Question 52: What approaches are effective for you to reduce aromatic levels in the ULSD product streams?
TEMME (Albemarle Corporation)
To reduce aromatic levels, we definitely need to assess the unit’s capabilities. Is it a high hydrogen partial pressure unit with psig greater than 800, and does it have a higher than 4.0 hydrogen availability ratio (HAR)? If both answers are greater than those reference points, then full-loading of NiMo catalyst can be employed to give higher hydrogenation and very good aromatic saturation results. Potentially, using a base metal- or high metals-content catalyst or noble catalyst can be done as well.
For base metal catalyst or high metals-content catalyst, it can operate in a sour or a high H2S environment, whereas a noble catalyst cannot do so as effectively. If you have a lower hydrogen partial pressure unit, it might limit the amount of NiMo catalyst that can be employed effectively in a stable manner. So, with a lower hydrogen partial pressure unit, it may require higher reactor temperatures for aromatic saturation that can cause the aromatic saturation equilibrium point to be reached sooner. It can cause increased deactivation rates.
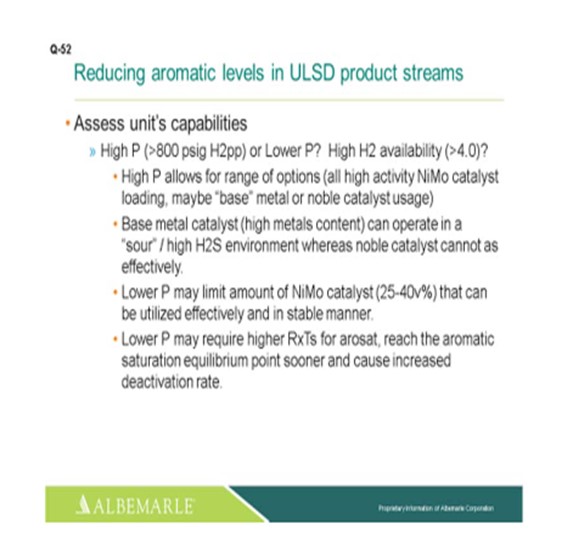
The next slide illustrates the aromatic saturation equilibrium curve phenomena where TAis the max aromatic saturation temperature. As you get past that, and if you do not have as much aromatic saturation going on, you will get to a certain temperature where the amount of aromatics saturated and where those aromatics that are produced come to an equilibrium point, TB. Beyond that, you will have higher deactivation rates. So not everyone has the ability to really change the hydrogen partial pressure; but yes, increasing the hydrogen partial pressure can help greatly with aromatic saturation performance.
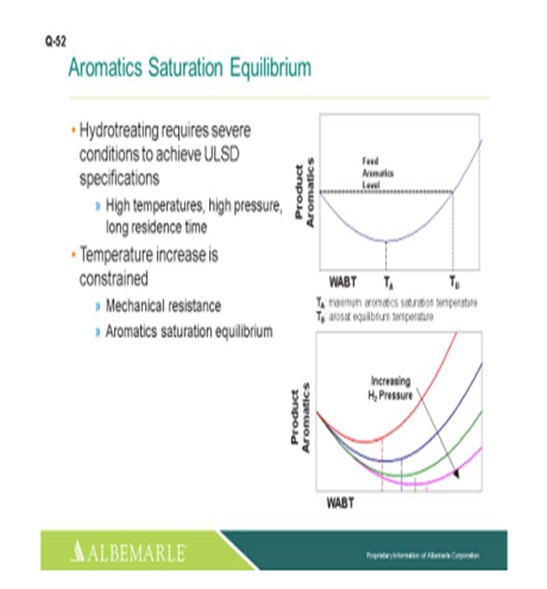
Here we have a unit where there is very good aromatic saturation performance with the use of a base metal catalyst. After 500 days onstream, there was a feed upset due to a heavy gas oil feed incursion. So, there was a little bit of an activity hit, but the unit kept on performing.
