Question 51: For hydroprocessing reactor modifications that involve the addition or removal of distribution trays and flexible thermocouples, what is your Best Practice for welding support rings or support lugs on a reactor wall? What is your Best Practice for removal of these items when they are no longer required?
SIVADASAN (UOP LLC, A Honeywell Company)
When you are trying to remove the attachments from the reactor, do not touch them unless it interferes with your process flow, catalyst loading, or internal installation or access. When the rings are welded to the support rigs, remove the rings and leave the lugs in its place. If both the lugs and the rings are welded into the shell, try to cut a short distance from the shell, using appropriate cutting methods, in order to minimize the heat input and potential damage to the shell from the cutting operation. When trying to install the attachment, avoid welding to the base metal; because once welded, a post-weld heat treatment may be required.
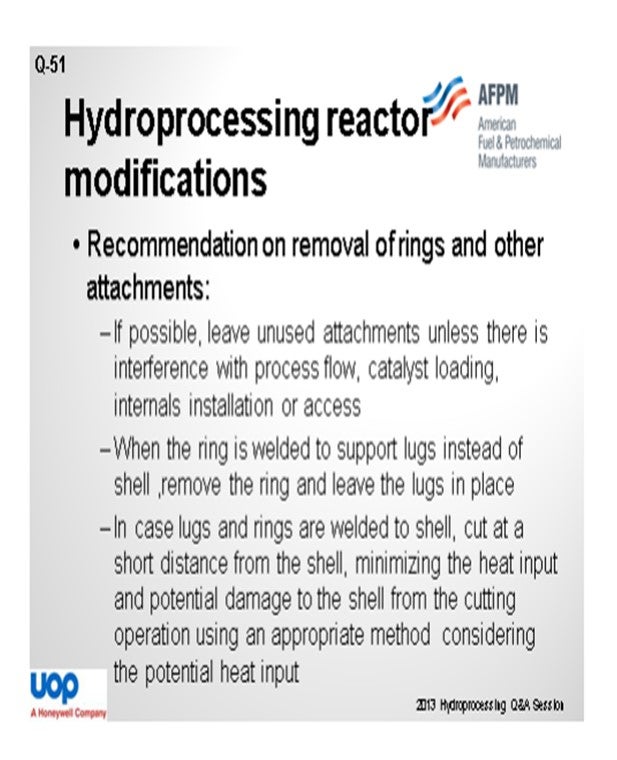
If you plan to go ahead with the cutting operation, do the removal of the coke and hydrogen from the base metal and do an NDE (non-destructive examination) of the area to be welded to detect any flaws that may be affected or ruined by welding. The weld needs to be full-penetration and ground to a generous concave contour. The weld-and-attachment chemistry should match what it is being welded to at the base metal. Once the welding has been done, do an NDE to detect any defects. Once the NDE is complete, a recertification based on the laws prevailing in that country may be required.
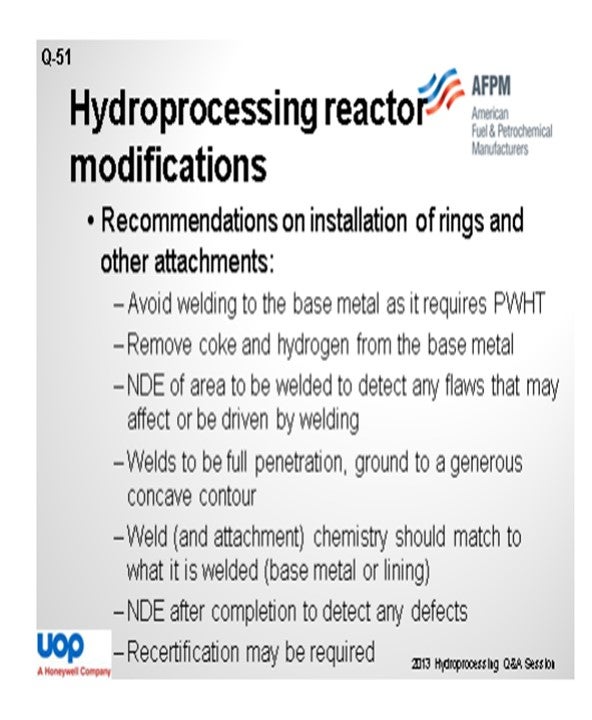
RAJESH SIVADSAN (UOP LLC, A Honeywell Company)
In hydroprocessing reactors, support rings are used to support internals like a tray or catalyst support grid. Support rings are fixed on the reactor ID (inner diameter) either by weld buildup to the base metal or forged as part of the shell course. The following recommendations apply to reactors made of low chrome base metal in hydrogen service:
Recommendations on Removal of Rings and Other Attachments
1. If possible, leave unused attachments in place. They should be removed if they will interfere with process flow, catalyst loading, internals installation, or access.
