Question 47: What evaluations are required for hydrocracking units to increase conversion due to processing heavier feedstocks?
WATKINS [Advanced Refining Technologies (ART)]
Pilot plant studies should be done to evaluate catalyst performance with new proposed feeds. If you are planning to make revisions to your unit, you certainly want to consider catalytic changes; perhaps more selective to diesel or gasoline. Your operating cycle could possibly decrease or increase with conversion, depending on which way you are tending to go. Additionally, heavier feeds may actually produce greater volume swell or more products in your hydrotreater or hydrocracker, so you might need to consider mechanical modifications downstream. If you cannot get more barrels out of the unit, you must figure out what needs to go in there.
Since you are considering changes to increase conversion, your feed could increase conversion just by changing composition. It could also drastically impact your hydrogen consumption. If you have available hydrogen, you will want to know whether you have enough to be able to make this change. If you are going to run short, then it may not be a good idea because it will decrease your cycle length. Also consider mechanical changes to your unit, specifically your reactor internals. Depending on your system and the types of conversion and cracking, you may have higher heat release; so you will want to know if it will be necessary to add internals. Will you need to add a quench zone or redistribution zone in your unit?
As we mentioned earlier, your analytical lab might be worth considering. You are making a change to your feed; you are heavying it up, or something similar. What are the analytical capabilities of your lab? If it is simply feeding a D-86 or D-1160, then you may need to consider that 2887 or a true boiling point. How often can you do that? If it becomes a burden, you do not want your analytical lab to be responsible for restricting operations in your refinery. You want to know your process and understand those feed changes.
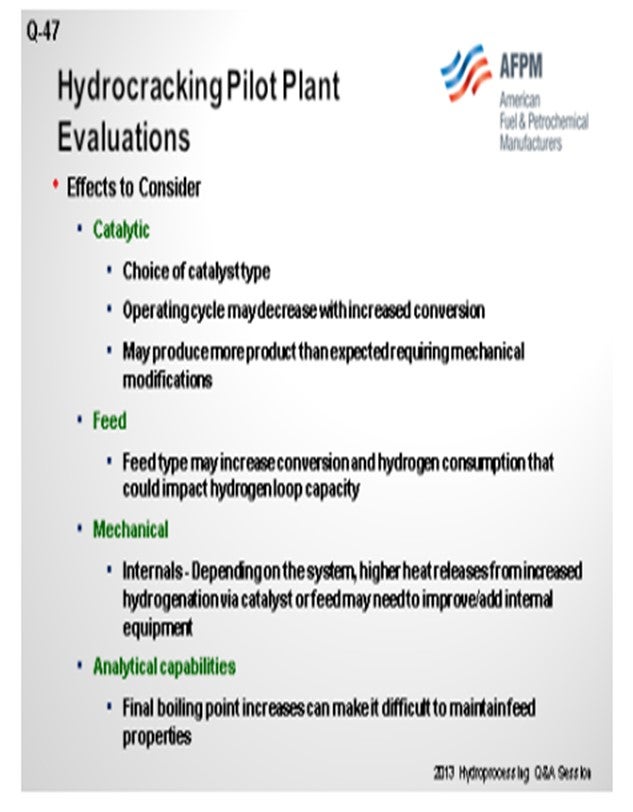
SIVADASAN (UOP LLC, A Honeywell Company)
We are generally examining the feedstock, as Brian had mentioned, and also the feedstock characterization to identify any compounds which may have an effect on hydrocracking reactions. Based on that, you will also analyze the hydrogen consumption. Changes in the feed composition will affect your hydrogen consumption. We will also investigate cycle length objectives, corrosion issues, and any effects on the downstream units as a result of a change in conversion of the unit.
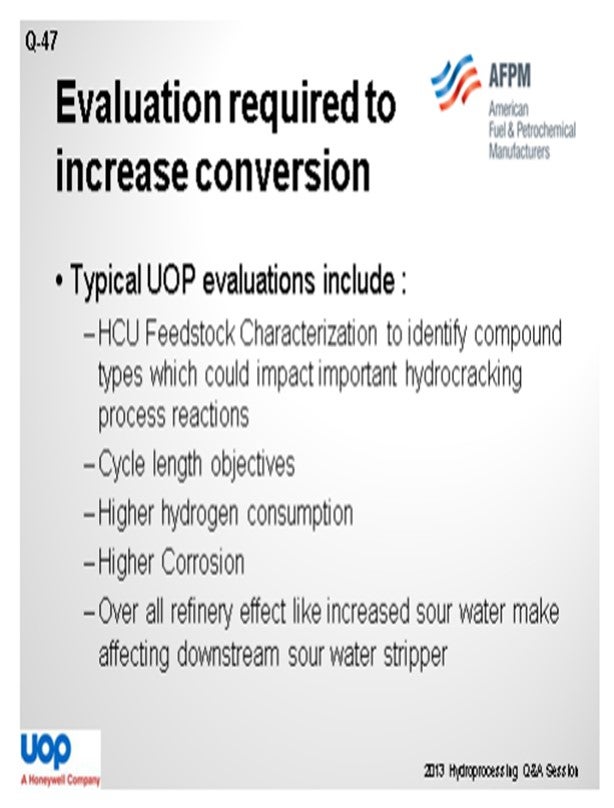
GATES (Motiva Enterprises LLC)
If you are considering processing heavier feeds in a unit that was not designed for this mode of operation, you should have a detailed licensor or engineering evaluation review the pre-heat exchangers and fired heaters. You should consider the impact to catalyst life and evaluate the potential need for a different catalyst to accomplish the goals of hydrogen saturation. If you process heavier feed at higher conversion, you will have higher hydrogen consumption; so hydrogen availability may be a concern. The separation, distillation, and potentially product cooling should be reviewed.