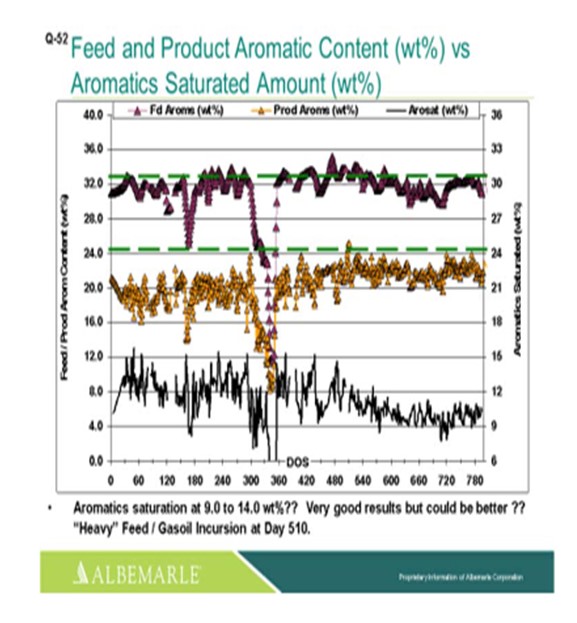
The next slide is a deeper illustration of the aromatic saturation equilibrium point concept that shows that increased pressure will help shift the maximum air sat temperature up a little higher.

So what other approaches are effective? Feed selection, feed adjustment, use of appropriate feeds, and feed cutpoint should be assessed to fit desired product goals and cycle length. With higher operating pressure units, they have much more ability to process all feeds; whereas, a moderate to lower pressure unit may be limited in the more straight-run diesel and some limited amount of coker diesel or LCO. And then, obviously, reduction of high aromatic feed or endpoints of that feed can aide aromatic level reduction, especially towards end-of-run.
An equipment solution could be the addition of a second-stage air saturation reactor, but that additional equipment and noble metal catalyst can be expensive. But then, the resulting product can yield high payback.
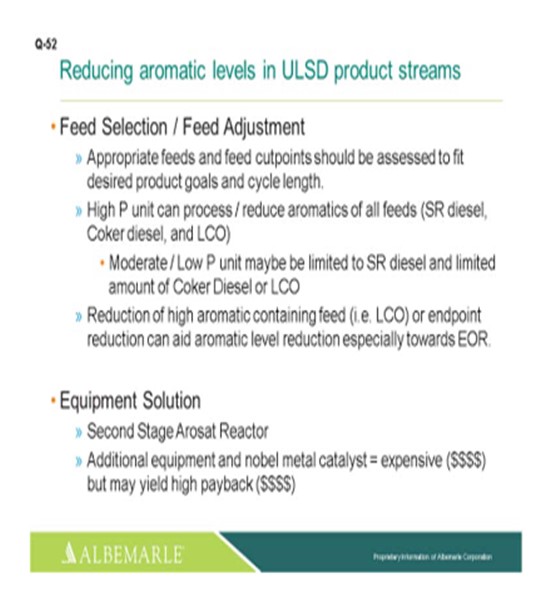
MORELAND (Valero Energy Corporation)
Valero operates two refineries in California, and they each take a different approach to producing low aromatics CARB diesel.
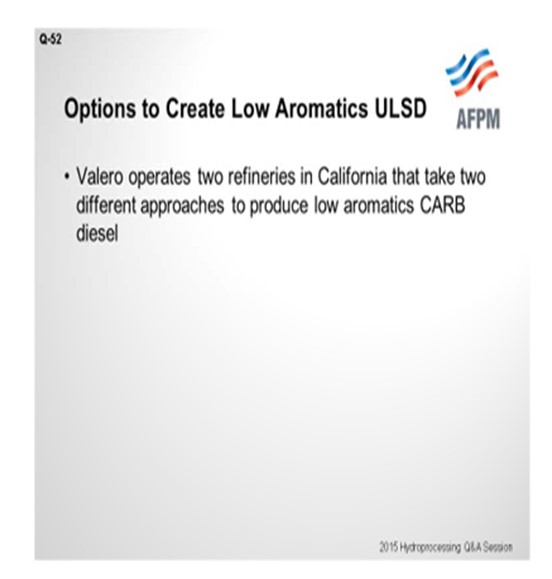
The slide is about the Benicia single-stage ULSD unit four-bed reactor with high activity NiMo catalyst in Beds 1, 2, and 3. The bottom bed is loaded with the highest activity catalyst we can find. It is one of the bulk metal catalysts we talked about before. We tend to run a flat to slightly ascending temperature profile targeting 675 to 680°F in the bottom bed to hit that maximum aromatics saturation point to which Paul referred. This unit also operates around 900 to 1000 pounds of pressure, and we control feed aromatics and reactor temperature profile to meet a 24% weight CARB waiver fuel for that unit. We have other high pressure ULSD units in our system that run in a similar mode not necessarily to make a low aromatics product, but to maximize volume gain and cetane uplift.
