Question 48: What is your experience bringing hydrocracking catalyst online without ammonia attenuation? Are there alternative methods or technologies to temper catalyst activity without adding ammonia?
MORELAND (Valero Energy Corporation)
Hydrocracking catalyst needs to be passivated during sulfiding to avoid potential temperature runaway as temperatures are increased to complete the sulfiding process. In our experience, there are four different ways that we attenuate the catalyst activity. The first is to inject ammonia prior to the high temperature sulfiding to passivate the catalyst. We have used both aqueous and anhydrous ammonia for this passivation. Four of our hydrocrackers utilize this method.
The second method is to inject another amine that decomposes to ammonia at reactor conditions. For examples, we have used MDEA (methyl diethanolamine), MEA (monoethanolamine), or TBA (tri-n-buytlamine). One of our hydrocrackers recently used MDEA for hydrocracker catalyst passivation.
The third method is to switch to a higher nitrogen-containing feed for the high temperature sulfiding stage. Three of our units use this method, though we will caution you to be extra careful with passivation via this method and follow procedures. Several cases where we have had temperature excursions on startup have occurred when we were trying to utilize high nitrogen feed for passivation and either procedures were not followed or temperature ramps were faster than anticipated.
Then finally, gas-phase sulfiding: There is no need for passivation if there is no hydrocarbon in the system. Just using hydrogen and H2S can sulfide the catalyst without risk of runaway. Five of our units use that method. I will show you a couple of pros and cons.
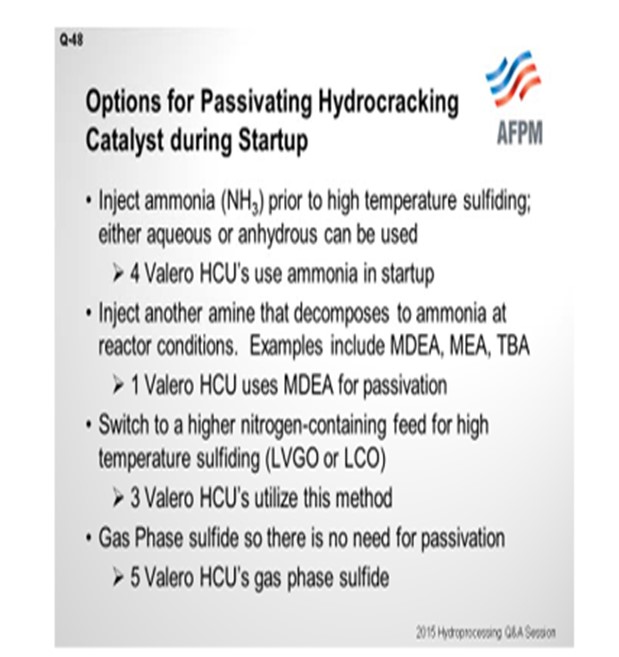
The next slide shows one example of using an amine for sulfiding. It is probably the most uncommon for those of you in the audience. You can see that the red and blue lines are the reactor temperature profiles. The blue is the inlet; the red is the outlet. The purple is the DMDS (dimethyl disulfide) injection rate on the right axis. The light blue color is the MDEA injection. As we heat up to the low-temperature sulfiding temperature and begin DMDS injection, we start the low-temperature sulfiding step. We heat up to about a 425°F inlet here, and then we inject the MDEA during the low-temperature sulfiding, once sulfur uptake is established, to build up the ammonia into the system. The ammonia generated from amine decomposition passivates the catalyst. We then can start the temperature ramp-up to the finishing temperature of around 600°F for the sulfiding. You can see from the dates that this catalyst activation was fairly recently conducted.
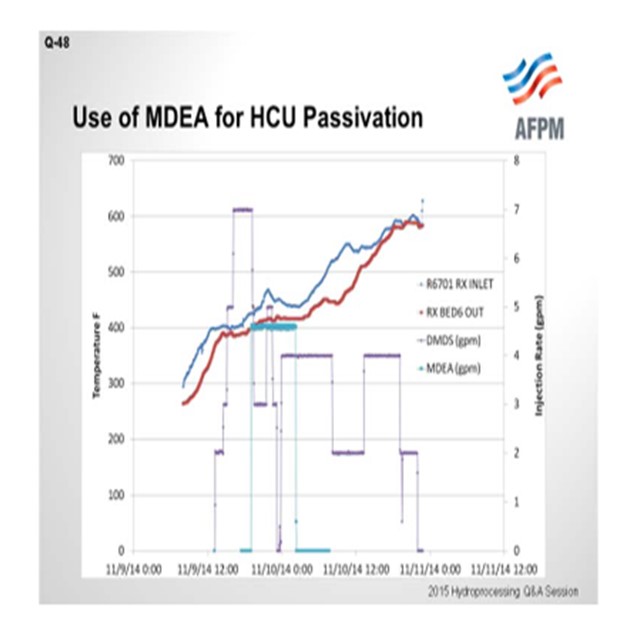
Finally, I want to cover the pros and cons of gas-phase sulfiding because we do use this in five of our hydrocrackers. On the pro side, we can begin sulfiding at a lower pressure: less than the minimum pressurization temperature. Many of our units have limited capability to pressure-up to normal operating pressure and are limited to 100 to 200 psi per-hour ramp rates. Therefore, pressuring up to 2000 pounds can take a significant length of time. So, there is time savings to be able to sulfide catalyst as you are coming up in pressure, as well as reduced risk of catalyst reduction if there is not sulfur in the system yet. The risk of reducing catalyst is greater at higher reactor hydrogen pressures.
