Question 50: Butylene demand and prices in relation to other refined products reached a record level in 2017. What caused it and what can we do in the FCC to produce more butylenes?
TIFFANY CLARK (BASF)
Higher demand for butylene is result of octane shortage in the gasoline market stemming from several main causes.
First, the overall gasoline demand in the U.S. has surpassed previous record levels. Of this demand, there is a higher demand for premium-grade gasolines as a much higher percentage of new cars and light trucks now require higher octane gasoline due to higher compression engines. The percentage of premium grade gasoline has increased from 8% in 2010 to 12% today.
In addition, stricter fuel regulations, on sulfur levels, continue to be implemented globally. As Tier 3 gasoline standards are going into effect in the United States, refiners are striving to find ways to reduce the sulfur content of their gasoline pool to meet the 10-ppm requirement. China and Europe have implemented similar sulfur standards in 2017 and 2009, respectively. Compliance with these tighter sulfur requirements often leads to octane loss due to gasoline post treating.
Increasing amounts of tight oil that are being process now have also resulted in lower overall gasoline pool octane. Tight oil derived FCC feeds are typically light and paraffinic yielding gasoline that is also highly paraffinic with a low octane value.
While ethanol partially filled these gaps, other high-octane blending components, such as alkylates, need to be ramped up in order to meet the higher octane-barrel demand. Alkylate has become an even more preferred gasoline blending component in recent years, as it contains no sulfur, no olefins, no benzene, and has a low vapor pressure and high-octane number.
As a result, many refiners are focusing on alkylate production for profit maximization, and hence the desire for butylenes has increased. The fuels market accounts for 81.5% of total world consumption of butylenes with 43% of globally produced butylenes going into making high octane blending components via Alkylation units. With long-term global fuel demand expected to continue to favor clean, low-sulfur fuels and increasing use of high compression engines requiring higher octane gasoline, increasing selectivity for butylene will likely continue to be preferred.
In the FCC, butylene yield can be increased a few ways. Increasing conversion by raising riser outlet temperature will increase butylene yield. However, increasing riser outlet temperature can also raise dry gas and reduce LCO yield, which is not an ideal scenario for a refiner who is WGC limited or has a high LCO value. Since FCC’s account for approximately half of world’s butylenes production, ZSM-5 additives have been an obvious choice to meet the increase in butylene demand. While the other co-product from ZSM-5, propylene, also was highly favored in the past, its relative pricing has been subdued due to proliferation of propylene production from Propane DeHydrogenation (PDH) units. As such, butylene selective base catalyst and additives have become the tools of choice in recent years for FCCs to increase the relative production of butylenes.
SAEED ALALLOUSH (Saudi Aramco)
Butylene production can be increased from FCC with using formulated catalyst, but it will be limited to some extent.
ANN BENOIT and KEN BRYDEN (W.R. Grace & Co.)
Increase in butylene price is most likely attributed to keeping the refinery alkylation unit full to produce high octane low sulfur gasoline blend stock to help in the era of tight oil processing and TIER 3 regulations. The lower fraction of 650°F+ material in tight oils compared to many other crudes tends to result in less FCC feedstock production from the crude distillation unit. The paraffinic nature of many tight oils results in lower FCC gasoline octane. Reduced FCC feed rate can cause alkylation units to run at lower rates while the lower FCC octane reduces overall octane in the refinery. It has become more important for refiners to keep the alkylation unit full so that it can produce a high octane, lower sulfur blend component to help meet octane and TIER 3 requirements. Since C4 olefins are the preferred feedstock for alkylation units, refiners are looking at ways to produce more from the FCC. The answer will first address the formation mechanism of C4 olefins and then discuss how to increase the C4 olefin production by the FCCU. Feedstock, operating conditions, catalyst effects and the role they play in C4 olefin production will be discussed afterwards.