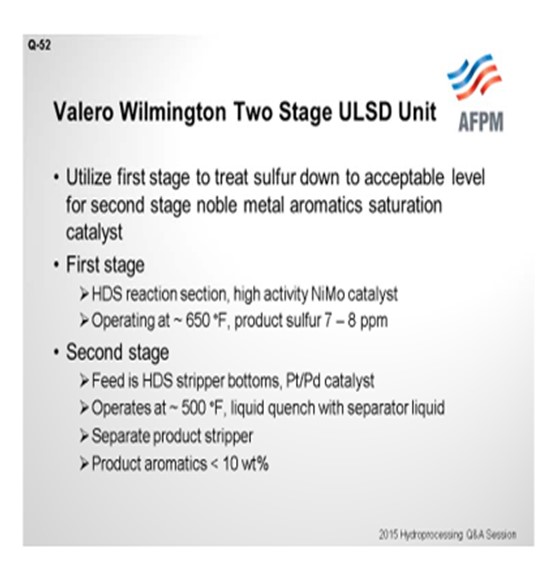
Next is Valero’s Benetia single-stage ULSD unit four-bed reactor with high activity NiMo catalyst in Beds 1, 2, and 3. The bottom bed is loaded with highest activity catalyst we can find. It is one of the bulk metal catalyst we talked about before. We took the runner flat to slightly ascending temperature profile targeting 675 to 680°F in the bottom bed to hit that maximum aromatics saturation point to which Paul referred. This unit also operates around 900 to 1000 pounds of pressure, and we control feed aromatics and reactor temperature profile to meet a 24% weight CARB oil refuel for that unit. We have other high pressure ULSD units in our system that run in a similar mode not necessarily to make a low aromatics product, but to maximize volume gain and cetane uplift.
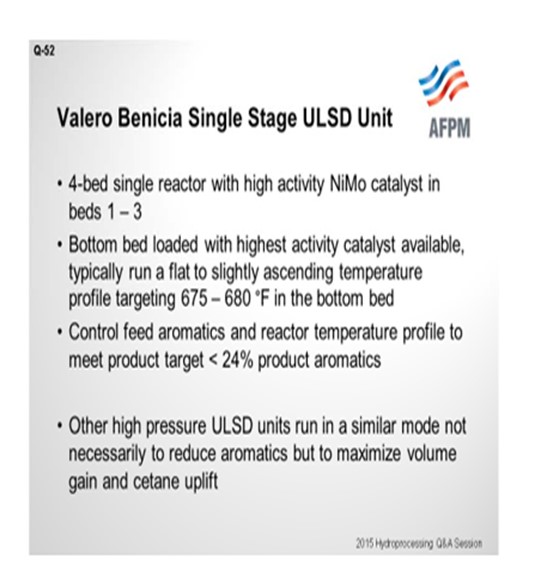
McARTHUR (Phillips 66)
I have a slide, but it does not add any additional information that the other two guys haven not already discussed. So in the interest of time, we will move on.
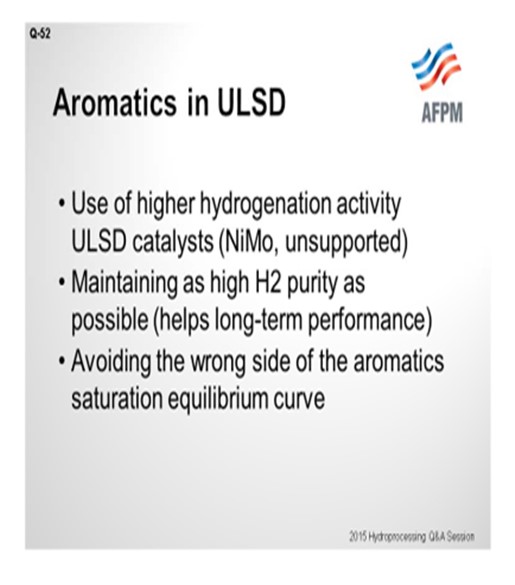
RAMÓN FARACH (Hargrove & Associates, Inc.)
