Question 57: How are you optimizing the use of wet gas scrubbers caustic use and SOx additives?
TIFFANY CLARK (BASF)
You can utilize a SOx additive in addition to a Wet Gas Scrubber system in order to reduce caustic consumption and minimize cost. Utilizing a SOx additive can be optimized by calculating the caustic savings + value of additional liquid sulfur produced - the cost of the Sox additive. As you can see in this graph, the value of SOx additive can be calculated for varying caustic costs and SOx reduction percentages and should generate a curve like is shown here with the optimum at the top of the curve. In addition, it is worth noting that pickup rate is dependent on SOx concentration. Higher SOx concentration means higher pick-up rate.
DEWEY STUART (Motiva Enterprises)
This is managed with cost benefit analysis depending on market cost of the two and downstream processing cost and limitations. As you switch from caustic to SOx additives the amount of H2S treatment in the FCCU overhead increases. This can lead to additional loads on the Scrubbers and potential pH shifts on the water treatment systems. If the capacity if not available in the downstream treatment, then the remaining H2S in the system can exceed limitations for the receiving units possibly including downstream fired heaters. If the water treatment sections do not have pH control and typically run basic (generally and issue on units running more hydrotreated feeds) the corrosion mechanisms can shift. Some mechanisms to consider are acid corrosion, wet H2S, Ammonium Bisulfide, Ammonium Chloride, Carbonate Cracking, and CO2 Corrosion. Depending on the individual systems the approach for control will very.
JARRED DREWRY (Johnson Matthey)
In response to escalating caustic prices, at least 10 refineries in the US alone have begun using SOx reduction additives in their FCCs to reduce caustic use. A moderate amount of SOx additive (50-300 lb/d) can substantially reduce the required caustic 30-60%, particularly in full burn units. Overall savings range from $100,000 to more than $1 million annually. There may also be other refinery advantages such as reduced waste water treatment.
STEVE GREMILLION (W.R. Grace & Co.)
SOx emission control continues to be an important topic for many refiners, particularly in regions and countries where more stringent environmental emission targets will come into effect. Two of the most common approaches utilized by refiners for complying with SOx emission targets are the use of wet gas scrubbers (WGS) and the application of FCC SOx reduction additives. While WGS’s are typically very effective for SOx control, they can result in high OPEX costs, particularly those associated with caustic soda price. A recent analysis of the US market shows that more than 50% of refiners operating WGS’s are also using SOx reduction additives to optimize WGS caustic usage.
Over the past two years, global caustic pricing has increased considerably. Figure 1 highlights caustic pricing in various regions of the US and EMEA. While the pricing varies by region, a consistent increase in caustic price has been observed over the last two years in all regions. This increase in caustic pricing has a significant impact on OPEX costs for refineries operating a WGS and provides economic incentive for the optimization of WGS caustic usage via the application of SOx reduction additives.
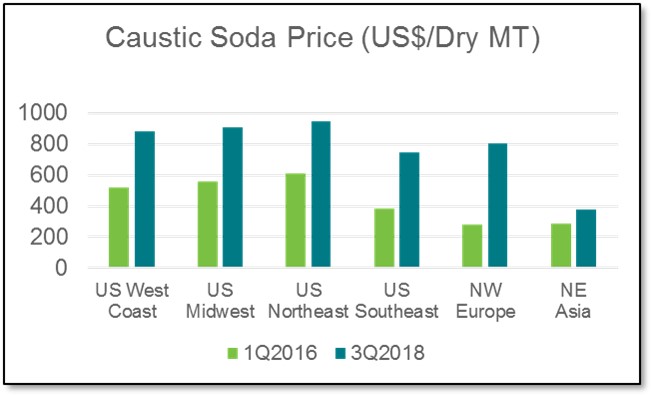
Figure 1 – Caustic Soda Market Pricing
Because SOx reduction additives are a well-established method of reducing FCC SOx emissions, it is possible to make an accurate estimation of the potential cost savings associated with using an optimum combination of WGS caustic and SOx reduction additive to meet SOx emission limits.
Key factors affecting the available cost savings are the uncontrolled SOx emissions (i.e. the SOx level that would be obtained without the use of any SOx reduction technology), targeted SOx emission level, caustic soda pricing, SOx reduction additive performance, and SOx additive price.
Figure 2 shows an example of the daily OPEX cost of using SOx reduction additive compared to WGS caustic to control SOx emissions.
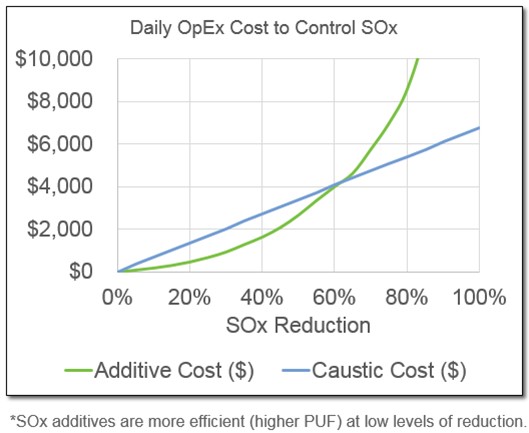
Figure 2 – OPEX Comparison Example
SOx reduction additive performance is typically represented by the PUF (lbs SOx removed/ lbs of additive). Observed PUF is unit specific and varies significantly across industry due to differences in regenerator operating conditions and regeneration kinetics, target SOx removal percentage, and specific additive type.
It is also important to note that PUF decreases as the percentage of SOx reduction increases. Due to this fact, there is a breakeven point where the additive cost and the caustic cost have the same OPEX. This is shown in Figure 2 when the additive cost (green line) and the caustic cost (blue line) intersect. Using additive to obtain a level of SOx reduction anywhere to the left of the breakeven point will reduce operating cost. Maximum OPEX reduction is achieved when using SOx reduction additive at the point where the distance between the two lines is greatest and then using WGS caustic to obtain additional SOx reduction beyond that point.
Based on these factors, it is very important for the refinery to work closely with their additive supplier to develop an accurate economic evaluation to understand where this breakeven point is for their specific operation and determine the optimum combination of caustic use in the WGS and SOx reduction additives for meeting SOx emission targets.