Question 5: What is the panel's experience with hydrotreater fouling/poisoning issues arising from processing synthetic or bitumen-derived crudes? How can the impact be mitigated?
BODOLUS (CVR Energy)
This question is directed more at the bitumen-derived type of crudes. I call all of them mined crudes from tar sand sources. We process a lot of these materials at our two refineries. The crude goes under the name of Western Canadian Select, which oftentimes is not very select. Next, I want to review the categories of contaminants. You can have the elemental poisons, arsenic, and phosphorus. Typically, they are associated with the origins of the heavy oil deposit, or perhaps they are introduced during processing or transport to the refinery. We have run across organic bound chlorides. Of course, you will have some silicon contamination if some of the material was coked up north and produced naphtha where you have the silicon liability. Iron and other metals can be present in the oil, again, either introduced during processing or as part of the original deposits. One interesting situation I alluded to in a few of the other questions is that the mineral contaminant, and the clays associated with these mined tar sands, are suspended by chelating hydrocarbons. As you hydroprocess those tar sands, you remove the stability of the chelating agents, and the clays may indeed deposit on you.
I think the question before was targeted at the next issue; that is, the refractory chemical compounds that are left behind. If these compounds have been processed before, then all that is left are the tough guys. I know that over the years, there has been a lot of emphasis put on the hindered aromatic sulfur compounds, dibenzothiophenes, and hindered dibenzothiophenes. As analytical techniques improved and you were able to look at these trace compounds a little better, we also found some nasty nitrogen-based compounds. These are similar, but they are nitrogen analogs to the dibenzo family. There is the five-membered nitrogen carbazole, and then there is a six-membered nitrogen acridine family. All of these boils between the range of 650°F and 700ºF. They are very intractable compounds. Note that the acridine shown on the right side of the slide does have an unshared nitrogen pair that goes after the metal centers, which can really tie up your catalyst.
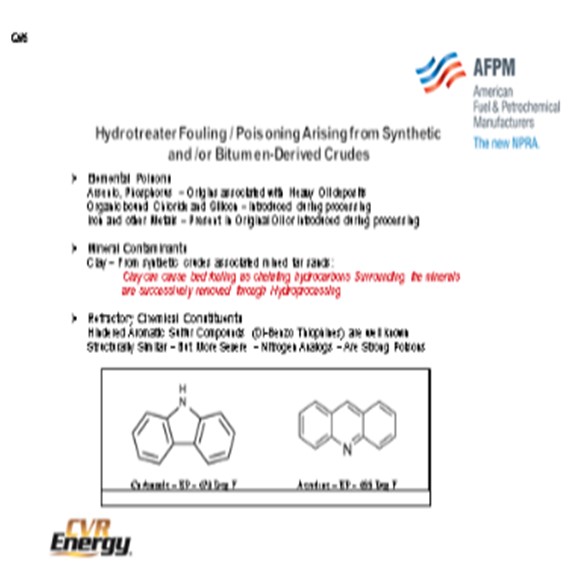
As far as mitigation methods, I would like you to keep this mantra in mind: Treatment without proper diagnosis is malpractice. Typically, that is associated with doctors; perhaps, less likely associated with lawyers, but I feel that engineers also need to practice this mantra. So, unless you really know your poison, you will not be able to deal with it effectively.
In the mitigation plan, of course, you can always try to abate the problem externally. Avoid that crude or those particular types of materials in your refinery. If you cannot avoid them, then go about possibly removing them at an upstream unit through desalting or filtration. Then as another option, perhaps you could chemically neutralize it if you are dealing with a chemical compound.
As the fallback position during a turnaround, it is very important to meet with your catalyst vendor and stack the bed in your favor. There are many different poison guards availableto do that including silicon traps, arsenic guards, metal traps, and asphaltene destruction-type catalysts. Talk to your catalyst vendors because they will have a list of these guards that you can evaluate. So it is very important to strategically grade your bed for both activity and contaminant capture. Again, catalyst selection is important further down in the bed for dealing with the tougher actors.