Oh, you are holding us back from dinner.
ROBERTSON (AFPM)
Ramón, be sure you say really loud who you are! [Laughter]
RAMÓN FARACH (Hargrove & Associates, Inc.)
Just a really quick comment. As a process engineer for a former employer, I was responsible for a medium pressure ULSD unit that struggled to meet product color specifications towards the end-of-run as we passed the maximum aromatics saturation temperature. Typically, we tried to run equal outlet temperatures on every bed with our four-bed reactor to maximize cycle length. However, we did find some success extending our cycles by running an inverted temperature profile near the end-of-run, heating up the first bed and quenching the bottom bed as much as possible to achieve the target 675 to 680°F for maximum aromatic saturation. That is just another approach for reducing aromatics and addressing color problems at end-of-run.
PETER BENDTSEN (Haldor Topsoe, Inc.)
For many refiners, it is a target and necessity to reduce the aromatic content in their ULSD product streams. The reasons can be multifold:
1.The ULSD product quality must meet specifications on a maximum aromatic content (meeting local aromatic specifications, such as CARB, or if Cetane Index Spec cannot be met for ASTM D-975 diesel and a total aromaticity of less than 35 vol% becomes governing).
2.Meeting secondary objectives, typically increasing cetane number, lowering of API gravity, reducing NOx, and particulate matter.
To reduce aromatic content in the ULSD product, there are some simple, but often less economically favorable, approaches such as:
1.Feed Control: Reduce amount of cracked material, especially LCO streams to reduce aromatics and nitrogen content, especially effective on coker streams and manipulate feed boiling points to reduce aromatics and nitrogen content; and,
2.Product Control: Blend in higher grade products with lower aromatic content.
CATALYTIC APPROACHES
The most effective and often most economical method to reduce aromatic levels in ULSD product streams is during hydroprocessing. In order to discuss this in more detail, a little background on aromatic compounds will be helpful.
When looking at aromatic species, it is normally distinguished between polynuclear aromatics, PNA, which are two+ benzene ring structures and monoaromatic (MA) species (one benzene ring structure) due to the much different reactivity of these classes of compounds.
In a hydroprocessing environment, the last aromatic ring (mono aromatics) is much harder to saturate as compared to saturating one-ring structures in PNAs. Hence, in a hydroprocessing environment, the polyaromatics are relatively easily converted to monoaromatics, which, however, are not easily converted to their products (naphthenes). It is magnitudes harder to reduce the last benzene ring to a naphthene due to larger amount of H2 involved.
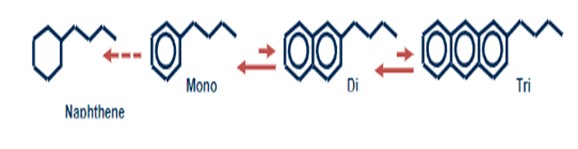
Base Metal Hydrotreating: Saturation of PNAs in hydroprocessing is dictated by the equilibrium between the PNA and the monoaromatic compound; i.e., the degree of saturation (=conversion) of PNA to MA is a function of hydrogen partial pressure and operating temperature for the hydrotreating process. Examples of typical saturation profiles can be seen below in Figure 1. For a fixed hydrogen partial pressure, as is the case for most existing hydrotreating units, the degree saturation then follows the operating temperature. For higher pressures, higher degrees of PNA saturation is seen. Accordingly, it is beneficial to increase operating pressure and hydrogen purity of the treat gas as much as possible (as the practical knobs to turn) for maximum aromatic saturation; and if operating at a low temperature at the beginning of the cycle, then temperatures can be increased to increase aromatic conversion.
