Question 50: What are the technology evaluations and engineering studies required for revamping a diesel hydrotreating unit to substantially increase throughput?
LIOLIOS (DuPont Clean Technologies)
In any major revamp of throughput for a DHT (distillate hydrotreater), establishing a realistic design basis and engineering certainly never really exists. The idea is to look not just to the point but at deviations and feedstock properties, expected changes in compositions, and past history of contaminants. Evaluation of the reactors in the high-pressure loop is where we tend to do a concentrated effort because there is a lot of give-and-take on cycle life versus temperatures to accomplish the objectives of a particular throughput increase in the revamp. Obviously, we have to look at liquid and space velocity, catalyst selection, and hydrogen availability.
We have been successful revamping a couple of DHTs by adding liquid hydrotreating reactors, either adding or revamping series reactors by putting a liquid reactor in front. In one case, converting a trickle bed to a liquid reactor had some substantial advantages without significant changes in the stripping or fractionation areas. It is a great way to get a revamp. It not only increased capacity; but in some cases, you will be able to get to the lower sulfur in the product.
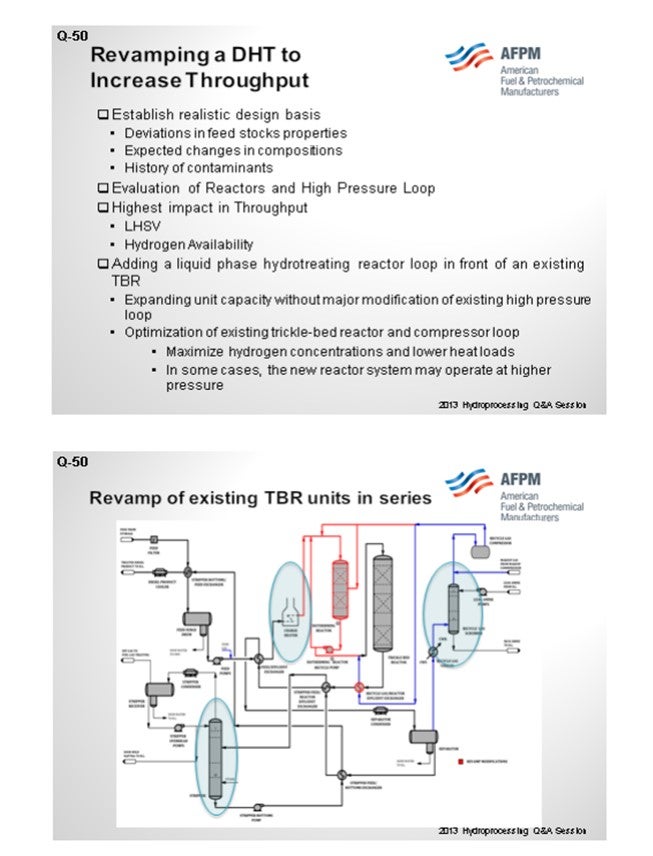
SHARPE (Flint Hills Resources, LP)
If your charge feeds are limited, especially for end-of-run conditions or with no cracked stocks in the feed, the feed effluent train can be upgraded for additional heat recovery. You have to give careful consideration to doing that to avoid dropping the downstream hot high-pressure separator below the salt deposition temperature. If the hot high-pressure separator gets too cold, the salts can partition to the liquid phase and end up in your downstream fractionation equipment causing fouling, plugging, or corrosion issues. I have referenced API 932B for you to review the guidelines. If your hot high-pressure separator is too cold, you can put a cold feed bypass around the exchangers to help control the temperature. Obviously, it will not work if your charge feed is limited. In our Eagle Ford crude cases, we are running cold on the reactor circuit, in general, and then putting a cold feed bypass, which will help control your hot high-pressure separator temperature. In that case, make sure you design your mixing point very carefully to avoid thermal fatigue issues. API 570 and 571 have some guidelines on proper design.
