Question 54: Please comment on both personnel and process safety concerns when transporting and receiving crude via rail and truck. What laboratory analyses support this effort?
HERLEVICH (Marathon Petroleum Corporation)
We receive crude by truck and rail at two of our seven refineries. I have prepared three slides to share with you: one for personnel, one for process, and one for sampling. Most of the tight oils we bring in are from under-developed fields that do not have proper gas plants; therefore, they come in fairly wild. Light ends are really the biggest issue.
From a personnel safety standpoint, we wear normal PPE (personal protective equipment), as you would find elsewhere in the refinery: Nomex® and the H2S (hydrogen sulfide) monitor. If there is a benzene hazard, we use respirators. This situation may occur when making up the hose connections. As I mentioned, tight oils tend to be high vapor pressure, which is the real issue. There are also normal hazards associated with elevated work on gangways. Anyone who has worked on a rack knows the difficulties of raising gangways, especially when ergonomic issues are present. So be mindful of ergonomics when you are going through your refineries. Take time to ensure the best possible situation for the people moving the gangways.
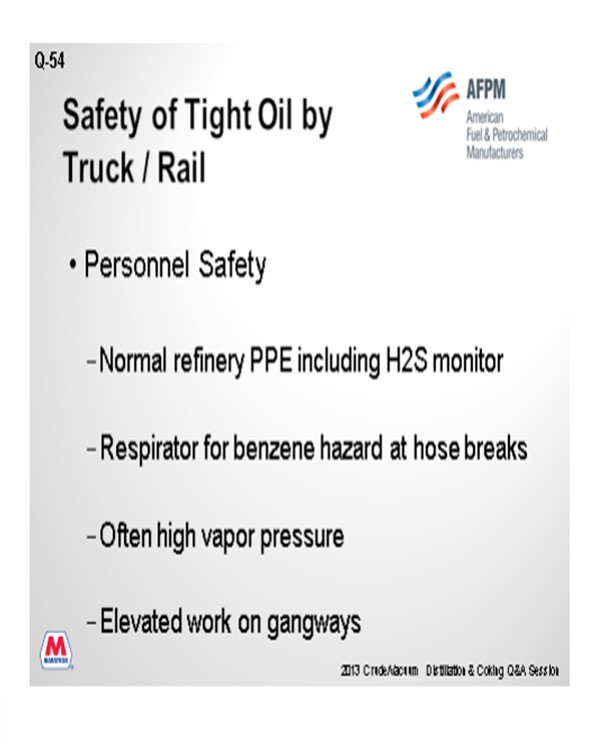
The next slide focuses on Process Safety. First: typical chalking and grounding practices. Sometimes you find folks getting a little lax in these areas, but they are very important. The biggest issue is the light ends; so in both facilities, we de-pressure the railcar to a safe location with vapor recovery. Next, we unload either by pushing the crude with nitrogen or by using a pumped system.
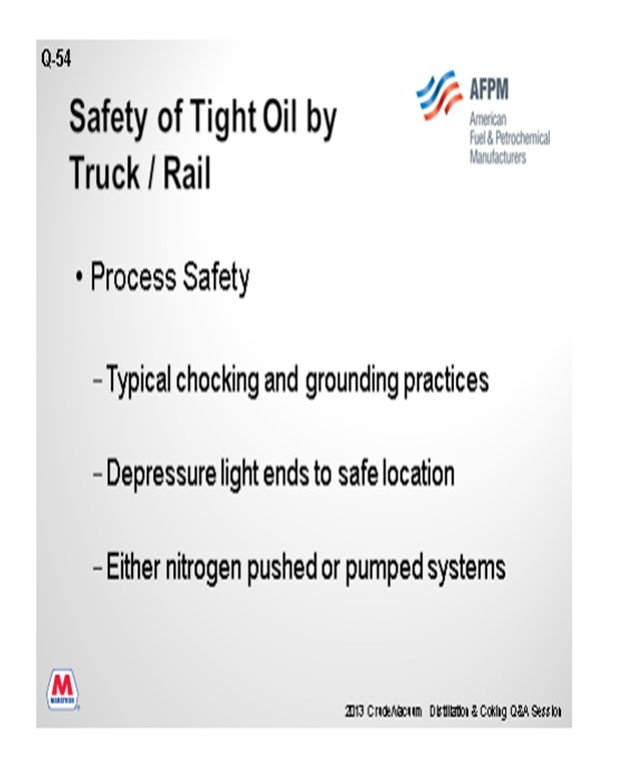
As far as sampling goes, we typically do routine BS&W (basic sediment and water). One of the plants has an RVP (Reid Vapor Pressure) analyzer located nearby. At this plant, they analyze for wild batches and then track its progress through the plant. Full crude analysis is done less frequently, perhaps annually.
