Question 53: What is the panel’s experience with addressing reforming unit stabilizer salting?
PIZZINI (Phillips 66)
I actually have three examples that all apply to a reformer stabilizer. The first slide shows what we call our hot wash. By that, I mean we do not lower the temperatures. We will keep the bottoms re-boil temp in the 440°F to 480°F range. We then have two options on this hot wash. If we just see a high differential pressure on the overhead cooler, then we will put the water in front of that air cooler. It will never actually get into the column. It goes through, condenses, and takes the salts with it; and then, that salty water gets rejected off of the accumulator. You must make sure you are draining that water fast enough to avoid refluxing it.
Another option we have used is putting water in with the feed at 1vol% to 2 vol% for a limited time, maybe 15 to 20 minutes. The goal with that wash is not really to remove the salts because we know that only the evaporated water is leaving in the overhead. We are not letting free water go out of the bottom. However, this technique can buy us a lot of time, sometimes four or six more months before we need to do an offline wash. it is redistributing the salts that happen to be on the trays and which may be causing tray fouling. These salts get redistributed with that particular wash, which buys us some time.
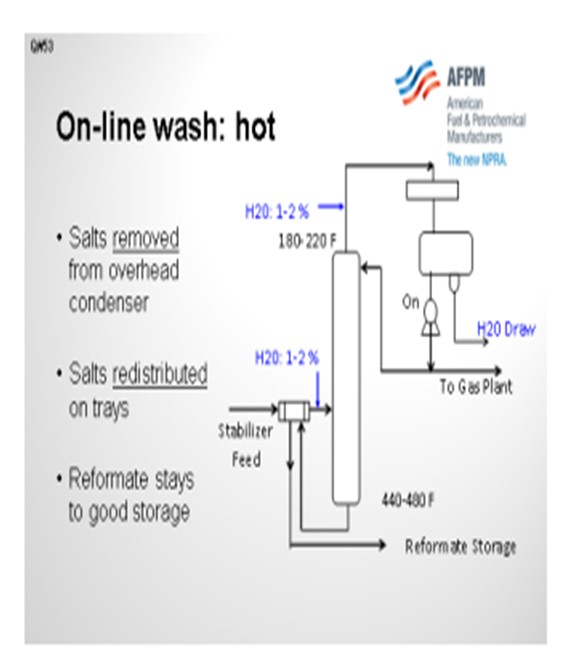
The next slide may be a little more familiar. In this case, you drop the temperature of the column far enough to let free water go out with the bottoms. Now the water you put in dissolves the salts, and that whole mixture leaves out of the bottom of the column. The water rate is a little higher in this example. That hot wash is about 1 wt% to 2 wt%. In this wash, you are putting in water a little more aggressively. You will still get water overhead, so you have to be prepared to drain the overhead accumulator. Another option is to put that water into the reflux line. With the stabilizer feed wash, you also remove salts from the feed exchangers. Now you do want to line the column bottoms to off-spec product storage because it will have a high RVP (Reid Vapor Pressure). You also want to make sure you have some way of recovering the water that is going to end up in the tank farm.
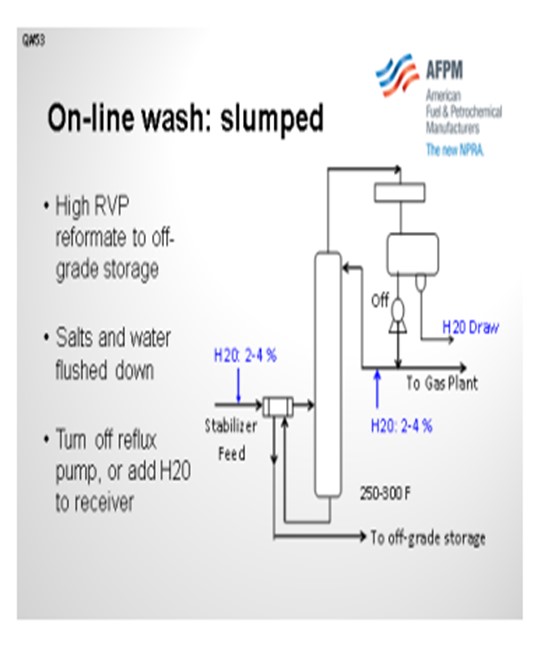
The third example is an offline wash. If you have to take feed out of the unit, a quick and efficient way to do it is to bring water into the overhead accumulator, get a nice high level, and then turn on the reflux pumps for a very high volume wash all the way from the top of the column down. By that time, you will have turned blinds and be routing the slop oil and water
mixture into a dropout system or oily water sewer. Some of our sites have tried just putting insteam. If you put in enough steam, you will be able to dissolve salts. The concern with that option is that you do not really know if you have gotten them all out. So, we would not recommend just steaming.
