Question 52: Explain the differences with renewable and Biodiese. Can renewable feedstocks be co processed with traditional diesels in an existing ULSD (Ultra Low Sulfur Diesel) unit and how does this impact RIN's (Renewable Identification Number)?
Celeste McLeod (CRI)
Renewable Diesel is a hydrocarbon. Commercially, Renewable diesel is made from hydrotreating vegetable oil & animal fat. Renewable diesel must meet the specifications for diesel, either ASTM D 975 or D 396 in the United States.
Biodiesel refers to Fatty Alkyl Methyl Esters that have been produced by the transesterification of vegetable oils or animal fats. The resulting FAME or "Biodiesel" product still contains oxygen, and is therefore, an oxygenate. Specifications for biodiesel are contained in ASTM D 6751.
Renewable feedstocks, i.e., vegetable oil and animal fats, can be co-processed with traditional diesels in existing ULSD units. Catalyst selection is a consideration as these feeds contain oxygen. Additional considerations that should be reviewed during a management of change or equivalent process evaluation would include things such as:
•New feed components and side reactions
•Higher hydrogen consumption
•Accumulation of CO, CO2 and other lights in recycle gas
•Undesirable product cold flow properties depending on co-processing percentage in the feed
•Fouling resulting from poisons (Na, P, Cl) and diene formation and polymerization
•Coking and corrosion
How does this impact RIN's (Renewable Identification Number)? A RIN is a 38-character numeric code that corresponds to a volume of renewable fuel produced in or imported into the United States. RINs remain with the renewable fuel through the distribution system and ownership changes. The RFS mandates are prorated down to “obligated parties”—individual gasoline and diesel producers and/ or importers—based on their annual production and/or imports. Under the Renewable Fuels Standard (RFS2) only certain pathways qualify for RINs. The eligible pathways for generating RINs are defined by their renewable biomass feedstock input, the technology used for processing, and the resulting fuel products. Each pathway is assigned a D-code that groups all resulting pathway derived fuels together.
A table containing eligible feedstock, pathways and fuels produced is available at the EPA website: http://www.epa.gov/otaq/fuels/renewablefuels/new-pathways/rfs2-pathways-determinations.htmPertaining to vegetable oil neat processed and vegetable oil co-processed, they would each have to meet the prescribed greenhouse gas reduction, etc., excerpt from above website referenced table
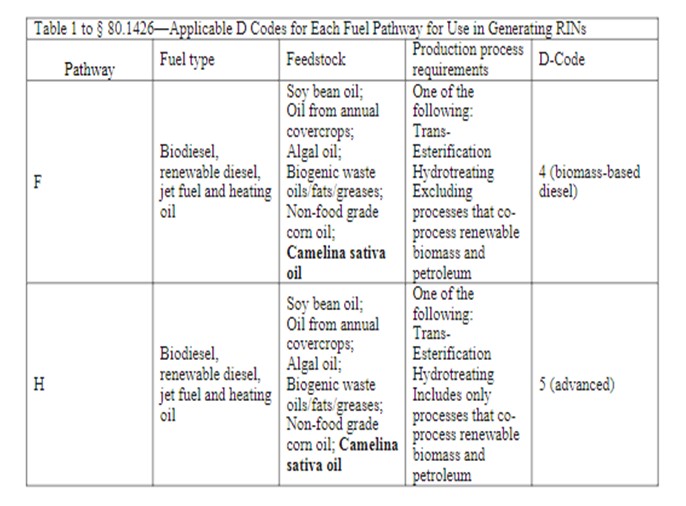
Operations that meet the 100% vegetable oil/animal fat processing requirements and greenhouse gas reduction would likely be successful in fuel registration for a D-Code of 4, allowing for generation of RIN’s once the facility registration process was completed and approved.
Operations co-processing the vegetable oil/animal fat and greenhouse gas reduction would likely be successful in fuel registration for a D-Code of 5, allowing for generation of RIN’s once the facility registration process was completed and approved.
Approval of such lies with the US EPA, and refiner’s own evaluation group should determine the best application scenario for their purposes.
Brian Watkins and Charles Olsen (ART)
Fuels that are produced when vegetable oils or animal fats are processed in traditional refining processes are considered Co-Processed Renewable Diesel. Some common sources of renewable feeds are those produced for food grade oils such as soybean, rapeseed and other vegetable oils. The traditional process for introducing these sources into the diesel pool is to use the transesterification reaction for breaking the glycerol from the fatty acid chains.
Advanced Refining Technologies’ (ART) has completed extensive pilot plant studies demonstrating that these types of feeds can be co-processed with traditional diesels in an existing ULSD unit. Refiners who use the co-processing method would have exact knowledge of the bio-based fuels that are incorporated into the diesel pool which helps to ensure the finished blend quality.
