Question 5: Automobile manufacturers are considering requiring the use of higher-octane fuels in order to meet a mandated increase in Corporate Average Fuel Economy (CAFE) standards. What strategies might you employ should demand for higher octane gasolines increase?
KEADY (Technip USA)
I think this is a great question, and I found it very interesting to look into this. Over the years, gasoline and engine manufacturers have worked together to give us the type of cars we have now and the type of fuels we buy. There is a push to design the engines with higher compression, so that requires octane. So first you use technology, because that is my background. Of course, I am going to say that we need process design and technology to put in technology to take your straight chains and make them into branch chains to give you a higher octane. But another consideration is changing the octanes that we make available to the market.
A friend of mine took a picture of the petrol available in the UK, and I took a picture at a gas station near I-10 and Kirkwood where I work at Technip. In Europe, the standard is EN 228 with one gasoline octane. Now when you look at the pump, it says, “95 octane” and the other grade says, “97 octane”. So sometimes people say, “Oh, they have higher octane in Europe.” They do not have higher octane; they just report RON octane versus here in the U.S. where we have 87%, 89%, and 93%, which is an average of the RON and the MON octane.
What they were telling me there is that the lower-octane gas is available in the U.K., but they get to charge the same price as they do for the mid-range octane. The reasons are that no one uses it much anymore and because it is a niche market for those who have vehicles that still use the lower octane. Then of course, they provide 97%, which is in line with our higher-octane gas; so this is a possibility.
If you want to get rid of the naphtha which might have some of the lower-octane, you can always export it as olefin feedstock; that is, if you are in a location where this is available. Also you can reform coker naphtha, but you have to watch for RON loss there.
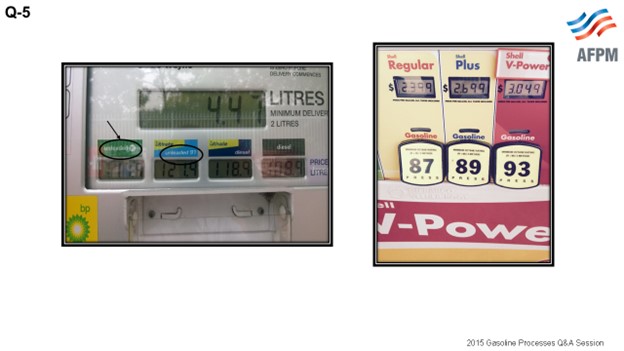
LAMBIE (KBC Advanced Technologies, Inc.)
From a fuel standpoint, higher octanes and increased miles per gallon do not necessarily go hand in hand. Two fuels can have the same octane but have different heat contents or BTUs (British thermal unit) per gallon and yield different miles-per-gallon performance. To increase the miles per gallon of the fuel itself, one needs to increase the heating value or heat content of the fuel. One strategy to increase the heat content of fuel is to increase severity/octane in reformers. The resulting higher aromatic content reformate will have a higher energy density; and hence, will provide improved fuel efficiency. Most reformers in the U.S. have the capability to increase reformer severity as they have been reduced as a result of the ethanol mandate. Alternatively, those refiners bypassing heavy naphtha to the gasoline pool can process the naphtha in the reformer to increase the heat content. One must consider increased benzene and aromatics production from increased reformer feed or severity to make sure the increases do not prevent meeting gasoline pool specifications.
Another strategy would be to consider the use of secondary biofuels, such as butanols. Butanols have a higher energy content, by approximately 30%, than ethanol and a lower oxygen content, which allows for blending about 12.5 vol% versus 10 vol% into the pool. In addition, butanols have a low RVP which allows for blending lighter, more volatile components. Butanol’s low water solubility would allow for blending the component at the refineries. Both increased reformate and butanols would contribute higher octane in miles per gallon to the fuel.
Some other areas to increase octane would be C5/C6 isomerization options, as long as the RVP is not limiting. There have been some recent developments in the C7 paraffin isomerization technology versus reforming, which “increased the yields and overall octane” of naphtha. That should be investigated for its merit.
Incremental alkylation capacity will continue to be very profitable.
MEL LARSON (KBC Advanced Technologies, Inc.)
One difference between the markets in Europe and the U.S. is that in the U.K., they actually have tailpipe testing. In the U.S., there is very limited actual tailpipe emissions testing. The manufacturer may show, via internal testing, that it has achieved the target CAFE standard using premium gasoline. But then, the consumer goes out and puts in regular gasoline. So as long as there is a price differential, one has to map out what the consumer will do, as opposed to the actual tailpipe emission spec. This will not have a big impact until every station, or every vehicle is checked annually for tailpipe emissions, and then we will be being driven to a certain fuel standard.