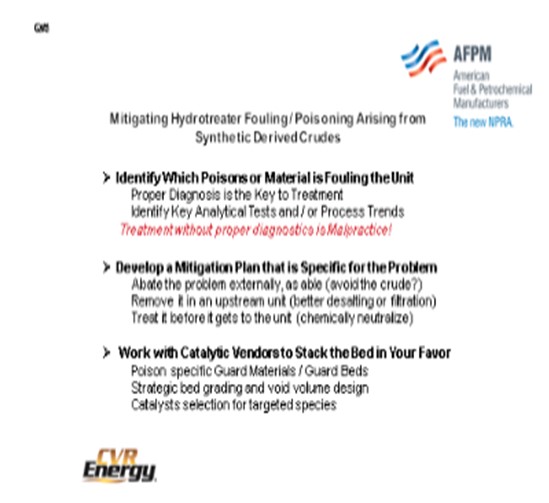
ESTEBAN (Suncor Energy, Inc.)
For obvious reasons, at Suncor Energy, I had access to several folks who have a great deal of experience processing synthetic crudes. We have found that a typical issue in our units is feed filtration, and we continue to struggle with it. However, good feed filtration at the 15μ (micron) to 20μ range helps prevent fouling and then, obviously, bed grading and trap catalyst.Trap catalyst targeting arsenic and silicon is used because those are the typical compounds we find to be issues. Inter-bed grading, if required, can also prevent some of the pressure drop built across the reactor.
The other key point Chris mentioned is that the synthetic crudes can often be deceiving because they may look like they have low sulfur content. But in reality, you are left with all of the difficult sulfurs. So, I would recommend pilot testing, if you are considering synthetic crudes, just to ensure that you have the appropriate activity required in your reactor.
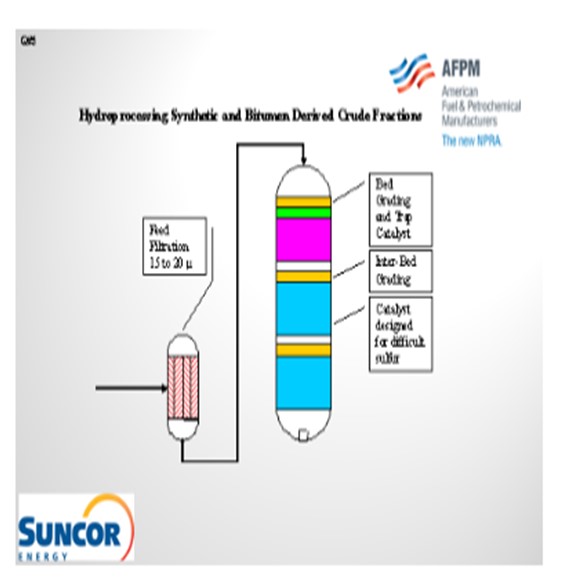
OHMES (KBC Advanced Technologies, Inc.)
I have a couple other points about some of the contaminants. In addition to what Chris covered, we have been hearing about titanium and, in some cases, mercury. At the Annual Meeting this year, there was a really good paper and presentation on mercury. It is one of those issues where you need to be a little more eyes-wide-open about what might be coming into the plant now as you bring in these crudes. As some people have been saying, it depends on what you are getting.
This slide shows a simple graphical representation of the upgrading process. If you are getting the synthetic crudes, again, the properties can be deceptive. You think you are getting low sulfur/low nitrogen feedstock, but these materials have typically been highly processed already such that the remaining contaminants are difficult to remove. It also really depends on what else might be blended with it if you are getting synbit or dilbit. Most people are aware of the blends they are buying, but it should be monitored.
