Question 49: Each hydroprocessing unit has an optimum strategy for full load-catalyst replacement: oxidized versus presulfided. How does the strategy change for a partial reload (e.g., top-bed skim or replacement)? Are there other situations when pre-activation is justified?
TEMME (Albemarle Corporation)
Use of either oxidized or presulfided catalysts can work fine. It depends on safety approach, cost allowance, time goals, and handling the processing preference. The main point is safely carrying out this skimming operation, whether or not it is oxidized catalyst or presulfided catalyst. In terms of skimming, safety has to be the first consideration; because after the catalyst bed skim,if you are going to be loading, you must do so under inert conditions since the remaining catalyst load is pyrophoric. Now presulfided catalyst can allow for a quicker startup timeline, but it can also add extra expense and logistics. For example, presulfided catalysts generally must be delivered in bins instead of super sacks. For some catalyst replacement skims, the catalyst being skimmed is just low activity catalyst; and therefore, you can actually do an online sulfiding if you bypass the amine scrubber and allow the recycle hydrogen to sour up, getting some H2S in it to provide the sulfiding needed.
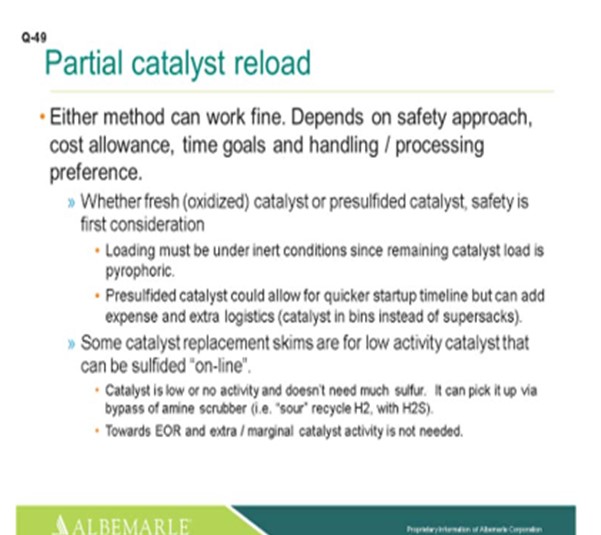
Other situations where presulfided or preactivated catalyst is justified includes when there are process storage limitations. Use of presulfided catalyst allows the product to get on spec sooner or even allows processing of cracked feed sooner, if cracked feed protection (CFP) treatment from Eurecat is utilized, which can be very helpful for processing coker naphtha streams or LCO streams. There are units that are heater-limited and which cannot get up to a high reactor temperature greater than 610°F to complete the high-temperature sulfiding on straight-run feed. And especially for smaller units and naphtha hydrotreater units, with limited amounts of catalyst, the cost of presulfided catalyst can be far outweighed by the time savings for getting the unit online.
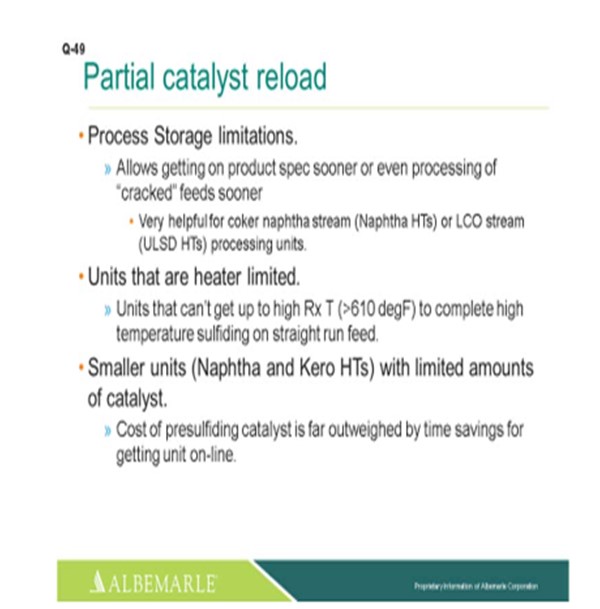
WRIGHT (Hunt Refining Company)
To focus on the second part of that question – situations to use pre-activated catalysts, Paul touched upon smaller units and their heater limitations. Other possibilities include when: 1) flaring of H2S is unacceptable, 2) a unit’s compressor is unable to handle the heavier sulfiding gas, or 3) the possibility of an odor complaint will unacceptable to the company. And finally, there could be a unit where there is metallurgy that is unable to tolerate high levels of H2S and its gas.