One consequence of co-processing is an increase in n-paraffins in the diesel. This can be of significant value for ULSD as they have typical cetane numbers ranging from 95 to 110 which can provide a significant boost for those refiners processing feeds with lower cetane (i.e., FCC LCO’s). The typical diesel hydrotreater has only a small effect on cetane with cetane upgrade of about 2-4 numbers.
Another concern is that these renewable feed sources can include various contaminants. An analysis of several different bio feed sources has indicated the presence of contaminants such as sodium, calcium and phosphorus. Since these renewable feeds are derived from a biological source, they also contain a high concentration of oxygen. The oxygen content ranges from 10 to 15% and is entirely dependent on the length and degree of saturation of the fatty acid chains. This quantity of oxygen is important, as under normal hydrotreating conditions the oxygen will react with the hydrogen to form water. This water, if generated in a significant enough quantity, may cause problems such as weakening the catalyst support or redistribution of the active metals and loss of surface area. At the expected blending ratios of 10%, the oxygen content is around 1 to 1.5 wt%, and even if all of the oxygen is converted, this is unlikely to generate enough water to be a significant problem.
Due to the addition of unsaturated chains from the bio component, there is expected to be an increase in hydrogen consumption to saturate these C=C bonds. The co-processing of bio components may yield improvements in the diesel cetane due to the increase in n-paraffin content in the diesel product. These n-paraffins, however, raise concerns about the bio feed-based diesel cloud point. Normal paraffins have a significantly higher cloud point than other hydrocarbons of similar carbon number. Since hydrotreating converts the fatty acid chains into long chained n-paraffins, it is expected that the cloud point of the hydrotreated product will increase compared to the product using the SR base feed.
Tony Barnette (UOP)
Biodiesel (or FAME- Fatty Acid Methyl Ester) is a product of the transesterification of oils, fats, or grease, resulting in the production of FAME and glycerin byproduct. Renewable Diesel is the product of hydroprocessing of oils, fats, or greases, resulting in a full hydrocarbon product (first as n-paraffin, followed by isomerization to produce a high grade, isomerized hydrocarbon product with properties verisimilar to petroleum diesel. High value propane and naphtha by-products are also produced. Other important differences to note:
•The FAME product is an oxygenate, and as such, is not as stable as conventional diesel, or renewable diesel, both of which are full hydrocarbon products. As a result, FAME cannot be transported in existing diesel pipelines, whereas Renewable Diesel can, greatly reducing transportation costs of delivering this fuel.
•Renewable Diesel has both a higher cetane number and lower density than either FAME or petroleum diesel, allowing it to be an excellent blend stock into a refiner’s diesel pool. Blending of Renewable Diesel allows the blending of lower value feed stocks with higher density and low cetane number- creating a synergistic effect and increasing the value of these lower quality feeds.
•Renewable Diesel has higher RIN value (1.7 RIN/ gal for Renewable Diesel, vs 1.5 for FAME) due to higher energy content.
•Higher value byproducts (propane and naphtha for Renewable Diesel, vs. glycerol for FAME), which can be used within the refinery, with existing infrastructure for handling and transportation.
•Renewable Diesel cold flow properties generally can be adjusted to meet seasonal requirements, without the need to switch to higher cost feedstocks- a two stage process for producing Renewable Diesel can maintain excellent cold flow properties while processing lower grade feedstocks simply by adjusting the degree of isomerization in the second stage, whereas in production of FAME, cold flow properties are dependent on the feed used (i.e. when lower cloud point fuel is required, the process must switch to higher cost feeds that can produce FAME with lower cloud point).
Can renewable feedstocks be co processed with traditional diesels in an existing ULSD (Ultra Low Sulfur Diesel) unit and how does this impact RIN's (Renewable Identification Number)?
Tony Barnette (UOP)
Renewable feedstocks (such as vegetable or seed oils, used cooking oil, or animal fats) can be co-processed in an existing diesel hydrotreater unit with limitations. These limitations include:
•Byproducts- renewable feedstocks contain significant oxygen, and when hydroprocessed this oxygen forms either water or carbon dioxide in quantities that a typical distillate hydrotreater is not equipped to remove.
•Heat Release- renewable feed stocks have a much higher heat of reaction, resulting in much higher heat release in the reactor. Generally distillate hydrotreaters are not designed to handle this high heat release, and may exceed to units recycle or quench capacity. Higher temperatures that may result from this high heat release can also reduce catalyst life.
•Generally, without modifications, conventional distillate hydrotreater systems are only able to process ~ 5 vol% renewable feed stocks without modifications to handle the above issues.
Additionally, there are disadvantages to producing renewable fuel via co-processing, such as:
•While co-processing does not affect the value of the RIN for the product, Renewable Diesel produced by co-processing is not eligible for the current $1/ gallon blender tax credit.
Renewable Diesel product is not available as a neat product, and is therefore not available as a separate product that might be sold at a premium.