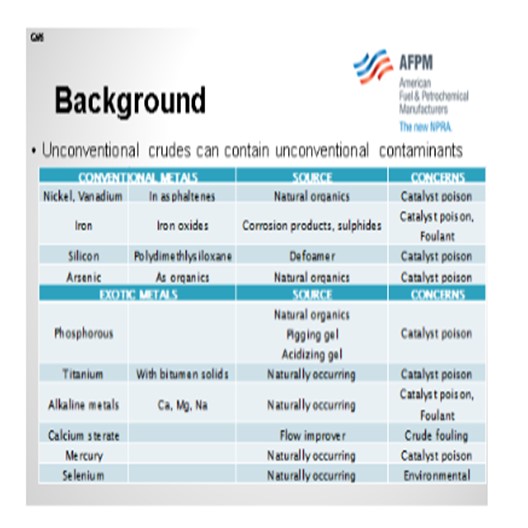
I know we talked about the Canadian crudes, but there are also the Venezuelan upgraders. We have had clients processing that material and seeing wide variations, depending on how the upgraders are performing. For instance, if the upgraders are having maintenance issues, the crude buyers may go from receiving no-bottoms crude to having a lot of bitumen in the purchased crude.
Another issue to mention is exchanger fouling. Again, people are seeing this problem in the crude vacuum units. Proactive crude quality tracking is an area where refiners have been lulled into complacency and are not actively completing. But with the new crudes being brought in, you want to make sure you have a good understanding of what you are getting. Particularly for those who are either processing this material or shale crudes, crude buyers are asking – upfront and in advance – about some of the completion chemicals being used by the upstream companies. This way, they will be able to set some limits in the crude that they may be getting and have an understanding of what is coming down the pipe in order to plan for it.
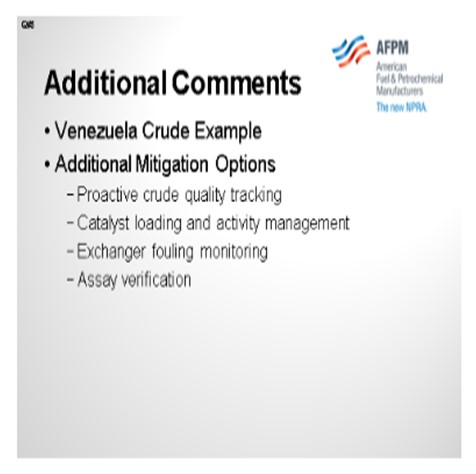
KEVIN PROOPS (Solomon Associates)
James, you mentioned filtering the reactor feed. Are you using cartridge or backflush-type filters? If it is backflush, where are you sending the backflush material?
ESTEBAN (Suncor Energy, Inc.)
The answer is “yes” in all cases. At the Denver Refinery, that has been a struggle for us. We have cartridge filters. We have not been very successful at feed filtration, although we are continuing to work on it. In Edmonton, we have a backwash system. The backwash is sent as feed to the FCCU.
BODOLUS (CVR Energy)
Our facilities and historic lab have experience with both backflush and cartridge. We have good relationship with the cartridge vendor. An interesting tradeoff in the automatic backwash filters is that the problem often comes and goes without you knowing about it. What is interesting with the cartridge filtration is that if you start buying a lot of cartridges, management wants to know why. You can then deal with the problem, if it is intermittent. Both can work, if appropriately applied. I have had experience with both, but filtration is key. On some of our units, we have had up to a six-year run. You cannot get there without filtration.
DAN WEBB (Western Refining)
Synthetic crude is a full boiling range material. If it is not, would you say that it is susceptible to polymerization? Do you have to keep it oxygen-free when you are handling it?
ESTEBAN (Suncor Energy, Inc.)
The crude itself?
DAN WEBB (Western Refining)
It is best to keep Lifecycle in a nitrogen-blanketed environment. Does it age when exposed to air?
ESTEBAN (Suncor Energy, Inc.)
