Question 58: Does your site/company require the use of a chemical wash to mitigate possible pyrophoric scale hazards in columns with structured packed beds?
LEE (BP North America)
We currently have an Advisory Policy requiring an oxidative chemical wash to help preclude any event from pyrophoric scale accumulation when the towers utilize structured packed beds. This policy is currently being progressed to a Mandatory Process Safety Policy. We have had several pyrophoric fires over the recent years. In some instances, an inadequate or nonexistent chemical wash prior to opening the column manways was the contributor. All of these fires occurred with structured packed beds, not random packed beds. We are less concerned with random packed beds due to their lower propensity to trap pyrophoric scale. It is noted and recognized that an oxidative wash will not assure or guarantee a nonevent. Several of the fires did undergo a vapor phase oxidative chemical cleaning, but it was apparently ineffective at getting to or neutralizing all of the pyrophoric scale. In another instance, no oxidative chemical wash was conducted.
Our current philosophy is that an oxidative chemical wash, in both the liquid and vapor phases, must be conducted as a minimum mitigating procedure. Commercially available vendor products, which are at least equivalent to generic potassium permanganate oxidizers, are typical used. As noted, we strongly advise that a liquid phase oxidative wash be conducted in addition to the vapor phase washing, which we have found to be inadequate in large diameter towers.
The oxidative wash should be differentiated from a detergent chemical wash for removing oil and oily coke deposits. Any chemical wash should also be differentiated from a waterwash or steaming, which is prudent for tower entry and cleanliness; but again, this does not address the pyrophoric iron scale hazard. Maintaining the bed in a wet and cool condition (less than 105°F) is a good practice that we also undertake along with providing a temporary water supply pipe with a deluge spray nozzle at or in tower manways for emergency wetting of the bed, if required. It should also be noted that precautions must be taken around the tower peripheral equipment where pyrophoric scale can be washed or pushed; for instance, the reboiler where the scale can be trapped and smolder upon air ingress.

This graph shows the relative temperature profile, on the top plotline, of a structured packed bed that experienced a pyrophoric fire during a cooldown phase. The other plotlines were located in other packed beds which did not have an event.

Next are some photos of what it looks like after an event. The first two photos show a damaged structured packed bed.

