Question 48: What is the range of activity for FCC catalysts in the FCCUs? When is catalyst activity considered too low? When do you decide to reformulate versus changes in operating conditions in order to increase unit conversion?
TIFFANY CLARK (BASF)
BASF receives ECAT from about 200 FCC units worldwide. Of these, the ECAT activity ranges from 60-80, with approximately 75% of the units operating in the 70-76 activity range. The global average for 2017 was 72.5 and so far in 2018 the global average is 72.7.
In general, the average for the Americas has trended up year after year with Europe, Middle East and Asia staying relatively flat. The graph at the top left shows global ECAT annual average activities back to 2001 and the chart at the bottom shows the global range of these activities for the past 10 years.
Within this range, the bell curve varies a little from year to year as you can see here, with 74 being the most common in recent years.
Too low of a catalyst activity is relative to your individual refinery economics, configuration and feed composition, but it is very rare to see units operate below 65. Optimum catalyst activity should be determined with your LP or kinetic model using representative unit data.
Increasing conversion via operating severity versus catalyst activity can have different outcomes and again, is also dependent on your refinery economics. The window of conversion increase using operating severity is often limited by downstream process limitations and yields selectivity. For example, higher riser outlet temperature increases conversion but also promotes more thermal cracking that can result in higher dry gas and coke.
Catalyst reformulation should be considered if there have been significant or permanent changes in feed composition, feed rate, unit economics or if a new constraint has been reached at the FCC or an upstream or downstream unit. In many cases, interim catalyst formulation tweaks can achieve higher conversion and optimized selectivity, while meeting seasonal differences in product objectives.
ALEC KLINGHOFFER (Coffeyville Resources)
- Catalyst Activity “too low”?
- Increased slurry yield
- Downstream units (Alky, hydrotreaters) not full or utilized to full capacity.
- Regenerator “cold” which is affecting operating variables.
- When to “reformulate”?
- Major change at the refinery
- Crude slate changes
- Refinery configuration change.
- Long term economics/market forces change.
- Diesel vs gasoline
DEWEY STUART (Motiva Enterprises)
Catalyst activity ranges greatly depending on the type of unit, type of catalyst, unit constraints and type of feeds. Oversimplifying resid feed units would run MATs closer to 65 while non resid feed units would run greater than 72.
Catalyst activity is too low when the coke makes results in low regenerator bed temperatures. Once again, this changes significantly from unit to unit. The primary driver that dictates the Regenerator minimal temperature is if the unit is a full or partial combustion unit. Partial combustion units can be running at lower temperatures than full combustion units. In all units the transition between partial and full combustion should happen quickly as the transition can quickly lead to safety and/or environmental effects.
Primary driver on operating conditions versus reformulation of catalyst is around time. Short term or quick moving is managed with operating conditions while longer term forecast is addressed with reformulation.
BOB RILEY and MICHAEL FEDERSPIEL (W.R. Grace & Co.)
FCC catalyst activity is conventionally defined as 100 – (LCO, wt% + Bottoms, wt%), and is most often measured in microscale laboratory units. “Activity” refers to the propensity for the catalyst to upgrade heavier products into higher value, higher volume products. The absolute numbers measured will depend on several factors, including the specific testing unit and conditions, the choice of feedstock, and the quality of the catalyst being tested. There is no standard range or universally accepted testing equipment for FCC catalyst activity (although MAT and ACE® are popular designs), and each testing lab measures catalyst activity on a different scale, because of the reasons cited above.
In Grace’s database, since 2014, the range of microactivity measured on individual samples has been between 48 and 85, with the overall average of 71.7 (Figure 1). This includes over 62,000 individual measurements, and the shape of the distribution is skewed right of normal because conversion reactions in the FCC are empirically approximated by 2nd order kinetics. To correct for this, one can look at Kinetic Conversion (defined as Conversion / 100-Conversion); this data is centered on a Kinetic Conversion of 2.6 over the same period, and much more closely resembles a normal distribution (Figure 2). It is important to note that the 48 to 85 Ecat activity range represents individual sample activity results; industry average Ecat activity typically ranges from low 80s too low to mid 60s.
Figure 1. Equilibrium catalyst activity as measured in Grace’s Ecat program since 2014.
