Question 59: We are reformulating our FCCU catalyst. What are your Best Practices to post-audit the catalyst change?
FEDERSPIEL (W.R. Grace & Co.)
Evaluating an FCC catalyst reformulation is not something you are able to do overnight. It is a long commitment to post-audit the catalyst reformulation. Because of that, preplanning really is critical. Right? You want to make sure that you plan out for the trial in a manner that will let you do your post-audit effectively. You will want to define the objections and constraints very clearly in the beginning of the trial and establish sample and data collection, both the timing on that and the methods. Then, you should develop an evaluation plan. What does success look like for this reformulation? Because of the time commitment it takes to do a catalyst trial, the average age of catalysts inside an FCC unit could be anywhere from 20 days. This timeframe might be a fast reformulation effort to some units that go to an average age of 100+ days, which is a lot longer timespan. During that time, how many people in the audience draw straight lines on the DCS (distributed control system) for six months in a row? I am not going to pull up the polling app, but I guess the response is zero.

Using chronological plots by themselves is not an effective way to evaluate catalyst reformulation, so we have to introduce some other methods. Using cross-plots is one where you plot process variables. Instead of just against time, you plot them against another process variables. Further, you can use ACE (Advanced Cracking Evaluation) testing or pilot plant testing. Modeling can be used as well.
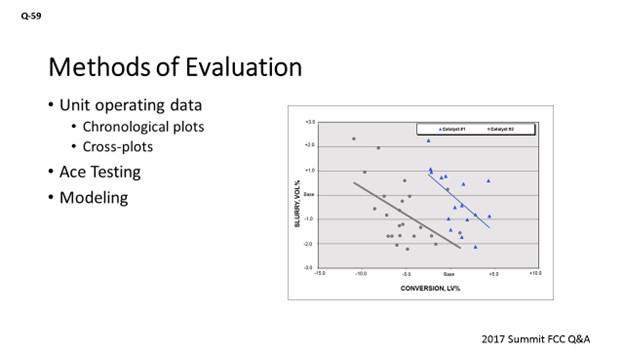
There are complications you will have to consider when you are planning for reformulation and the post-audit of it. Feedstock availability: Ideally, you would be able to run at least some period – both on your initial catalyst and your reformulated catalyst – using the same feed. That will eliminate a major variable in the evaluation. If you have shifts in economics that force you to change your operating mode, clearly you will have to consider that scenario, too. If you move from gasoline mode to trying to produce propylene to take advantage of that market, the post-audit will clearly be more difficult to extra out of the trial. On longer trials, you can run into summer or winter effects on blowers and compressors that will change your constraints; so, plan and account for such seasonal effects. There are logistical concerns with handling the catalyst, especially if you are reformulating from Vendor A to Vendor B. You might not use the same logistics company, so consider that as well. Lastly, putting in the wrong catalyst can be really expensive and will certainly complicate the catalyst trial. If you do not plan for and risk-mitigate it properly, you will end up cutting the trial short, which will be costly for you.
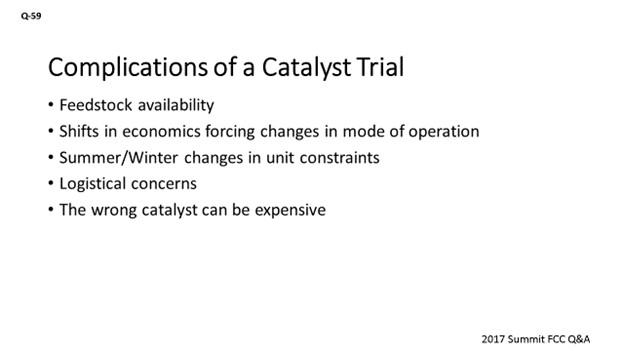
BHARGAVA (KBC Advanced Technologies, Inc.)
Catalyst change is one of my favorite topics, so it is appropriate that I answer this question. We have conducted catalyst evaluations for several clients; and not only have we been successful executing these base catalyst changes, but we have also found improvements for selecting the right catalysts for additives. We evaluated ZSM-5 additives from different vendors and have been successful differentiating ZSM-5 that comes with the base catalyst vendor with ZSM-5 coming from another catalyst vendor that just sells ZSM-5. We understand that small changes in the FCC yields are difficult to find, and these small changes – in themselves – equal millions of dollars of improvements you can do on a catalyst. One of the ways we bring value to the table is by putting in a very rigorous system of evaluating catalyst. As was just said, we also must do the preplanning, which I will talk about in my last bullet point. What we do is use simulation models. We installed a test run program to do a test run every two weeks during the catalyst transition, and we developed calibration factors.