Not that I know of.
OHMES (KBC Advanced Technologies, Inc.)
You blended in a lot of coker material, so all that polymerization material forms; but now, it is blended in with the crude, so to speak. We are not really seeing a lot of people nitrogen-blanketing their tanks. It is aged; it is formed; and now it can separate out differently. “What hurts you inside the plant” is actually a question we will cover later. The question asks about when you have olefin problems inside the refinery.
LEICHTY (Chevron USA, Inc.)
My experience is that the synthetic crudes in Canada are either derived from cokers, VGO hydrocrackers, or resid hydrocrackers. If derived from cokers, the products are almost always hydrotreated; and thus, no olefins should be present. As such, there should be no storage requirements that differ from conventional crude oils. Similarly, there are no special storage considerations required for synthetic crude oils derived from VGO and resid hydrocrackers since there should be no olefins present.
BODOLUS (CVR Energy)
Synthetic type crudes have a higher probability of containing elemental poisons such as arsenic, phosphorus, organic-bound chloride and silicon. Some of the contaminants track back to the original heavy oil deposits (arsenic and phosphorus) while other contaminants are introduced during the production of the synthetic crude (silicon and chlorides). For synthetic crudes associated mined tar sands, mineral contaminants such as clay can cause bed fouling as chelating hydrocarbons surrounding the minerals are successively removed through hydroprocessing.
The chemical constituents of the synthetic crude will include the residual “refractory” type compounds remaining from previous hydroprocessing. Synthetic crudes will have proportionally more aromatic sulfur and aromatic nitrogen compounds in the heavy ends of the distillate cut. By now, most synthetic crude consumers are familiar with how difficult the hindered dibenzothiophene is to process, but there are also nitrogen based analogs that can be even more challenging. The carbazole family represents the five-member nitrogen bound dibenzo aromatic compound while the acridine family is a six-member nitrogen bound dibenzo aromatic compound. Acridine is a more potent inhibitor of hydroprocessing than carbazol (C12H9N) due the basic character of the unshared pair of electrons in the aromatic plane.
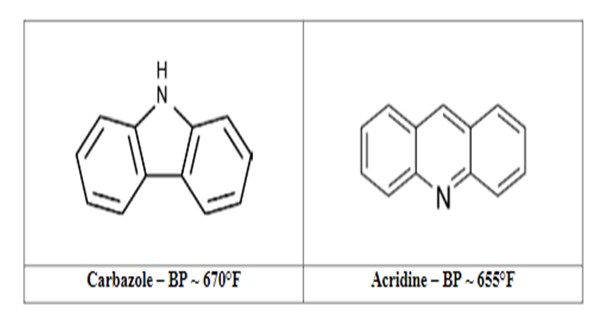
Mitigation needs to be targeted at the specific cause and addressed on a case-by-case basis. Proper diagnosis of the problem is the key to treatment. Confirm the presence of the poison or fouling component with analytical data or process information. For elemental chemical poisons, apply strategies to remove the contaminant in an upstream unit or obtain poison specific bed material in the reactor unit. For mineral based fouling in secondary beds, catalyst size selection may be helpful in increasing bed void volume. For refractory sulfur and nitrogen compounds seek catalytic solutions that will help optimize severity in the active reactor beds.
ESTEBAN (Suncor Energy, Inc.)
There are several challenges with processing synthetic or bitumen-derived crudes. Fouling issues are typically a result of problems in upstream units and poor feed filtration. Good feed filters and installing a graded bed system to trap out particulates will address the fouling issues. However, not all contaminates can be filtered and some materials can come out of solution with increased saturation as material is processed through the reactor which, if possible, can be mitigated by the use of graded material on the top of subsequent beds.