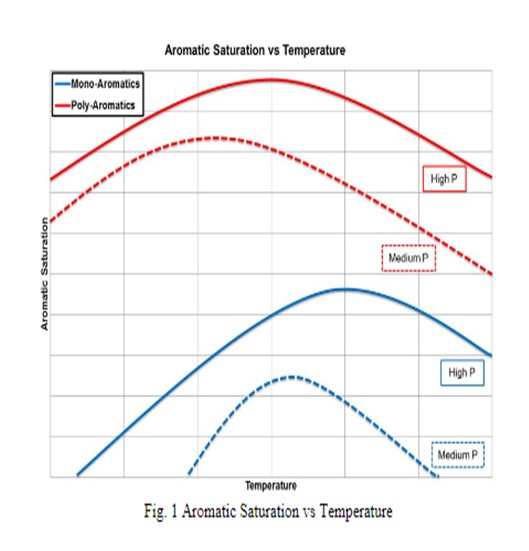
When the PNAs are converted to monoaromatics, the total aromatic content of the ULSD fuel is not reduced; rather, the percentage of monoaromatics increases by same amount as the polyaromatic content is reduced. Hence, total aromatic content stays the same. Refer to the examples in Table 1 below exemplified by a high LHSV system operating at medium and lower pressure.
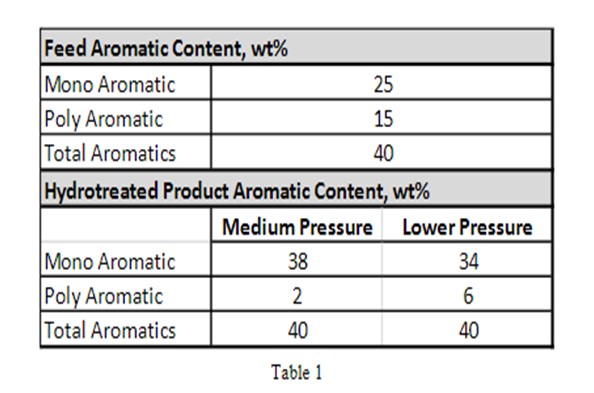
As can be seen from the example above, it is necessary to reduce the monoaromatic content to reduce the total aromatic content of a ULSD stream.
Where PNA species are rather easily converted to monoaromatic species, the conversion of monoaromatics to the corresponding naphthenes is dictated and limited by both reactivity/catalyst activity and equilibrium constraints. From
Figure 1 above, it is seen that at high temperatures, an equilibrium between monoaromatic species and the corresponding naphthenes is governing. As seen in the figure, the maximum saturation occurs at higher temperatures as the pressure is increased, which is consistent with a shift in the equilibrium concentration. The existence of a maximum conversion at a given pressure indicates a limitation imposed by thermodynamic equilibrium.
This means that to effectively, and significantly, reduce aromatic levels in ULSD product, often higher activity catalysts and hydrogen partial pressures are required; and these are often combined with directionally lower LHSV (high residence time) across the catalyst bed. Saturation of monoaromatics is promoted by high catalytic activity (right-type catalyst) and favorable operating conditions and/or process layout.
The saturation of monoaromatics is documented by Haldor Topsoe, Inc. researchers to take place on the active BRIM® sites of the hydrotreating catalysts. In general, NiMo-promoted catalysts tend to have a higher concentration of active BRIM® sites over CoMo-promoted hydrotreating catalysts. Since the degree of removal of monoaromatics is driven by catalyst activity up to a certain temperature (where equilibrium sets in), then higher activity catalyst products (with more active BRIM® sites) is strongly favored. This especially applies to Haldor Topsoe, Inc.’s NiMo promoted TK-609 HyBRIM™ that has market leading hydrogenation activity for maximum aromatic reduction.
The effectiveness of a NiMo catalyst system is highly dependent upon the system hydrogen pressure and LHSV: the higher the hydrogen partial pressure and the lower the LHSV, the higher the degree of monoaromatic saturation will be. When installing TK-609 HyBRIM™ aromatic removal, degrees of upwards of 30 to 60% can be achieved under the right conditions, i.e., high hydrogen partial pressure (800 psig+) and lower LHSV (< 1.3 hr-1).
As a further caveat, monoaromatic saturation is strongly inhibited by organic nitrogen. Hence, catalyst performance is very dependent on feed nitrogen content and the ability/activity of the catalyst towards removing the organic nitrogen species, i.e., to achieve substantial monoaromatic saturation and effectively reduce aromatic levels in ULSD product streams, it is first required that almost all organic nitrogen is removed in the top part of the reactor to render the bottom part of the reactor virtually free of organic nitrogen for high levels of aromatic conversion. That is, the higher the nitrogen content of the feedstock, the more difficult the feed is when it some to reducing total aromatic content.