What are calibration factors? These calibration factors are an indication of the mechanical efficiency of the unit. Given the mechanicals are the same, it helps you track the catalyst changes. So, the calibration factors are a proxy for what the catalyst is doing in the unit. Once you have the calibration factors, you can then make an apples-to-apples comparison. The feed changes in six months. While the catalyst is changing your operating conditions, constraints change. So, we make that comparison at constant constraints, and then we evaluate the results. We do sensitivities on different situations to determine which catalyst will work under which situations.
We benchmark. We find the cracking property on the catalyst to tell us what sort of changeout we have from the catalyst analysis. We do the analysis at 25% changeout, 50% changeout, and 75% changeout to validate the results when we do the analysis. Do not rely on the vendor estimates because they can be very different from what you actually see on the unit. You definitely want to employ an independent third-party company that either benchmarks or uses the pilot plant to give you yield estimates on your feedstock. It has to be done on your feedstock by an independent party to give you yield estimates at different cat oils at different ROTs (reactor operating temperature). Look for metal tolerance tests.
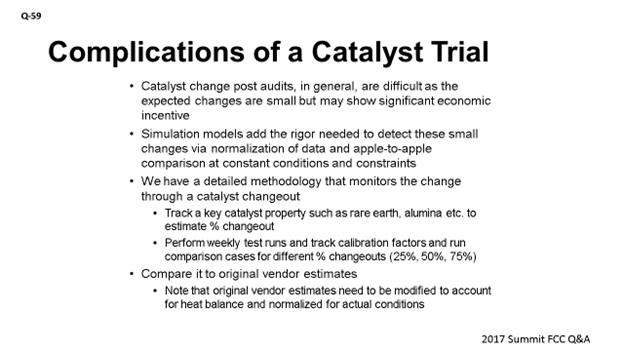
KBC has seven tests required to be done for each catalyst, if you are going to do the full catalyst evaluation. Once you get those results, you cannot use those results for any comparison on how good the catalyst will be, even at constant conversion, which is typically what the vendors or independent lab will give you. You need to change that data into a heat-balance model. These estimates have to be normalized so they will represent your unit. So, you need a base run calibration of your unit and then superimpose the catalyst effects on the base case calibration under heat-balance situations to get the right estimates you are seeking. Then, do a post-audit and compare it with the catalyst results.
DINKEL [Marathon Petroleum Corporation (MPC)]
I will echo that we like to look at multiple methods for confirmation; but within Marathon, we have our own circulating riser unit. That is where we heavily rely on looking at both the catalyst assessments for changeout, as well as the post-audit data. As Mike was saying, we are able to isolate variability from the commercial unit which allows us to focus on catalyst performance. We can look at the original feedstock at the end of the catalyst changeover, as well as the feedstock at the end of the run, which may be as much as six months down the road.
During the Annual Meeting in March, we co-presented a paper with Albemarle that detailed a catalyst changeout and got into more discussion on our uses of pilot plant. You can refer to the paper for more details, which was entitled “An Action Plan to Improve FCC Unit Performance at the Marathon Galveston Bay Refinery”.6
PHILLIP NICCUM (KP Engineering, LP)
I wholeheartedly agree with the suggestion to use a model to adjust the data. What I found and observed to be the most successful is that you can also do this leading up to the catalyst change. Take some routine tests, perhaps once a week. Get some good data, and then adjust it to some basis of a feed quality in operating conditions. Then, continue this process as you go into the trial. You will then have a way to isolate the feedstock quality changes and the operating condition changes that are inevitable and required in the operation. Using that data, you can then reflect on the effect of the catalyst. I am not a fan of using pilot plants to test it, because you cannot be certain of the testing protocol itself. The catalyst may be better in the pilot plant then it will be in your commercial unit. So, I believe in the benchmarking of the actual data and the collection of reliable data on routine basis, as well as watching the trial from the beginning. If it starts to go south, correct it before it gets bad.
BOB LUDOLPH [Shell Global Solutions (US) Inc.]
As part of the preplanning Mike outlined, do not forget the operability of the catalyst. For example, you may not get the opportunity to see the yield shifts if the catalyst circulation is challenged. So, go through the various unit operating parameters, identify where the unit operation could become constraining, and prevent your full realization of what the new catalyst has to offer. Try to put in some milestones early, while you are changing out, to check if you will be able to appreciate the projected yield structures. Just make that a part of your preplan.
