Question 56: 1973 FCC Process Question 13: When an older cat cracker is modified to incorporate riser cracking, has anyone encountered a limitation on the amount of conversion that could be obtained? In order to achieve maximum conversion, has anyone found it necessary to return to using a limited level of bed cracking?
FEDERSPIEL (W.R. Grace & Co.)
I would like to call on Warren Letszch who was on that panel in 1973. He can cover the historical answer and provide us with any updates, if available.
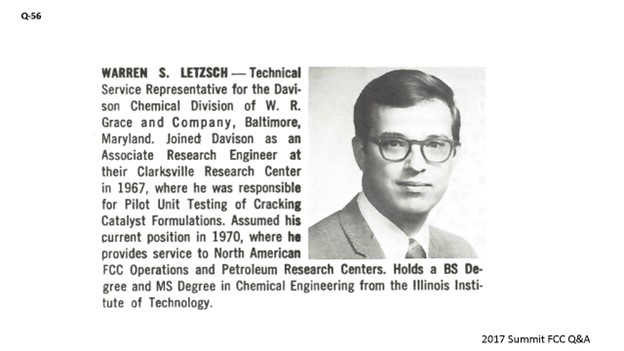
WARREN LETSZCH (TechnipFMC Process Technology)
Yes, I do remember that panel. It was at the Hyatt Regency Hotel in Houston, Texas, and there were about 700 people in the audience. In those days, we had about 1300 people coming to the meeting.
Let me put this question in context for you. The biggest advancement in catalytic cracking was the advent of the zeolite catalyst. That started in fluid units really in about 1965. By 1970, 30% of the units were still running amorphous cracking catalysts. Now just to give you a nickel’s worth of background here: All cat crackers built with amorphous catalyst were basically designed in the early days to have anywhere from a minimum of 50% recycle up to 100% recycle.
Why do you suppose we call it ‘light cycle oil’ and ‘heavy cycle oil’? Many units were designed with two risers, and the risers were equal: One was a recycle riser, and one was a fresh feed riser. The zeolites were at least – in order of magnitude – more active than the cracking catalyst we were using. In fact, if you want to think about our own operations today, think about running an activity level of about 40 on your catalyst versus the 65 or 70 or whatever you are running. Most of the units were designed with a space velocity of about two, so there was as much catalyst in the reactors as there generally was in the regenerator. When the zeolitic catalysts came out, everyone was anxious to put in the FCCU and see what was going to happen.
You currently use cracking catalyst that typically contains anywhere from 25 to 35 wt% (weight percent) zeolite. The very first cracking catalyst that came out in 1965 to around 1970 contained anywhere from about 3.5 to 7 wt% zeolite; so, by 1973, a high level was 12 wt%. So, what did people do? They put the zeolite catalyst into the unit. In some cases, the catalyst did not work; in others, it did. We discovered three things that were important in the operation. First, we had to cut down the residence time of the catalyst in the reactor. With a two-space velocity, the catalyst could be in the reactor for five minutes or more. With the riser cracker, of course you cut it down to seconds. We also found out that paraffinic feeds worked very well. Aromatic feeds were not all that great. And guess what? We learned that carbonium ion mechanism does not allow the cracking of aromatics.
The other critical thing was the carbon-on regenerated catalyst. We found that the carbon on the regenerated catalyst had to be below 0.3 wt%, and preferably down to at least 0.2 wt% to work. Quite simply, the residual coke left on the catalyst is all associated with the zeolite, not with the matrix. A couple of years ago, I presented a paper about this at the Annual Meeting. In it, I explained that with about 7% coke on the zeolite, the zeolite will not work anymore. Early FCCUs were designed for as much as 0.5% carbon on regenerated catalyst. Why? Because there was not any real benefit, as far as activity on the old amorphous high-alumina cracking catalyst. Also, you have to remember that we all had carbon steel. We had partial-burn regenerators. There were units that ran 1050°F in the regenerator. A really high temperature was 1150°F. At 1200°F, you were getting nervous. At that point, people would put water sprays up there to protect the carbon steel cyclones.