Summary: To reduce ULSD aromatic content in conventional hydrotreating, consider the following:
1.Maximum activity: Choosing right catalyst, i.e., NiMo and maximizing catalyst volume,
2.Maximize hydrogen partial pressure by maximizing operating pressure and maximizing treat gas hydrogen purity,
3.Minimize feed aromatic and nitrogen content, and
4.Considering operating temperatures, possibly operating colder towards reactor outlet, if possible, by use of quenching.
Noble Metals Hydrotreating: Metal sulfide catalysts (NiMo) are often not used when aiming for deep hydrogenation of aromatics due to their relatively low turnover frequencies and a temperature operating range that is relatively high as compared with the thermodynamic limitations of the hydrogenation of aromatics.
For the deep hydrogenation of aromatics, there are dedicated technologies available, such as two-stage HDS/HDA (hydrodesulfurization/hydrodealkylation) solutions. This implies a hydrotreating reactor in the first stage (HDS) to remove all organic sulfur and nitrogen to very low levels (a few ppm) and then a noble metals promoted [Pt/Pd (platinum/palladium)] in the second stage for high aromatic conversion. The HDS/HDA is an elegant process with little yield losses and good improvement in product properties along with reducing aromatic content.
From aromatic saturation, there are general secondary benefits: density reduction and volume swell/gain. With access these days to cheap H2, it makes economic sense for many refiners to increase hydrogen consumption through aromatic saturation for max product yield.
Hydrocracking: Hydrocracking is another option for reducing ULSD aromatics content in that naphthenes are cracked and hydrogenated to paraffins, and this drives more aromatic saturation. This technology is often not preferred as it intrinsically comes with higher yield losses. However, hydrocracking is the ultimate tool for aromatic reduction in ULSD, but it is also more costly. This would be considered where only very high aromatics reduction or high API gravity uplift is good enough and not be reached with any other technologies. For instance, this could apply to upgrading heavy LCO to on-spec ULSD product.
MIKE ROGERS (Criterion Catalysts & Technologies)
Refiners are often interested in lowering the ULSD product aromatic level to achieve higher cetane (due to a market opportunity or a regulatory requirement) or to meet an aromatics regulatory limit. Sometimes, lowering diesel product aromatics is necessary to meet the product color specification. Aromatics impact diesel engine performance because they have poorer combustion properties than paraffins and other diesel-range hydrocarbon species. The amount of aromatics in the diesel fuel will therefore affect the efficiency and power output of the engine and also the hydrocarbon emissions in the exhaust. Cetane number reflects the ignition characteristics of the diesel.
Reducing product aromatic levels requires adding hydrogen to the aromatic rings. The diagram below shows a series of aromatic saturation reactions: The diaromatic naphthalene molecule is saturated to monoaromatic tetralin, which is then saturated to decalin. Further hydrogen addition opens the aromatic rings of the decalin molecule to create the normal paraffin n-decane. Cetane number progressively increases from 1 to 77 via these saturation reactions.
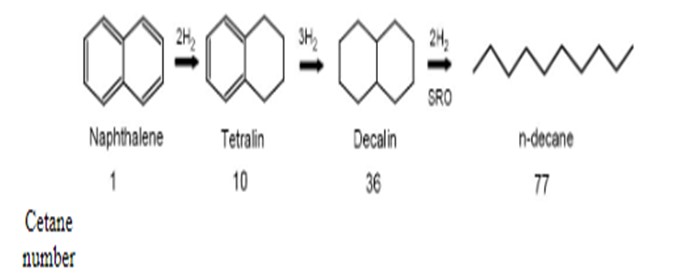
The saturation reactions are reversible. Overall aromatic conversion is governed by both reaction kinetics and equilibrium. The equilibrium point for the aromatic saturation reactions is strongly affected by aromatics concentration, temperature, and hydrogen partial pressure.
The chart below demonstrates the temperature and liquid hourly space velocity (LHSV) effect on aromatics reduction. Aromatic saturation reactions are slow at low temperature. Increasing temperature will increase the rate of aromatic conversion. However, the reaction eventually reaches the equilibrium point, and then increasing temperature further will actually reverse the reaction. The dotted line indicates the equilibrium conversion rate as temperature is varied. Reducing the reactor space velocity will increase aromatics saturation, as shown by the three solid lines. Additionally, using higher activity nickel-molybdenum (NiMo) catalysts will increase the aromatic saturation rate for a given temperature and space velocity.

