Question 51: For advanced (closed) riser termination systems, where does coke form inside the reactor vessel? What is the typical amount accumulated during a run?
MINAZ MAKHANIA (UOP)
The quantity of coke is heavily dependent on reactor technology, feed quality, and operating conditions. In earlier termination devices the riser outlet was open to the reactor. The vapors would spend a lot of time in the reactor resulting in coking. In direct connect systems, there is significant hydrocarbon entrainment down the diplegs. This hydrocarbon can spend significant time in the reactor resulting in coking. Minimizing the time, the hydrocarbon vapor spends in the reactor is key to minimize coking. The coke produced in the reactor space can build up on the reactor walls or refractory, pressure equalization openings, and other flexible joints that can lead to either equipment failure or increased maintenance costs. UOP’s advanced riser termination system is VSS. The latest VSS technology creates a hydrocarbon free environment in the dilute phase of the reactor by maximizing riser hydrocarbon containment and using a physical barrier between the process and annular space. This helps.
prevent coke formation in the reactor dilute phase. Coke has been eliminated from the reactor annular space. The VSS technology has been used as a process revamp improvement as well as a technology upgrade to address coke formation.
Also, UOP has moved away from the use of slip joints that tend to coke over and seize if the rope seal is not properly maintained. Properly designed dome steam is also important. Coke can still form at the backside of the reactor cyclone gas tubes especially in resid units, UOP now includes coke anchors in the design to provide a site for deposition of coke. Reactor plenum is also susceptible to coke formation depending on feed quality and degree of atomization of feed.
Amount of coke accumulated:
With UOP’s latest VSS technology – while processing low con carbon feed, only about a 1” coke layer is observed in the reactor plenum, all other areas of the reactor are free of coke. While processing high con carbon feed, significant (1” to 10” thick) coke build up is observed in the reactor plenum, up to 4” thick coke deposits on back side of the reactor cyclone gas outlet tubes at the location of the coke anchors and a very small / insignificant (<1” thick) coke deposits on other components of the riser termination system are observed.
DEWEY STUART (Motiva Enterprises)
Typical locations of coke, in the reactor vessel of closed coupled systems, is in the top head of the reactor starting around the cyclone hangers and the plenum. We have also experienced coke growth on the exterior of the cyclone bowl. At our location this has varied from TA to TA. The most accumulation experienced occurred from operation or location of the stripping and purge steams for the system. During steam curtailment these are one group of systems that can save on steam however this comes at a cost. A minimum flow to keep the top section feeding the low flow zones should always be maintained. High residence time of the vapor and the coke coted catalyst fines stripped from the reactor stripper leads to thermal cracking and coke formation. This becomes a significant hazard to remove during unit turnarounds. While removing the coke care should be taken to prevent workers from exposure to falling coke. Typical accumulation when all purges are designed and operated well should be limited to a thin layer.
CASEY LANG (MERRICK & Co.)
Closed containment with form on space between stripper and vents, key to minimizing coke is minimizing this space.
MATTHEW WOJTOWICZ (UOP)
The quantity of coke is heavily dependent on reactor technology, feed quality, and operating conditions. In earlier termination devices the riser outlet was open to the reactor. The vapors would spend a lot of time in the reactor resulting in coking. In direct connect systems, there is significant hydrocarbon entrainment down the diplegs. This hydrocarbon can spend significant time in the reactor resulting in coking. Minimizing the time, the hydrocarbon vapor spends in the reactor is key to minimize coking.
The coke produced in the reactor space can build up on the reactor walls or refractory, pressure equalization openings, and other flexible joints that can lead to either equipment failure or increased maintenance costs.
UOP’s advanced riser termination system is VSS. VSS technology has evolved over the last 20 years. Most of the improvements have been reliability driven. The latest VSS technology creates a hydrocarbon free environment in the dilute phase of the reactor by maximizing riser hydrocarbon containment and using a physical barrier between the process and annular space. Additionally, steam is injected into the dilute phase above the barrier. With these features, coke has been eliminated from the reactor dilute phase. The VSS has been used as a technology upgrade in revamps to improve process performance and to address coke formation.
UOP has moved away from the use of slip joints that tend to coke over and seize if the rope seal is not properly maintained. Coke can still form on the back side of the gas tube in units that process residue. The reactor plenum is also susceptible to coke formation depending on feed quality and degree of atomization of feed. UOP has incorporated design features to address these areas as well.
Evolution of UOP’s VSS Riser Termination Technology
Before evolving to the VSS riser termination technology, UOP gained experience with all types of riser termination technology. Since 1983, UOP’s designs for riser termination devices have focused on reducing the post-riser vapor residence time in the reactor vessel. Since many of UOP’s efforts have involved technology upgrades in existing units (revamps), a variety of mechanical systems have been implemented to accommodate the wide variety of existing reactor sizes and styles. All the UOP designs emphasize operating flexibility and mechanical reliability.
UOP’s current riser termination design incorporates the state of the art, VSS technology to help minimize the vapor passing into the reactor vessel and thereby help minimize non-desirable reactions.
