Question 48: What is your experience with carbon on regenerated catalyst levels in partial burn operations? How do you confirm an optimal level of carbon to ensure desired product yields? How do metal amounts or feedstock play a role in controlling carbon on regenerated catalyst?
TODD HOCHHEISER (Johnson Matthey)
The optimal level of carbon on regenerated catalyst (CRC) is often a balance between conversion and feed rate. Lowering CRC can be achieved by increasing air rate. In FCCs that are air blower or regenerator temperature limited, this can result in a feed rate reduction or residue processing reduction. The benefit of operating at the lower CRC is increased ecat activity and conversion.
The JM laboratory conducted an expert with a spent catalyst sample. The spent catalyst contained 1.2 wt% carbon and was taken from a two stage FCC unit processing residue feed. The sample was divided, and the coke was burned off to varying levels ranging from 0.07 wt% to 0.82 wt%. Each sample was then processed on a ACE unit. MAT decreased by 1 wt% for each 0.2 wt% increase in CRC (see Figure). The activity loss slope will be specific to the FCC, catalyst type, and ACE testing protocol.
Another method to evaluate the impact of CRC on activity is based on routine ecat testing. Ecat activity results are usually reported after calcining the sample. ACE testing can also be conducted on the sample prior to calcining. The activity gain from calcining shows the impact CRC has on that particular sample. A trend can be developed by plotting the activity delta from calcining versus CRC.
When operating at higher CRC, delta coke is reduced. For units that are delta coke limited, the right balance needs to be found between CRC and delta coke. If feed metals are increased, delta coke will increase. One method to combat the higher metals is to raise CRC thereby lowering delta coke. In this scenario, the higher metals will impact conversion negatively for two reasons: ecat metals poisoning and operating at higher CRC.
Catalyst formulation can be evaluated to switch to a lower delta coke catalyst. This will allow lower CRC while still staying within regenerator temperature limits. Metal trapping additives can also be used to reduce delta coke.
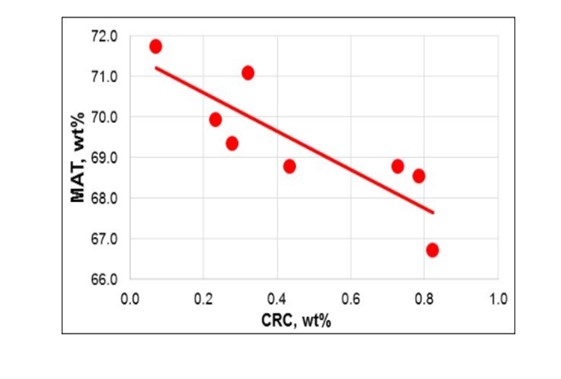
DAVID HUNT (W. R. Grace & Co.)
FCCU partial combustion operation brings additional operating complexity relative to a full combustion regenerator operation. Before equilibrium catalyst activity is measured by the catalyst supplier, coke is traditionally burned clean, and the activity is reported on a carbon free basis. For operations where carbon on regenerator catalyst is greater than ~ 0.25 wt.% the effective in unit equilibrium catalyst activity may be less than the reported value.
Excessive carbon level can be a process safety risk in addition to producing high slurry oil and lower conversion. Carbon will generally cover the most active sites enriched with the youngest catalyst fraction.
The amount of carbon on the regenerated catalyst is influenced by several factors including the following:
- Feedstock and recycle rates
- Feedstock properties (Conradson carbon)
- Regenerator combustion air rate
- Flue gas carbon monoxide (CO)
- Regenerator temperature
- Regenerator and riser residence time
- Catalyst activity
- Metals
- CO combustion activity
- Additives
- Particle Size Distribution
Excessive carbon on regenerated catalyst is often a challenge for constrained units operating a partial combustion regenerator at increased feed rates with heavier feedstocks.
When feedstock Conradson carbon levels increase additional coke is deposited onto the catalyst in the riser. Since the regenerator operates with no excess oxygen, the incremental coke on catalyst increases CO levels and finally carbon on regenerated catalyst for the same combustion air rate. Slurry recycle produces an even more dramatic effect due to the relatively high Conradson carbon level.
Dehydrogenation metals such as nickel and vanadium behave in a similar fashion as Conradson carbon. In the riser delta coke on catalyst increases with these metals moving the regenerator into a deeper partial burn with higher carbon on regenerated catalyst at fixed operating conditions.
Excessive CO combustion activity can strongly drive the C + O2 > CO2 combustion reaction versus C + 1/2O2 > CO consuming more oxygen relative to carbon increasing carbon levels on the catalyst.
Increased average particle size has been linked to higher carbon on regenerated catalyst. Increased regenerator bubble size and less mass transfer to the emulsion was suspected. (1)
Slow combustion kinetics at low regenerator temperature have caused high carbon levels. (1)
Grace is also aware of instances where high levels of “hard coke” are observed on regenerated catalyst where traditional regenerator temperatures are unable to burn the catalyst clean. Several factors are believed to be at play. Grace has worked closely with our customers in those instances to optimize the unit and bring carbon levels back to acceptable levels.
Generally lower catalyst activity and an increased amount of metal trapping are required to reduce delta coke and maintain optimal levels of carbon on regenerated catalyst in a constrained partial combustion regenerator operation with residual feedstocks. Working with your catalyst supplier to continuously optimize the catalyst and partial combustion operation is highly recommended to ensure a profitable and safe operation.
- Indian Refiner Presents Troubleshooting Examples for a Partial Combustion FCC Regenerator, Das et al, Oil and Gas Journal, Sept 4, 2000
CHRIS STEVES (Norton Engineering Consultants, Inc.)
The catalyst and air distribution in a partial burn FCC regenerator will have an impact on the carbon on regenerated catalyst, as well as the operation (primarily regenerator temperatures). The impact on yields for different CRC levels will depend on the feed quality and the catalyst type and should be evaluated through unit testing and trending of historical information, taking care to compare periods with similar feed types and catalyst types.