So, this was really the advent of high-temperature regeneration and where riser cracking became the norm. At that time, some refiners went to a riser cracker and could not get all the conversion they wanted. A lot of them got it just by dropping the bed level in the reactor and just letting the riser come up. In some cases, they would have to go back to the reactor bed.
But if you did not have enough activity, the easiest fix was just to add more catalyst or go to a catalyst with a higher zeolite concentration. The riser pressure drop is a way to create more catalyst contacting. That was not really the best solution; but occasionally, it would happen. Then the question came down to whether or not, in the revamp, you caused another limit on the unit that was really not related to the reactor performance. I have news for you: Some of these people could not handle all the gasoline in the gas plant. Suddenly, you are running your FCC unit and the gasoline yield goes up 8% on fresh feed. Your debutanizer may not be able to handle that much. It was a problem that refiners were happy to have. So, yes, we did find a few people that went back to bed cracking. That is basically the answer I gave and the history behind it.
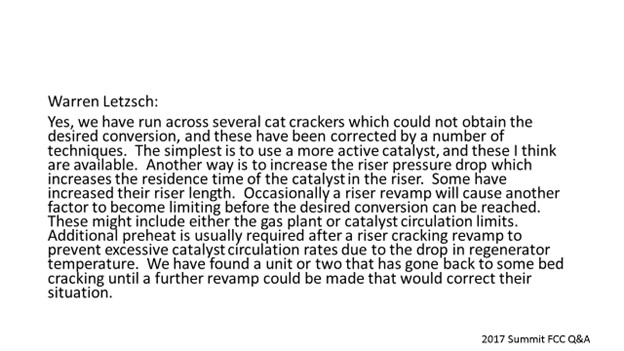
ROBERTSON (AFPM)
Thanks, Warren. I think you said more words than were up there on your slide. [Laughter]
MALLER (TechnipFMC Process Technology)
I will be brief with my response. I find it interesting to hear some of the history that was certainly before my time, especially because TechnipFMC now has a process that – although relatively new compared to 1973 – is employing the same technology and concepts mentioned in the question: bed cracking. We have a process which is using a riser that distributes catalyst and reactor effluent into a bed to continue the cracking reactions. We use that bed cracking to get additional residence time so we can get additional conversion of the naphtha that is generated in the riser and convert it to LPG. This process is intended for on-purpose petrochemical feedstock production. We are able to produce LPG yields over 40%, with half of that being propylene. This particular bed cracking method is also able to produce a relatively high percentage of ethylene.
BOB LUDOLPH [Shell Global Solutions (US) Inc.]
I would like to poll the audience. How many of the people here work for companies that continue to operate bed crackers? [No response] Wow! Shell is one. [Laughter]
MELVIN LARSON (KBC Advanced Technologies, Inc.)
KBC has seen a number of units that were built in the 1960s and 1970s that have gone up to such high conversion levels that water removal is no longer achievable in the overhead receiver. We see a lot of naphtha streams that are supersaturated with water going into primary and secondary absorbers, so we know of many places that have been expanded hydraulically and through conversion. The original equipment will just not get the water separation you really need to run a dry, safe gas plant. You will get H2S and all kinds of nasties in the absorber systems. So, you should check for water content or saturation, looking for your contaminant levels to see if you have tower problems. If you can get the water out, you will actually get a whole new gas plant.
ROBERTSON (AFPM)
Thank you. And thank you, Warren.
ALEX MALLER (TechnipFMC Process Technology)
Technip has a process in which a combination of riser cracking and bed cracking is used to maximize conversion. We have found that there are limits to the conversion that can be achieved in traditional riser cracking. By adding the bed cracking, we are able to supply additional residence time and catalyst/vapor contact with which to complete the conversion of naphtha to LPG. With this process we are able to attain LPG yields well in excess of 40% with a variety of feedstocks. Maximum conversion is achieved with feeds that are very rich with hydrogen, which could be hydrotreated VGO (vacuum gas oil) or even hydrotreated atmospheric tower bottoms.