You also want to carefully evaluate the safety concerns of having a potential temperature runaway under these new conditions. If you are increasing your conversion, you will likely see higher bed exotherms. So when you understand your available quench and the position of the quench valves, you should evaluate to determine if you will have sufficient control of the exotherms in the reactors.
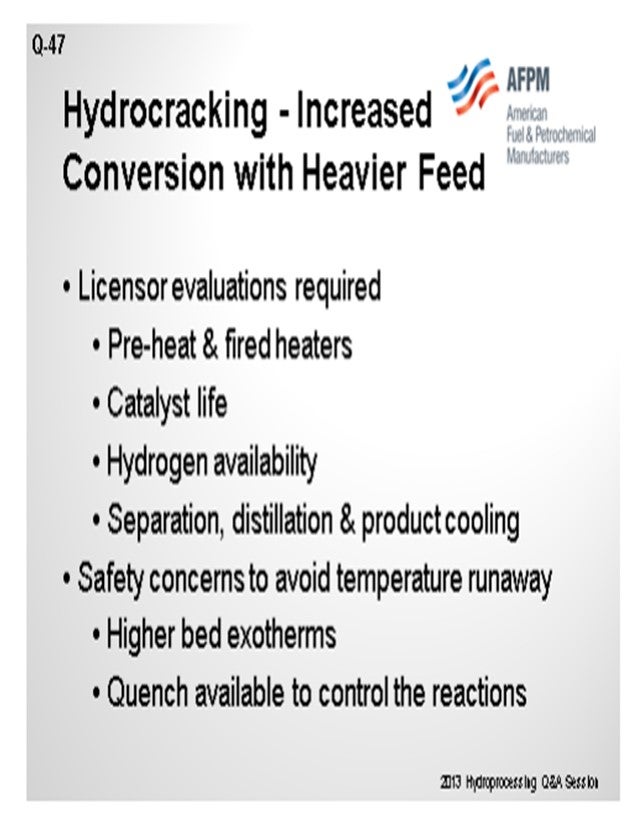
BRIAN WATKINS [Advanced Refining Technologies (ART)]
Evaluations for increased conversion of heavier feedstocks must consider catalytic, mechanical, and analytical capabilities. Depending upon catalyst choice, the operating cycle may decrease with increased conversion; so it is important to work closely with your catalyst supplier. Depending upon feed type, increased conversion may result in an increase in hydrogen consumption and may therefore have an impact on hydrogen loop capacity and operating safety systems. An increase in conversion can also produce more light products, often requiring mechanical modifications to ensure that the process equipment can handle it. Finally, as the feed endpoint increases, it is usually more difficult to maintain consistent feed properties. Be sure to consider increased analytical requirements and possible upstream unit modifications to ensure that feed quality is maintained. It is also a good idea to explore the need to improve the reactor internals in order to better handle the higher heat release that is likely to accompany the higher hydrogenation required by a more aromatic (heavier) feed.
RAJESH SIVADSAN (UOP LLC, A Honeywell Company)
Many refiners are finding that there are incentives to include difficult materials in their hydrocracking unit feed blends. It is very important to develop a detailed understanding of the nature of such difficult feed components. Decisions should be supported by analytical characterization; and in many cases, by well-designed pilot plant studies. Typical UOP evaluations include:
1. HCU feedstock characterization to identify compound types which could impact important hydrocracking process reactions such as
• API gravity,
• Sulfur,
• Refractory nitrogen compounds,
• Breakdown of aromatic species by four- and five-ring aromatic structures to identify HPNA (heavy polynuclear aromatics) precursors,
• Asphaltenes,
• Metals, or
• Feed distillation endpoint.
2. Cycle length objectives including
• Graded bed quantity – ∆P issues,
• Activity loss in hydrotreating and cracking reactors,
• Higher deactivation through remaining cycle, or
• Impaired product quality and selectivity.
3. Higher hydrogen consumption, such as makeup gas limitation
4. Higher corrosion including
• Washwater requirements or
• REAC corrosion.
5. Refinery: increased load on downstream sour water unit
DAVID VANNAUKER (Haldor Topsøe, Inc.)
Depending upon the feed and conversion severity change, a comprehensive evaluation may be required. There are many questions that need to be addressed. For example, are the feed pumps adequate? Will the feed surge drum effectively remove the water? Will the feed filters properly work? What will be the impact upon the required hydrotreating temperature, run length, and nitrogen slip? What is the expected temperature increases in the cracking beds? Is the quench adequate? Is there sufficient hydrogen for full rates and maximum conversion? Will the salt point change? Is another waterwash location required? Will the separator drum remove the water? Can the downstream fractionation system handle the changing yield slate?