Question 53 How are you planning to meet Tier III gasoline specifications? Please share your strategies for post-treat and pre-treat options, feedstock selection and catalyst technology? Can renewable feedstocks be co-processed with traditional diesels in an existing ULSD (Ultra Low Sulfur Diesel) unit and how does this impact RIN's (Renewable Identification Number)?
Amit Kelkar and James Esteban (Criterion Catalysts & Technologies)
FCC gasoline has the highest sulfur content and is also the largest volume component of the mogas pool of a typical US refinery. Consequently, most refiners are evaluating options to reduce FCC gasoline sulfur (to 20 – 30 ppm) to comply with Tier III regulations. Options under consideration include FCC feed pretreat, FCC gasoline post-treat or a combination of the two.
The CAPEX for a grass-root FCC feed pretreat unit is significant; however, HDS performance of existing pretreat units often can be improved with minimal capital investment. In some cases, simply increasing operating severity while utilizing the best available catalyst technology such as Criterion’s CENTERA® technology provides an acceptable cycle life and meets desired product specifications. In addition, many refiners are considering the addition of reactor volume, improvement of catalyst utilization by installing new reactor internals, and hydrogen partial pressure improvements via compressor modifications, recycle gas scrubbers, membrane units, and higher purity hydrogen sources. These changes in modes of operation and modifications are critically tied to improvements in catalyst performance and technologies. In many refineries the drive to improve product yields and maximize profitability has made FCC feed pretreat a highly desirable and profitable process. \
Several refiners, working closely with Criterion, are evaluating options for improved operating severity of FCC feed pretreat units targeting maximum aromatics saturation for improved FCC yields and profitable hydrogen upgrade. Increased FCC pretreat severity results in improvement in the quality of the FCC feed leading to higher conversion and improved yields. This option is constrained by the pressure rating & H2 availability of the pretreat unit; low pressure pretreat units (< 800 psi) with MU H2 limits are not typically suitable for higher severity operation. It is important that the capabilities of each unit be carefully considered using resources such as catalyst manufacturers and technology licensors to evaluate potential for meeting refinery specific targets.
CAPEX for a new FCC gasoline post-treat unit is lower than for pretreat and can be an attractive option. Post-treat technologies which reduce FCC gasoline sulfur content while minimizing olefin saturation & octane loss are well established in the industry. Octane loss is expected to increase at the higher severity required for Tier III; recent developments in post-treat catalyst can be employed to minimize this loss.
In conclusion, a strategy to comply with Tier III regulations depends on each refinery’s unique configuration and constraints. In most cases, it involves a combination of changes to both post-treat & pretreat operation.
A paper presented at the Annual Meeting earlier this year discussed this issue in more detail (Tier III Capital Avoidance with Catalytic Solutions by Patrick Gripka, et al.)
Roberto Amadei (Chemical & Energy Development srl.)
A pre-condition, to be carried out, of the optimum strategy for compliance with Tier III gasoline specifications and ULSD renewable and traditional diesel specifications is the following (already outlined above in our response to Question #7).
The naphtha catalytic reforming unit has to be partially unloaded, by subtracting from its traditional feedstock the higher-boiling C6 hydrocarbons, including naphthenes, benzene and hexane. Typically, the optimum allocation of this material unloaded from reforming is the isomerization unit. The deriving set-up of reforming and isomerization has the potential of generating value in several ways and in no way destroys any value. However, also in case of an allocation of the above material different from the isomerization, its unloading from reforming keeps a significant potential of generating value.
The main components of the optimum reforming + isomerization set-up generated value are the following:
-hydrogen net production gain,
-gasoline yield gain,
Gasoline octane number gain, changeable at will into an additional gasoline yield gain, compliance, with margin, with the most severe limits of gasoline benzene content in the world, such as the 0.62 vol% content required by the United States Environmental Protection Agency, in the US resulting in saleable benzene content credits, significant energy savings, besides the hydrogen net availability gain one, emissions reduction of all of the pollutants and greenhouse gases types, in addition to the above, both in the gasoline production and consumption segments, also carrying out a gasoline lifecycle emission reduction of a few percent of CO2 equivalent, higher octane gasoline production capacity increase, improvement of the engine operation and maintenance.
The case study experimental results pointing out the above and the relevant theoretical explanation can for instance be seen in PTQ and Digital Refining 2013 Q1, article “Improved hydrogen yield in catalytic reforming”, or in “Gasoline Processes”, 2011 NPRA Q&A and Technology Forum.
Referring to the particular North America case, we premise that the optimum set-up of reforming and isomerization carries out the production of gasoline and hydrogen in lieu of fuel gas. With this due premise, we can conclusively deduce that the above hydrogen gain is much more convenient than the hydrogen production carried out by means of special units consuming the cheap shale gas (SMR).
Precisely, neglecting here the gasoline-fuel gas replacement value, said hydrogen production gain is over three times cheaper, as far as the variable (operating) costs alone are concerned. In fact, in the case of the optimum reforming-isomerization set-up, the shale gas should be used, for combustion in the furnaces, in order to replace the fuel gas not produced anymore by reforming. In such a way the rate of substitution of fuel gas by shale gas is 1:1. On the contrary, any use of shale gas for producing hydrogen would require the consumption of more than 3 units of shale gas (taking into account all the energy flows, both consumed and produced by the SMR unit) per each unit of produced hydrogen (rate of substitution: >3:1).
Moreover, depending on the specific refineries, the relevant hydrogen gain can even avoid the capital costs of either installations or revamps or even duplications of the special, highly energy consuming, hydrogen generation units.