WARREN LETZSCH (Technip USA)
My experience in the past with Europe is that frequently European refiners were really motor octane-limited, not research-limited, in terms of blending their gasoline. For instance, if you could make more alkylate, it would be very, very helpful in Europe. So I would to like the ask the panel if any of you are seeing any C5 alkylation helping with vapor pressure and if there is possibly another way of being able to get lighter ends into gasoline pool. The other observation I have made is that it seems as if half of the reformers today seem to be running for hydrogen rather than for octane anyway. In fact, I did not really realize that you could run a CCR (circulating catalyst regenerations) unit in such a low octane number; and again, it seems like there is a lot of room there for things. I sure would like to hear your comments.
DUNHAM (UOP LLC, A Honeywell Company)
We have seen a lot of interest in C5 alkylation, particularly when crude prices were high and natural gas price was low and we were getting a lot of cheap isobutene on the market. That is a real economic driver for C5 alkylation. If you can get cheap isobutene, it makes sense to alkylate the C5. You get a little vapor pressure reduction. One of the factors in alkylating C5 is how much isopentene you make. There is a lot of hydrogen transfer and C5 olefin conversion to isopentene, and then you can consume more isobutene. People are starting to look at that option.
Just about the time we thought people were going to move into this, there was a little drawback on propylene economics; so people started alkylating propylene to fill their units instead of C5. However, we may get back in that situation where C5 is attractive, if they start selling propylene more and isobutene price stays low.
DOMINIC VARRAVETO (Burns & McDonnell)
I want to comment on the C5 alkylation issue that someone just brought up. We have worked with some customers who are looking at sulfuric acid C5 alkylation. Our experience is that there is no one out there doing this to a very great extent and that some of the operators will try to co-process, but the best results are achieved from a dedicated C5 alkylation arrangement. So co-processing is a compromise type of an opportunity; dedicated processing works better.
ERIC YE (DuPont Clean Technologies)
Even without potential regulatory increases in minimum octanes, in a low price gasoline environment, it seems clear that lower prices result in premium gasoline demand. As such, refiners should already be employing strategies to increase the production of high octane blendstocks. As with any strategy, the impact of any moves to increase the octane pool needs to consider the impact of modifications on the total refinery economic return. Such concerns include yield shifts to non-gasoline products, such as fuel gas and LPG; gasoline RVP constraints; butane containment; and if applicable, petrochemical operations, to name a few.
Excluding the increased use of ethanol, which is currently limited by the current E10 blendwall restrictions, some options a refiner may consider increasing the octane pool include:
-
Reducing the Volume of Low Octane Blendstocks: Straight run naphtha (SRN) is one of the lowest octane blendstocks in a refiner’s gasoline pool. Some refiners, particularly a number in overseas refineries, employee a strategy of cracking SRN in an FCC. While cracking SRN in the FCC reduces the amount of low octane naphtha available for gasoline blending, it also generates an increased volume of light olefins that can be alkylated to create a high octane and low RVP gasoline blendstock. With butane prices selling at significant discounts to gasoline, such an action could prove to be quite lucrative for the refiner provided that such an action does not adversely affect the refinery FCC or fuel gas balance.
-
Employing Isomerization: SRN can be isomerized to realize a 10-15 octane number improvement. However, the relatively high RVP of the isomerate (15 to 20 psia) restricts the volume of isomerate that can be blended into the gasoline pool. In addition, the upgrading process results in modest C5+ yield loss and an increase in LPG and fuel gas production.
-
Increasing Alkylate Capacity: If a refinery has light olefins (C3=, C4=, and C5=) available, consideration should be given to maximizing alkylate production. While C3 and C5 alkylation produces a product that is lower in octane than high-octane C4= alkylation, the alkylate still has an octane significantly above regular unleaded (RUL) gasoline. In addition, the low RVP of the alkylate allows a refiner to blend in high octane and high RVP blendstocks, such as butanes, to further boost the octane pool. For refiners with existing alkylation units, modifications to the configuration or operation of the alkylation unit can often generate 1 to 3 octane number improvements of the overall alkylate product. The modifications are specific to the type [HF or H2SO4 (sulfuric acid)] technology and the particular configuration, but some options for sulfuric acid alkylation units include external feed chillers, segregated contactors, or high efficiency bundles.
-
Increasing Reformer Severity: Increasing reformer severity is an option to increase the octane pool. However, such a strategy must take into account reduced C5+ yields and increased fuel gas and LPG production.