In 1995, UOP commercialized VSS technology which was specifically designed for higher capacity units with an internal riser while maximizing hydrocarbon containment, operating flexibility, and mechanical reliability. UOP’s VDS technology offers the same benefits for units with external risers. VSS technology has evolved since it was initially commissioned in 1995. These enhancements have further improved hydrocarbon containment, operating flexibility, and mechanical reliability. A few of these enhancements are summarized below.
Hydrocarbon Containment Advantage
VSS separation technology represents the highest hydrocarbon containment technology available, and it provides more than 99% containment of the hydrocarbon product vapor relative to only 94-97% for the next best system (direct connected cyclone systems). The containment advantage is based on the quantity of hydrocarbon product vapor that is entrained with and adsorbed on the catalyst discharging from the first stage cyclones. This hydrocarbon is equivalent to as much as 6% of the riser vapor. The hydrocarbon carry-under spends relatively long residence times in the reactor vessel before finally exiting out through pressure equalizing tubes.
VSS separation technology is designed to eliminate the hydrocarbon flow which exits at the bottom of the conventional riser separation devices as well as efficiently separating the catalyst from vapor exiting the riser. The top of the stripper and the bottom of the VSS chamber are integrated with each other allowing the riser and stripper vapors to be contained. These vapors are prevented from entering the reactor vessel where they can undergo non-selective thermal cracking due to long residence times. The containment advantage of VSS technology is illustrated in Figure 1. Since the original implementation in 1995, the design has been tweaked to further improve hydrocarbon containment. The bed level has also been optimized further improving yield selectivities.
Figure 1 VSS Hydrocarbon Containment Advantage
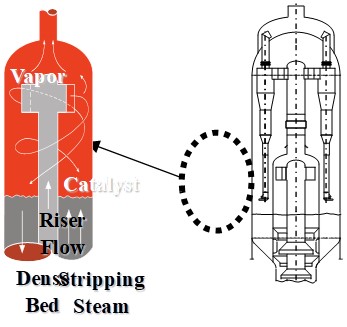
The superior hydrocarbon containment performance of the VSS technology provides improved yield performance over all competitive systems. The hydrocarbon not contained by the primary separation device undergoes significant non–selective thermal cracking due to long residence times in the reactor vessel. This results in a significant increase of dry gas as well as major losses of gasoline, LCO and overall product olefinicity. Dry gas production at the expense of the gasoline and LCO production represents an opportunity loss which limits the profitability of the FCC unit. Additionally, the reduced olefin content of the gasoline will result in a reduction in the octane of final FCC gasoline product. VSS technology reduces nonselective, post-riser cracking and can help maximize the profitability of the FCC unit through improved gasoline selectivity, improved gasoline octane and reduced dry gas.
Operability and Reliability Advantage
UOP has significant experience within Fluid Catalytic Cracking technology and has garnered a reputation for designing technologies for maximum operability and reliability. VSS technology offers clear operational advantages over previous generation riser termination devices (RTD’s), including ease of startup, turndown flexibility, reduction in reactor coke formation, and reduced incidents of severe erosion of internal components.
During FCC unit startups, operations can experience pressure upsets which quickly send large amounts of catalyst into the reactor vessel. Pressure upsets of this kind are known to quickly overload other RTD designs and send large amounts of catalyst to the main column. This can cause costly high catalyst to make up rates and can cause problems in the main column or the main column bottoms product. Conversely, VSS technology can easily handle pressure surges and reduce the risk of catalyst carry overusing its unique primary separation design. This operational advantage manifests itself as smoother and more robust operation of the FCC unit during upsets and is relatively more forgiving during unit startups.
Not only does VSS technology offer process and operability advantages, but it also can provide several reliability advantages. Coke formation in a reactor is largely influenced by the reactor technology and appropriate use of steam. The coke produced in the reactor space can build up on the reactor walls or refractory, pressure equalization openings, and other flexible joints that can lead to either equipment failure or increased maintenance costs. The latest VSS technology creates a hydrocarbon free environment in the dilute phase of the reactor by maximizing riser hydrocarbon containment. This prevents damaging coke formation in the reactor dilute phase. Coke has been eliminated from the reactor annular space. VSS technology has been used as a process revamp improvement as well as a technology upgrade to address coke formation.
UOP’s design methods include several considerations and features which have dramatically reduced the incidents of severe erosion of internal components over time. Internals are designed with appropriate orientation and velocities to minimize erosion potential in critical areas such as cyclone inlets. UOP also specifies proven refractory and abrasion resistant lining materials in these areas which often survive a run with only small sections requiring repair. Utilizing these design methods, VSS technology offers improved mechanical reliability of the reactor internals, improved unit availability, and reduced maintenance costs over RTD alternatives. Also contributing to the high mechanical reliability of the technology is the fact that over 95% of the catalyst separation occurs in the low velocity, VSS chamber – meaning that less than 5% of the catalyst will enter the higher velocity cyclones. There are multiple refiners with UOP’s latest VSS technology that achieve 99+% on-stream efficiency with minimal maintenance required to internals following a 5+ year campaign.