The following approaches are effective ways to reduce ULSD product aromatics. These can, of course, be applied together to leverage the full capabilities of the hydrotreater and the catalyst system.
1.Maximize hydrogen partial pressure.
‐Maximize the unit pressure.
‐Maximize hydrogen purity in the makeup gas.
‐Maximize recycle gas rate (Criterion recommends that the recycle gas hydrogen content be at least four times the hydrogen consumption rate).
‐Maximize the feed initial boiling point to reduce the amount of feed vaporization.
2.Minimize LHSV by maximizing catalyst volume and catalyst utilization.
‐Use the most effective reactor internals, such as those offered by Shell Global Solutions (HD Trays, UFQ Quench internals, outlet baskets, etc.) to maximize the amount of catalyst that can be loaded into the reactor and to increase catalyst utilization by improving liquid distribution through the catalyst bed.
‐Follow Criterion’s Catalyst Loading Guidelines to maximize the amount of catalyst loaded into the reactor.
‐If the refinery has multiple diesel hydrotreaters, optimize feed to each unit to hydrotreat only the most aromatic streams in the highest-pressure unit and send the lower aromatics feed components, such as kerosene or straight-run distillates, to the lower pressure unit (the point of this optimization is to reduce the space velocity within the highest-pressure unit).
3.Optimize the catalyst bed temperature and bed temperature profiles through the cycle.
‐Set the catalyst bed temperature at the point to achieve maximum aromatic saturation. This approach will likely result in product sulfur ‘giveaway’. However, smart quench operation can minimize the impact on catalyst cycle life.
‐Bed temperature profiles can sometimes be optimized to maximize aromatic saturation, particularly near the end of the catalyst’s lifecycle. If the temperature of the last bed of a multi-bed reactor bed is beyond the aromatic equilibrium temperature, lowering the temperature by increasing the quench rate may reduce the product aromatic level.
4.Improve reaction kinetics by using highest hydrogenation catalysts.
‐Use maximum-activity nickel-molybdenum catalysts with the highest hydrogenation capability. For example, Criterion’s CENTERA™ catalysts, like DN-3636, are being used in many commercial units to increase aromatics saturation, thereby increasing the amount of high-aromatics feed being treated and increasing the amount of volume gain. Some of these units process as much as 80% light cycle and coker diesel.
5.Utilize additional Enhanced Aromatic Saturation (EAS) Options.
‐If the above options do not yield the desired product aromatics, further aromatics reduction is possible using an enhanced aromatic saturation unit with a two-stage reaction system. Such units have a first-stage reactor containing base-metal catalyst, which lowers sulfur and nitrogen levels. H2S and NH3 are separated from the first-stage reactor effluent, and the liquid stream is fed to a second-stage aromatic saturation reactor that contains either a high-activity base-metal CENTERA™ catalyst or an H2S-tolerant deep aromatic saturation (DAS) noble-metal catalyst, such as Criterion’s C-654 or C-684 catalyst. C-654 and C-684 catalysts tolerate moderate levels of H2S (<100 ppm) in the recycle gas and produce the lowest possible product aromatic level.
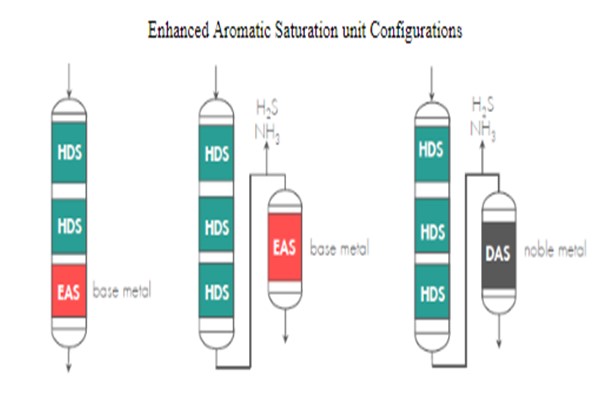
LCO and coker gas oil have low value as blending stocks because of their poor cetane and high sulfur levels. Thus, upgrading the maximum amount of these streams to ULSD is often very economically attractive but also very challenging, as far as product quality and run-length management. Criterion and Shell Global Solutions have a wide range of well-proven technologies and know-how to help each refiner take advantage of its unique opportunities and overcome even the most difficult challenges.