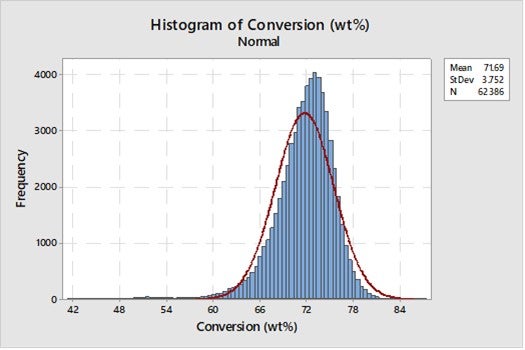
Figure 2. Kinetic (2nd order) conversion as measured in Grace’s Ecat program since 2014.
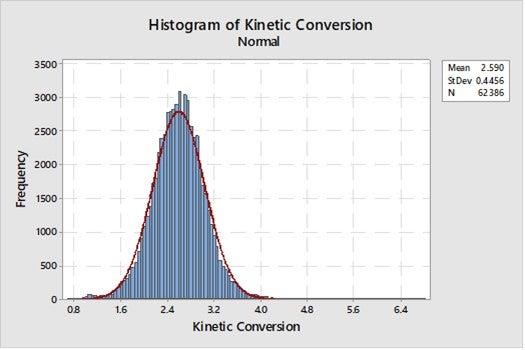
Catalyst activity requirements are a function of the objectives and constraints of any given FCC, which means that each unit likely requires a unique catalyst activity (or range of activity) to meet its goals. Catalyst activity is a function of the fresh catalyst composition, the catalyst addition/replacement rate, in-unit conditions (temperatures, residence times, and potential for thermal or hydrothermal deactivation), and the metals level and type on the FCC equilibrium catalyst.
Optimizing catalyst activity requires an intimate understanding of objectives and constraints; it is highly desirable to define the quantitative difference between today’s performance and the desired unit performance as opposed to the qualitative direction of desired shifts from current operation.
Symptoms of low catalyst activity can include low conversion, low regenerator temperatures, high cat to oils, and erratic regenerated slide valve delta P. These symptoms often represent the constraints present in low activity FCC operations. Feedstock, upstream units, and refinery flexibility will often dictate the operating window necessary for FCC catalyst activity.
In a typical VGO or resid operation, low catalyst activity leads to low regenerator temperatures and higher cat to oil ratio, often up to the limit of control as established by the stability of the slide valve differential pressure. In this scenario, the lower limit of catalyst activity is often set by circulation limits as manifested by low slide valve delta P. Higher cat to oil ratio is generally desirable for units pursuing maximum conversion. However, in some instances the higher cat to oil may not compensate for the lower catalytic activity which could result in lower conversion. Catalyst additions, reactor temperature, and even feed temperature can all be used as control handles to maintain an adequate differential pressure or enough level of conversion.
In contrast, a highly hydrotreated feed operation is likely to see low catalyst activity manifest as low regen dense bed temperatures, often near the point where combustion is not adequate to fully regenerate the catalyst. The lower activity limits in these operations are typically much higher than those in VGO service, and in this scenario, catalyst additions or catalyst reformulation are typically the best handles for managing regenerator temperature. Other methods, including torch oil injection, slurry recycle, fired air heater use, or even reduction in stripping steam, often cost more in lost products or in catalyst deactivation than they gain in unit operating stability. Routine use of these “other methods” for heat balance control should be viewed as an indicator of catalyst activity being too low.
Regarding reformulation vs. changes in operating conditions, catalyst reformulations are recommended to manage sustained changes in refinery operating requirements. Whether for increasing conversion, or managing virtually any new requirement on the FCC, the timing is a critical factor in the decision between the use of catalyst vs. the use of operating conditions. Examples of sustained changes that could merit a catalyst change include adjacent units nearing end of run conditions, sustained use of new feedstock, degradation of the mechanical condition of the FCC equipment, or market trends which require long term production of a modified yield slate. Because of the timing required to properly design, deploy, and turn over new FCC catalyst formulations, the main drivers for reformulation should be matched to the time scale of the unit’s ability to realize the benefits. For shorter term needs, it is often more desirable to consider changing operating conditions or using FCC additives to modify yield selectivities or manage short term refinery requirements. Operating conditions which can increase conversion include increased reactor temperature, reduced feed temperature, increased catalyst additions, reduced carbon on catalyst (partial burn units), and removal of low conversion feed components (slurry recycle, other low hydrogen content feeds, etc.).