitrification issues with the bugs. Unreacted scavengers leaving the desalter in the oil phase will ascend the tower and form chloride salts, usually above the dew point of water. These salts will foul trays, create corrosion issues in the tower, diesel, kerosene, and heavy naphtha run down lines, and create corrosion and fouling problems in hydrotreater filters and feed/effluent exchangers. Depending on the scavenger used and crude tower overhead temperatures, there have been reported cases of deposition and corrosion in the overhead condensing system.
Frank Tracy (ConocoPhillips)
We have experienced atmospheric crude tower overhead corrosion / fouling at two refineries that has been attributed to amine based H2S scavenger in the crude supply. We are not aware of any product quality issues.
Sam Lordo (Nalco Company)
There are a number of papers written on this subject, for example, “Chemistry And Impacts Of Commonly Used Amine-Based H2s Scavengers on Crude Unit Towers and Overheads”, JM Garcia and SA Lordo, NACE 2007 Paper No. 751, and “Crude Distillation Unit- Crude Distillation Tower Overhead System Corrosion”, NACE International Publication 34109 (2009 Edition).