-
Hydrocracker Heart Cut: Most hydrocrackers have the ability to produce two separate gasoline boiling cuts: light heart cut and a heavy heart cut. The low aromatic content of these streams results in a blendstock that is relatively low in octane. The heavy heart cut normally possesses a high N+2A and thus produces a high-octane reformate with minimal C5+ yield loss and LPG/fuel gas production. Depending on the particular refinery option, the light heart cut could be directly blended into gasoline and the reformer supplemented with SRN that possess a higher N+2A.
SCOTT LAMBIE (KBC Advanced Technologies, Inc.)
C3/C4 Paraffins Processing: Dehydrogenation of paraffins and alkylation of the olefins produced will provide a premium quality, high-octane blendstock for the gasoline pool. Additional alkylation capacity would be needed to accommodate the increased olefin production. Alternatively, isobutane can be dehydrogenated to produce isooctene and then saturated to produce isooctane, if desired. This process produces a very high-octane gasoline blendstock.
Similarly, converting LPG to aromatics will produce a high octane, but highly aromatic product is a processing option. The benzene content would be very high and would need either extraction to produce a benzene product for sales or alkylation with a light olefin to produce a gasoline component. Again, the economics of producing gasoline via this route may be hard to justify.
C5/C6 Processing: Increasing light naphtha octane via isomerization technology has significant potential but comes at the expense of high RVP, which makes it difficult to blend into the gasoline pool.
There are a number of isomerization unit configurations that can increase the octane of light naphtha. A few options are as follows:
-
Adding a deisopentanizer on the light naphtha can add from 1 to 2 octane numbers to the combined isomerate, depending on light straight-run (LSR) iC5 content.
-
Recycle options, either mol sieve or a deisohexanizer (DIH), can increase product octanes to the upper 80s.
-
Super deisohexanizer to recycle nC5 to extinction, in addition to recycling nc6 and most methyl pentanes, can increase isomerate octane to the low 90s.
The increase in RVP may become problematic or prohibitive to light naphtha upgrading options.
Reforming: Many refineries have the ability to increase the feed rate to the reforming unit by reducing the amount of heavy naphtha sent directly to blending. In addition, many reformers have the capability to increase the severity or octane of reformate as well. This flexibility resulted from compliance with the ethanol mandate that increased the octane of the gasoline pool considerably. The combination of increased severity and throughput in the reformer helps increase the octane and heat content of the gasoline pool and, as a result, increases the fuel efficiency or miles per gallon.
Higher reformer throughputs and severities will result in increased aromatics and benzene production that will need to be managed in the gasoline pool. Additional technologies – such as extraction, saturation, or alkylation – may be necessary to reduce benzene levels to meet gasoline specifications.
C7 Processing: The merits of isomerizing C7 paraffins, as opposed to reforming, warrants investigation.
Alkylation: Many units today are at or near maximum capacity. Increasing I/O (isobutane/olefin) ratios will increase alkylate octane incrementally but will unlikely have a major impact on the pool octane. Refiners constrained on capacity may consider lower I/O ratios to accommodate more feed. However, this will come at the expense of lower octane. Refiners not constrained on capacity may consider alkylating propylene or amylenes; again, at the expense of octane. However, these feedstocks will compete with their alternate dispositions. In addition, the alkylation unit may need to be revamped to accommodate the propylene/propane and pentanes/amylenes feedstocks.
Additional alkylation capacity will continue to be very economical. The most likely source of olefin feedstock is an FCC unit, which would most likely require additional feed. This will be an economic decision based on crude selection and overall refinery economics.
FCC: Additional feed can yield additional olefins for alkylation units. The source of FCC feed will have to be rationalized with crude economics. Provided economics are positive, feed rate additions – and hence, olefins production increases –may coincide with alkylation capacity additions. Maximization of ZSM-5 to produce olefins for alkylation will have the added benefit of increasing FCC naphtha octane. The gasoline pool aromatics and benzene content need careful consideration.
sobutanol’s low blend RVP is a significant advantage versus ethanol as it would allow for blending more light naphtha, isomerate, or butane to the gasoline pool. The lower oxygen content would allow for blending up to 16.5% isobutanol while maintaining the same oxygen content in the gasoline pool as 10% ethanol. This increased volume results in increased octane to the pool overall, as well as doubles the RIN (renewable identification number) credits from 10 to 21.9 per gallon of gasoline. The ability to blend isobutanols at the refinery is another big advantage for refiners as this allows for minimizing giveaway in gasoline blends. Isobutanol’s energy content is approximately 17% higher than ethanol, which improves the average mpg (mile per gallon) of gasoline.