This photo shows a reboiler where some of this pyrophoric scale got pushed through the reboiler bundle with air ingress.
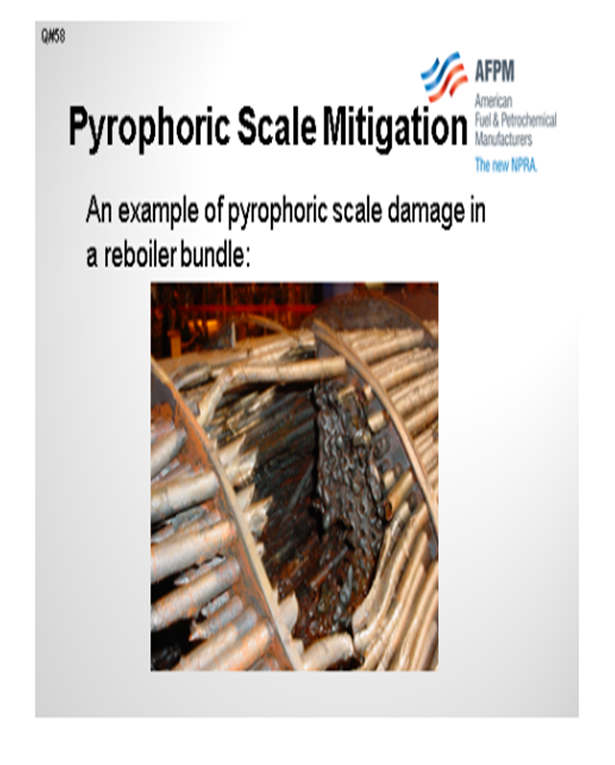
CLIFFORD (Motiva Enterprises LLC)
Similar to Howard, my company does not mandate chemical washes at this time. We will typically use a potassium permanganate-type solution and generally try to keep the beds wet. We will monitor temperatures and have a water spray available if any adverse conditions are noted.
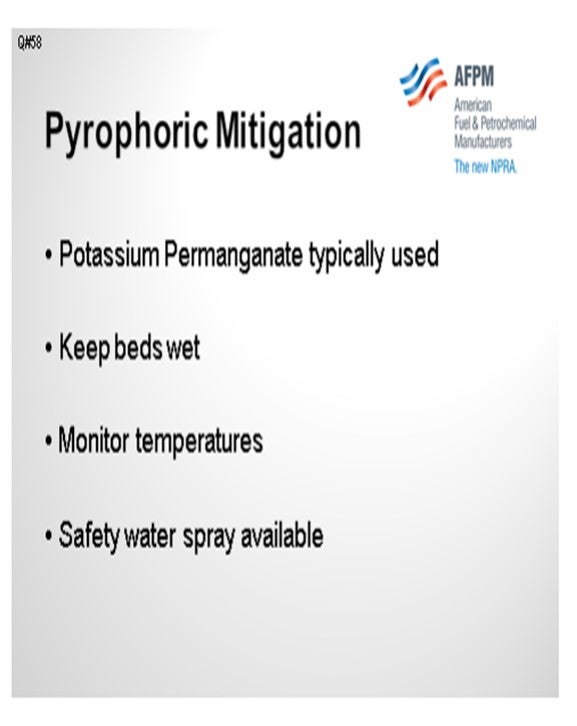
BASHAM (Marathon Petroleum Corporation)
I have a quick point on the safety considerations of potassium permanganate. It is a very strong oxidizing agent, so you really need to ensure that you are not mixing it with chemicals that are incompatible with it. Generic refinery cleaners are typically used. These cleaners are incompatible with strong oxidizing agents to the point where if they are mixed, there will be a very strong exothermic reaction which can generate temperatures high enough to cause thermal burns. So, if you are using the potassium permanganate or any strong oxidizer, make sure you understand the chemical compatibilities.
STEPHEN PERRY (Motiva Enterprises)
It is important to realize that although this might be a big issue for us as we move around in the industry, there are a lot of young people coming into the industry for whom self-heating due to pyrophoric iron is not common knowledge. Self-heating is written in the procedures. Yet, I go out in the plant and see that the water spray cooling systems are not in place to handle an event if the equipment starts to heat up. Even though these safety systems are part of the procedure, they are not in place. So, I think it is incumbent upon us to make sure we are having discussions with the younger process engineers about what happens to make sure we are covering the bases.
RODRIGO CARDOSO (CITGO Lake Charles)
Instead of using permanganate, do you have any experience using some type of peroxide that is not as strong as permanganate? My second question is: How you do it to monitor temperature, especially when it comes to the towers with only a few TIs (temperature indicators), for example?
CLIFFORD (Motiva Enterprises LLC)
I have no experience with peroxides. Generally speaking, in terms of monitoring temperatures, the console operators can monitor DCS (distributed control system) temperature indicators. You can also have local handheld temperature readers when you are entering the column to make sure that there are no hot spots.
RODRIGO CARDOSO (CITGO Lake Charles)
You do not have anything attached to the tower wall, such as a temporary temperature reading device, right?
CLIFFORD (Motiva Enterprises LLC)
I am not aware of anything being attached to the tower wall.
LEE (BP North America)
We have not used peroxides, per se. There are plenty of permanganate solutions and alternative vendor products that are equal. If the solution oxidizes the scale, then that surely would be the consideration. So yes, as Steve said, you can use the available thermocouples, assuming they go down to near ambient on the scale. Some folks also might have a SOx (sulfur oxide) monitor as another mitigating device to help sense anything occurring in the tower environment.
CLIFFORD (Motiva Enterprises LLC)
My site company does not mandate it; however, it is a recommendation where iron sulfide may be present. We regularly passivate iron sulfide scale with a potassium permanganate solution, but we may elect to keep the bed wet with a water spray. We will monitor temperatures and recommend a safety water spray to be on standby if any heating is observed.
BASHAM (Marathon Petroleum Corporation)
At Marathon Petroleum Company, it is not required company wide. However, individual refineries have permanganate wash integrated into their standard procedures of preparing the crude vacuum tower for shutdown. While a permanganate wash will help, it will not provide 100% assurance that the risk has been mitigated. The presence of plugged distributors over the packed beds will make it impossible to ensure that all of the packing has been neutralized. For this reason, it is prudent to have a fire hose available to spray down the packing if smoldering is observed.