No cracking catalyst passivation is required, which I already mentioned. There is less risk or almost no risk of temperature excursion during sulfiding, at least in terms of a runaway based on hydrocarbon cracking chemistry. And then, rotating equipment failure consequences are reduced, particularly the loss of a charge pump during sulfiding. You do not have any liquids circulating.
The downsides of gas phase sulfiding: There is some hydrocracker pretreat catalyst with certain additives that are not able to be gas-phase sulfided to preserve activity. I think Scott referred to that earlier. There is also an additional cooldown step required prior to feed-in, so some of the time savings we get in the earlier step are reversed because we have to cool back down to, say, 300 to 350°F before we put in oil. Additionally, there is less temperature control in gas-phase sulfiding, so temperature can go up, particularly just due to the exotherm from the sulfiding itself or from an absorption exotherm from the first time you put in oil. There is also a lower hydrogen purity due to the loss of sponging excess methane make from DMDS decomposition. So those are some of the cons of gas-phase sulfiding.
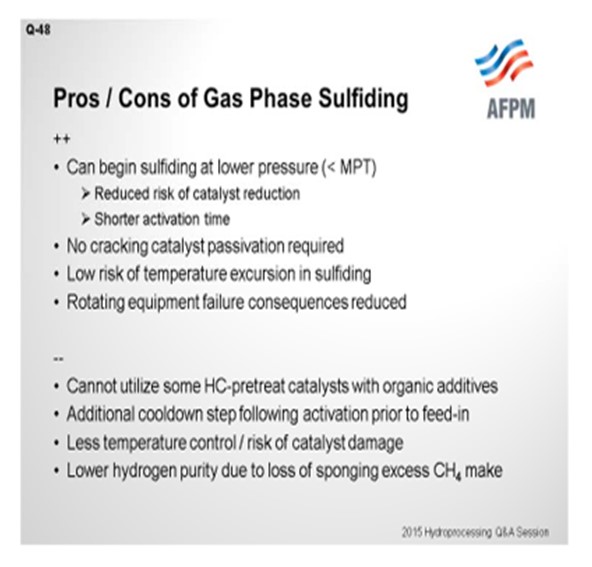
PEDERSEN (UOP LLC, A Honeywell Company)
Andy, you did a really good job going through all of those various scenarios. I would suggest, however, that even with liquid-phase sulfiding, ammonia passivation is not absolutely necessary. Lower activity hydrocracking catalysts can be safely started up without ammonia passivation, although careful compliance with startup procedures is necessary. Certainly, during the gas-phase sulfiding step, there is minimal risk for temperature runaway. Many units that have completed gas-phase sulfiding have also used ammonia passivation of the cracking catalyst to facilitate ramp-up of temperatures after oil introduction, particularly units that are heat-balance-constrained and which require aggressive ramping of cracking temperatures in order to bootstrap up the reactor inlet temperatures.
Ammonia is a very effective acid site inhibitor. The other advantage of ammonia is that it is very easily removed from the catalyst surface when it is time to push the conversion. Andy mentioned the use of aqueous ammonia. There has been a lot of success with the application of aqueous ammonia, as well as anhydrous. He also mentioned a variety of chemical additives that can be used to produce ammonia artificially.
The issue with chemical additives is that, to a large extent, they are not very efficient. The nitrogen content is relatively low. Many of these additives have some toxic characteristics that constrain the operator with regard to handling, and some of the popular amines are quite expensive. So it can get very costly to take this approach. For example, with TBA, there is only 7% nitrogen in the composition, which only produces 9% on weight of ammonia for the amount of TBA injected. Quite a line of trucks can be required to complete ammoniation of cracking catalyst in a big unit.
MORELAND (Valero Energy Corporation)
That is right.
PEDERSEN (UOP LLC, A Honeywell Company)
Andy mentioned the use of MDEA to generate ammonia, which is, as he indicated, a relatively recent development in the industry. I want to note that even with MDEA, the nitrogen content is less than 12%. And more importantly, for every mol of ammonia produced, two mols of water are generated. So consequently, injecting MDEA produces just as much water as injecting the most popular form of aqueous ammonia, which is 30% ammonia solution. I want to mention that there is also now a technology available to inhibit hydrocracking catalyst acid activity offsite prior to catalyst loading. This approach has been applied successfully in a couple of instances.
MORELAND (Valero Energy Corporation)
I meant to mention that one of the reasons we use MDEA is because that chemical was already approved in our plant at the time, which can make turnaround planning a little more straightforward. It is also not that expensive.