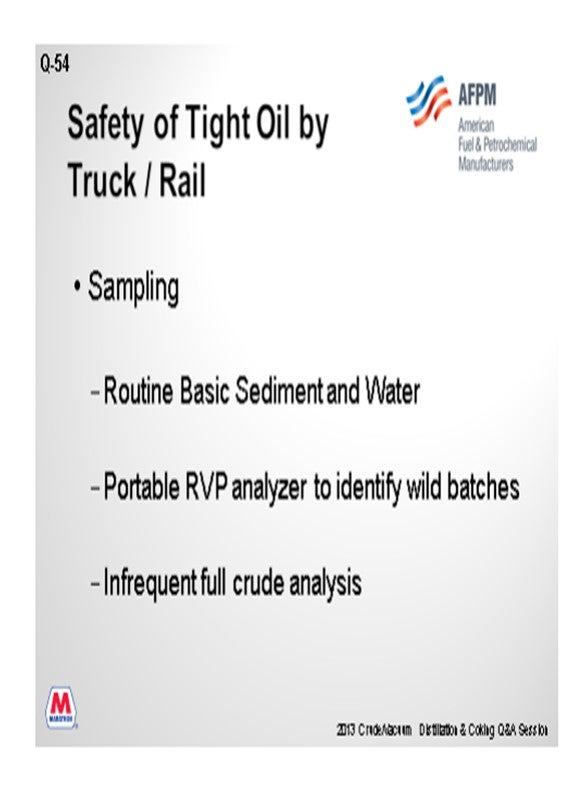
I have also included some information related to Process System Refinements. Being so wild, we had to install vapor eliminators upstream of the pumps. Even after letting the pressure off of the railcar, there were still problems with the pumps gassing off. Regarding piping system hydraulics, they were designed to minimize flashing. Whereas in a refinery you would normally desire very big pipes, in this case you might need to minimize the discharge piping diameter to avoid two-phase flow due to flashing service. Interestingly, in our pumped service, we installed variable frequency drives to change the speed of the pump. Here the motor speed was tied to the pump vibration monitor. It is a fairly unique system. Then when we get a really wild batch of crude, we can dial back the offloading rate.
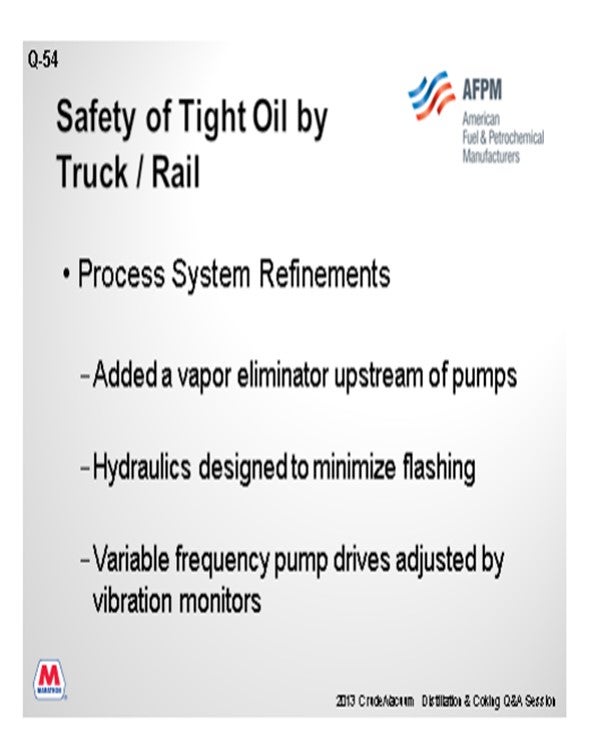
SLOLEY (CH2M Hill)
A few plants use specific laboratory analysis. They are using tests that are essentially standard crude assay tests including the Reid Vapor Pressure, hydrogen sulfide content, and flashpoint when unloading. Most crude transported by either railcar or truck has some hydrogen sulfide scavenger added at some point in the handling system before it gets to the plant. Since trucks are typically driven into the plant by individual drivers, safety issues with access and control are more difficult with trucks. The largest personnel exposure in unloading comes from the physical connection and movement at the trucks and railcars. The facilities need to be arranged to allow for simple, straightforward control of vehicle and personnel access to minimize risks. The safety procedures put in place per our clients include blue-light and blueflag signaling to prevent moving connected railcars. These procedures need to be followed rigorously. Nearly all facilities have automatic de-railers and truck/tank immobilizer systems as a final layer of protection. However, the intent is for this to be a backup layer. It is not a standard control feature. If you have a derailment or truck immobilization, it will need to be investigated and the root cause identified and solved. The intent of the standard facilities and procedures should be to have no derailed tanks or trucks. The facilities can be configured to either use pusher cars or puller cars when moving rail. If at all possible, you should favor puller cars having a locomotive on the front end of the cars where the personnel can see what is going on as they control the train. This setup has resulted in significantly fewer derailments and safety incidents than with puller trains. In addition, facilities need proper layout and grading for the spill containment and handling and other environmental issues.
TOM GERMANY (Calumet Specialty Products Partners, L.P.)
One of our exposure times is when we actually do our measurement. When we put in our rail system, we did not put in a flow meter; we actually gauged the tanks. Does anyone have techniques to gauge it without opening up the big manway using a bent or gauging nozzle?
HERLEVICH (Marathon Petroleum Corporation)
I am not aware of any.