The FCC-gasoline pre-treat and post-treat options and the ULSD processes consume hydrogen and energy. Furthermore, the FCC-gasoline post-treating causes reduction of the FCC-gasoline octane number and yield, due to saturation of high-octane olefins.
It is apparent that the optimum set-up of reforming and isomerization, as it provides hydrogen gain, reduction of energy consumption and gasoline octane plus yield gain, counteracts the FCC pre-treat and post-treat options and the ULSD processes negative effects. Plus, it provides additional very low sulfur combined reformate-isomerate gasoline blending component, due to its yield gain, thus allowing a higher sulfur content of the FCC-gasoline for a given full gasoline sulfur content: this allows to carry out a further reduction of the FCC pre-treat and/or post-treat options negative effects.
The two last paragraphs outline the qualitative aspect of the matter. As far as the quantities in play are concerned, HOP (Hydrogen-Optimization) analyzes and optimizes the operation and any asset of the specific refinery as a function of the specific refinery plant structure, refinery supply slate and predicted upcoming additional needs of hydrogen, energy, gasoline octane and gasoline yield, also providing alternative cases results.
Here we owe an explanation: HOP is an Alliance established between Chemical & Energy Development and Prometheus, rendered very suitable by the worldwide hydrogen thirst that deserves the maximum management efficiency. Chemical & Energy Development brings to the new Alliance its deep knowledge and practice of the specific, above indicated, technology and Prometheus brings to the new Alliance its deep knowledge and practice of planning and optimization procedures and of refinery engineering design.
The resulting project gives a substantial contribution to meeting the Tier III gasoline and ULSD specifications.
Brian Watkins and Charles Olsen (ART)
Tier 3 gasoline regulations are requiring that all gasoline is to contain ≤10 wppm sulfur. This is a decrease from the current Tier 2 regulations of ≤30 wppm sulfur. This change in product sulfur can have a dramatic impact on refiners that have a significant portion of their gasoline pool generated from the FCC. In order to meet this regulation, there are only two methodologies to reduce the gasoline sulfur pool, and both involve some level of hydrotreating, either before or after the FCC unit. The process of hydrotreating after the FCC unit however can have a dramatic effect on the gasoline octane levels due to the additional olefin saturation that occurs when removing the last amount of sulfur.
For those refiners that utilize a hydrotreater in front of their FCC unit, changes to that operation need to be considered in order to meet the desired product targets. To address these needs, Advanced Refining Technologies LLC (ART) utilizes the ApARTTM Catalyst System for FCC pretreatment. This technology is designed to provide significant increases in HDS conversion while at the same time providing significant upgrading of FCC feedstock quality and increasing yields. In essence, an ApARTTM Catalyst System is a staged bed of high activity NiMo and CoMo catalysts where the relative quantities of each catalyst can be optimized to meet individual refiner’s goals and constraints. ART has continued to develop a better understanding of the reactions and kinetics involved in FCC pretreating, and through its relationship with Grace Davison Refining Technologies, a detailed understanding of the effects of hydrotreating on FCC unit performance.
It is clear that FCC pretreating plays an important part in reducing the sulfur content of FCC products. ART has completed many studies looking into the effects of hydrotreating on FCC performance and the quality of the FCC products. The work demonstrates that reducing the sulfur in FCC gasoline and LCO simply requires a reduction in the sulfur of the FCC feed by increasing the severity of the pretreater. Figure 1 shows the relationship between FCC feed sulfur and the resulting sulfur of the FCC gasoline.
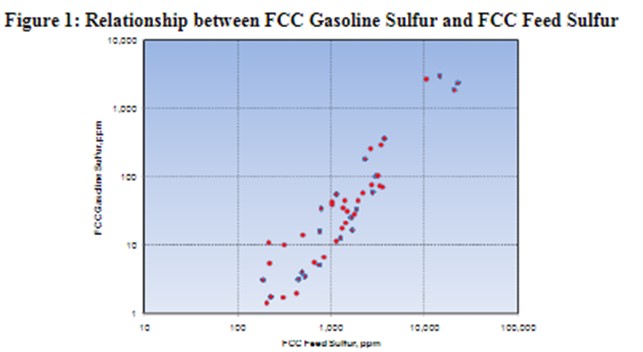
This data was generated using a variety of FCC feeds that had been hydrotreated over several types of catalysts and catalyst systems. As can be seen in the chart, there is a good correlation between FCC feed sulfur and the corresponding FCC gasoline sulfur. In this case, the sulfur content in the FCC gasoline is roughly 100 times less than the sulfur in the feed to the FCC. Increasing the severity of the pretreater operation in order to drive down the product sulfur will tend to move the catalyst towards more of a PNA mode of operation. This mode of operation, while beneficial to the FCC in many ways, can impact the cycle length due to the increased temperatures. Both the hydrotreating catalyst system and the operating strategy for the pretreater are critical to providing the highest quality feed for the FCC. Driving the hydrotreater to remove nitrogen and PNA's improves FCC product value when targeting gasoline production, but this needs to be balanced against the increased costs of higher hydrogen consumption and shorter cycle length that result from this mode of operation. Use of tailored ApARTTM catalyst systems with 586DX and AT795 can optimize the FCC in order to produce not only high-quality feeds to the FCC but also lower sulfur products resulting in less impact on downstream hydrotreating. This tailoring can also be beneficial if the FCC products are able to be blended directly without hydrotreating, as they can be driven towards lower sulfur and higher gravity products allowing the refiner to be able to blend these fuels directly without sacrificing the FCC gasoline octane level.