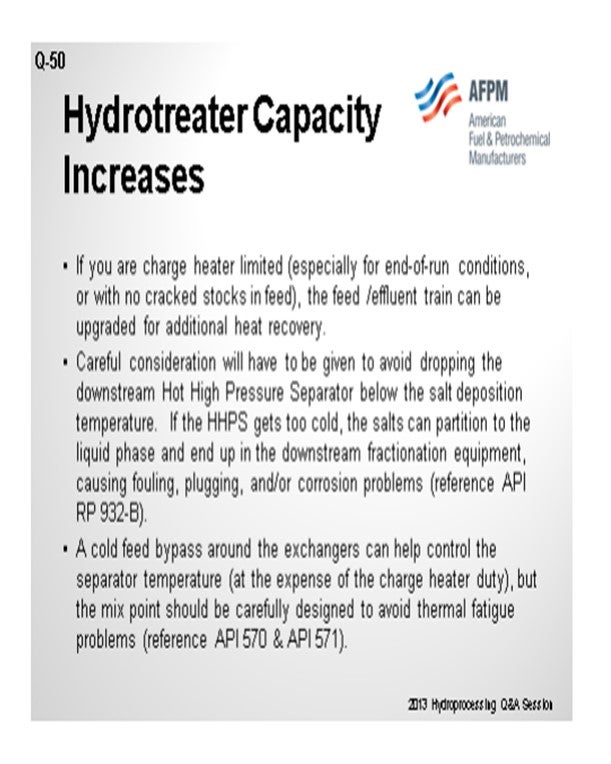
Other envelope issues to consider: Your waterwash systems need to be evaluated and revised to provide adequate washwater capability. Water removal capabilities of the upstream charge drum and downstream equipment need to be evaluated to avoid reliability issues associated with corrosion or potential product quality issues. On ULSD revamps, the feed cutpoint has to be a major bearing on your sulfur species and, therefore, treating requirement reactor sizes. If you are not changing out the reactor, catalyst life and run-length penalties must be assessed. Potential vibration issues in exchangers, piping, thermal wells, and quills need to be evaluated due to changing velocities and flow regimes.
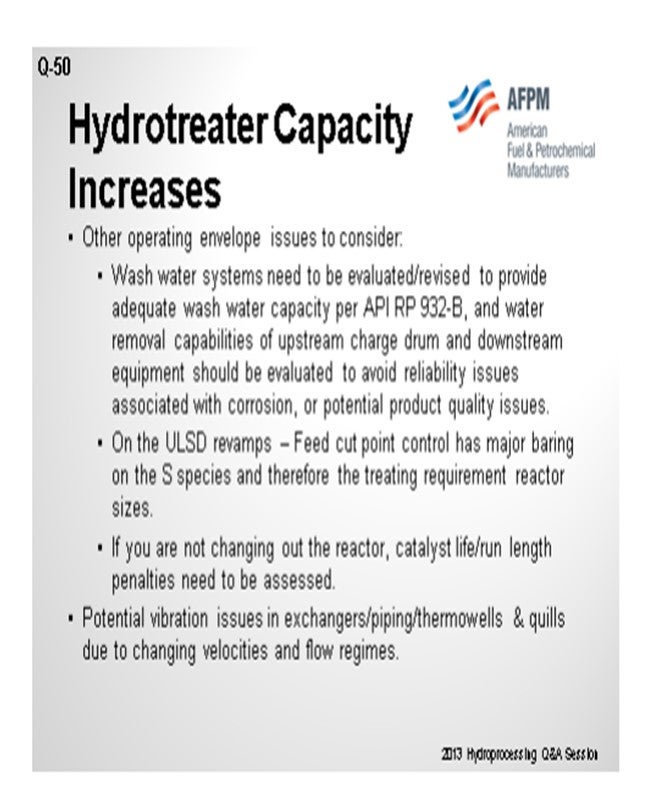
The fractionation capabilities need to be evaluated and will be very unit-specific, depending on your required product specs and fractionator heater capabilities. One of the big considerations is hydrogen system management and optimization for an upgrade on rate in optimizing catalyst life management. You need to look at what maximum catalyst axial ∆Ts (temperature differentials) are allowable, which will depend on your bed outlet hydrogen partial pressure. You also must ensure that there is enough emergency reserve quench available for feedstock variations and unit perturbations and upsets. That is important, especially if you will be running more cracked stocks with your revamp. By the same token, quench valve capacity testing and availability are important for sizing basis. Hydrogen uptake for bed and hydrogen partial pressure limits of the bed outlets, both for catalyst light management and potential ∆P problems, needs to be evaluated. That is important from your emergency reserve quench as well.
