Question 56: Light slop oils are frequently collected and routed back to the crude unit with fresh crude. In a capacity limited crude unit, this results in backing down crude rate. What are your considerations for injecting slop/recovered oils into process units that avoid backing out crude feed?
PRICE (Fluor Corporation)
This question is a compilation of several that were originally submitted. One of those questions focused on being able to put slop into a pumparound, so we are going to address that as well. But of course, the most important factor about running slops is knowing what it is: understanding whether it is wet or not, whether the quality is known, and whether the quality is consistent.
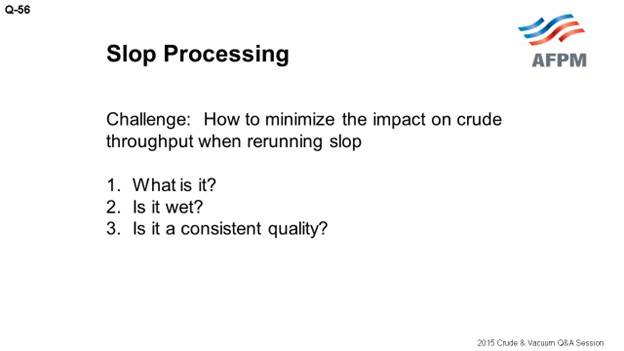
Ideally, you should segregate your slop. It is not always practical; but if you have some sort of segregation in your slop system, you will be better able to process it optimally. What works in some cases is definitely not acceptable in other cases. If you just have one bulk slop tank where everything goes, you are definitely limited. It would be great if you could enforce the rule that says, “If you make it, you need to reprocess it.” But once again, that is difficult to enforce and also very expensive, from a capital standpoint.
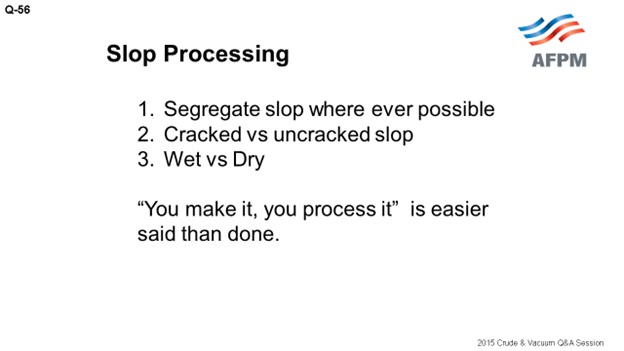
When the slop is wet and uncracked and the quality is variable, it will optimally be processed with your crude (at the unit charge pump) where it can be heated and desalted. There are not a lot of other locations that do not carry operational risk. If you have an uncracked slop stream that is consistent and a known quality, it can be injected into a pumparound return as long as it is dry. You need to choose which pumparound return to use based on the endpoint of the slop and the pumparound return temperature. If you choose to reprocess slop in a pumparound return line, it is important to make sure the pumparound temperature is low enough so that when you inject the slop, it will not flash in the distributor.
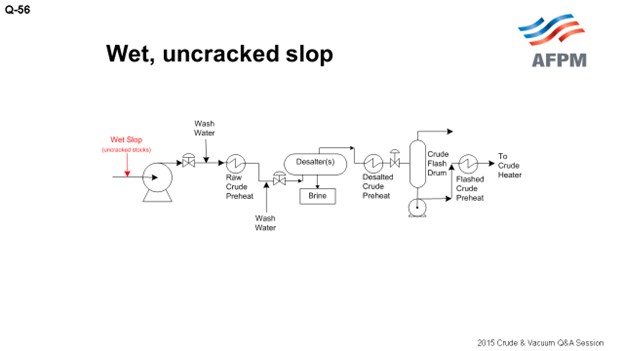
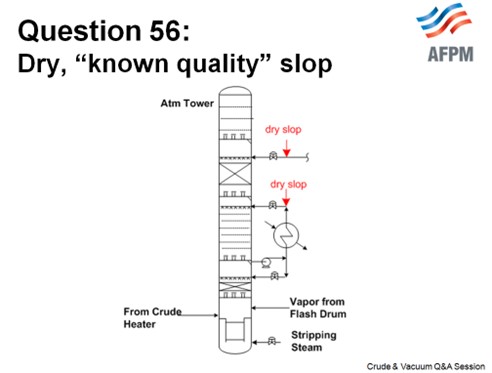
This slide shows a generic atmospheric tower. You can put your slop into any of the pumparounds, depending on the quality, but you want to make sure that it is low enough in the tower that there is some fractionation and to ensure that you will not end up with off-test jet.