To mitigate poisoning of active catalyst, proper amounts of catalyst in the guard beds, ahead of the active catalyst beds is required for contaminant removal/capture of poisons. Suncor’s experience has identified the main poisons to be nickel, vanadium, arsenic, and silicon. The initial challenge with such feeds is the measurement of the concentration of poisons. Suncor has found arsenic and silicon concentration to be especially challenging as outside lab results widely vary and some are in error by a factor as high as 10. It is our practice to have samples processed by several independent labs to confirm results and analyze spent catalyst for metals loading. The following discussion describes the effects and potential solutions for feed streams with these poisons: Arsenic is present in the bitumen-derived crude in the form of alkyl-arsenic compounds.
Arsenic interacts more strongly with nickel than other metals used in hydrotreating catalysts. Consequently, it has a severe poisoning effect on NiMo (nickel molybdenum) catalysts. Arsenic (As) reacts with nickel to form nickel arsenide (NiAs). Based on this stoichiometry, a nickel-based arsenic trap can theoretically pick up about 1.28 wt% As for each 1 wt% Ni on the catalyst. The actual capacity will depend on process conditions (in particular temperature) and the concentration of arsenic in the feed. Arsenic is a permanent poison, so it is not removed via regeneration or other means. Arsenic has an affinity for Ni which provides an opportunity for efficient trapping. Arsenic trapping capacity of trap catalyst available generally varies from 2 wt% to 4%, but arsenic slippage to active catalyst can happen before the trap bed becomes fully saturated. Experience at our Edmonton refinery has shown that active NiMo catalyst can pick up ~1 wt% arsenic as well.
The typical source of silicon in these feed streams is Antifoam chemicals used in coker units which become highly concentrated in the naphtha cuts. However, upgraders and refiners have been known to try heavier anti foams to distribute silicon into distillate as well. Accurate measurement of the concentration of silicon in feed streams can be difficult and is often provided by our catalyst vendors. Silicon forms a chemical bond with the alumina surface and hinders access to the active sites. Suncor’s experience has demonstrated trap catalyst can usually uptake 6 wt% to 9 wt% silicon [sometimes reported as silica (SiO2) which would be double in wt%]. That being said, silicon uptake is highly temperature dependent and catalyst vendors can provide pickup information regarding performance specific to each unit.
Nickel and vanadium are typically a concern above 2 ppm (parts per million). These poisons are found in high concentrations in bitumen-derived feeds but usually end up in vacuum tower bottoms products. In order to prevent high concentrations of these metals in feed streams to hydroprocessing units, careful monitoring and control of vacuum gas oil endpoint is critical. Abnormal and improper vacuum tower operations can cause a spike in nickel and vanadium in product gas oil streams. Proper attention should be paid to wash oil grid operation and potential grid damage identified to prevent high endpoint material in the gas oil streams. As well, vacuum tower product streams should be properly managed during upset operating conditions to avoid contamination of downstream unit feed streams.
In addition to fouling and poison, mitigation often these feeds can be more difficult to treat than expected due to previous treating. While on the surface some synthetic feeds appear to be low in sulfur and easy to treat, they can be deceiving because they have been previously treated and the sulfur left in the streams is more difficult to remove requiring higher reactor temperatures. In order to properly predict the impact of such feeds on each specific unit, we recommend pilot testing be performed to provide reactor performance and life cycle predictions.