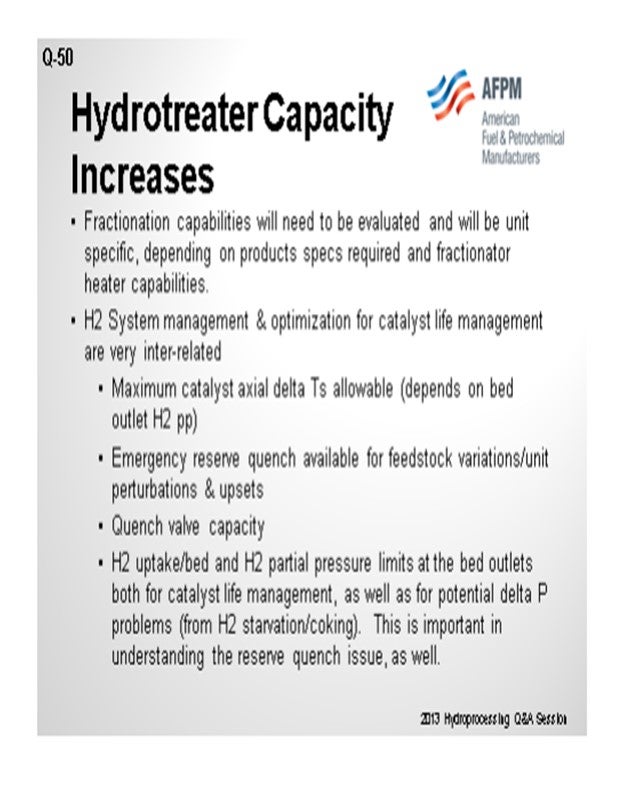
R.E. “ED” PALMER (Wood Group Mustang, Inc.)
One of the biggest issues on a revamp is the mechanical design conditions of the entire reactor loop; because once you push capacity, the whole pressure outlet system goes up. The other point is really the upset pressure on the separator drum.
I want to make another comment. On any revamp study, we like to see a good set of operating data before we do a process simulation of the whole unit based on the data, including a really good reactor loop hydraulic profile to understand the real equipment and piping pressure drops versus the target pressure drops
JEFF JOHNS (Chevron Products Company)
I agree with a lot of the points that were shared. One of the most neglected considerations I have seen most recently has been the relief system. One of the easiest ways to get more feed through a hydroprocessing unit is to increase the size of letdown valves from the separator, but a lot of people forget to then evaluate the relief capacity downstream for a potential blow-through case. That omission has caused serious incidents within the industry.
GATES (Motiva Enterprises LLC)
I also want to add that as you are increasing unit charge rates, you are likely changing the operator response times to unit upset conditions. So, it is probably a good idea to take a quick look at the PHA (Process Hazard Analysis) and reevaluate to confirm that there were no sudden changes in operator responses to emergency conditions.
HELMY ANDRAWIS (WorleyParsons)
We get a chance to revamp quite a few hydrotreaters. Most of them are 30 to 40 years old, so certainly design pressure and temperatures on relief systems. For quite some time, we have seen many units pushed beyond their design limits and throughput.
I also want to make a comment about inspection reports. We take for granted that some of this equipment is good. We have had quite a few experiences where the inspection reports did not quite reflect the exact conditions of the units.
SHARPE (Flint Hills Resources, LP)
That is a very good point about the PSV (pressure safety valve) of a blow-through case. When reviewing a blow-through case, you need to look not just for liquid and hydrogen together, but also for hydrogen only. Frequently, a hydrogen-only blow-through case will set your downstream and relief valve pressure rating and sizing basis.
XIOMARA PRICE (GE Water & Process Technologies)
I agree with the waterwash revamp and making sure it is adequate because a little waterwash can be worse than no waterwash at all in your system. In addition, when revamping your unit, make sure that the filters are in front of the unit so that:
1) the throughput you have is continuous,
2) you are not fouling the system, and
3) you are able to maximize your throughput.
One other area that tends to get neglected is that you have not designed the unit to have problems; but when you do, to have the right-sized valves to put in the chemistries that you may need to address the problems. It is quite important to think about injection points when designing your systems.
JOHN PRICE (WorleyParsons)
Another consideration that is often overlooked is the assessment of cooling capabilities with revamps. Reviewing the cooling tower’s designed hydraulic and cooling capability and/or the air fin cooler’s design as compared with the current operating performance is typically neglected in the early stages of an engineering effort for expanding hydrotreating units.
GLENN LIOLIOS (DuPont Clean Technologies)
The first step in any revamp analysis is to establish a realistic design basis with careful consideration to sensitivity of changes in feed stream properties, composition, and contaminants. We generally start by evaluating the reactors and the high-pressure loop as these two systems are typically the major limitation. For most systems, the reactor space velocity and hydrogen availability limit high throughput increase.
Considering liquid-phase hydrotreating technology can provide a unique solution. Adding a reaction loop upstream of the existing trickle bed can provide great capacity increase capabilities. This allows for expanding the unit capacity without having to modify the existing high-pressure loop as the hydrogen is carried by a liquid recycle. By moving part of the hydroprocessing load to the new reactor system, the trickle bed reactor and compressor loop can be optimized to maximize high hydrogen concentrations and lower heat loads. In some cases, it is possible to design the new reactor system to operate at higher pressure, thereby allowing additional optimization of the new purposed trickle bed reactor.
