Question 60: When is your return on investment (ROI)adequate to justify installing a desalter to treat purchased FCC feeds? What other factors besides FCC catalyst impact and unit corrosion are used to determine ROI? How do these desalters differ, mechanically and operationally, from a conventional crude oil desalter?
PHILLIP NICCUM (KP Engineering)
This is a three-part question. The first question is: When is the return on investment (ROI)adequate to justify installing a desalter to treat purchased FCC feeds? The capital and operating costs of an FCC feed desalter are supported by improvements in performance, operating costs, and reliability. The ROI is adequate when the capital is available, the project fits owner’s strategic goals, and it meets or exceeds available return on other relevant investments. The ROI threshold number is very site-specific.
The second question asks: On what is the ROI based; for example, FCC catalyst impact and unit corrosion? Desalting improves FCC feedstock in three major ways:
1) reducing salt content,
2) eliminating entrained water and slugs of water, and
3) reducing particulates and other contaminants in both the water and the oil.
Desalter installations for purchased FCC feeds are typically justified by the savings in FCC catalyst makeup costs from reduced FCC feed sodium content.
The sodium content of imported FCC feed and the percentage reduction in feed sodium content alone are not the only variables impacting the ROI of an FCC feed desalter. Residue FCC units with higher feed vanadium and nickel contents, even without sodium contamination, operate with much higher catalyst addition rates than gas oil FCC units to control catalyst activity, and this tends to buffer the impact of the sodium contamination. Therefore, calculated estimates of catalyst savings must be made using the particulars of the FCC feedstock and operation in question. See the Answer Book (1) below for a few examples.
Another important factor in the ROI is whether or not the desalter would be used continuously or just part-time.
The side benefits of the FCC feed desalting usually just reinforce the catalyst cost-based justification, including
*Fewer FCC unit upsets due to shots of water coming straight into the unit,
*Reduced concentrations of calcium and iron on the FCC catalyst,
*Reduced ammonium chloride salt formation at the top of the main fractionator, and/or
*Removal of particulate matter that contaminates the catalyst.
The last question is: How do these desalters differ mechanically and operationally from a conventional crude oil desalter? Mechanically speaking, FCC feed desalters and crude oil desalters are basically the same. Both types of desalting units remove contaminants by employing electrostatic precipitation to separate a hydrocarbon/water emulsion. Each type of unit is composed of an ASME Section VIII, Division 1 process vessel containing a set of internal electrodes (grids) and distribution headers, with a transformer(s) mounted on top of the vessel. The size of the process vessel and the number and KVA rating of the transformers is dependent on the characteristics of the feedstock, the design flowrate, and other operating and process parameters. The focus of FCC desalting is typically sodium reduction for protection of catalysts, whereas crude oil desalting seeks to remove water and associated salts for corrosion protection in the crude distillation unit and overhead circuit. Both types of units may also remove an appreciative number of solids that enter with the feedstock and, as such, may contain specialty internals (headers and spray nozzles) that facilitate “mud-washing” of the unit at some frequency. Even though FCC feed desalters and crude oil desalters are basically the same, there are several lessons learned from FCC feed desalter projects that warrant consideration in new FCC feed desalter installations.
1.Controlling sodium content in purchase FCC feed is nearly impossible. Even if purchased FCC feeds have not been shipped by water, FCC feed desalting may still be required. It cannot be assumed that purchased atmospheric residues or topped crudes have already been desalted properly or even desalted at all.
2.Some crude topping operations use significant amounts of caustic rather than desalting to suppress chloride hydrolysis in crude unit heaters. This caustic can add 7 to 10 pounds of sodium per 1000 barrels over that of the base native crude.
3.If imported FCC feeds will not be processed all the time, provisions in the system design and mothballing procedures for part-time operation of the desalter are important to prevent corrosion and fouling issues while the desalter is offline for extended periods.
4.Operating the desalter on feedstocks that do not need desalting can be an economic burden:
a. The water content of the FCC feed may increase through the desalter.
b. Depending on the quality of the desalter makeup water, running the FCC feed desalter on internally produced gas oils can increase gas oil contaminant concentrations.
c. Unnecessary expenditures are incurred for desalter chemical additions.
5. Reduced crude, which comes directly from crude desalting and distillation operations, contains no free water but includes salt in crystalline form. Therefore, makeup water for FCC feed desalters should be installed as far upstream of the desalter as possible to give salt crystals the maximum opportunity to dissolve. See the Answer Book (2) below for more information on this topic.
6. As with crude desalters, FCC feed desalter makeup water should be of suitable quality. It is possible to reuse refinery water streams, like sour water stripper bottoms and vacuum tower ejector condensate, as desalter washwater. See the references given in the Answer Book for additional information. Since reduced crude, topped crude, and even whole crude from paraffinic tight oils are often good candidates for FCC processing, some general considerations for desalting tight oils or other highly paraffinic crudes are also included in the material and references provided in the Answer Book (3) below.