To maximize C4 olefins in the FCCU, one first needs to understand the mechanism of their formation. Figure 1 summarizes the fundamentals of butylene selectivity and maximization. The cracking pathways involved can be thought of as four stages. In Figure 1, the desired pathway for maximizing butylene is depicted with green arrows and the undesired pathways with red arrows. The first stage is cracking of the feed to naphtha range olefins. These cracking reactions can occur on zeolite or on matrix surfaces. In the second stage, these naphtha range olefins can further react to form naphtha range paraffins by hydrogen transfer (an undesired pathway), or crack to form C3 and C4 olefins. The rate of cracking of gasoline range olefins to C3 and C4 olefins is faster and more selective on ZSM-5 zeolite than Y-zeolite. The C3 and C4 olefins that are produced in stage 3 can further form propane, iso-butane and butane (via H-transfer reactions), which are undesired when maximizing butylene. These H-transfer reactions occur much faster on zeolite than on matrix. Based on this fundamental reaction scheme, butylene can be maximized by decreasing the hydrogen transfer activity and by minimizing the cracking of naphtha olefins to propylene.
Figure 1. Butylene maximization and selectivity fundamentals.
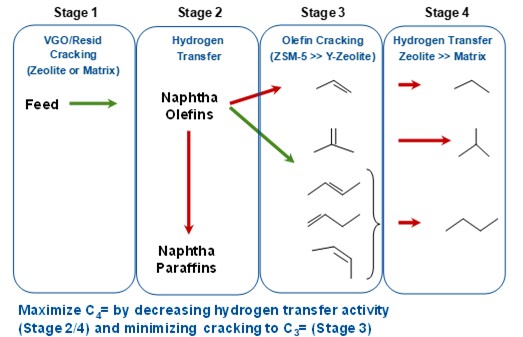
Feedstock Effects:
Even though feedstock is typically not a controlled variable for refinery process engineers, it does impact butylene production and thus warrants a brief discussion. The chemical nature of the starting feedstock will affect its reaction products. As a feed becomes more aromatic, the olefinicity of the LPG stream will drop (Reference 1). As a feedstock becomes more naphthenic, LPG olefin production drops. This is because naphthenes are good hydrogen donors and react with gasoline range olefins to form aromatics and gasoline range paraffins (Reference 2). Since gasoline range olefins are the precursors to LPG olefins, this depletes the pool of available precursor molecules required to form LPG olefins and reduces LPG olefinicity.
Operating Condition Effects:
Typically, total C4 production depends on conversion, regardless of whether the conversion is achieved by reactor temperature or catalyst to oil ratio (Reference 3). Figure 2 shows data from a Grace DCR™ pilot plant study that demonstrates the relationship between total C4s and conversion. As conversion increases the total C4s will increase which, in turn, can increase butylene yield. One thing to note is that that the ratio of isobutane to butylene is strongly influenced by reactor temperature. Since hydrogen transfer has higher activation energy than cracking, the rate of cracking increases faster with temperature than the rate of hydrogen transfer (Reference 4). Thus, as reactor temperature increases, the ratio of iC4/C4= decreases.
Figure 2. Relationship between conversion and total C4s.
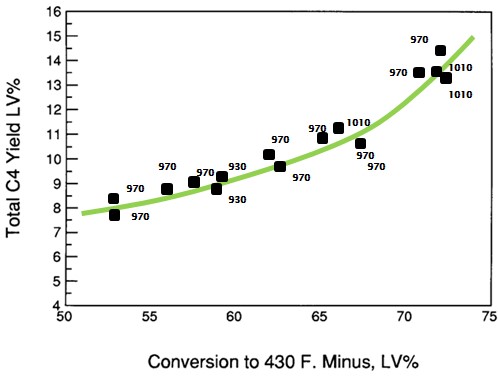
Catalyst Effects
The base catalyst can be reformulated to increase butylene by reducing the rate of hydrogen transfer. Reducing hydrogen transfer can be done by lowering the rare-earth on zeolite or by adjusting the zeolite/matrix ratio. Lowering the zeolite/matrix ratio of the base catalyst will increase the gasoline range olefins and thus the amount of butylene produced from these precursors. This is a consequence of the lower intrinsic hydrogen transfer activity on matrix surfaces relative to that on zeolite surfaces.
