Question 55: Given the expansion of the Industrial Internet of Things (IIoT), “Big Data”, cloud-based technologies, and advanced analytics, how are you applying these cutting-edge aspects into their work processes and toolkit to optimize FCC yield, reliability, and safety performance?
BHARGAVA (KBC Advanced Technologies, Inc.)
Some of the biggest challenges we have seen with “Big Data” revolve around security. Within the KBC software suite, we focus on security as our major differentiator. Given the connectors we have in The Cloud, we can now download the data from the refinery in a secure fashion and put it into one location; so, when people retrieve the data, they are all looking at one consistent set. That way, Yield Accounting is not looking at different numbers for closures from their perspective alone. The process engineer has his/her own mass balance that creates a lot of issues around the refinery.
The other big issue here is accessibility of the data: who inputs the data and who has the access to change it. All those issues must be addressed before you start using The Cloud to improve your data that is already on The Cloud. Because we are able to use this data and have access to lots of capacity, we are now able to micromanage, if you please, in terms of identifying and doing performance audits. We are even using this approach for shift performance information to see how one shift is doing against another. We can now get most of the information from The Cloud because we are able to store more data. This easy access to information has allowed simulation to move to a different level. We have been able to use the gobs of data we have from the DCS (distributed control system) to develop models that are more accurate. We can calibrate these models. In fact, in some of the real-time applications we have used, we have been able to calibrate the models on the hour. These models also allow us to set operational targets more accurately. That is about as far as we have gone with “Big Data”. So, it is all about finding your best possible operation and what you have done across the shift on a 24-hour average.
The benefits of having more data, sifting through it, and identifying good stable operation data to develop simulation models are all being used to generate LP (linear program) vectors, which are then used by the planners to help with crude selection and then do a gross optimization. From a yield perspective, it has definitely helped a lot. From a safety reliability standpoint, we now have enhanced unit monitoring. The old method of unit monitoring was to gather a number of KPIs (key performance indicators), have an operating range, and then try to optimize the unit in the operating envelope. We have used simulation as a way to help with some calculated variables that affected reliability of the unit. We have expanded the windows from operating envelopes to an integrity operating window to allow people to have a much better idea of or prediction capabilities on equipment failure.
Finally, having this data on The Cloud has allowed the SMEs (subject matter experts) from within the corporate level of the company to look at the same data set and help with the optimization of the unit from a remote location. You can also do this with third-party consulting companies to allow for another perspective with a fresh set of eyes to help make sure that the unit is running optimally on a daily basis.
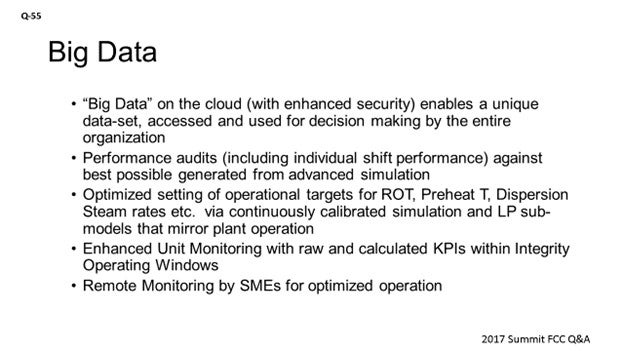
SANJAY BHARGAVA (KBC Advanced Technologies)
With the advent of “Big Data” and cloud-based technologies, refiners are now able to harvest mega data in a process environment. Hundreds of thousands of values are being generated every few seconds to measure, monitor, control, and optimize plant operations. The major benefit of “Big Data” is to demystify the different plant data used by various parts of the organization by using with a common set of information that is utilized by all departments. In the modern refinery, the key is transparency in strategy, philosophy, and shared goals. The benefits are seen in reliability, safety, and operator consistency.
Also, refiners using in-house or third-party simulation technologies are able to extract precise information from these “lakes” of data about the performance and compare it to the best possible performance of the plant. Some companies are already tapping into this pool of information – through the use of simulations – to provide a robust means for selecting a set point or target setting of the independent variables.
The data is also being used in open-loop controls (and limited closed-loop controls) to help make advanced decisions to improve plant performance. The simulation models are being calibrated and updated to maintain prediction fidelity. The calibrated models are being used to generate LP vectors to keep the refiner’s planning models updated in order to mimic actual plant operation which will optimize feed and operating conditions, such as riser outlet temperature, feed preheat temperature, and main fractionator cutpoints in FCCs.
Advanced or enhanced unit monitoring applications are being used by refiners to convert raw data into key performance indicators. These applications are being linked to simulation technologies in real-time to generate calculated/derived key performance indicators focused on ensuring operation within integrity operating windows (IOWs) to help improve the plant reliability and safety and to maximize plant life by monitoring for corrosion, erosion, fouling, and accelerated mechanical equipment damage in order to allow for early action and prevention which will improve reliability and safety performance. These enhanced applications are also being used for predictive maintenance, as well as for monitoring the performance of operators between operating shifts and bringing shift performance closer to best possible operations, which will benefit all shift teams. These advanced unit monitoring applications, in addition to the cloud-based technologies with added security, are now being used by managers to view plant performance dashboards on their mobile devices. Finally, the data can also be used to perform remote monitoring by subject matter specialists – both within and outside of the organization – to optimize FCC operations. This monitoring can be now done due to enhanced security systems put into place to protect refinery data.
KATHERINE JONES (Honeywell UOP)
Honeywell recognizes the untapped potential of the industrial internet of things (IIoT) and sees these capabilities as the next revolution in industry:
-
IIoT enables users to leverage all data available including stranded data that, until now, has not readily used in business decisions.
-
Cloud-based solutions allows for a more collaborative environment to enable users to benefit from global expertise.
-
The use of big data and analytics, combined with the computing power of the Cloud, enables the investigation of large data sources and the discovery of new insights.
Maintaining high onstream efficiency and reliability are critical parameters for maximizing plant profitability. To help our customers maximize the use of their assets, Honeywell UOP offers a suite of cloud-based services with the Honeywell Connected Plant. One of these services, Process Reliability Advisor, combines plant data with UOP Process models that are tuned to current operation, plus a fault model which are cause-and-effect relationships and troubleshooting guides specific for the process. The service utilizes a cloud-based platform that supports big data analytics and machine learning to drive continual innovation.
Process Reliability Advisor enables our customer to:
-
Detect performance gaps early and perform mitigation steps,
-
Understand the unit’s current performance and asset utilization based on constraints, and
-
Promote learning and knowledge retention, leveraging UOP insights and context.
More information can be found at www.uop.com/cps including videos on how Process Reliability Advisor works.