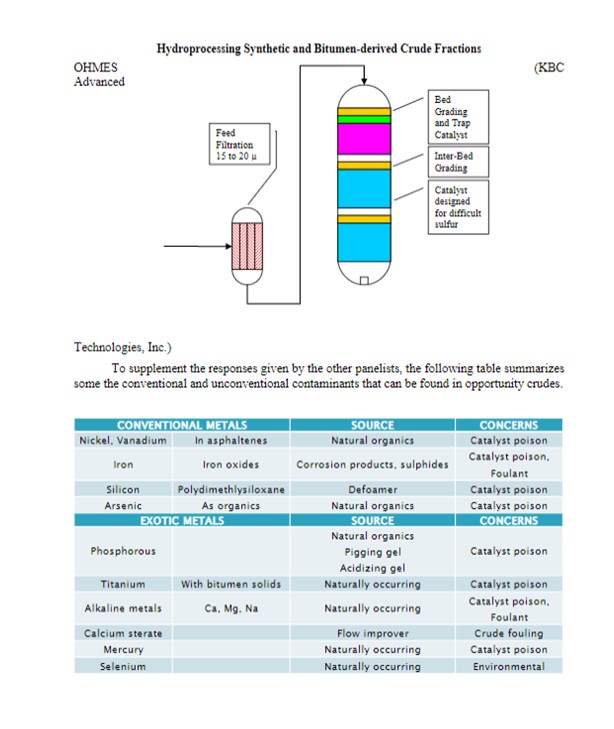
Several of the exotic contaminants are ones that most refiners do not typically track or follow. However, those refiners processing opportunity crudes have become more active in looking for these contaminants in their crudes and watching for the impact on downstream equipment. In addition, the level and “location” of said contaminants is strongly dependent on the source of the opportunity crude. The following simplistic graphic summarizes the different sources and production methods for unconventional crudes from upgraders.
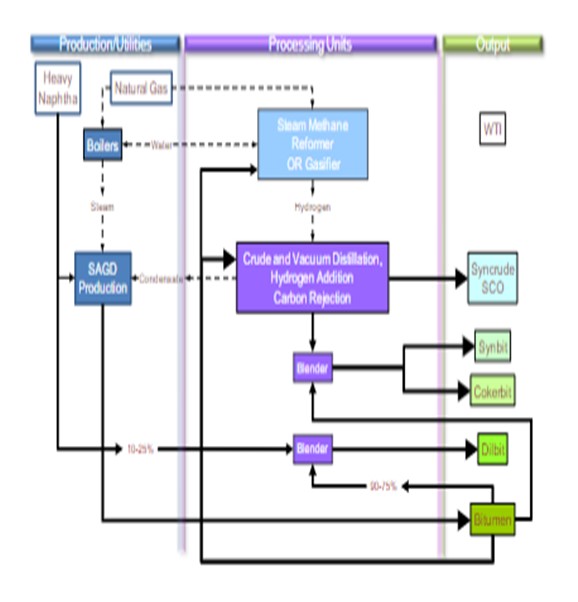
Therefore, understanding the source and production method provides valuable insight into the types of contaminants to expect and how these will impact the plant.
When discussing opportunity crudes, most think of Canadian synthetic crudes or shale oil crudes like Bakken and Eagle Ford. However, other crude sources exist and are processed in the industry. Venezuela has been running upgraders since the late 1990s and though their production levels continue to fall, refiners are still processing the material. Those processing Zuata crudes can confirm that the quality and cut range content vary substantially, depending on how the upgraders are being operated and how the agreements are arranged.
Some additional mitigation options are recommended:
•Those successfully processing opportunity crudes are actively monitoring crude quality, both on properties and cut range material content.
•Catalyst grading and activity tracking and management are more critical now than ever. Unconventional contaminants are highly poisonous to catalyst and can quickly deactivate catalyst.
•Exchanger fouling monitoring has now become more important than just understanding the impact on throughput and energy conservation. Exchanger monitoring packages, such as Petro-SIM™’s HX Monitor, are very useful in understanding how exchanger fouling is occurring in the facility, particularly when operating conditions and feedstock qualities are varying frequently.
•When planning and scheduling for these crudes, ensure the assays are representative of the actual material processed in the plant. While some discrepancy will always occur, having representative assays for various mixes, fields, and sources will help the refinery generate plans and operating schedules that are achievable and have sufficient flexibility to manage the natural swings and variations that occur.