ZSM-5 based additives also increase butylene production. ZSM-5 cracks the C6+ gasoline range olefins to propylene and butylene. Figure 3 shows the effect of ZSM-5 on the olefin's distribution. Adding ZSM-5 additive will consume gasoline range olefins and produce both propylene and butylene. The increased propylene yield with ZSM-5 additives is not always desirable. There are specific catalysts and additives that are tailored to increase butylene yield in the FCC. Grace’s butylene selective catalyst (ACHIEVE® 400) is formulated with dual zeolites with tailored acidity to deliver an optimum level of butylene to keep the alkylation unit full and maintain refinery pool octane. With traditional ZSM-5 technology, cracking of gasoline olefins extends beyond C7s and into C6s and thus generates a disproportionate amount of propylene relative to butylene (Figure 4). The dual-zeolite technology works synergistically with a high diffusivity matrix to selectively enhance olefinicity, preferentially cracking C7 and above gasoline olefins into butylene. The result is a higher ratio of C4 to C3 olefin yield than traditional light olefins additives. Figure 5 illustrates the butylene selectivity improvement of this catalyst compared to a system using conventional ZSM-5 based additive (Reference 5). In addition to increasing butylene selectivity, the catalyst also increases octane of FCC naphtha.
Figure 3. Effect of ZSM-5 additive on olefins distribution (from Reference 4).
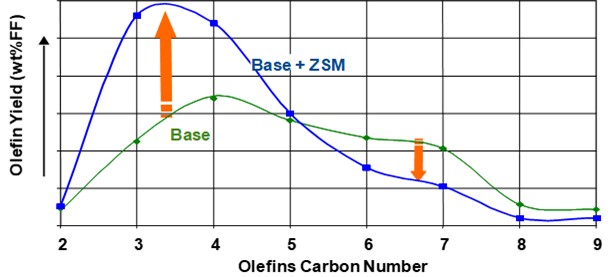
Figure 4. Selectivity from cracking gasoline range olefins over ZSM-5 additive and ACHIEVE® 400 Catalyst.
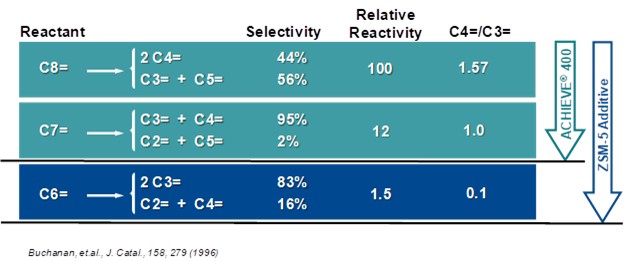
Figure 5. Butylene selectivity improvement of ACHIEVE® 400 catalyst compared to a system using conventional ZSM-5 based additive.
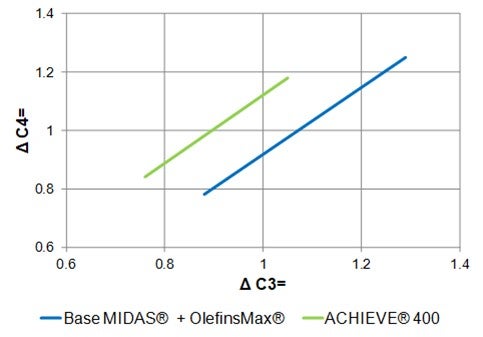
Similarly, there are butylene selective FCC additives that allow refiners to achieve a higher butylene to propylene ratio than that obtained with traditional light olefin additives. This allows refiners to increase their butylene yields from the FCC without committing to a full-fledged FCC catalyst reformulation. Figure 6 shows the results from an ACE™ evaluation comparing Grace’s butylene selective additive (GBA™) to conventional light olefin additives. Results show at increasing additive use both types of additives increase total LPG olefins. However, GBA™ achieves both a higher butylene-to-propylene ratio and a higher boost to FCC gasoline RON compared to the traditional ZSM5 additive. The increased octane is driven by improved isomerization activity.
