Question 48: What are the typical guidelines for reactor loading if the decision is to not fully load with catalyst? Is it acceptable to short load a reactor, and what are the recommended minimum and maximum distances below the inlet distributor?
VICHAILAK (Marathon Petroleum Corporation)
First of all, it is a bit unclear why one would want to short-load the reactors. Can it be done? Yes, especially if it is a gas-phased operation. If it is a mixed-phase operation, then it probably could become an issue. For liquid phase, if you have bubble cap trays or something like that and the top of the catalyst is just way too far from the distributor trays, it is possible that you could disturb the flow path and create maldistributions. We normally recommend a void space of 6 to 12 inches. We have a unit that runs at 15 inches with the bubble cap, which is doing well. Instead of short-loading, the best option we recommend is to utilize the catalyst activity that best matches the application. You can also look at the regenerator catalyst instead of using full highactivity catalyst, but you will have to increase the amount of bottom support operating layers in order to lift the bed up closer to the distributed trays. Be careful on the bottom support layers because they are heavy and adding too much support material will have an impact on the foundation of the unit.
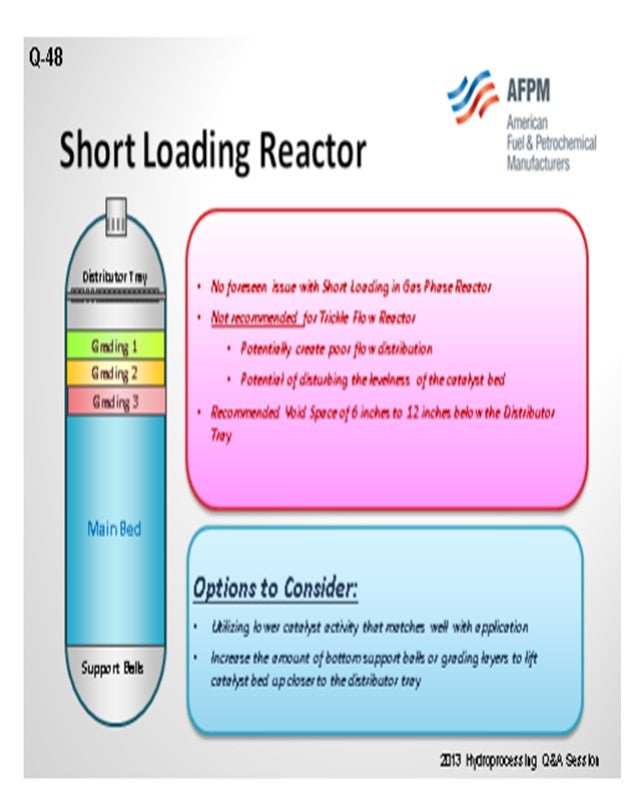
SIVADASAN (UOP LLC, A Honeywell Company)
UOP has seen a commercial unit where short loading of the catalyst was done. We generally give a guideline maximum allowable void height of 12 inches and a recommended target of around 6 inches. In the situation where the refiner intentionally does a short loading, we tell him to put in a layer of 8 inches or more of CatTrap® 65 or CatTrap® 80 to achieve a good distribution.
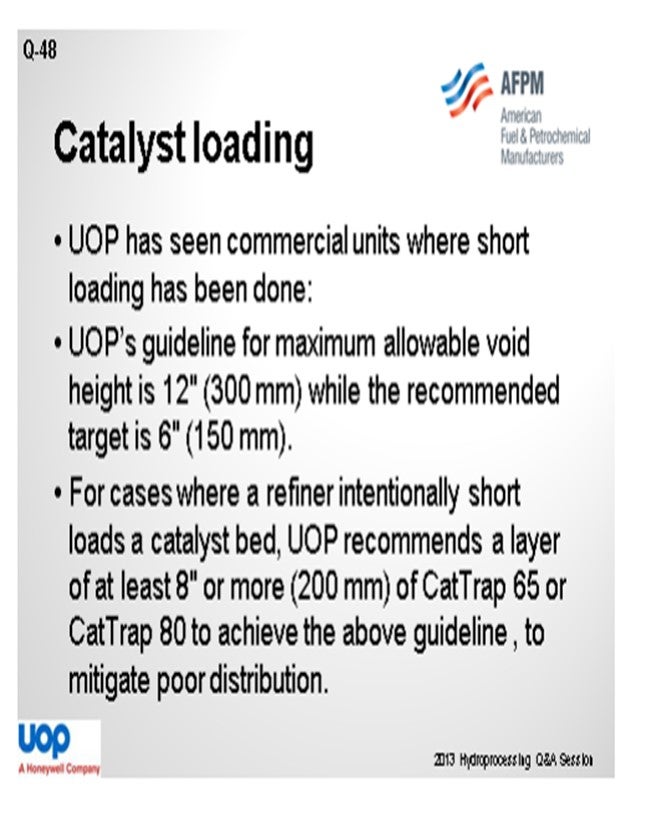
MONTRI VICHAILAK (Marathon Petroleum Corporation)
For gas phase application [i.e., NHT (naphtha hydrotreater)], short loading the catalyst bed will unlikely have any impact on the overall expected performance.