Consideration #1
Some examples of estimated reduction in catalyst makeup rate are included below to demonstrate that more than feed sodium content and an estimated percent reduction in the feed sodium content are needed to derive the catalyst saving benefit of a desalter installation. Other parameters of the FCC operation–for example, the nickel and vanadium content of the feedstock–also play an important role in estimating the impact of the desalter on FCC catalyst makeup rate. For example, in hypothetical 50,000 bpd FCCU operations shown in the following table, an FCC unit processing some residue with 3 ppm sodium in the total feed and a gas oil FCC unit with 3 ppm sodium in the feed may expect different catalyst makeup reductions from a new desalter installation,assuming a 90% reduction in sodium. In these cases, the catalyst makeup for the gas oil FCC unit would be lowered by 2.2 tpd (tons per day) while the residue FCC catalyst makeup rate would be reduced by only 1.3 tpd.
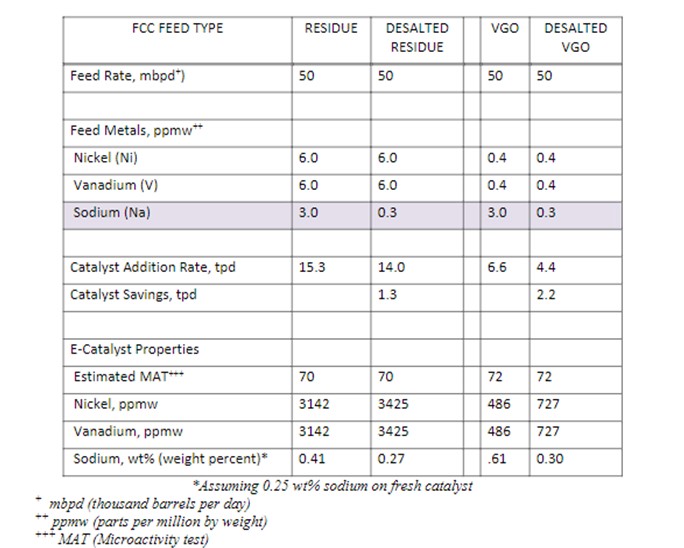
Another set of examples is included in the next table where the base sodium content of the feed is increased from 3 to 6 ppmw. In these examples, the VGO operation still shows a larger estimated reduction in FCC catalyst makeup for the desalted feed.
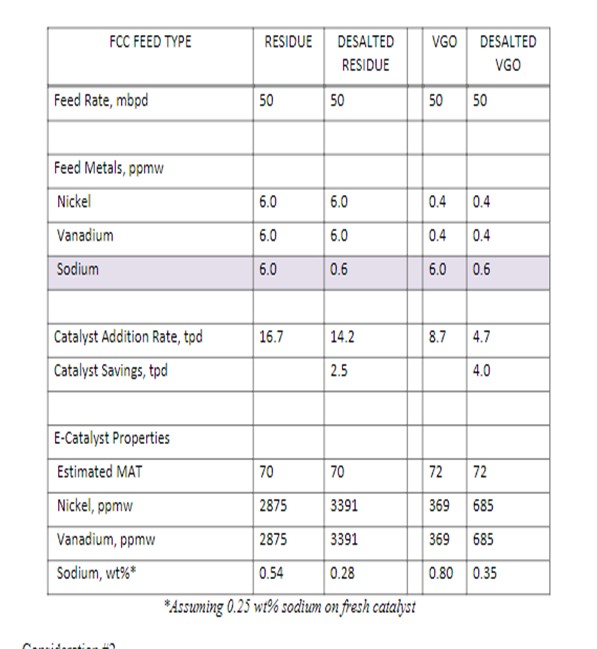
Consideration #2
Reduced crude which comes directly from crude desalting and distillation operations contains no free water but includes salt in crystalline form. Therefore, since imported feeds may have been previously desalted, makeupwater for FCC feed desalters should be installed as far upstream of the desalter as possible to give salt crystals the maximum opportunity to dissolve into the added water. (In crude desalters, a good portion of the salt in the raw crude is dispersed in the water produced with the native crude.) Plant operating experience has shown that salt dissolved in water is much easier to remove in the desalter than crystalline salt in the oil phase. Therefore, since imported feeds may have been previously desalted, makeupwater for FCC feed desalters should be installed as far upstream of the desalter as possible to give salt crystals the maximum opportunity to dissolve into the added water.
The two figures show the feed and effluent of a desalter processing imported LTO atmospheric residue filtered through 0.45-micron glass fiber filter paper and toluene rinsed. Based on salt levels, the feed was either not desalted, poorly desalted,or a purchased blend of desalted and non-desalted atmospheric residues.
Testing showed that the material on the filter paper was predominantly carbon, oxygen, sodium, chlorine, and iron. The testing was done with SEM/EDS (Scanning Electron Microscope/ Energy-Dispersive X-ray spectroscopy), which is unable to detecthydrogen.