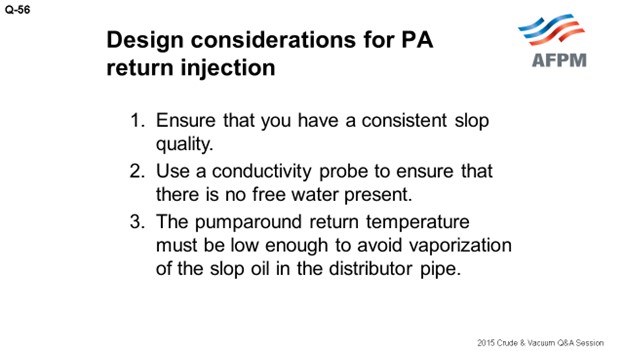
This slide shows reference information within Henry Kister’s book. There is some discussion on the topic about the use of conductivity probes to detect free water, which more refiners are starting to use more when injecting their slop into a pumparound.
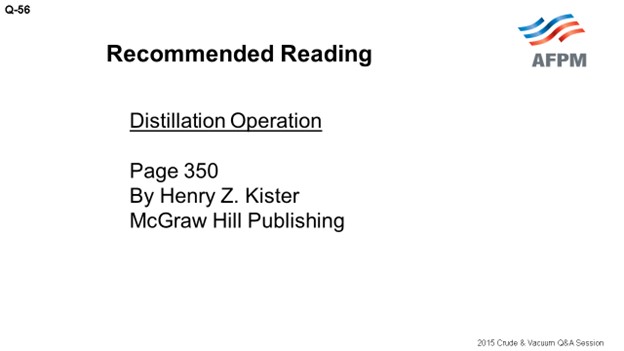
Cracked slops are optimally processed in the cokers since they contain olefins. Many people do process them with their crude charge, but it is not recommended.
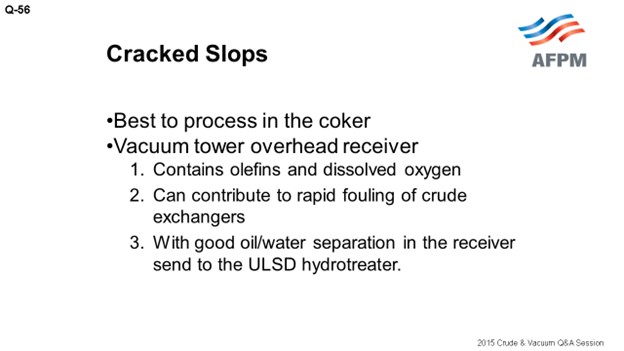
There is one special slop stream which is very unique: the hydrocarbon stream that comes from your vacuum tower overhead receiver. This stream exists in varying quantities, but it can be several thousand barrels per day, depending on how you run your vacuum tower. This stream may be a lighter version of the top liquid product from the vacuum tower (often called ‘vacuum diesel’ by many refiners). This stream is unique because it contains dissolved oxygen, as well as being very olefinic. We know of several cases where it is routed and processed with the raw crude charge to the crude unit, but it contributes to very rapid heat exchanger fouling. One refiner is now successfully sending this directly to his ULSD (ultra-low sulfur diesel) hydrotreater. To effectively run this stream in a ULSD hydrotreater, it is essential to have good oil-water separation in the vacuum tower overhead receiver.
WATTS (LyondellBasell Industries)
I am mainly going to talk about our practical experience. Obviously, we try to minimize the material we run back to our crude units. Typically, on a daily basis, the only materials we run back to the crude units are what we call hot mix and drips, which are basically kerosene and a lighter material that is collected from the downstream units. We run our slop stream to the cokers. When we are looking at processing other intermediate streams, we do a lot of the things that Maureen mentioned. We look at the origin, the distillation, and many other properties. When in doubt, we do process it through the crude unit.
To my knowledge, the only place where we inject an intermediate stream on a crude unit in a pumparound is where we inject the atmospheric gas oil that we pull off of our crude tower into the lower pumparounds on our vacuum tower, essentially bypassing the vacuum heater. But that is not a stream we are storing in a tank and pulling back, so we know the properties of that stream fairly well.
MAYO (CITGO Petroleum Corporation)
Just an additional suggestion: Like Maureen said, if you have that option, look at high vanadium and low vanadium slops. All of the high vanadium slops definitely go back to the crude tower. We consider most low vanadium slops as an option to be processed to the FCCs (fluid catalytic cracking) as well.