PEDERSEN (UOP LLC, A Honeywell Company)
No, not that one. [Laughter]
TEMME (Albemarle Corporation)
Andy and Mike covered the question comprehensively, so I have nothing further to add.
DAVID GATES (Motiva Enterprises LLC)
I want to comment on the use of ammonia passivation and say that I believe most folks are strongly recommending the use of aqueous ammonia as opposed to anhydrous ammonia due to safety concerns. So certainly, if you are going to use anhydrous ammonia, make sure you are taking proper safety precautions.
TEMME (Albemarle Corporation) Yes. Absolutely.
JAMES (TIM) CAMPBELL (Eurecat U.S. Corporation)
I want to add onto Mike’s last comment. Eurecat’s process is called HCAP. HC means the hydrocracking catalyst is fully activated; AP is acidity protection. Basically, it eliminates the need for ammonia, amines, and high nitrogen feed. It is a lot faster, at least 50% faster, than a gas-phase startup.
VIJAY SRINIVAS (Arkema Inc.)
I want to mention that we have a new amine which contains about 26% active ammonia and decomposes at low enough temperatures.
UNIDENTIFIED SPEAKER Bring in some energy. Is there a bar over there?
ROBERTSON (AFPM)
He is turning into Warren Letzsch before our eyes. [Laughter]
M. SCOTT GREEN (KP Engineering, LP)
I have a question for the panel. On the gas-phase sulfiding option, do you experience any problems with, say, pocketing of the water that is generated from the sulfiding? I know that in some units, such as naphtha hydrotreaters, where you have gas-phase sulfiding startup, the units sometimes have pockets that are not issues during normal operation but which can be on this step. Getting rid of that sour water while you are doing your activation is a lot harder than, say, on a liquid-phase sulfiding startup. The units designed for liquid-phase sulfiding are designed to push the water generated to the separator boots and get rid of the water automatically. So, do you have any issues with that on the gas-phase sulfiding startup option on the hydrocrackers designed for liquid-phase sulfiding?
MORELAND (Valero Energy Corporation)
In our procedures, we must make sure those sour water boots are lined up and that the water will go the same place. But often, we do not have oil-in. Operations may have them all blocked in. The next thing you know, you are filling the separator with water. So it is a good consideration in gas-phase sulfiding.
RANDY ALEXANDER (Reactor Resources LLC) I want to point out that Reactor Resources pushed for the use of MDEA and completed one of the first jobs with it. The idea was safety. MDEA has a safety health hazard rating of 1; ammonia has a rating of 3. So it is just a safer method of injecting nitrogen into the system and getting away from ammonia, which can be hazardous. Tributylamine (TBA) also has a hazard rating of 3. The advantage of TBA is that it does not form water when it decomposes. So it is used in some special cases where water is an issue.
DAVID VANNAUKER (Haldor Topsoe, Inc.) Haldor Topsoe, Inc. has tested a variety of different startup procedures in their pilot plants and has performed more than 50 HDC commercial unit startups without the use of ammoniation. Understanding the feed, operating conditions, and the zeolite can lead to a significant savings in expenses by avoiding the cost of ammoniation facilities and an improvement in profitability by reducing line-out time and getting the products to finished tankage. On-specification production improvements have ranged from a shift to a couple days. The Topsoe startup procedure without the use of ammonia is also a very safe startup minimizing the runaway concerns. For a hydrocracking unit, this is extremely valuable.
JOE FLORES (Criterion Catalysts & Technologies / Zeolyst International)
From an activation standpoint with hydrocracking catalyst, it is always easier to gas-phase sulfide rather than liquid-phase sulfide. An advantage with gas-phase sulfiding is the ability to start sulfiding at lower pressures without having to wait for MPT (minimum pressurizing temperature) to be reached. In addition, since there is no liquid present, the need for passivation of the hydrocracking catalyst is not required. Liquid-phase sulfiding will add potential issues due to dealing with ammonia injection; i.e., pump and safe handling issues. There are also several necessary precautions to prevent cracking of the oil when raising temperature to complete liquid-phase sulfiding activation of hydrocracking catalysts.
Premature cracking of the oil can result in coke laydown and/or a temperature excursion, leading to loss of activity or even a possible loss of containment.
An additional complication of liquid-phase sulfiding is that many unit charge pumps cannot operate at low pressure, so the sulfiding must be conducted at higher pressure. Sulfiding at high pressure in the presence of hydrogen, before H2S breakthrough, can lead to metals reduction on the catalyst, resulting in loss of catalyst activity.
The hydrocracking catalyst needs to be passivated. Methods of passivating the catalyst include using anhydrous or aqueous ammonia injection, amines, or an appropriate straight-run gas oil containing high concentrations of nitrogen.
Liquid-phase sulfiding introduces additional complications and variables to control, and a failure of a piece of equipment during the sulfiding can lead to an undesired outcome. When performed according to recommended guidelines, either liquid or gas-phase sulfiding will give similar activity.