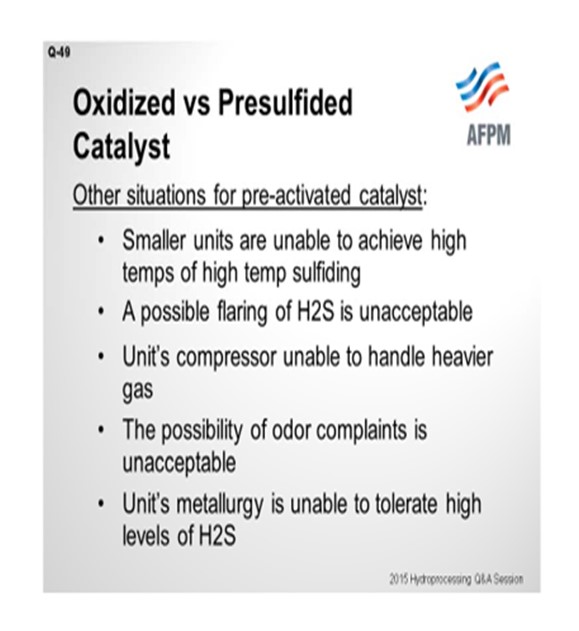
PEDERSEN (UOP LLC, A Honeywell Company)
I will add a couple more scenarios where it might be beneficial to use preactivated catalyst. We have seen some refiners who operate parallel trains within a unit. They will shut down one train for a catalyst changeout and keep the other train running during the turnaround. In those cases, either from a logistical standpoint or from a time standpoint, it is often highly beneficial to use preactivated catalyst. Another situation where preactivated catalyst might be useful is if the downstream catalyst is noble metal. In that case, a refiner might preactivate the base metal treating catalyst and pre-reduce the noble metal catalyst.
TEMME (Albemarle Corporation)
Just to follow up on Sam’s point of the possibility for odor complaints: There have been some refineries that have had those issues, especially with some neighbors being close to the fence line. So an internal recycle line back from the fractionator and back to the feed surge drum can help reduce or do away with that possibility of odor complaints.
SUDIPTO CHAKRABORTY (Albemarle Corporation)
I want to add one scenario when catalyst may need to be presulfided. Sometimes, for a coker naphtha unit or naphtha unit having sufficient diolefins, a diolefin reactor will be needed. The diolefin reactor typically runs at a much lower temperature. So to save costs, it may not be designed for a temperature that is required during sulfiding, especially the temperature needed during high-temperature sulfiding stage. So, for those cases, you will need to use presulfided catalysts for the diolefin reactor.
SERGIO ROBLEDO (Haldor Topsoe, Inc.)
Typically, it is not required to pre-activate our active graded-bed rings when performing a skim. Enough sulfur is typically present in the feed to sulfide the rings over time.
As for main bed catalyst, it depends on the amount of catalyst being replaced. A good rule of thumb is that if less than 10% of the bed is being replaced, then there is no need to pre-activate the catalyst being installed. This will have minimal impact on activity, and the native sulfur in the feed will sulfide the catalyst. However, if the catalyst is serving a separate purpose (i.e., demetalization), then pre-activation may be warranted depending on the level of contaminants and cycle length objectives.
If a full top-bed replacement, or more than 10%, is expected to be skimmed, then pre-activation should be performed as there may be too much of an activity penalty from the beginning, if in-situ sulfiding is not an option. In units, such as naphtha units, where the level of sulfur in the feed is very low and the operating temperatures are also low, pre-activation is typically justified.
RUOYAN COLEMAN (Criterion Catalysts & Technologies)
Several factors play a role in the decision of using oxidized versus pre-sulfurized or presulfided catalysts for a unit startup. The typical factors to consider for a full-load startup include the startup duration, presulfided catalyst cost, presulfided catalyst handling and loading requirements, and the comparative environmental impact versus using a sulfiding agent like DMDS to sulfide the catalyst. Typically, the presulfided catalysts can shorten the startup duration and, therefore, reduce the costs associated with unit downtime.
Since the ex-situ presulfiding adds additional costs, an economic analysis has to be performed to evaluate the higher cost associated with the presulfided catalysts against the savings from the shorter startup duration. For partial-load cases, the amount of catalyst is relatively small, so the total cost of using presulfided catalysts will be lower.
In some instances, for partial-load replacement where the percentage of catalyst volume that needed to be sulfided is small (for example, a top-bed skim or replacement), oxidized catalysts can be sulfided by the H2S in the recycle gas generated by the fresh feed. Each case should be individually evaluated to determine the best solution.