If the existing trickle bed unit has two reactors in series, revamping the first reactor to liquid phase technology has also shown substantial capacity increases with much lower capital investment than other options.
As with all revamp studies, the aforementioned work is evaluated several times to make sure that the capital optimization and operability meet the project threshold. There are always tradeoffs, and this re-evaluation is a critical step to maximize the benefits based on the constraints of the existing unit.
Next, we evaluate the heat integration and the fractionation equipment. Finally, we evaluate the product rundown system and safety valves. A thorough evaluation will also include a review and potential upgrade of existing reactor internals to state-of-the-art internals.
Other items that may need to be considered are amine absorber, including amine type; catalyst options for higher activity; and, feed section, including charge heater.
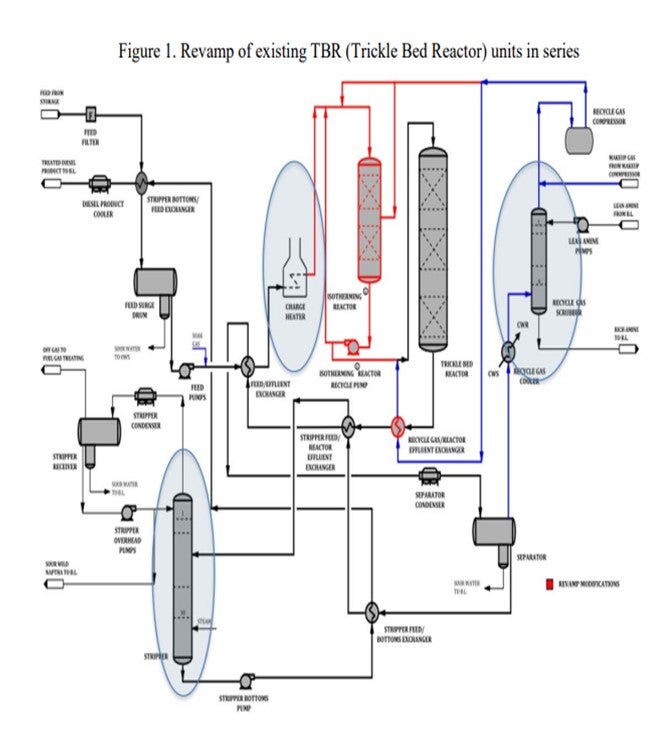
JESUS PEREZ (Alfa Laval Inc.)
A key study to perform is how to increase heat recovery without adding pressure drop on the diesel hydrotreater unit. Significant fuel savings in the fired heater can be achieved by minimizing the HAT (hot approach temperature), which is also known as ROT-HIT (reactor outlet temperature–heater inlet temperature) of the feed-effluent heat exchanger. The installation of a welded-plate heat exchanger can provide both higher heat recovery and lower pressure drop. Since the 1990s, Alfa Laval Packinox has commissioned 22 welded-plate heat exchangers in distillate hydrotreating applications all over the world with one more unit being delivered next year. For additional information on the subject, we suggest that you refer to Alfa Laval Packinox’s response to Question 23 from the 2008 NPRA Q&A. This question was, “What is your experience with and acceptance of high efficiency plate exchangers in high-pressure hydrotreating service?”
HOWARD WU (Haldor Topsøe, Inc.)
1) Kinetics are used to determine if the existing reactor would have enough catalyst volume to meet the process objective for the higher throughput. If it does not, then one may need to add an additional reactor or accept shorter cycle lengths. Topsøe has done many ULSD, CGO, and coker naphtha unit revamps. We have found that adding additional reactor volume is quite feasible and economical for refiners and allows the unit to operate at a lower gas-to-oil (G/O) ratio, thereby avoiding investment in a larger compressor. Topsøe offers Reactor Design Packages (RDPs) which are geared for the addition of reactors for refiners whose main bottlenecks were in catalyst volume.
2) Engineering is utilized to determine if existing equipment can handle the higher flow. With a higher throughput, the pressure drop will be higher in the system and the existing compressors, heaters, exchangers, vessels, towers, and pumps may no longer be adequate. Topsøe will provide refiners with a Revamp Process Design Package (Revamp PDP) or a Revamp Engineering Design Package (Revamp EDP) to simulate the whole unit and identify limitations of equipment. It includes development of new PFD with hydraulic analysis, heat integration, and process evaluation of vessels, rotating equipment, and towers.