LUIS GORDO (Amec Foster Wheeler)
Depending on the distillation range, vapor pressure, light ends, and contaminants of the slops material, light slops can be injected directly into the fractionator itself. However, it is necessary to ensure that these slops are free of water and solids and that they are also heated to the injection tray temperature. If by doing this and assuming that particular section of the distillation tower is not limited, then light slops can be processed without backing out the crude capacity.
EBERHARD LUCKE (CH2M)
Injection of slop oils into any process unit is a very complex issue and requires careful consideration of all aspects that can impact the operation of that process unit. Here a few points for consideration:
-
The most common process units considered for slop processing are the crude unit and the delayed coker.
-
Slop injection into the crude unit will always back out crude oil feed to the unit. In most cases, the same statement is true for the delayed coker, but there are some special cases where the unit capacity is not impacted.
-
One of the most common problems of slop injection is the capability (or lack thereof) to dewater the slop before reprocessing. Water slugs can cause major disturbances in the operation of the unit receiving the slop.
-
Similar problems can occur if the slop contains other contaminants that can be carried over into the receiving process unit.
-
In many cases, slop reprocessing is an intermittent operation and may be treated as non-standard operational mode.
-
Slop injection should occur in a spot of the receiving unit where it will blend with material of similar distillation range. If the quality of the slop (distillation range and/or density) varies significantly, multiple injection options should be considered.
-
Slop disposition in a delayed coker can be achieved in different ways. Not all options are suitable for all types and qualities of slop oil and need to be investigated in detail before implementation. Examples:
-
Injection into the main fractionator via fresh feed or directly onto pumparound return trays,
-
Use as a velocity medium in the coker heater,
-
Use as quench oil in the coke drum overhead lines,
-
Use a quench medium for the coke drums; i.e., separate quench step between steam stripping and water quench, and/or
-
Injection into the coker blowdown system.
CHRIS STEVES (Norton Engineering)
With proper detailed analysis, the slop/recovered oils could potentially be routed directly to downstream units such as the naphtha hydrotreater or distillate hydrotreater. However, most refiners do not choose to perform this analysis and find it easier to just re-run the material through the crude unit. In order to maximize processing of crude feed, it is probably better to investigate and minimize the sources of light slop that must be reprocessed. Sometimes sloppy operation can be improved, or leaking valves repaired, which will have a big impact on the volume of collected slop.
MAUREEN PRICE (FLUOR)
Reprocessing of slop oils (not recovered oil from the water treatment plant) is a concern faced by all refiners. Ideally, each unit would be responsible for reprocessing the slop that it produces, but this approach would result in a large tank farm that would not be a good investment.
The two biggest questions faced by refiners when reprocessing slop is the presence of water and the distillation tail (or end point) of the materials. The uncertainty in these two variables leads many refiners to reprocess all slop with the crude charge and the resulting economic penalty of backing out crude throughput. Not often acknowledged, uncracked slops can also contribute to accelerated heat exchanger fouling, another economic penalty to the refiner.
The design of the slop system has a large impact on how the slop is reprocessed. If slop from cracking units is segregated from the light slop oils associated with uncracked products (crude and other units), they can be reprocessed in the crude unit with a lower potential to impact the exchanger fouling. Cracked slops are usually processed in the delayed coker unit, which can also accept uncracked slop oils when the crude unit is limited.
The presence of water in light slop oil can be analyzed using conductivity measurement to make sure there is no water present before it is injected into a suitable pumparound. Ensuring that no free water is present is critical to prevent damage to tower internals. Additional information can be found in Distillation Operation by Henry Z. Kister.2
If light slop oil is not contaminated with any heavy fractions, injecting it to the bottom pumparound return of the atmospheric tower is a possibility. The resulting pumparound return temperature has to be low enough to avoid vaporization of the light slop oil inside the distributor pipe. A consistent slop quality is important to avoid upsetting the tower operation.
The slop oil injection rate should be adjusted to minimize the impact on the crude preheat temperature.
One source of slop oil is the vacuum column overhead receiver. This oil, which is likely to contain olefins and dissolved oxygen, is often recycled back to the crude charge pump, which may contribute to accelerated fouling in the downstream exchanger. As a cracked stock, an alternate destination for its disposition, if available, is a coker. If there is good separation in the receiver, some refiners have been able to send this specific recovered oil to the ULSD hydrotreater.