2. Where the ring is welded to support lugs but not to the shell, and when leaving everything in place is not possible but only the ring needs to be removed, then remove the ring and leave the lugs in place. In this case, cutting at or near the shell is not required. If cutting near the shell is necessary, the points in #3 (below) apply.
3. Cut lugs and rings welded to the shell a short distance from the shell (e.g., closest approach of the cut to the shell at least 10mm). The intent is to minimize heat input into the shell and minimize the potential for damage to the shell from the cutting operation. The cutting method should be chosen considering the potential heat input. A dehydrogenation heat treatment may be necessary before cutting, and NDE before and after cutting is advisable. If coke is present, it must all be removed. NDE before cutting may identify a defect (e.g., crack) that might be driven by the cutting operation, and NDE afterwards may identify a defect caused or enlarged by the cutting operation.
Recommendations on Installation of Rings and Other Attachments
1. Welds should be full-penetration, ground to a generous concave contour. Stainless steel rings should not be circumferentially welded. Weld (and attachment) chemistry should match to what it is welded (base metal or lining).
2. Welding to the base metal should be avoided. PWHT (post-weld heat treatment) of low chrome requires an elevated temperature [e.g., 690°C ± 15°C (1275°F ± 25°F)]
3. Removal of hydrogen from the base metal (dehydrogenation heat treatment) and removal of coke may be necessary.
4. NDE of the area to be welded to find any flaws that may affect or be driven by welding. If welding to lining, UT to confirm the lining is 100% bonded. For heavy loads, UT of the base metal may be necessary to ensure there are no laminations.
5. Weld the lining using a procedure that does not require PWHT of the base metal, i.e., the heat-affected zone does not penetrate the lining. This will require a mockup to confirm.
6. NDE should be conducted after completion of the attachment to detect any defects caused or driven during the attachment process.
7. A recertification of the reactors may be required.
KLAUS RISBJERG JARLKOV (Haldor Topsøe, Inc.)
Adding support rings or clips to a reactor shell depends on several factors:
• Existence or absence of weld overlay,
• Size of bracket/support ring, and/or
• Magnitude of the load size support and weld size.
If the reactor is provided with weld overlay, adding a support ring/support clip may be done using low heat input welding using a weld size, which will not affect the base material. The welding must be done by a certified stainless steel welder. If a strong weld is required, a larger weld can be applied by using several pass welds with sufficient cooling time in between the passes. The root pass should be touchable by hand before continuing with the next pass.
If the support ring/lug/bracket is heavily loaded and requires being fully welded to the base material, pre-heat treatment and post-weld heat treatment will be required in accordance with the code.
Carbon steel reactors will require both pre-heat treatment and post-weld heat treatment in accordance with the code.
Support rings/lugs made of stainless-steel material can be removed by grinding. Use caution not to damage the weld overlay. Sometimes it will be possible to weaken the weld beads on the brackets and thereafter remove it by knocking it from side to side until it breaks. For heavier brackets/support rings, gauging may be used. Leave at least 1/8" to the weld overlay and use a protection shield between the weld overlay and gauge. If the bracket is removed flush to the weld overlay, pre-treatment of the area is recommended.
Attachments that are welded to carbon steel or low alloy steel, pre-heating, and other heat treatments specified in the welding procedure shall also be applied in order to prevent cracking.
ROBERT TORGERSON and SYDNEY GARRETT (Gayesco International)
We find it extremely rare, during hydroprocessing reactor modification, that rings or support lugs are added to the reactor other than near the outlet collector on the final bed. It is much more common to use low profile support rods attached to the distribution tray for inlet points with only the end of thermocouple penetrating into the active catalyst to minimize interference. Outlet points utilize low profile supports coming up from the catalyst support beams directly aligned with the inlet point above. This prevents the necessity of welding to the reactor.
Additionally, it is possible to use any existing attachments in the reactor as part of the thermocouple support network. Supports for old pipewells or previous thermocouple installations are good examples. We have also had retrofits involving welding of supports to the wall; but given the ease of the vertical support rod installations, that practice has significantly decreased.