MICHAEL FEDERSPIEL (W.R. Grace & Co.)
Preplanning is an important part of ensuring that the catalyst reformulation and post-audit are successful. Before the catalyst trial begins, it is important to define catalyst objectives and establish a clear evaluation plan on how these objectives will be monitored and evaluated for the trial. Sample and data collection guidelines and establishing a good base case should be done before the trial. It is critical that the samples and processed data needed to monitor the reformulation are routinely collected before and during the trial. It is also suggested to work closely with Operations, the refinery lab, and your catalyst supplier to guarantee that samples are being collected and the proper analyses are being performed.
After the process data and samples are collected and analyzed, there are several different methods – such as cross-plots, lab testing, and modeling – that can be applied to evaluate the benefits of a reformulation. The first method is the use of cross-plots. Cross-plots are an extremely useful tool to look at operating data and e-cat data on a similar basis. One example of a cross-plot is shown in Figure 1 where a refinery reformulated the catalyst to improve bottoms upgrading. At similar conversion, the refinery was able to achieve lower bottoms.
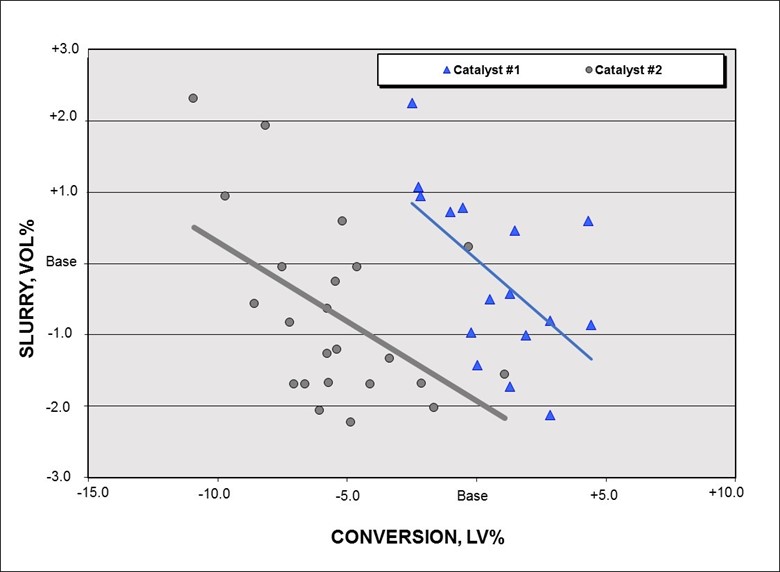
Figure 1. Slurry LV% (liquid volume percent) versus Conversion LV%
Other cross-plots, such as gas factor versus equivalent nickel or gasoline octane versus reactor temperature, could be useful to help determine the benefits of a catalyst reformulation. The catalyst objectives will determine which cross-plots are the most meaningful for the trial. When drawing conclusions on cross-plots, different operating conditions, feed quality, and catalyst health should be taken into consideration. This is why laboratory testing and models should be used in conjunction with cross-plots.
Laboratory testing can be used to help evaluate the catalyst reformulation. ACE testing and Grace’s DCR® (Davison Circulation Riser) testing can be conducted on the equilibrium catalyst to help determine the benefits of the reformulated catalyst. The advantage of lab testing is that it is conducted using fixed operating conditions and a fixed feedstock, thereby removing the uncertainty in results solely derived from unit operating data due to variability in these parameters over the course of the evaluation. Lab testing should be done with the refinery feed, base equilibrium catalyst, and reformulated equilibrium catalyst. The equilibrium catalyst should be chosen with similar metals levels which may not be possible during the trial if the unit experiences a shift in metals levels.
Another method to evaluate catalyst reformulation is the use of models. Models are tooled used to quantify catalyst reformulation benefits since they can be developed to predict yields shifts at defined conditions. When developing, calibrating, and using models, it is important to make sure that data input contains no errors. Before using a model to determine catalyst reformulation benefits, model-predicted yields should be compared to actual yields to validate the accuracy of the model. If the model cannot be validated, it should not be used in the evaluation.
