Question 57: Do you experience any corrosion and fouling in the preflash or crude towers as a result of running at dew point temperatures or below in the top of the towers? If so, what steps do you take to mitigate and control this problem?
Doug Meyne (Champion)
Preflash Tower
Preflash towers and overheads are not particularly susceptible to corrosion and fouling because chloride hydrolysis is minimal at Preflash feed temperatures. Without chlorides, aqueous corrosion in crude oil distillation is minimal. By extension, Preflash corrosion control and fouling issues are considered outliers. Some refiners use a water wash in the Preflash overhead and some use corrosion inhibitors. Many uses nothing. Neutralizers are rarely used. Admiralty bundles are common in Preflash towers because water-side corrosion is normally the greater risk. The Preflash tower itself shouldn’t corrode, unless it is due to just plain long service and old age. There are always exceptions to the rule. Mitigation and control needs should be reviewed for each case with a corrosion engineer and/or the corrosion inhibitor supplier for the refinery.
Crude Tower
First and foremost, don’t try to fight corrosion and fouling in a crude tower operating at low temperature with neutralizer (see “Neutralizers” answer on question #56).
For years the best course of action to address a low temperature Crude tower has been to reduce the chlorides into the tower and add a filmer into the reflux. This is still a good approach; however, it’s not always enough. Just as Preflash tower corrosion is low without chlorides, the same can be true with Crude towers. There are several ways to reduce chlorides into the tower, but that’s a large topic that needs to be answered in a different question or forum. However, corrosion control of a tower to deal with chlorides that do get into the tower is germane to this question.
In order to deal with this question in a way that is truly helpful, it is necessary to use a product application example. Champion has been using a filmer with a proprietary salt dispersant in it for years. Not too long ago we found ourselves tasked with bringing corrosion under control in a tower that had experienced serious tower corrosion and tray replacements for over 30 years. The Crude tower operated with a top temperature around 200F, and the reflux was sub-cooled resulting in localized dew points in the tower. The graph below shows the relative success of an increase in the filmer rate into the tower reflux. Increasing this rate resulted in historically low corrosion rates on the top tray corrosion probe. What this graph doesn’t show is that for over a year following the increase of filmer into the tower, the top tray corrosion probe stayed below 5 mpy. Furthermore, the inorganic fouling that was routinely experienced in the filters on the first side draw was essentially eliminated. In other words, with the right approach, tower corrosion can be controllable using enhanced filmer technology.
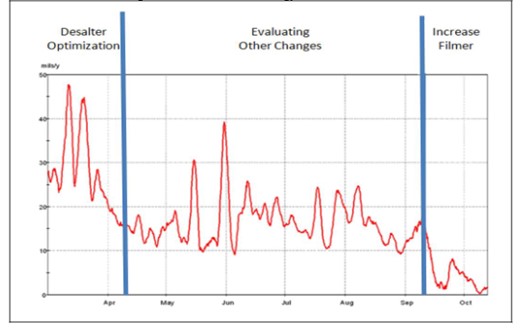
Ralph Goodrich (KBC Advanced Technologies, Inc.)
Problems we have seen have occurred primarily in crude column top sections where the water mole fractions are normally much higher than in preflash tower overheads. This has even become more prevalent with the current desire to maximize distillate yields which puts pressure on minimizing the naphtha/kerosene cut point, impacting both existing units as well as the design of new facilities. Most refiners try to maintain at least a 15 to 20°F margin above dew point; however, a number of refiners we have worked with are operating at lower approaches. In a situation where operating near or at dew point conditions is unavoidable, there are a series of possible steps that can be made to try to help alleviate any corrosion and fouling issues.
The first step should be to ensure stripping steam rates are optimized and trimmed back where possible. Secondly, ensure the desalters are operating as effectively as possible to minimize the quantity of corrosion causing material ending up in the downstream crude unit. Also, check with your specialty chemicals vendor to see if there are other potential steps involving any other chemicals and/or additives which may in their experience be helpful in your situation. Evaluate any proposed changes to see if they may be applicable.
Another step would be to determine if you can safely water wash the top section of the crude tower using the existing hardware. If so, periodic water washing should help alleviate the problem. However, crude towers are not normally designed with the proper facilities for a water wash so there is a good chance this may not be a solution.
Longer term, if operating at the dew point is going to continue, or if there is pressure to reduce the naphtha cut point even further, changes to the unit hardware should be considered. This could include upgrading the metallurgy in the tower, adding water draw(s), and providing facilities to allow periodic water washing of the tower top section.
Paul Fearnside (Nalco Company)
Anytime you have a “wet tower “you will have increased corrosion. Steps taken to control this are:
1)Change process conditions to dry out the tower via increased reflux or pump around return temperatures.
2)Minimize the amount of stripping steam used to dry out the tower.
3)Improve desalter performance by: a.Increasing the amount of desalter wash water for better salt removal. b.Increasing the dehydration efficiency across the desalters.
4)Change the tower top or tray metallurgy
5)Start, or better utilize, caustic injection to reduce the acid loading to the section of tower affected.
6)Increase the amount of filming amine corrosion inhibitors used for increased protection.