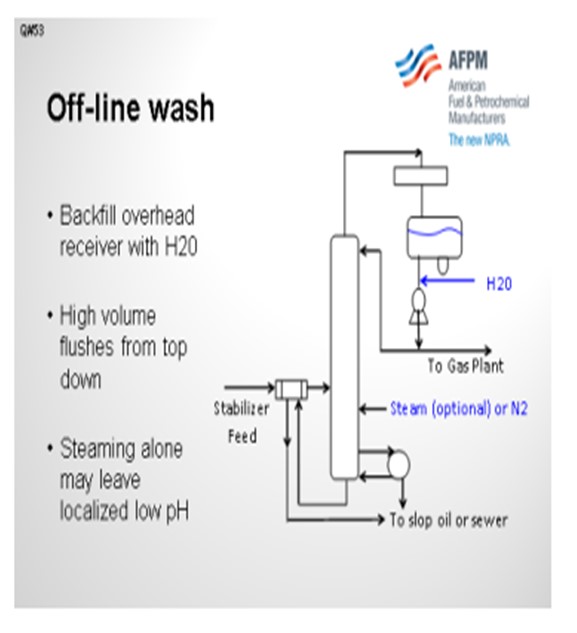
STEVES (Norton Engineering Consultants, Inc.)
My experience in the slump tower operation is the same as what Paul described. The refinery where I work had chloride removal beds on the stabilizer feed, but we still saw salting issues at the top of the stabilizer tower. When tower performance and pressure drop indicated excessive salting, we slumped the tower and washed with condensate through the reflux line. As Paul mentioned, we have to segregate the wet reformate from the bottom of the tower to segregated storage for later reprocessing.
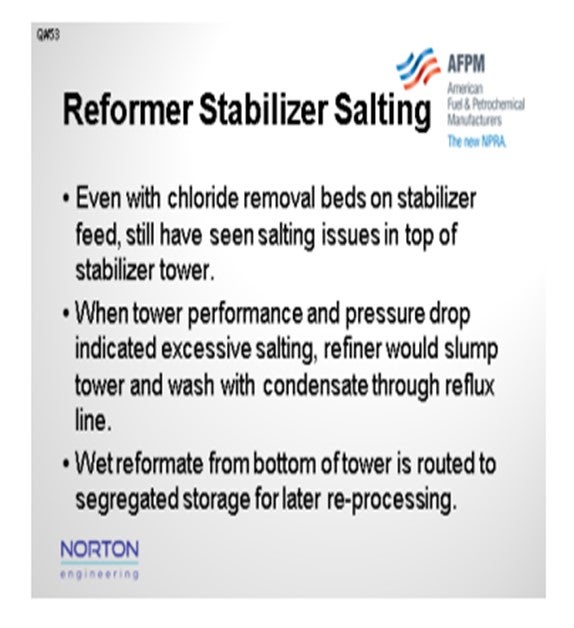
Eventually, though, we re-trayed the stabilizer at this refinery to better remove butanes and meet the vapor pressure specification on the full-range reformate. These new higher capacity trays were also equipped with a directional fixed valve that kept the trays clean. This new tray design was very successful in lengthening the interval required between the waterwashes. We used to go about six months; now we are able to get up to two years plus of good operation before having to do a slump and water-wash.