Two model methods can be used to determine catalyst reformulation benefits. The first method is to calibrate and validate the model for the base catalyst. After the new catalyst is fully turned over, this model can predict what the yields would have been on the base catalyst at similar operating conditions. The predicted yields are then compared to actual yields to determine the benefit of the reformulation. The second method is a double-check of the first method. The model needs to be calibrated and validated for the reformulated catalyst. This model can then determine what the yields would have been on the new catalyst at base catalyst conditions. These predicted yields can be compared to the actual yields before the trial to determine the benefit. The results from both methods should be compared to make sure that the methods show similar benefits.
In conclusion, evaluating a catalyst reformulation can be very complicated since it is extremely rare for a unit to run in a stable manner with similar operating conditions, similar feed quality, and similar catalyst health. This variability in operation is why several methods need to be used to quantify the benefits of the catalyst reformulation.
SANJAY BHARGAVA (KBC Advanced Technologies)
Post-audits are very important to verify if the catalyst performed to its original estimates from the catalyst vendor and if it shows the same yield and property shifts as originally proposed. We prefer a very detailed post-audit consisting of high-quality, stable, and data-validated test runs (four to eight) performed on a weekly basis on the base catalyst followed by weekly test runs during the transition. A key catalyst parameter (such as rare-earth or alumina) is used to track the transition of the existing catalyst to the new catalyst. The unit performance (yields, properties, coke/gas selectivity, etc.) is also tracked and normalized using a simulation model and projecting several different simulations runs under constant conditions and constraints. This procedure is done with calibrated models at the base catalyst at 25% changeout, 50% changeout, and 75 to 80% changeout. Economics are applied to all the cases to determine the value of the catalyst change and then compared with the original delta estimates from the vendor. Next, the values are converted into heat-balanced yields, properties under constant conditions and current constraints to determine the success of the catalyst change.
This exercise is difficult since small changes are frequently expected which have a major economic benefit. So, there is a big incentive to have sophisticated tools and methodologies to perform stable test runs and do additional data validations.
BRYAN DINKEL [Marathon Petroleum Corporation (MPC)]
Best Practice for post-auditing catalyst changes on a unit includes using multiple types of reviews to provide assurance that all of the data is pointing in the same direction. We will use commercial data reviews, catalyst supplier assessments, and pilot plant testing – coupled with the utilization of a kinetic model – to translate pilot plant results to better reflect commercial unit results. In my experience, review of commercial data alone is often muddled with feed quality shifts; so typically, there are challenges getting clean baseline and post-changeout data sets for review. Catalyst supplier reviews will usually isolate catalyst performance based on their standard feeds and ACE (Advanced Catalyst Evaluation) run data, which is insightful but not as reflective as circulating riser unit (CRU) results. Within MPC, we utilize our internal circulating riser unit upfront in the catalyst selection phase and in the post-auditing period. The CRU allows us to isolate catalyst performance shifts and then plug that information into our kinetic model to optimize the unit against operating constraints. You can refer to the March 2017 AFPM Annual Meeting paper, co-written and presented by Albemarle and MPC, entitled “An Action Plan to Improve FCC Unit Performance at the Marathon Galveston Bay Refinery”7 for discussion in more detail.
REBECCA KUO (BASF Corporation)
In a perfect world, during a catalyst change there would be no feed or operational changes. However, this rarely occurs; therefore, the best way to post-audit a catalyst change is to track the equilibrium catalyst (e-cat) yields by ACE (Advanced Cracking Evaluation) testing, as the testing is done with a standard feed at constant operating conditions, so any deltas are attributed to the catalyst only. It is important to note, when comparing ACE yields reported by different catalyst suppliers, that the absolute yields will not be comparable as all suppliers use different feeds and operating conditions. The trends from baseline are the most crucial to track. Another option is to conduct lab testing (such as ACE or circulating riser unit) using the FCCU feed with both e-cats to post-audit the catalyst changes at apples-to-apples conditions. If using this option, make sure that important e-cat properties – such as Ni (nickel) and V (vanadium) – are similar between the two catalysts. If post-auditing the catalyst change with the operating data and reactor yields, a Best Practice is to use a kinetic model – such as FCC-SIM or a statistical model – to normalize the data for changes in operating variables and feed properties. Build a comprehensive and statistically-sound base case with the incumbent catalyst and project forward to the new catalyst. Any deviation from the model will be due to the catalyst change. Finally, when conducting a post-audit of a catalyst change, it is crucial to understand the turnover of the catalyst inventory. A rule of thumb is to start tracking the catalyst effects around 50% turnover; as at this time, about 75% of the activity will come from the new catalyst. At 75% turnover, about 90% of the activity will come from the new catalyst.