A typical distance from tray to the top of the catalyst bed for trickle bed application, where gas and liquid flow through the catalyst bed, is 12 inches. Some of the new high-performance trays advertised to be able to load the reactor as close as 6 inches from the tray.
For bubble cap types of distributor trays with a short-loaded bed, the momentum of liquid jet out from the distributor onto the catalyst can potentially create a disturbance to a perfectly loaded bed and cause maldistribution. However, Marathon had an experience of having a distance of 24 inches from the bubble cap tray to the top of catalyst without having any issues. For spray nozzle types of distributor tray where the mist of liquid is sprayed onto the catalyst bed, short loading should be acceptable.
MONTRI VICHAILAK (Marathon Petroleum Corporation)
For gas phase application [i.e., NHT (naphtha hydrotreater)], short loading the catalyst bed will unlikely have any impact on the overall expected performance. A typical distance from tray to the top of the catalyst bed for trickle bed application, where gas and liquid flow through the catalyst bed, is 12 inches. Some of the new high-performance trays advertised to be able to load the reactor as close as 6 inches from the tray. For bubble cap types of distributor trays with a short-loaded bed, the momentum of liquid jet out from the distributor onto the catalyst can potentially create a disturbance to a perfectly loaded bed and cause maldistribution. However, Marathon had an experience of having a distance of 24 inches from the bubble cap tray to the top of catalyst without having any issues. For spray nozzle types of distributor tray where the mist of liquid is sprayed onto the catalyst bed, short loading should be acceptable.
Instead of short loading the reactor and leaving a large room below the distributor tray, there are many other options that can be considered. For example, add more inert balls to the bottom of the reactor or add more gradings/inert on the top of the bed. One should take into consideration that inert balls are much heavier than the catalyst. Additional inert balls in the reactor will also add weight to the reactor foundation and its support structure. Marathon prefers utilizing correct catalyst that has optimum activity level for the application and allows normal loading of the reactor.
RAJESH SIVADSAN (UOP LLC, A Honeywell Company)
UOP has seen commercial units where short loading has been done. UOP’s guideline for maximum allowable void height is 12” (300 mm) while the recommended target is 6" (150 mm). A void height greater than 12” below the V/L (vapor/liquid) distribution tray may allow liquid to coalesce which can significantly compromise liquid distribution across the catalyst bed.
For cases where a refiner intentionally short loads a catalyst bed, UOP recommends a layer of at least 8” or more (200 mm) of CatTrap 65 or CatTrap 80 to achieve the above guideline, to mitigate poor distribution.
SERGIO ROBLEDO (Haldor Topsøe, Inc.)
The impact on whether to short-load or not is dependent on whether the reactor is vapor-only or mixed-phase flow. If the reactor is vapor-only, then no distribution tray is present and there is no penalty for short-loading the reactor (as long as there is enough activity to meet the required cycle objectives).
If the unit is mixed-phase flow, then it is not ideal to short-load the reactor. This is because the larger distance between the top of the catalyst bed and the bottom of the tray will result in poor flow distribution. For Topsøe’s VLT distribution tray, there is no actual minimum distance, but the practical distance is about 6 to 12 inches (depending on reactor diameter) as anything lower than that would prevent the catalyst handling company from loading the catalyst bed and ensure that it is level. The maximum distance recommended is 18 inches from the catalyst bed to the bottom of the distribution tray.
If it is decided that more activity is not needed, then there are a couple of options that can be done. Higher amount of grading, or even inert rings, can be placed on the top of the catalyst bed. Another option is to load a lower activity catalyst at a lower cost. If the concern is start-of-run pressure drop, the bed can be sock loaded (if currently dense-loaded) or a larger size catalyst can be installed. Last, a larger layer of inert ceramic balls can be loaded in the bottom of the bed to push the catalyst bed up and ensure the entire catalyst volume is filled.