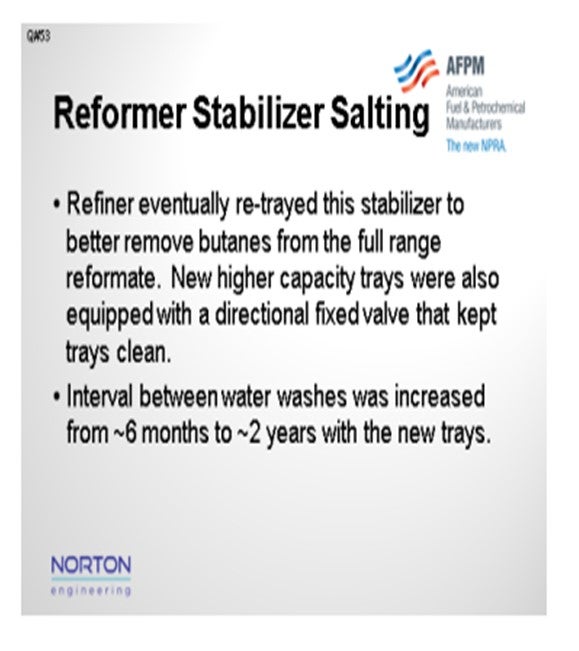
WILLIAM BANDY (Tesoro Refining and Marketing Company)
When you do not slump the tower and leave the bottom of the tower hot, do you run the risk of causing a really corrosive environment in those top trays where you are at a dry point or where the water is just starting to evaporate off?
PIZZINI (Phillips 66)
One factor I did not mention is that we will make sure that wash continues long enough until the water being drained off of the accumulator reaches a neutral pH. Our original practice was to just put in the water until the pressure drop got better, which might be 10 minutes. We did experience some overhead corrosion using that technique, so we changed the procedure to make sure that water injection continues until all of the water coming out is neutral.
WILLIAM BANDY (Tesoro Refining and Marketing Company)
There are there still some salts left in the tower, right?
PIZZINI (Phillips 66)
Correct.
WILLIAM BANDY (Tesoro Refining and Marketing Company)
Those salts that remain incipiently wet are really corrosive compared to the salts that actually did make it into the solution.
PIZZINI (Phillips 66)
We have not seen excessive tray corrosion. Within a few hours, I would expect that it is a dry environment. It takes a little while to get all of the water to evaporate, but we will probably shift this back to dry. The salts are still there, but they are no longer wet.
PAUL FEARNSIDE (Nalco Company)
Another alternative that does not require any water is the use of salt dispersion chemistry. This procedure will not only allow you to clean the tower within an eight- to 12-hour period using a “cleaning dosage”; but with a small maintenance dosage, it will keep the salts moving throughout the tower to avoid future foiling.
PIZZINI (Phillips 66)
Ammonium chloride salts tend to accumulate in the top one-half of reformer stabilizers over time and show up as increased tray ∆P (delta P; pressure differential) and/or increased overhead condenser ∆P, both of which should be routinely tracked. P66 has had success with three different types of stabilizer washes.
1) Least disruptive is an “online” wash which is done at normal column operating temperatures to prevent sending high RVP material to tankage. Boiler feed water or condensate is added to the stabilizer feed line at around 1 wt% to 2 wt% [e.g., 4 gpm (gallons per minute) to 8 gpm on 20 mbpd (thousand barrels per day) stabilizer feed]. Water is drained from the overhead accumulator every 20 to 30 minutes to prevent refluxing salt-bearing water back into the
column. Salts are removed from the overhead condenser as the water evaporates overhead from the stabilizer and passes through the condenser. Salts in the column are not actually removed; they are redistributed across more tray area, which typically resolves tray ∆P issues for several months or until the next scheduled outage.
The wash is continued until the pH of the water exiting the overhead accumulator is near neutral (7 pH). Stopping the wash too early can lead to corrosion from leaving wetted salts behind. The system needs to be well drained and dried to prevent corrosion in the tower and overhead system.
2) The second type of online wash is similar to the first, but the reboiler temperature is “slumped” to 250°F to 300°F to allow water and salts to flush down the tower. This approach requires pre-planning to direct the reformate to off-grade storage which can handle 10 RVPto 12 RVP material and water. As heat is cut, the reflux pump will need to be shutoff. Water is injected into the stabilizer feed at 2 vol% to 4 vol% for 30 minutes, and then into the reflux line at a similar rate for 30 minutes. Water off of the column bottoms and overhead is tested for pH, conductivity and chlorides. The wash cycles are repeated until the washwater has properties similar to the fresh water. Drain the tower overhead system frequently over the next two days as the unit dries out.
3) The third type of wash is performed offline. Steaming out an offline tower is often sufficient at removing salt deposits. A higher volume wash can be performed by batch filling the overhead accumulator with water and using the reflux pumps to flush the column from the top down. It is a good idea to perform this type of wash proactively whenever the stabilizer is down.