BRUCE WRIGHT (Baker Hughes)
If the synthetic crude is fully hydrotreated, then few problems would occur, similar to a straight run hydrotreater feed. If the synthetic crude is only partially hydrotreated, or not hydrotreated at all, then polymer formation and deposition in the feed/effluent exchangers and reactor bed could be experienced. Baker Hughes LIFESPAN™ antioxidants, anti-polymerants, and antifoulants can effectively control polymer formation and fouling in both the feed-effluent exchangers and reactor bed.
HIROSHI TOSHIMA and STEVE MAYO (Albemarle Corporation)
Synthetic crudes from Canada, Venezuela, Urals, and elsewhere often involve inherent arsenic contamination. The effects of arsenic can be seen in all units processing synthetic feedstocks, but coker naphtha units are typically the most severely impacted. Arsenic has adverse effects on HDS (hydrodesulfurization) and HDN (hydrodenitrification) activity of hydrotreating catalyst. As little as 0.5 wt% arsenic can reduce HDS activity by 30% to 50%. Hence, it is important to protect the main bed catalyst of hydrotreaters experiencing arsenic contamination. Arsenic guard catalysts can be placed at the top of the reactor to contain arsenic penetration into the main catalyst bed for much of the cycle. These catalysts typically have high nickel content to which the arsenic is attracted.
Synthetic feedstock processed in delayed cokers produces lighter products containing, not only arsenic, but also silicon. Silicon deposition on arsenic trapping catalysts can severely impact the catalysts arsenic capacity since it covers the nickel site to which arsenic is attracted. Arsenic traps with high silicon capacity often show superior arsenic capture performance in these units.
GREG ROSINSKI, CHUCK OLSEN, and BRIAN WATKINS (Advanced Refining Technologies)
There is large variation in the quality and types of synthetic crudes, and there can be problems with trying to process many of them. In general, synthetic crudes can be classified into two basic types.
One is a blend of upgraded naphtha, distillate and gas oil range with no resid or bottoms material included. Fully upgraded synthetic crudes are more difficult to treat than might be expected from a typical feed characterization. The upgrading process typically includes several hydrotreating and hydrocracking steps, as well as coking processes to lighten up the material to make its flow characteristics easier to handle. The molecules left in the oil are the more refractory and difficult to remove species. The fractions that are pulled from the refinery’s crude processing units, however, typically have a high API along with the lower sulfur and nitrogen masking these difficulties. These crudes can also pose a difficulty with the presence of silicon which can be introduced from the coking process or through flow enhancers added after processing, and if left undetected will poison downstream hydrotreaters.
The other crude type utilizes the whole bitumen including bottoms which has been blended with other sweet synthetic or more conventional crudes. With synthetic crudes that do contain bottoms there can be significant problems with poisoning. Since these types of synthetic crudes contain bitumen they can have higher levels of Ni+V in the HVGO (heavy vacuum gas oil) compared to similar boiling range materials from conventional crude oils. This can be dealt with in the hydrotreater using an appropriately sized bed of demetallization catalysts, such as ICR132 and ICR161. Some of these crudes may also contain silicon, from upstream coking process and/or arsenic present in shale derived oils. In these cases, a combined silicon/arsenic guard such as AT734G from ART can be used to help mitigate the impact of these poisons.
Many of the synthetic crudes may also contain very fine particulates of clay or sand that are associated with asphaltenes or other heavy polycyclic molecules. These particulates can be removed through proper use of the desalter to avoid crude tower fouling. However, these small particulates typically <5 microns, when not properly removed, can pass through feed filters into the catalyst beds resulting in pressure drop issues. Often this pressure drop can occur is lower catalyst beds due to the denaturing effect of hydrotreating on the heavy molecules. The removal of sulfur, nitrogen, and aromatic saturation, as well as the heat and hydrogen present, can release the fine particulates further into the hydrotreater and cause them to precipitate out. Use of larger void spaced catalyst can help alleviate this problem to some level; however, we are not aware of anyone who has found a solution that completely alleviates this problem.