Figure 6. ACE® Evaluation of Grace’s GBA™ additive vs. conventional light olefin additives
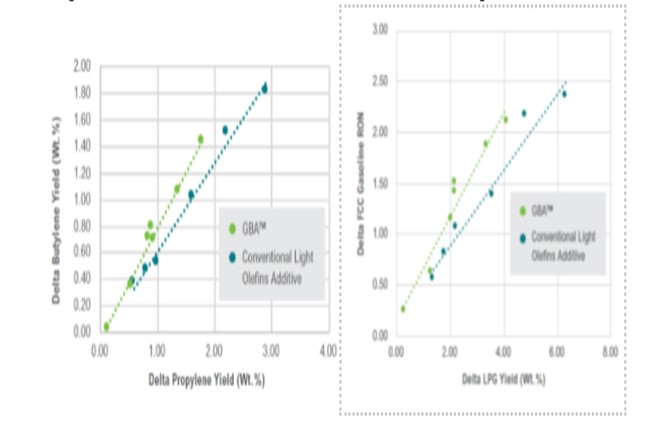
In summary, increasing butylene can be achieved by changing feedstock, operating conditions, catalyst reformulation, or additive use. Proper choice of catalysts and additives based on operating objectives and unit constraints is critical in maximizing butylene selectivity. Grace’s technical service team has the experience and resources to help refiners evaluate feed, operating condition and catalyst shifts to maximize butylene selectivity.
References:
(1) Harding, R. H.; Zhao, X.; Qian, K.; Rajagopalan, K.; Cheng, W.-C., “Fluid Catalytic Cracking Selectivities of Gas Oil Boiling Point and Hydrocarbon Fractions,” Industrial & Engineering Chemistry Research 1996, 35, 2561.
(2) Zhao, X.; Harding, R. H., “ZSM-5 Additive in Fluid Catalytic Cracking. 2. Effect of Hydrogen Transfer Characteristics of the Base Cracking Catalysts and Feedstocks,” Industrial & Engineering Chemistry Research 1999, 38, 3854.
(3) Grace Guide to Fluid Catalytic Cracking, Chapter 6, FCC Operation.
(4) Zhao, X.; Roberie, T. G., “ZSM-5 Additive in Fluid Catalytic Cracking. 1. Effect of Additive Level and Temperature on Light Olefins and Gasoline Olefins,” Industrial & Engineering Chemistry Research 1999, 38, 3847.
(5) Bryden, K.; Federspiel, M.; Habib, E.T.; Schiller, R., “Processing Tight Oils in FCC: Issues, Opportunities and Flexible Catalytic Solutions,” AM-14-16, 2014 AFPM Annual Meeting, March 2014, Orlando, FL.
HEATHER BLAIR (Johnson Matthey)
With tier 3 gasoline starting to kick in at many refineries in 2017 octane loss increased across post FCC finishing units to meet low sulfur demands. Butylene remains the best alky feed for high octane and therefore butylene economics became even more valuable to increase or maintain overall gasoline pools.
There are a few options in the FCC that help increase butylene yield. The best and most economical option is often the use of an additive such as butylene selective ZSM 5 (ZMX) that cracks gasoline range molecules into smaller olefins for alky feed. By doing this the octane losses from post treating units are lessened while simultaneously increasing alky feed and boosting gasoline pool octane.
MATTHEW WOJTOWICZ (UOP)
Worldwide demand for butylenes has been increasing since a low point in demand in 2008-2010. Between 2013 and 2017, the worldwide consumption of butylenes grew at a rate of 3.2% (Compound Annual Growth Rate or CAGR). The consumption of butylenes is also expected to grow into the future – the worldwide consumption is expected to grow at a rate of 2.8% (CAGR) between 2017 and 2022. A similar situation is expected in the United States (US) with a butylene consumption growth rate of 2.7% (CAGR) between 2017 and 2022.
Butylenes are consumed in fuels and chemicals applications. In 2017 the worldwide consumption of butylenes as fuels was 82% of the total consumption (the remaining 18% was used in chemical applications). In the US, the 2017 consumption of butylenes as fuels was 87% of total the consumption (the remaining 13% was used in chemical applications). Clearly, the fuels application is the leading use of butylenes worldwide and in the US – they are used to produce high quality gasoline blend components – namely, alkylate, MTBE and ETBE.
The worldwide consumption of butylenes as fuels grew at a rate of 3.6% (CAGR) between 2013 and 2017, and it is expected to continue to grow into the future at a rate of 2.4% (CAGR) between 2017 and 2022.
Source IHS Markit data.