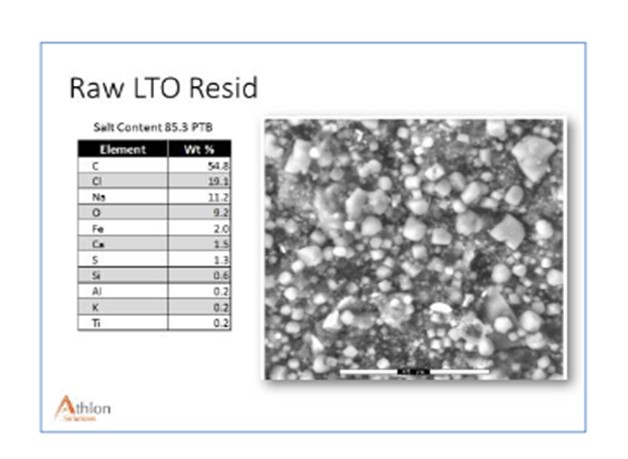
Slide Two shows the oil after desalting, caught at the same time as the raw oil in Slide One. The SEM image of filter paper showed significant NaCl, or salt, removal but very little impact on some of the other cations. Iron removal was insignificant from a total mass basis. A significant amount of iron was siderite rather than iron oxide or iron sulfide and was not easily removed with waterwashing. Phosphorus and barium are indicative of chemical treatment to prevent barium sulfate scale inhibition in formation.
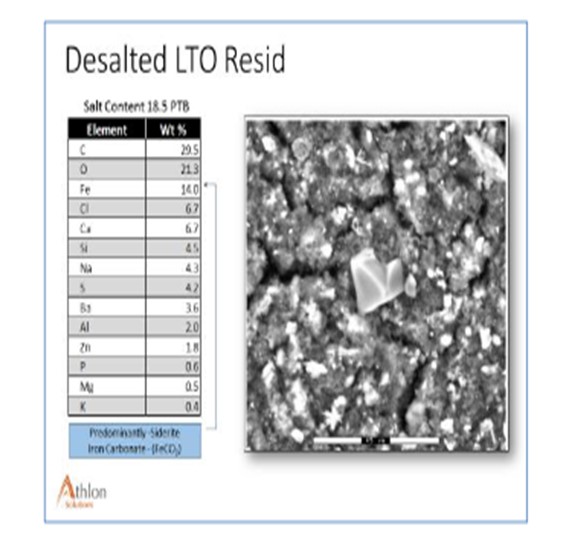
Slide 3 shows the estimated amount of each element removed in the desalter. The Na, Ca, Cl[sodium, calcium, and chloride], and some sulfates are readily removed. Iron and other metals are not removed as easily, and non-traditional techniques may be needed (pH adjustment).
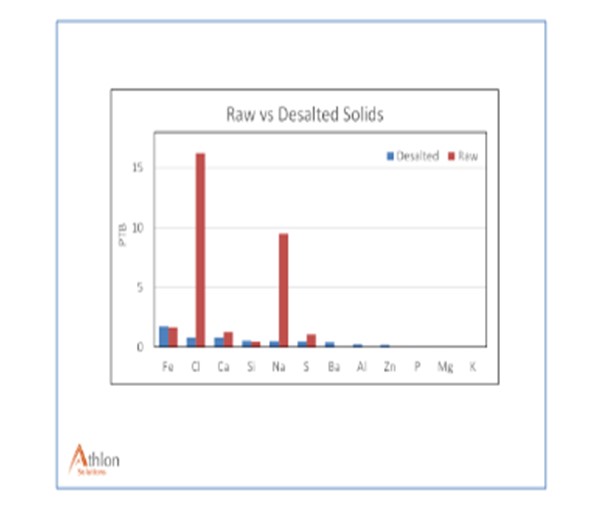
Consideration #3:
Since reduced crude, topped crude, and even whole crude from paraffinic tight oils may be good candidates for FCC processing, some general considerations for desalting tight oils or other highly paraffinic crudes are also included in the references provided in the Answer Book. A few items of note are listed below:
*Common tight oil characteristics include high levels of very fine filterable solids and alkaline metals, calcium, sodium and magnesium.
*The solids loading can be as high as 300 pounds per 1000 barrels of crude.
*While traditional desalter chemical treatment programs focused on salt and water removal, the focus is now shifting to also encompass solids, particularly Iron removal efficiency.
*High desalter temperatures (up to 300°F) are needed with heavy feeds or waxy feeds to ensure low viscosities for full dehydration as well as the melting of all the asphaltenes and high molecular weight waxes that can encapsulate salt crystals.
*Acidification of the desalter water has been found to remove additional amounts of iron oxide and iron sulfide particles found in many crude oils, but acidification has not been as effective in removing the iron carbonates found in some light tight oils.