GINGER KEADY (Technip)
“The efficiency of gasoline engines depends on the octane number, but that’s not something that’s changed in quite a while,” says Raymond Speth, a research scientist in MIT’s (Massachusetts Institute of Technology’s) Department of Aeronautics and Astronautics. “If [manufacturers] know the gasoline is higher-octane, they can design engines to have a higher compression ratio, which would make the engine smaller and more efficient, both of which are a benefit.”1
Suggested strategies to provide higher octane gasoline are the following:
-
Use technology to create branched paraffins for higher octane blending components by sending most light straight-run and saturated gas naphtha to isomerization.
-
Base gasoline octane on RON. Octane rating in Europe is RON and the U.S. is the average of RON and MON (MON designed for carbureted engines rather than modern, fuel-injected engines). The difference indicates sensitivity to changing operating conditions. BS EN 228 95 RON is a legal standard. No MON is posted, but 85 MON minimum is given in BS EN 228. There is no requirement for 97-98 RON, but it is provided at few select locations. The refiners are allowed to sell 90 RON to niche market (older cars), but octane is not easily available and is not cheaper.
-
Reduce the number of octane gasolines available on the market, i.e., drop lower octane gasoline.
-
Export light naphtha to be used as olefins feedstock.
-
Reform coker naphtha but watch the RON loss with the benzene removal.
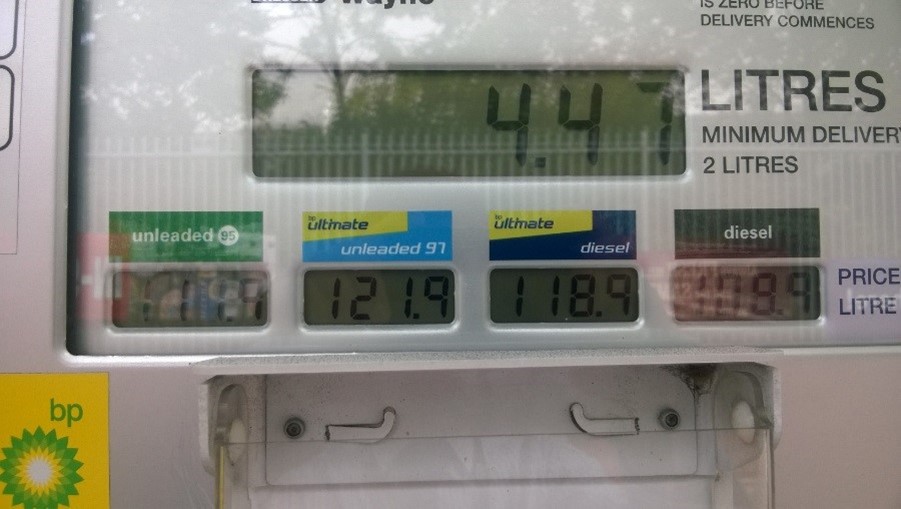
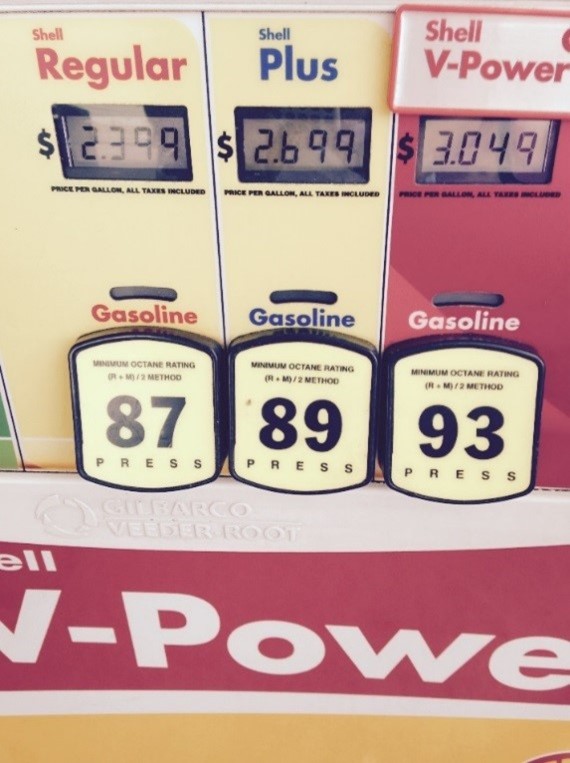